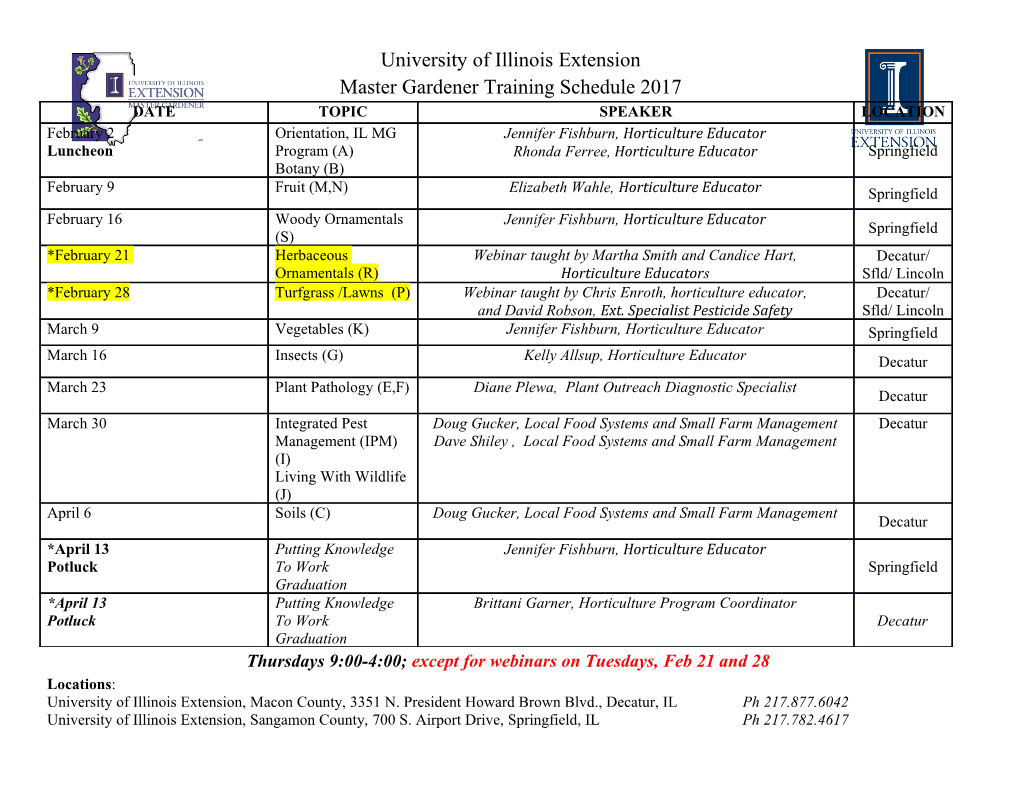
Investigation of laser-arc hybrid welding utilizing CMT, effects upon oxygen and nitrogen contents as well as the weld stability due to oxygen contents of the shielding gas and gap oxides Jan Frostevarg, Pan Qinglong, Masami Mizutani, Yousuke Kawahito, Seiji Katayama Abstract In this study, the effects upon weld arc stability and contents of oxygen and nitrogen inside the weld is investigated for laser-arc hybrid welding (LAHW) using the CMT arc mode. CMT is a controlled short arc technique that is here expected to be less sensitive to oxygen levels in the shielding gas. Having oxides or nitrogen inside the weld region is also known to alter the fluid mechanics such as surface tension, but also a cause for porosity. The gap preparation prior to welding is typically carried out by thermal cutting, water jet cutting or grinding. These edges are then placed to form the joint to be welded. In the case of thermal cutting, oxides are usually formed on the cut edge, adding oxygen into the melt pool when welding is conducted. The effects are studied by macroscopy, HSI and chemical analysis. The arc stability and oxygen and nitrogen levels in the welds are more affected by the oxides remaining from the laser cut edges than the oxygen in the shielding gas when the cutting oxides are removed. Keywords Laser hybrid, CMT, Oxides, Laser cut, Stability 1 Introduction Laser-arc hybrid welding (LAHW), combines a focused high power laser beam with an electric arc within the same processing zone [1-4], illustrated in Fig. 1. Compared to autonomous laser welding, LAHW provides filler wire to fill gaps and, aided by the arc, shape the weld surface. Gas Metal Arc (GMA) welding can be carried out by many different techniques. The most common arc modes supplied by all manufacturers are the Standard and the Pulsed mode. In LAHW the most commonly used arc mode is the GMA Pulsed arc mode, where one drop per arc pulse is transferred towards the melt pool in a semi-controlled flight [5,6]. J. Frostevarg Recently, another, even more controllable Pulsed short Luleå University of Technology, Dept. TVM, arc mode technique was developed, the Cold Metal SE-971 87 Luleå, Sweden Transfer (CMT) [7]. It utilizes controlled wire feeding and e-mail: [email protected] surface tension drop transfer. The wire is pulled back and Osaka University, Joining and Welding Research forth instead of using a constant wire feed. If the reduced Institute wire feed rate is deemed acceptable, the technique offers 11-1 Mihogaoka, Ibaraki, Osaka 567-0047, Japan e-mail: [email protected] smooth drop transfer and less electrical power needed by [email protected] to melt the wire. For LAHW, the CMT arc mode has also [email protected] been compared with the Pulsed and Standard arc mode in [email protected] recent studies [8-13], looking at weld stability and metallurgy. Fig. 1 Sketch of the laser-arc hybrid welding setup, including geometrical parameters The quality and strength of welds is significantly determined by surface geometry [14,15], that results from the complex fluid flow