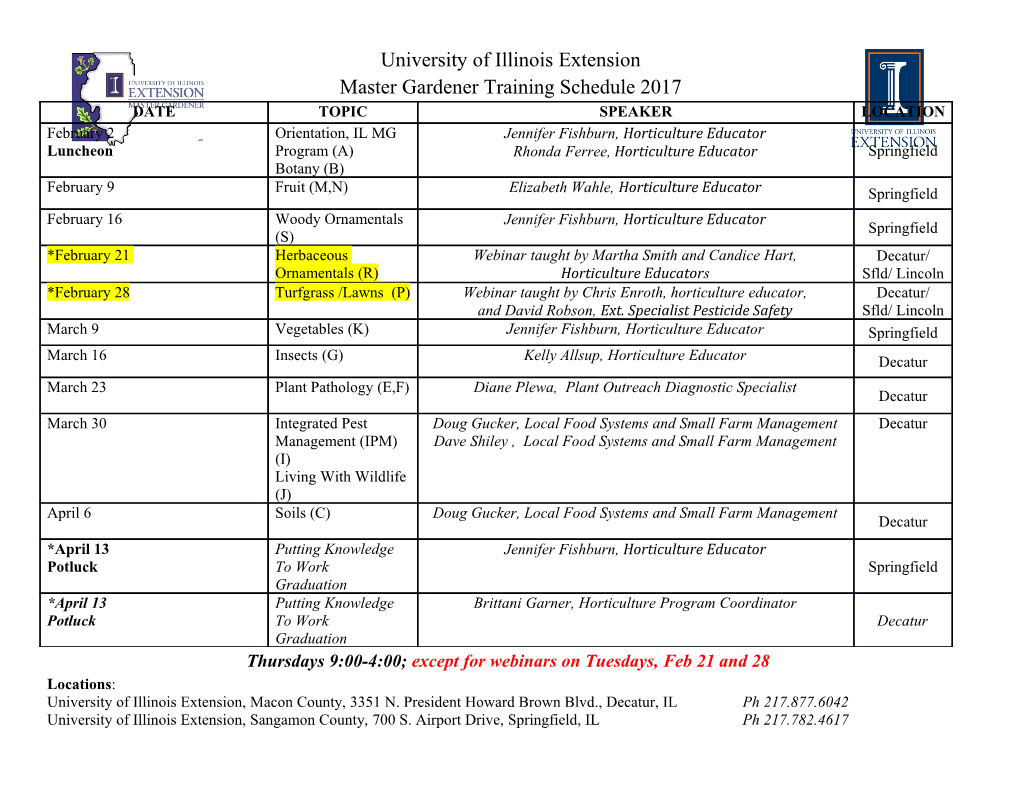
June 2000 • NREL/CP-500-27891 Wind-Tunnel Tests of Two Airfoils for Wind Turbines Operating at High Reynolds Numbers Dan M. Sommers Airfoils Incorporated James L. Tangler National Renewable Energy Laboratory Presented at the ASME Wind Energy Symposium Reno, Nevada January 10–13, 2000 National Renewable Energy Laboratory 1617 Cole Boulevard Golden, Colorado 80401-3393 NREL is a U.S. Department of Energy Laboratory Operated by Midwest Research Institute • Battelle • Bechtel Contract No. DE-AC36-99-GO10337 NOTICE The submitted manuscript has been offered by an employee of the Midwest Research Institute (MRI), a contractor of the US Government under Contract No. DE-AC36-99GO10337. Accordingly, the US Government and MRI retain a nonexclusive royalty-free license to publish or reproduce the published form of this contribution, or allow others to do so, for US Government purposes. This report was prepared as an account of work sponsored by an agency of the United States government. Neither the United States government nor any agency thereof, nor any of their employees, makes any warranty, express or implied, or assumes any legal liability or responsibility for the accuracy, completeness, or usefulness of any information, apparatus, product, or process disclosed, or represents that its use would not infringe privately owned rights. Reference herein to any specific commercial product, process, or service by trade name, trademark, manufacturer, or otherwise does not necessarily constitute or imply its endorsement, recommendation, or favoring by the United States government or any agency thereof. The views and opinions of authors expressed herein do not necessarily state or reflect those of the United States government or any agency thereof. Available electronically at http://www.doe.gov/bridge Available for a processing fee to U.S. Department of Energy and its contractors, in paper, from: U.S. Department of Energy Office of Scientific and Technical Information P.O. Box 62 Oak Ridge, TN 37831-0062 phone: 865.576.8401 fax: 865.576.5728 email: [email protected] Available for sale to the public, in paper, from: U.S. Department of Commerce National Technical Information Service 5285 Port Royal Road Springfield, VA 22161 phone: 800.553.6847 fax: 703.605.6900 email: [email protected] online ordering: http://www.ntis.gov/ordering.htm Printed on paper containing at least 50% wastepaper, including 20% postconsumer waste AIAA-2000-0043 Wind-Tunnel Tests of Two Airfoils for Wind Turbines Operating at High Reynolds Numbers Dan M. Somers James L. Tangler Airfoils Incorporated National Renewable Energy Laboratory 122 Rose Drive 1617 Cole Boulevard Port Matilda, Pennsylvania 16870-9483 Golden, Colorado, 80401-3393 Abstract Introduction The objectives of this study were to verify the Verification of codes used for the design of wind- predictions of the Eppler Airfoil Design and Analysis turbine airfoils, such as the Eppler Airfoil Design and Code for Reynolds numbers up to 6 × 106 and to Analysis Code1, has been limited to Reynolds numbers acquire the section characteristics of two airfoils being below 3 × 106 by the unavailability of high-Reynolds- considered for large, megawatt-size wind turbines. One number, wind-tunnel facilities. With the recent trend airfoil, the