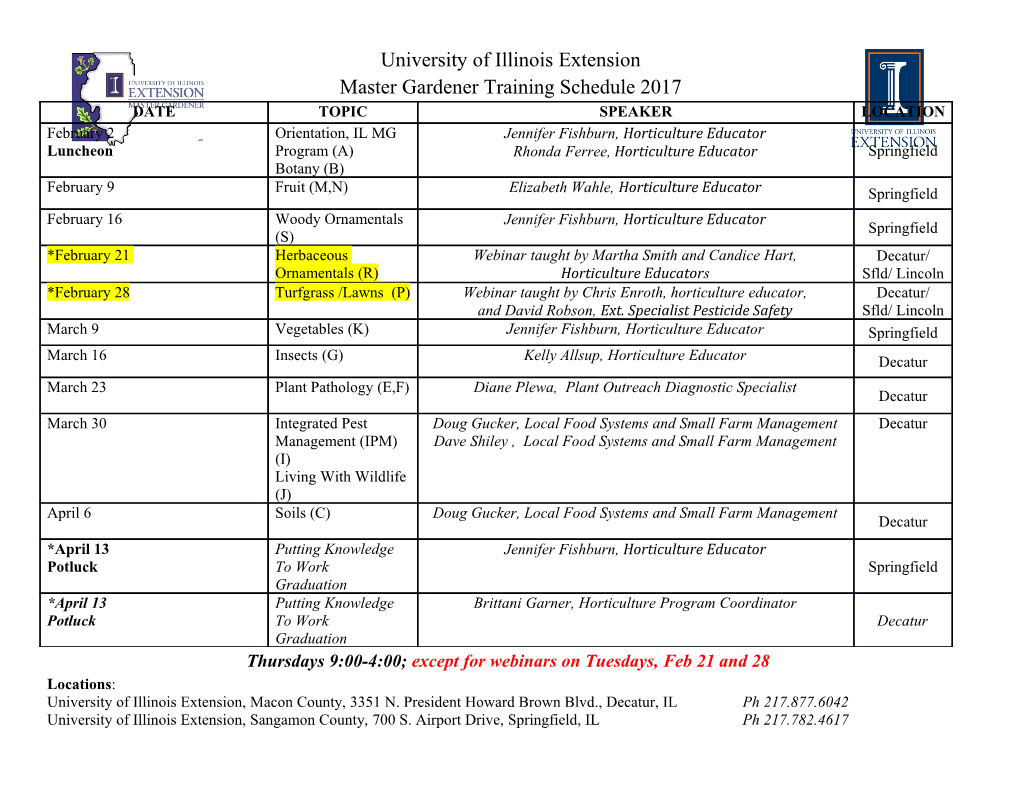
N O S B O R E Classic coating: varnish O J Y from the rib of a Francesco S E T Stradivari violin of c.1732 R U O C A close look into the history and chemistry of varnish making can shed new R A Y light on the mysteries of classic Cremonese varnish, as JOE ROBSON explains T A N G / R E X F E here is a genuine, well-deserved mystery are brought together in a particular A T U R E surrounding the making of a violin. The combination way that creates an entirely new S of materials, from the wood to the strings, fittings and substance, and one that is different varnish, as well as the interaction of the luthier with these from its ingredients in ways that materials, is – to say the least – complex. Likewise, could not be predicted by the there is a great deal of mystery surrounding violin varnish itself. ingredients’ own individual Classic Cremonese varnish in particular has a warmth of colour, characteristics. The index of a liveliness of reflection, a clarity and a longevity which have made refraction of a well-made varnish, it the pinnacle of violin coatings. Yet whether or not we ever unlock for example, which measures the secrets of the great Cremonese violin varnish, there should be how fast light travels through it, no mystery about varnish itself, its uses and its origins. Varnish is simply tree sap and vegetable oil cooked together. Yet The oldest varnish can be found on violin varnish displays true synergy in its materials. Its ingredients 2,500-year-old Egyptian mummy cases 60 THE STRAD NOVEMBER 2007 will be higher than that of any of its constituent parts. Each ingredient brings some of its own distinctive traits to the mix but also loses Classic Cremonese varnish in particular has others. Furthermore, when one component is changed, all of the other ingredients react in new ways. The ways in which raw materials a warmth of colour, a liveliness of reflection, interact in a finished varnish is determined by the varnish maker, and adjusted according to the qualities desired in the final varnish. a clarity and a longevity which have Good varnish is not just a fortunate mistake: it is the result of experience and expertise. made it the pinnacle of violin coatings As far as we know, the oldest varnish that still exists can be found on wooden mummy cases from Egyptian tombs that are more than 2,500 years old. This ancient varnish, made with five or six parts oil to one part resin, and without a cooked-in solvent, would have been Flax seeds are pressed to warmed and then applied to the cases produce linseed oil, one of the most important with a spatula. Because the tombs offered ingredients in varnish it protection from exposure, the varnish still looks good today. The earliest complete description of the varnish making process can be found in the eleventh-century Schedula diversarum artium by Theophilus Presbyter, a monk from either Switzerland or Germany. This manuscript explains the combination of linseed oil and heated resin needed to make a durable and beautiful coating for wood, outlining much the same process that was followed before Presbyter’s writings. The process that varnish makers follow today has not fundamentally changed since then. The first ingredient used in violin varnish is vegetable oil, usually walnut or linseed oil. Walnut oil is pressed from the raw nuts and then filtered to prepare it for varnish making. Linseed oil is pressed from the seeds of the brown flax plant, which is also the source of the fibre used in making linen. Flax is an ancient ingredient: it is known to have been used since 7,000 BC – remnants of flax linen have been found in Stone Age Swiss lake villages, and it was used in ancient Egypt to weave material for boat sails and to wrap mummies. In making violin varnish, linseed oil must be washed and filtered, then heated to remove any dissolved organic material. Once this process is complete, the oil is ready to be cooked for the final varnish. Linseed oil has a special quality that makes it particularly useful as a raw ingredient in varnish. If a thin film of soy or olive oil is spread on a piece of glass and exposed to light and warm air, it does not seem to change much. After a few days, the surface simply remains greasy. If a thin film of linseed oil is spread on a L E glass plate, however, within a few T T Ü B days a remarkable transformation N E F L takes place. The residue changes O W K from a greasy liquid into a tough, E H T O leathery solid called linoxyn. The drying I L B I B of varnish