mechanics caused by the electric arc and the laser keyhole [16]. The process parameter combination needs to be adapted depending on chosen arc mode and work piece conditions [17,18]. The welding process may otherwise become unstable, resulting in an uneven surface geometry or inner imperfections [9,19- 21]. High Speed Imaging (HSI) enables study of drop transfer and keyhole conditions [9,17,22,23]. The presence of a gap influences the metal flow and the arc [17]. Apart from having an impact on surface geometry [1], unexpectedly increased levels of oxygen and nitrogen contents within the weld is unfavourable. The increased amounts degrade the weld metal mechanical properties, especially concerning low temperature toughness. However, sometimes in certain weld metals the presence of oxides shows improved tendency to form acicular ferrite, improving the mechanical properties. It is also well known that absorption of nitrogen into the weld pool during welding causes porosity as the weld melt solidifies as the dissolved nitrogen is released as gas again. Due to this, it has been said that for general GMA welding, the involvement of air surrounding the arc into the melt pool should be prohibited and welding in strong wind should be prohibited. Different edge preparations have effect upon LAHW, and laser cutting seems to be preferred over welding with milled edges. Laser cutting results in oxides and striations on the cut surface. These oxides are believed to be harmful for weld performance due to pre-mentioned reasons. The oxide layers on the surface formed by thermal cutting processes should be removed or at least controlled regarding evaluation of residual oxygen content. Furthermore, it has been reported that oxygen contents greatly affects the weld bead formation [24,25]. In the world of laser and laser arc hybrid welding, the lowest possible levels of oxygen and nitrogen are required for achieving high quality weld caps with good morphology and mechanical properties. It is expected that the advantages of CMT should not only reduce the heat input into the work piece, but also offers a more stable deposition of weld wire that should not be very sensitive to the effects of the amount of CO2 in the shielding gas. The involvement of oxygen accompanied by decomposition of the shielding gas is usually necessary in other GMA welding processes. In this paper, the CMT-technique is used with LAHW in 10 mm thick steel sheets concentrating on arc stability and oxygen and nitrogen contents of the final welds when welding with and without oxygen in the shielding gas and the thermally laser cut edges. 2 Methodology 2.1 Welding equipment An illustration of the LAHW setup is shown Fig. 1, with the geometrical setup parameters listed in Table 1. The laser used was a 15 kW Yb:fibre laser (manufacturer IPG Laser GmbH, type YLR-15000 (fibre core diameter; 200 µm, beam parameter product; 10.3 mm·mrad, wavelength; 1070 nm). The laser was operated in the continuous wave (cw) mode, focused at the surface by 300 mm focal length optics to a spot size of 400 µm diameter (Rayleigh length ±4 mm). To