S825, was designed to achieve a high toward larger turbines, rated at over one megawatt, the maximum lift coefficient suitable for variable-speed currently available airfoil data are inadequate for the machines. The other airfoil, the S827, was designed to purpose of designing or predicting rotor performance. achieve a low maximum lift coefficient suitable for In addition, high-Reynolds-number, airfoil-code stall-regulated machines. Both airfoils were tested in verification is needed for the prediction of both the the NASA Langley Low-Turbulence Pressure Tunnel maximum lift coefficient (cl,max) and the width and (LTPT) for smooth, fixed-transition, and rough surface depth of the low-drag range. conditions at Reynolds numbers of 1, 2, 3, 4, and 6 × 106. The results show the maximum lift coefficient of The NASA Langley Low-Turbulence Pressure Tunnel both airfoils is substantially underpredicted for (LTPT)2,3 was used for this study because it is the only Reynolds numbers over 3 × 106 and emphasized the two-dimensional wind tunnel capable of chord difficulty of designing low-lift airfoils for high Reynolds numbers greater than 4 × 106 with low Reynolds numbers. turbulence (≤ 0.05%). Two airfoils, the S825 and S827, Symbols from the National Renewable Energy Laboratory (NREL) airfoil families4 were tested. Each airfoil was Cp pressure coefficient tested for smooth, fixed transition, and rough surface c airfoil chord conditions at Reynolds number of 1, 2, 3, 4, and 6 × 6 cd section profile drag 10 . cl section lift coefficient cm section moment coefficient This paper is condensed from the two reports, which L. lower surface includes the airfoil coordinates, covering this study.5,6 R Reynolds number S. boundary-layer separation point Airfoils T. boundary-layer transition location U. upper surface The 17-percent thick S825 airfoil was designed to x airfoil abscissa achieve a high maximum lift coefficient (≥ 1.40) α angle of attack relative to airfoil chord suitable for variable-speed wind turbines. The 21- Subcripts percent thick S827 airfoil was designed to achieve a ll lower limit of low-drag range low (restrained) maximum lift coefficient (≅ 1.00) max maximum suitable for large, stall-regulated machines. Both min minimum airfoils were designed to achieve extensive laminar ul upper limit of low-drag range flow (≥ 30-percent chord) on both the upper and lower surfaces for low drag. Transition to turbulent flow moves to the leading edge just prior to reaching _____________________ maximum lift, which minimizes the effect of roughness on the maximum lift coefficient. Both airfoils were This material is declared a work of the U.S. designed to exhibit benign laminar separation bubbles Government and is not subject to copyright near the leading edge at maximum lift coefficient. More protection in the United States. severe bubbles can lead to unpredictable and erratic 1 AIAA-2000-0043 maximum-lift-coefficient behavior. The design Methods specifications for the two airfoils are shown in Table 1 The measured pressure distributions were integrated to and the airfoil shapes are shown in Fig. 1. determine the lift coefficients. Profile drag was measured using a total- and static-pressure, wake- Experimental Procedure survey probe. The probe was positioned spanwise at the tunnel centerline. The