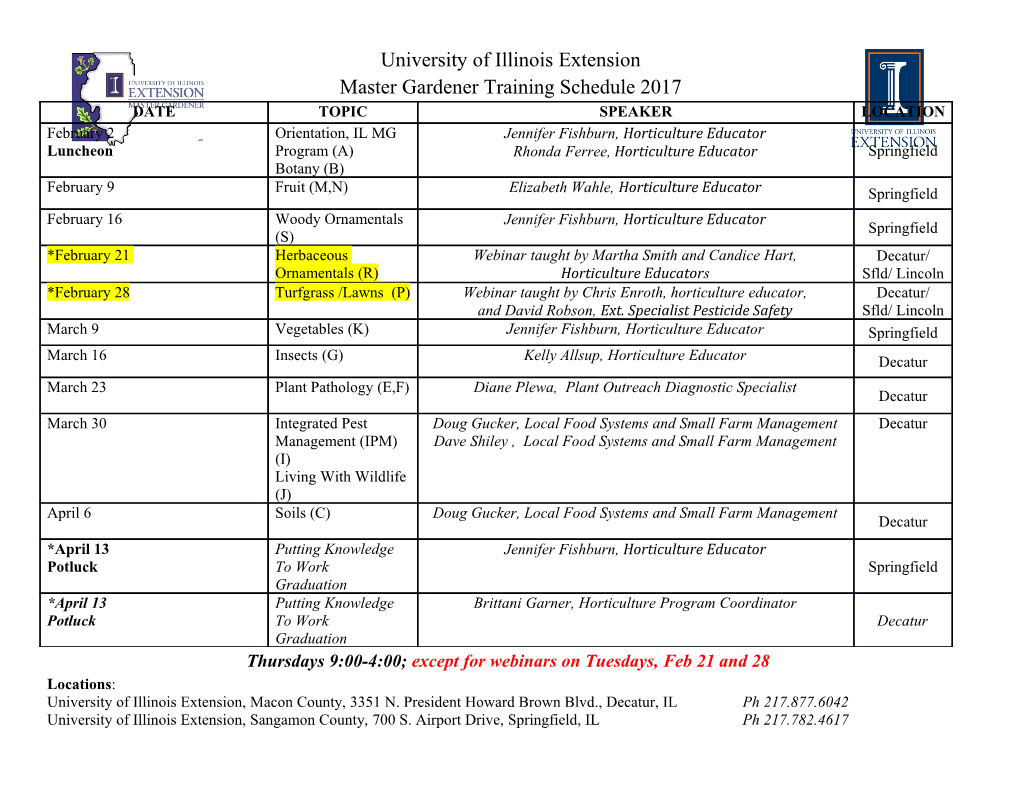
CO2 CAPTURE VIA PARTIAL OXIDATION OF NATURAL GAS Report Number PH3/21 April 2000 This document has been prepared for the Executive Committee of the Programme. It is not a publication of the Operating Agent, International Energy Agency or its Secretariat. Title: CO2 capture via partial oxidation of natural gas Reference number: PH3/21 Date issued: April 2000 Other remarks: Background Previous work by IEA GHG established pre-combustion decarbonisation (PCD) as a potential method of reducing CO2 emissions from natural gas–fired power stations. The PCD approach to emission reduction is now accepted as an alternative to CO2 capture by scrubbing the power station flue gas (post-combustion decarbonisation). A recent study by IEA GHG of the leading options for capture of CO2 in power generation (report PH3/14) concluded that, for natural gas feeds, that there was little to chose between pre- and post- combustion capture options.1 The objective of this study was to assess processing options that might improve the attractiveness of PCD as a method of reducing CO2 emissions. In the original study on this technology (report PH2/19) a process based on catalytic partial oxidation (CAPO), using air abstracted from the gas turbine’s compressor, appeared the most promising of the options examined. Although, as far as we are aware, a commercial-scale CAPO unit does not exist there appears to be no major technical reasons why such a unit could not be operated.2 In this study the CAPO process is taken as a reference case and potential improvements to the process assessed. The opportunity was taken to re-examine the relative merits of air- and oxygen-blown synthesis gas units. Approach adopted The study was organised in stages as follows: • a reference design was produced to serve as a marker against which potential improvements could be compared. This design was based on the process developed previously by IEA GHG and Statoil as reported in PH2/19. • a number of potential process improvements were identified and the engineering judgement of the contractor was used to assess their potential impact. The conclusions of this screening analysis are reported. • Five process variations were developed incorporating potential process improvements and two of these ‘improved’ processes were examined in more detail. The study was done by Fluor Daniel Inc. of California, USA. 1 The option of post-combustion scrubbing the flue gas using an amine-based solvent appeared marginally the cheapest for the present state-of-the-art. 2 Existing commercial applications of synthesis gas technology are based on steam reforming and/or oxygen- blown partial oxidation. Air-blown reactors are used commercially as secondary reformers in ammonia plant. If air is used, the synthesis gas will contain large quantities of nitrogen which, in most applications, is undesirable. In a PCD application, the presence of nitrogen is not a major disadvantage as it is needed to facilitate combustion of the hydrogen-rich gas in the gas turbine (see later in this report and the forthcoming report PH3/12). It is interesting to note that the developers of the Syntroleumtm version of the Fischer-Tropsch process suggest that using an air-blown process to produce synthesis gas is an effective way to reduce costs. i Results and discussion The objective of the study was to assess processing options that could improve the attractiveness of the pre-combustion decarbonisation process in natural gas-fired power plants. Figure S1 illustrates the main components of the reference process used as a basis to assess the effectiveness of potential modifications. Air and steam are used to produce a synthesis gas from natural gas by a combination of partial oxidation and steam reforming. The catalytic air-blown partial oxidation (CAPO) reactor is a single pressure vessel containing two reaction stages.3 The reactor pressure is dictated by the discharge pressure of the gas turbine’s air compressor. Shift conversion is used to convert the CO content of the synthesis gas to CO2 which is then captured in an amine-based scrubbing system. The hydrogen-rich fuel gas is fired in the gas turbine of a combined cycle to produce electricity. Figure S1: schematic of the reference CAPO process Syngas reactor Shift CO to storage conversion 2 CO 2 capture H2O, N 2 to stack H2-rich fuel gas Steam cycle natural gas air gas turbine processing options The following is a summary of the processing options considered in the report: 1. Syngas reactor. A wide range of technologies are in common use for the production of synthesis gases. Syngas can be produced in a steam-methane reformer, this is the method by which