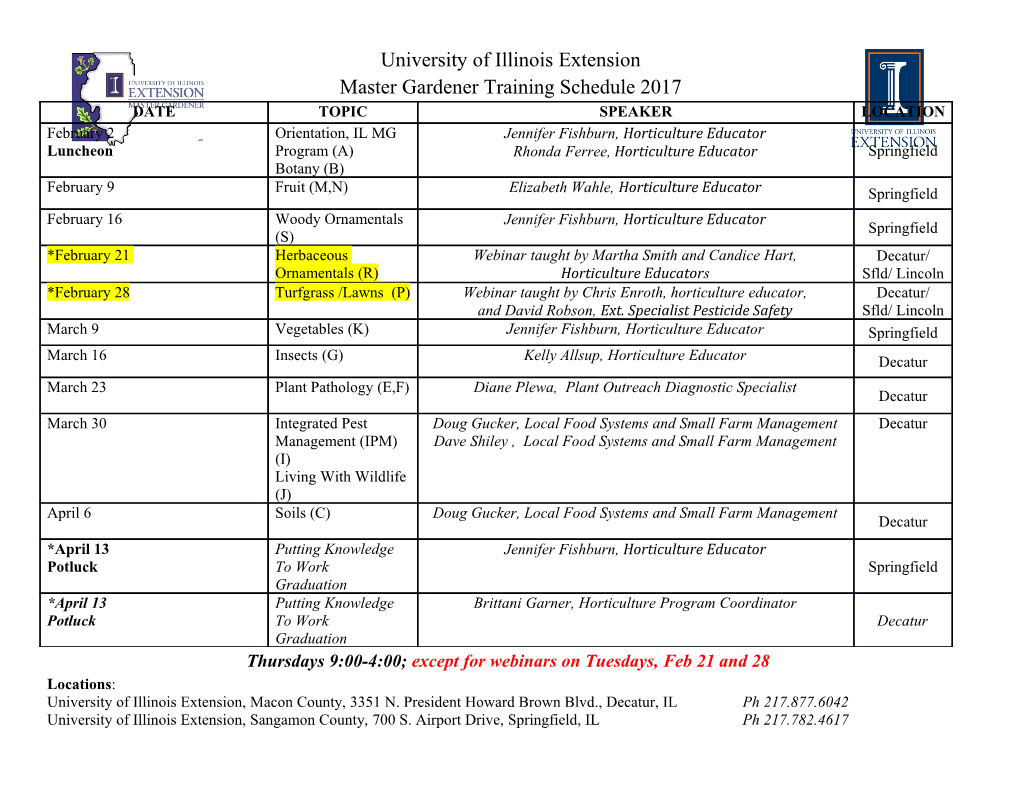
BY S. MÜLLER, M. DEICKE, & RIK W. DE DONCKER A viable alternative to ADJUST SPEED over a wide range at MINIMAL COST HE AIM OF WIND TURBINE SYS- TEMS DEVELOPMENT is to contin- T uously increase output power. A few years ago, the rated output power of production-type units reached 200 kW. By 1999, the average output power of new installations climbed to 600 kW. The largest series production units today are specified to deliver 1.5-MW output power (Table 1). It is anticipated that in the near fu- ture, power rating of wind turbines will increase fur- ther, especially in offshore applications. For example, the prototype of a Nordex N80 with a rated power of 2.5 MW was installed in March 2000 near Aachen. Many low-power wind turbines built to-date were constructed according to the “Danish concept” (Fig. 1), in which wind energy is transformed into electrical en- ergy using a simple squirrel-cage induction machine directly connected to a three-phase power grid. The ro- tor of the wind turbine is coupled to the generator shaft with a fixed-ratio gearbox. Some induction generators IEEE INDUSTRY APPLICATIONS MAGAZINE • MAY|JUNE 2002 •use WWW.IEEE.ORG/IAS pole-adjustable winding configurations to enable COURTESY OF ENRON WIND GMBH 26 operation at different synchronous speeds. However, at 1077-2618/02/$17.00©2002 IEEE any given operating point, this Danish TABLE 1. WIND POWER STATIONS CURRENTLY IN OPERATION WITH turbine basically has to operate at con- RATED POWER ABOVE 1.0 MW [1] stant speed. The construction and performance of Nominal Rotor Manufacturer/ Rotor Speed Power Diameter fixed-speed wind turbines very much de- Type Control Control pends on the characteristics of mechani- in (kW) (m) cal subcircuits, e.g., pitch control time DeWind D6 1,250 Pitch Variable 64 constants, main breaker maximum switching rate, etc. The response time of AN BONUS 2,000 CombiStall Const 76 some of these mechanical circuits may be in the range of tens of milliseconds. As a Nordex N80 2,500 Pitch Variable 80 result, each time a gust of wind hits the Enron EW1.5s 1,500 Pitch Variable 70 turbine, a fast and strong variation of electrical output power can be observed. Enercon E-66 1,800 Pitch Variable 70 These load variations not only require a Enron EW3.6 3,600 Pitch Variable 100 stiff power grid to enable stable opera- tion, but also require a sturdy mechanical Pro&Pro MD70 1,500 Pitch Variable 70 design to absorb high mechanical stresses. This strategy leads to expensive Vestas V80 2,000 Pitch Variable 80 mechanical construction, especially at high-rated power. Adjustable Speed Generators Modern high-power wind turbines are ca- pable of adjustable speed operation. Key Grid advantages of adjustable speed generators (ASGs) compared to fixed-speed genera- tors (FSGs) are: IEEE INDUSTRY APPLICATIONS MAGAZINE • MAY|JUNE 2002 • WWW.IEEE.ORG/IAS PGen I They are cost effective and provide simple pitch control; the control- ling speed of the generator (fre- Pmech quency) allows the pitch control time constants to become longer, ASG reducing pitch control complexity Compensation and peak power requirements. At lower wind speed, the pitch angle is 1 usually fixed. Pitch angle control is performed only to limit maximum Fixed speed “Danish” concept. output power at high wind speed. I They reduce mechanical stresses; gusts of wind can be absorbed, i.e., energy is stored in the mechanical inertia of the turbine, creating an “elasticity” that re- duces torque pulsations. 