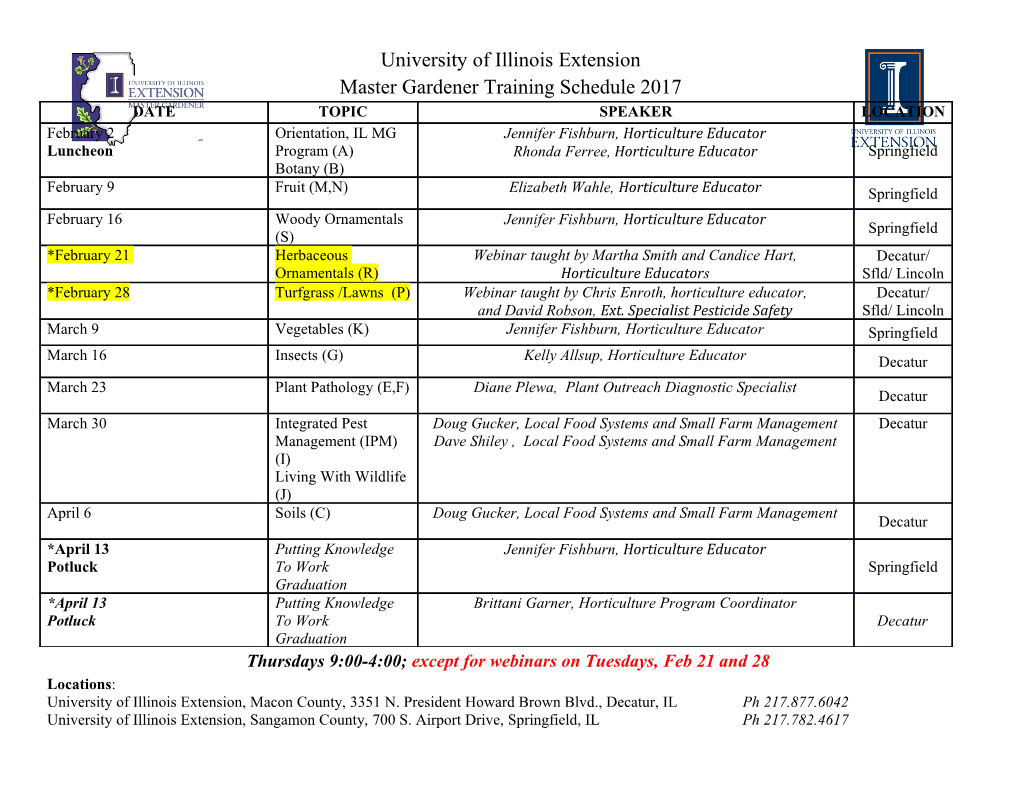
4368 J. Phys. Chem. C 2007, 111, 4368-4374 ZSM-5 Coatings on â-SiC Monoliths: Possible New Structured Catalyst for the Methanol-to-Olefins Process S. Ivanova,* B. Louis, B. Madani, J. P. Tessonnier, M. J. Ledoux, and C. Pham-Huu Laboratoire des Mate´riaux Surfaces et Proce´de´s pour la Catalyse, UMR 7515 du CNRS, 25 rue Becquerel 67087 Strasbourg Cedex 2, France ReceiVed: NoVember 14, 2006; In Final Form: January 10, 2007 Structured zeolite/silicon carbide composites were succesfully synthesized by ZSM-5 coatings deposited on macroscopic â-SiC foams with medium surface area. A homogeneous coverage of the support (30 wt % zeolite) by ZSM-5 crystals, having 1 µm average size, was reached after a double-coating procedure. The ZSM-5/â-SiC composite materials were characterized by BET, XRD, SEM, and H/D exchange methods. 27Al MAS NMR analysis revealed that all aluminum was present in a tetrahedral coordination, thus sitting in the zeolite framework. The existence of a nanoscopic layer of silica and silicon oxycarbide on the surface of the support ensures the strong anchoring of the zeolite crystals on the â-SiC substrate. The lack of secondary chemical reaction between the synthesis solution and the support allows a precise control of the Si/Al ratio in the final zeolite. The use of ZSM-5 coated â-SiC foam packings in the methanol-to-olefins reaction presents substantial activity/selectivity improvements compared to conventional zeolite packings. Moreover, the structured composites exhibit a higher stability toward deactivation by coking, compared to the powdered form of the zeolite. 1. Introduction SCHEME 1: Main Reaction Steps of the Methanol Conversion to Hydrocarbons In heterogeneous catalysis it is already recognized that a catalyst is not a new chemical compound, but a finely designed material. Chemical composition can efficiently work only in combination with well-organized micro- and macrostructure of the material. Moreover, the texture and mechanical properties of the catalyst strongly influence the appropriate choice of the allowing control of consecutive reactions and resulting in chemical reactor and the technology employed,1,2 and hence the increased product selectivity. Therefore, the development of investment cost. novel materials suitable for the design of structured catalytic beds is warranted. This is a valuable alternative to conventional Zeolites are known to possess a microporous structure with fixed beds and slurry catalytic reactors.3 Despite the increasing well-defined pore architecture and size. Moreover, the zeolites interest in structured catalytic beds, only a few practical can be loaded via ion exchange by cations to suit the require- applications have been reported consisting of structured zeolitic ments of a specific chemical transformation. Therefore, a control packings.4-6 of chemical composition and microstructure is ensured by zeolite Structured zeolitic packings can be prepared via a binderless synthesis. In contrast, the macrostructure of zeolite catalyst 7-9 10-19 packings is still fairly undefined. Zeolites are used in catalytic hydrothermal synthesis on metal grids or ceramics. Even fixed beds, randomly packed by powdered microgranules or well-covered, metallic substrates are known to catalyze many extrudated pellets a few millimeters in size. The main drawbacks reactions, and thus contribute to deep oxidation pathways. of fixed beds are (a) the high-pressure drop during the gas Another drawback of metallic supports for zeolite deposition passage through the catalytic bed, (b) limited heat and mass is connected to the big difference in the dilatation coefficients transfers, (c) flow maldistribution leading to loss of selectivity, of metals compared to silicates, which may cause a zeolite and (d) susceptibility to fouling by dust. attrition due to its detachment under temperature changes during reactor operation.20 Moreover, prior to the synthesis, the Furthermore, the use of inorganic binders for shaping the final chemical pretreatment of the metal support is crucial to increase zeolite material presents an important limitation, since these the chemical affinity between the zeolite and its carrier,21,22 thus binders partly block access to the zeolite active centers, which complicating the preparation of the catalyst. Metal grid supports diminish the zeolite efficiency in catalytic reactions. also exhibit high intrinsic weight, which is detrimental for the During the past decade there has been a growing interest in productivity per weight of the reactor unit. catalytic reactor engineering based on structured catalytic beds.3 Crystallization of zeolites on porous glass supports in alkaline Compared to traditional randomly dumped packed bed reactors, media has already been reported.16,23 The glass matrix is partially structured catalytic beds provide improved hydrodynamics. This transformed into zeolitic material, and as a result a biphasic leads for example to narrower residence time distribution, composite material with a bimodal pore system can be obtained. The synthesis procedure described takes place in basic media * To whom correspondence should be addressed. Telephone: 10-13 +33 3 90 242675. Fax: +33 3 90 242674. E-mail: ivanovas@ at high pH values. The strong basicity of the zeolite growth ecpm.u-strasbg.fr. medium renders less effective the use of silica or alumina 10.1021/jp067535k CCC: $37.00 © 2007 American Chemical Society Published on Web 03/01/2007 ZSM-5 Coatings on â-SiC Monoliths J. Phys. Chem. C, Vol. 111, No. 11, 2007 4369 petrochemicals and gasoline.29-31 The MTO reaction was chosen for two reasons. First, light C2-C4 olefins are valuable intermediates in the chemical industry and their demand is still 32 rising. Second, the yield in C2-C4 olefins is controlled by the contact time of the reactants with the catalyst. Therefore, the light olefins have to be quickly removed from the catalyst surface to prevent them from reacting further.33 On the basis on these considerations, as-prepared HZSM-5/SiC structured composite can be an effective MTO catalyst. 2. Experimental Section 2.1. â-SiC Characteristics. Silicon carbide was prepared by the gas-solid reaction between solid carbon and SiO vapors in the temperature range 1200-1400 °C according to the shape- memory synthesis developed by Ledoux et al.24,34 The method allows the synthesis of silicon carbide with different sizes and shapes, depending on their subsequent uses, and having specific surface areas (SSAs) up to 150 m2/g. SiC was used in its â-crystalline structure since the SSA is higher than the one from R-SiC.26 The support was used either in the form of extrudate pellets (2 × 6 mm in size) or as a foam (25 × 40 mm) having a pore openning of 2300 µm (Sicat Company, Otterswiller, France). Figure 1 shows the honeycomb structure of a SiC monolith. Prior to the synthesis, the support was