most hydrogen is made commercially; air/oxygen is not required. The other main process option is partial oxidation in which oxygen is one of the reactants. There are many hybrids of these two basic reaction routes such as for example, autothermal reforming, one variant of which is used as the reference process in this study. The choice of technology for synthesis gas production is often a marginal decision4 but it is generally agreed that steam-methane reforming of natural gas is cheaper than oxygen-blown partial oxidation. Partial oxidation using oxygen is preferred for production of synthesis gases if the feedstock is heavier 3 The reactor consists of a refractory-lined vessel having an inlet conical combustion zone, in which combustion/partial oxidation reactions take place, and a lower cylindrical volume containing a nickel-based reforming catalyst, in which the reforming reaction mainly occurs and the reactants reach equilibrium. 4 A comment received from an expert, about the previous study on this topic, was that “alternative routes to the production of synthesis gas from methane can be even found on the same site”. iii than natural gas, or if a high CO:H2 ratio is required. If partial oxidation with air can be used, it appears to be less expensive than steam-methane reforming. The use of advanced synthesis gas technology, i.e. a two-stage reactor system involving a gas-heated reformer (GHR), is assessed in some detail.5 A gas-heated reformer gives a significant gain in the efficiency of synthesis gas generation- this is reflected in both the calorific value of the raw syngas and the hydrogen content of the fuel gas (see table S1). However, in the overall power generation process, much of this gain is lost by a need to add large amounts of steam to the gas turbine feed to minimise emissions of NOx (see later). The extra cost of the more complicated reactor system off-sets a small overall gain in process efficiency, with the result that the power generated is more expensive (see tables 3-1, 8-4, and fig 8-1in main report). The conclusion is that there is no advantage to be gained by use of complicated (advanced) reactor systems to raise the efficiency of synthesis gas production, if the resulting hydrogen-rich fuel has to be diluted before it can be used in the gas turbine (see later). Table S1: Synthesis and fuel gas compositions Component Reference CAPO case ‘Improved’ process with gas -heated (mole%) reformer raw syngas fuel gas raw syngas fuel gas H2 27.5 50.7 33.4 59.6 N2 31.6 45.5 26.0 36.0 H2O 26.3 0.1 25.0 0.7 CO 8.0 0.3 10.2 0.8 CO2 5.8 2.1 4.8 0.5 CH4 + 0.5 0.7 0.4 2.0 Ar 0.4 0.6 0.3 0.4 Total 100.1 100.0 100.1 100.0 calorific value 6.5 8.6 8.6 13.4 (MJ/kg) (LHV) 2. Air vs. Oxygen. The use of oxygen (i.e. absence of nitrogen) limits the sensible heat carried out of the reactor by the syngas product. However, steam has to be added to an oxygen-blown partial oxidation unit to moderate the temperature. In an air-blown CAPO unit the nitrogen acts as a temperature moderator. At lower temperatures, less sensible heat is contained in the syngas and it is more likely that an air-blown configuration will show advantages. This study endorsed the conclusion of previous work (PH2/19) that the use of an oxygen-blown partial oxidation unit is less attractive than the reference CAPO case. The large power consumption of an ASU 6 and the relatively low efficiency of the partial oxidation unit, which operates at a higher temperature than the CAPO unit, lower the overall plant efficiency. In this study, Fluor Daniel calculate an efficiency of 40.7% for an oxygen-blown version of the process and 42.8% for the reference air-blown CAPO plant. 3. Shift conversion. The shift conversion reaction is exothermic. A two-stage shift system, as in the reference design, enables a high conversion to be achieved and most of the heat to be recovered at a high temperature. The efficiency of the plant is increased if this heat is used to pre-heat the fuel gas before it enters the gas turbine. A detailed design is needed to optimise capital expenditure on heat recovery against the reduced cost of power obtained through the increased efficiency. 5 There are various proprietary versions of this technology the development of which is largely based on ammonia plant technology introduced by ICI in the late 1980s. It usually involves the hot synthesis gas produced in one reactor being used to provide heat for reforming reactions in another reactor. (UHDE have developed a version of this process where both stages take place in a single vessel).
Details
-
File Typepdf
-
Upload Time-
-
Content LanguagesEnglish
-
Upload UserAnonymous/Not logged-in
-
File Pages105 Page
-
File Size-