1.2 I They dynamically compensate for torque and power Pel pulsations caused by back pressure of the tower. This N 1.0 back pressure causes noticeable torque pulsations at a rate equal to the turbine rotor speed times the num- 0.8 ber of rotor wings. 0.6 I They improve power quality; torque pulsations can be reduced due to the elasticity of the wind turbine 0.4 system. This eliminates electrical power variations, P/P Electrical Power i.e., less flicker. 0.2 Wind Speed I They improve system efficiency; turbine speed is ad- justed as a function of wind speed to maximize output 0 0 0.2 0.4 0.6 0.8 1.0 1.2 1.4 1.6 1.8 power. Operation at the maximum power point can be Turbine Speed n/n realized over a wide power range. Fig. 2 illustrates N 2 typical output power-speed curves as a function of tur- Electrical output power as a function of turbine speed. Pa- bine speed and wind speed. As a result, energy effi- ciency improvement up to 10% is possible (Fig. 3). rameter curves are plotted for different wind speeds. Maxi- I They reduce acoustic noise, because low-speed opera- mum power point tracking (red curve) can be realized with tion is possible at low power conditions. a speed variable system. 27 I Profit: Pitch Control Inverter output filters and EMI filters are rated for 1 100% p.u. output power, making filter design difficult and Power costly. I Converter efficiency plays an important factor in to- Profit: Speed tal system efficiency over the entire operating range. Variation Reference: Stall, Doubly Fed Induction Generator ASG System Constant Speed Recent developments seek to avoid most disadvantages of direct-in-line converter based ASGs. Fig. 5 shows an alter- native ASG concept that consists of a doubly fed induction Wind Speed 3 generator (DFIG) with a four-quadrant ac-to-ac converter based on insulated gate bipolar transistors (IGBTs) con- Efficiency gains due to adjustable speed wind turbines. nected to the rotor windings. Compared to direct-in-line systems, this DFIG offers the following advantages: I Reduced inverter cost, because inverter rating is typ- In addition, most ASG-based wind turbines can offer is- ically 25% of total system power, while the speed land-operation capability. Island operation is difficult to range of the ASG is ±33% around the synchronus realize with the Danish concept. speed (Fig. 6). I Reduced cost of the inverter filters and EMI filters, Direct-in-Line ASG System becuase filters are rated for 0.25 p.u. total system One possible implementation scheme of ASGs is shown in power, and inverter harmonics represent a smaller Fig. 4. A synchronous generator is used to produce vari- fraction of total system harmonics. able-frequency ac