calcined at 900 °Cinairfor2or5hinorder to form a nanoscopic layer Figure 1. Cellular structure of SiC foam monolith. of SiO2 on its surface. This layer ensures a strong interaction between the support and the gel during the zeolite synthesis - supports due to their partial dissolution, leading both to the through a superficial dissolution precipitation sequence. deterioration of the support and a modification of the gel 2.2. Preparation of the Zeolite Coatings. The open-cell SiC composition.16 foams or extrudates (5 g) were placed in a Teflon-lined stainless Silicon carbide exhibits the necessary intrinsic properties steel autoclave (70 mL). Its volume was partially filled with required to become a valuable candidate as zeolite support: high the reaction mixture (50 mL). The solution was prepared by thermal conductivity and mechanical strength, resistance to adding dropwise tetraethylorthosilicate (TEOS, 98%, Sigma- oxidation, chemical inertness, and ease of shaping.24-26 All these Aldrich) to an aqueous solution containing tetrapropylammo- advantages tend to indicate that SiC support can replace classical nium hydroxide (TPAOH, 1 M, Sigma-Aldrich), sodium supports such as alumina, silica, and carbon, especially in highly chloride, and sodium aluminate (NaAlO2, 98%, Riedel-de Hae¨n). endothermic and/or exothermic reactions.27,28 Silicon carbide The gel composition in molar ratios was as follows: TPAOH/ possesses a light weight which significantly reduces the fraction TEOS/NaCl/NaAlO2/H2O 2.16:5.62:3.43:0.13:1000. The gel of useless weight of the support within the overall weight of containing the support was aged for4hatroom temperature. the catalyst. Finally, â-SiC synthesized according to shape- Then the autoclave was put in an oven and the temperature was memory synthesis (SMS)26 also exhibits a medium surface area raised within1hto440K;thesynthesis took place during which renders it suitable for dispersing zeolite crystals on its 48 h under autogenous pressure. After cooling, the ceramic- surface. zeolite composite was filtered, washed several times with The aim of this work was to prepare new structured and distilled water, and sonicated (45 kHz) for 15 min to remove binderless ZSM-5 coatings via an in situ hydrothermal synthesis residual gel or loosely attached crystals. Finally, the solid was on SiC supports. Silicon carbide was also used in the present dried at 373 K overnight. study as a foam monolith owing to its open structure which A second synthesis was performed by repeating the coating significantly reduces the pressure drop along the catalyst bed. procedure, placing the ceramic-zeolite composite in a fresh The zeolite crystals were made to grow onto the structured solution having the same molar composition. supports kept in the synthesis mixture. Then, the zeolite/SiC The organic template was removed by treating the material composite was to be assessed for the catalytic conversion of in air at 773 K for 5 h. The composite was then ion-exchanged -1 methanol into olefins (MTO reaction; see Scheme 1). The with an aqueous 1 mol L NH4Cl solution (100 mL) for 16 h conversion of raw methanol to hydrocarbons over MFI-based at 338 K, and subsequently calcined at 773 K for5htoproduce catalysts is an alternative technology for the manufacture of the acidic H-form of the zeolite.
Details
-
File Typepdf
-
Upload Time-
-
Content LanguagesEnglish
-
Upload UserAnonymous/Not logged-in
-
File Pages7 Page
-
File Size-