tip of the probe was located 1.84 Wind Tunnel chord downstream of the trailing-edge of the model and The NASA Langley Low-Turbulence Pressure Tunnel could traverse the entire wake profile. (LTPT) is a closed-throat, single-return tunnel (Fig. 2) that can be operated at stagnation pressures from 100 to Standard, low-speed, wind-tunnel boundary 1000 kPa (1 to 10 atm). The unit Reynolds number can corrections8 have been applied to the data, along with be varied from 1 × 106 to 49 x 106 per meter (0.3 × 106 the wake-survey-probe total-pressure-tube to 15 × 106 per foot); the Mach number can be varied displacement correction9. from 0.05 to 0.47. The turbulence level in the test section7 is generally below 0.05 percent for unit Tests Reynolds number up to 13 × 106 per meter (4 × 106 per The models were tested at Reynolds numbers, based on foot) at Mach numbers up to 0.15. airfoil chord, of 1, 2, 3, 4, and 6 × 106 and a Mach number of 0.1 with transition free (smooth), with The wind tunnel test section is 91 cm (36 in.) wide by transition fixed, and with a grit roughness scaled from 229 cm (90 in.) high. Hydraulically actuated circular NACA standard roughness10. Transition was fixed plates provide positioning and attachment for the two- using grit roughness that decreased in size with dimensional model (Fig. 3). The plates are flush with increasing Reynolds number.11 as seen in Table 2. The the tunnel sidewalls and rotate with the model. The axis grit was located at 2-percent chord on the upper surface of rotation coincided approximately with the midchord and 5-percent chord on the lower surface. It was of the model, which was mounted horizontally between sparsely distributed along 3-mm (0.1-in.) wide strips the plates. The gaps between the model and the plates applied to the model with lacquer. The scaled, NACA were sealed. standard roughness consisted of 0.211-mm (0.0083-in.) grit applied from 8-percent-chord arc length on the Models upper surface to 8-percent-chord arc length on the Advanced Technologies, Incorporated, Newport News, lower surface for all Reynolds numbers. The grit size Virginia fabricated the two wind-tunnel models from was scaled from the NACA standard-roughness grit solid aluminum using a numerically controlled milling size by the ratio of the model chord used in the present machine. The models had a chord of 457 mm (18.0 in.) investigation to the model chord used in the NACA and a span of 91 cm (36.0 in.). The measured model tests. contours were within 0.1 mm (0.005 in.) of the prescribed shapes. Results Each model included a total of 120 chordwise pressure Pressure Distributions ports over the upper and lower surface. Upper- and Typical measured pressure distributions for the S825 lower-surface orifices were located to one side of and S827 airfoils are shown in Fig. 4 for an angle of midspan, staggered along a line approximately 10 attack of 3.0 degrees. The integrated pressure degrees from the free steam flow direction. All the distributions then yielded cl versus angle of attack orifices were 0.51 mm (0.020 in.) in diameter with their plots, which were documented for the complete test axes perpendicular to the airfoil surface.
Details
-
File Typepdf
-
Upload Time-
-
Content LanguagesEnglish
-
Upload UserAnonymous/Not logged-in
-
File Pages12 Page
-
File Size-