power. A power converter connected in I Improved system efficiency; Table 2 shows the sys- series with the ASG transforms this variable-frequency ac tem losses for different windmill concepts. The losses power into fixed-frequency ac power. Although these di- are shown separately for the generator and for the rect-in-line systems have been built up to 1.5 MW, several IGBT inverters. Approximately 2-3% efficiency im- disadvantages are apparent: provement can be obtained. I The power converter, which has to be rated at 1 p.u. I Power-factor control can be implemented at lower total system power, is expensive. cost, because the DFIG system (four-quadrant con- verter and induction machine) ba- sically operates similar to a Grid synchronous generator. The con- verter has to provide only excita- tion energy. In addition, compared to silicon-con- PGen trolled rectifier (SCR) based Kramer Pmech drives [3], the DFIG with a four-quadrant 3~ = SG converter in the rotor circuit enables de- = 3~ coupled control of active and reactive Gear Box Filter power of the generator. 4 Dynamic Model of a Doubly Fed Induction Direct-in-line wind turbine system. Generator To develop decoupled control of active and reactive power, a DFIG dynamic Grid model is needed. The construction of a DFIG is similar to a wound rotor induc- tion machine (IM) and comprises a three-phase stator winding and a three-phase rotor winding. The latter is PGen DFM fed via slip rings. The voltage and torque equations of the DFIG in a stationary ref- erence frame are: s*PGen s*PGen 3~ = ∂ψ Sj = vri=⋅ +j ={}123,, 3~ Filter Sj S Sj dt (1) IEEE INDUSTRY APPLICATIONS MAGAZINE • MAY|JUNE 2002 • WWW.IEEE.ORG/IAS Converter 5 28 Doubly fed induction generator wind turbine system. jXssi jXssσI vb vs vs vm Synchronous Machine-Type Induction Machine-Type Equivalent Circuit Equivalent Circuit i′ ′ R ′ i R is is i R is Xs IM ′ ′ Xsσ X Rσ ′ i v v v R M s vb vs M s is XM is 6 7 Maximum output power as a function of slip s (left) or Equivalent circuit and vector diagram of the (synchronous) speed ratio n/n0 (right). DFIG. (4) ∂ψ ⋅ π ′ = ′ ⋅ ′ +=Rj {} −⋅ϑϑ − ⋅ −2 vriRj R Rj j 123,, vv12sin sin dt 2 3 v =⋅ (2) d ⋅ π 3 −⋅ϑ +2 v 3 sin 3 dψ 3 =⋅p ⋅ j Tel∑ i j . 2 j =1 dϑ (5) (3) yields IEEE INDUSTRY APPLICATIONS MAGAZINE • MAY|JUNE 2002 • WWW.IEEE.ORG/IAS In these equations, all quantities are referred to the =+⋅ stator, i.e., transformed rotor quantities (superscript ′) are vvdq jv used. Transforming these equations from three-phase to (6) two-phase components and subsequently rotating all vari- ables into a synchronous reference frame (dq) according to ∂ψ vri=⋅+S +⋅⋅j ωψ S S S dt S S ⋅ π ⋅+⋅−ϑϑ2 (7) vv12cos cos =⋅2 3 v d ∂ψ′ ⋅ π R 3 +⋅ϑ +2 vri′ = ′ ⋅ ′ + +⋅j ωψ ⋅′ v 3 cos R R R R R 3 dt (8) P/Pr P/Pr 1 1 PG PG 0.75 0.75 PS PS 0.5 0.5 0.25 0.25 PR PGC PR PGC Slip n/n0 0.3 0.2 0.1 –0.1 –0.2 –0.3 0.7 0.8 0.9 1.1 1.2 1.3 -0.25 -0.25 8 Induction machine type equivalent circuit and vector diagram of the DFIG.
Details
-
File Typepdf
-
Upload Time-
-
Content LanguagesEnglish
-
Upload UserAnonymous/Not logged-in
-
File Pages8 Page
-
File Size-