thus depends on the linseed oil T S U Amber, the fossilised tree G constituent turning from a liquid to a U sap from forests that grew A G 30 –90 million years ago, solid as it is exposed to air and warmth. O Z R from which the resin E Linseed oil also gives the varnish film H component in varnish ; O T can come flexibility, an important quality since O H P K it allows the varnish to move with the C The earliest description of the varnish making process can be found in O T S wood as it expands and contracts. I the eleventh-century Schedula diversarum artium by Theophilus Presbyter NOVEMBER 2007 THE STRAD 61 I S T The second component of O How long and at what temperature C K P varnish is resin. Resins are simply H the amber is cooked will determine O T the solids found in tree sap. There O the hardness, brightness and depth of are four resins that have historically colour of the final varnish film. Pine been used to make violin varnish: resin can simply be introduced raw to amber, mastic, sandarac and pine the varnish mixture, or it can also be resin. Amber is the fossilised sap pre-prepared by heating in order to from ancient pine forests that grew separate the solids from the liquid 30–90 million years ago. It is mined components. This heating procedure or collected mainly around the produces rosin as a crystalline solid and Baltic Sea but has also been found turpentine as the liquid part of the in China, Central America and the pine sap. This turpentine is the third US. Mastic is crystallised sap ingredient in the making of varnish. harvested from an evergreen Turpentine can be introduced into shrub that grows throughout the the varnish mix in several ways. As Mediterranean region, and sandarac already mentioned, it may come from is the sap from a small conifer native the fractional distillation of raw pine to the Atlas Mountains of North resin into turpentine and rosin, with Africa. Both these resins also have the turpentine then introduced into an ancient history of medicinal the cooking of the varnish. It may use: mastic was used as a cure for come simply from undistilled raw stomach complaints throughout the pine sap used in the cooking of the Mediterranean, and sandarac was The flax plant is known to have been used by man since 7,000 BC varnish. In this case, since the amount an old Arab remedy for diarrhoea. and boiling point of the solvent portion The last resin used in violin varnish, pine resin, is collected from of pine sap differs from species to species, the varnish maker can a variety of pine species, including the Aleppo Pine, which is also control the properties of the final varnish by choosing their species the source of Greek pitch or rosin. Many of the oldest recipes for carefully. Finally, an alternative natural raw sap such as Venice violin varnish refer to Greek pitch as an ingredient: in his Classic turpentine, sap tapped from larch trees, may be used in the mix. Italian Violin Varnish (1985), Geary Baese quotes the 16th-century Turpentine acts as a solvent and aids the finished varnish’s Venetian Marciana Manuscript’s description of preparing drying properties. Yet the role of turpentine in the making of a ‘lustrous and beautiful’ violin varnish is the least varnish: ‘Take for one understood and the most measure: one pound of discussed aspect of the linseed oil, and make it whole varnish making boil in a clean glazed pot. process. Some historians Add half a pound of and violin makers believe pulverised clear and that no turpentine was beautiful Greek pitch, used in the making of stirring it in, incorporating varnish during the early it well on a gentle fire. and classic periods of Put in half a pound of violin making. Others, powdered mastic.’ however, believe that this Amber, mastic, remains an open question. sandarac and pine resin: The solvent power of each of these four turpentine appears in the different resins must historical record as early be treated in a different as 460 BC : the Greek way in the preparation historian Herodotus, of the final varnish. travelling in Egypt at Sandarac and mastic can that time, described the simply be dissolved raw use of ‘oil of cedar’ in in the linseed oil as it is the embalming process. heated. Amber, however, It was later referred to must be pre-cooked at N by Pliny the Elder in O S B temperatures of over O his Historia naturalis of R E O 300 ˚C in order for it to J 77 AD .
Details
-
File Typepdf
-
Upload Time-
-
Content LanguagesEnglish
-
Upload UserAnonymous/Not logged-in
-
File Pages4 Page
-
File Size-