prevent back reflections damaging the optical fiber a slight tilting of the laser was applied. The GMA torch was applied in a tilted leading position. The GMA welding equipment was a Fronius MAG power source TPS4000 VMT Remote. The wire feeder is a combination of a continuous feeding unit VR7000 with a Robacta Drive unit (from Fronius) that carries out the back and forth motion of the wire tip which enables the CMT-process used in the experiments. The welds were carried out using an articulated robot (Motoman). Table 1 Constant geometrical weld setup parameters, as presented in Fig. 1 Parameter (unit) (mm) (mm) (°) (°) (mm) f (mm) Value 18 2.5 7 -30 -8 300 퐿퐴 퐿 푇 0 푠 푑 훼 훼 푧 2.2 Experimental procedure Most of the parameters could not be freely chosen as they were preset by the system at different wire feed rates for a chosen synergy curve. From these presets, some adjustments are allowed. The filler wire used was Lincoln SupraMIG Ultra (AWS A5.18), a steel-based wire with a diameter of =1.2 mm. The plates welded were 10 mm thick steel Domex 420 MC (S420 MC), laser cut into pieces 50∅ mm wide and 200 mm long, clamped tight in a butt joint configuration with I-gap. The mill scale on the surface was sandblasted off prior to cutting, providing improved wetting and the avoidance of oxide inclusions and lack of fusion at the weld surface [1]. The material composition of the wire and the steel plates are shown in Table 2. The fixed weld parameters used in the experiments are seen in Table 3 and the variable weld parameters are seen in Table 4. The applied shielding gas was Argon mixed with a corresponding specified amount of CO2. The laser power and welding speeds where also varied to compare differences of the weld shape. In the performed experiments as specified, the oxides remaining on the cut surface was occasionally brushed off with a steel brush, without damaging the structure of the surface made by the laser cutting in order to investigate the influence of the oxides instead of surface structure. Table 2 Material composition (in wt%) of the steel plates and filler wire Name C Si Mn P S Al Nb V Ti Si Fe* S420 MC 0.10 0.03 1.50 0.025 0.01 0.015 0.09 0.20 0.15 98.01 AWS A5.18 0.08 1.70 0.85 97.37 * Displayed values are maximum, except for Fe, which is minimum. Table 3 Fixed (preset) weld parameter settings Welding Wire feed Parameter Shield gas flow Arc voltage Arc current Arc power speed rate (unit) (L/min) (V) (A) (kW) (m/min) (m/min) Value 1.5 3 20 13.3 115 퐴1.53 푤 퐹 푈 퐼 푃 푣 푣 Table 4 Variable weld parameter settings Protection gas Welding speed Average laser power Sample Joint cutting oxides brushed off CO2 content (%) v (m/min) (kW) 1 18 1.5 11 No 2 0 1.5 푃 11 No 3 18 1.5 11 Yes 4 0 1.5 11 Yes 5 18 1.5 10 Yes 6 0 1.5 10 Yes 7 0 1.8 11 Yes 8 0 2.0 12 Yes 2.3 Analysis The resulting welds were analyzed by different methods of the samples, in addition to ocular surface observation and macrographs of the cross sections of the welded samples.
Details
-
File Typepdf
-
Upload Time-
-
Content LanguagesEnglish
-
Upload UserAnonymous/Not logged-in
-
File Pages10 Page
-
File Size-