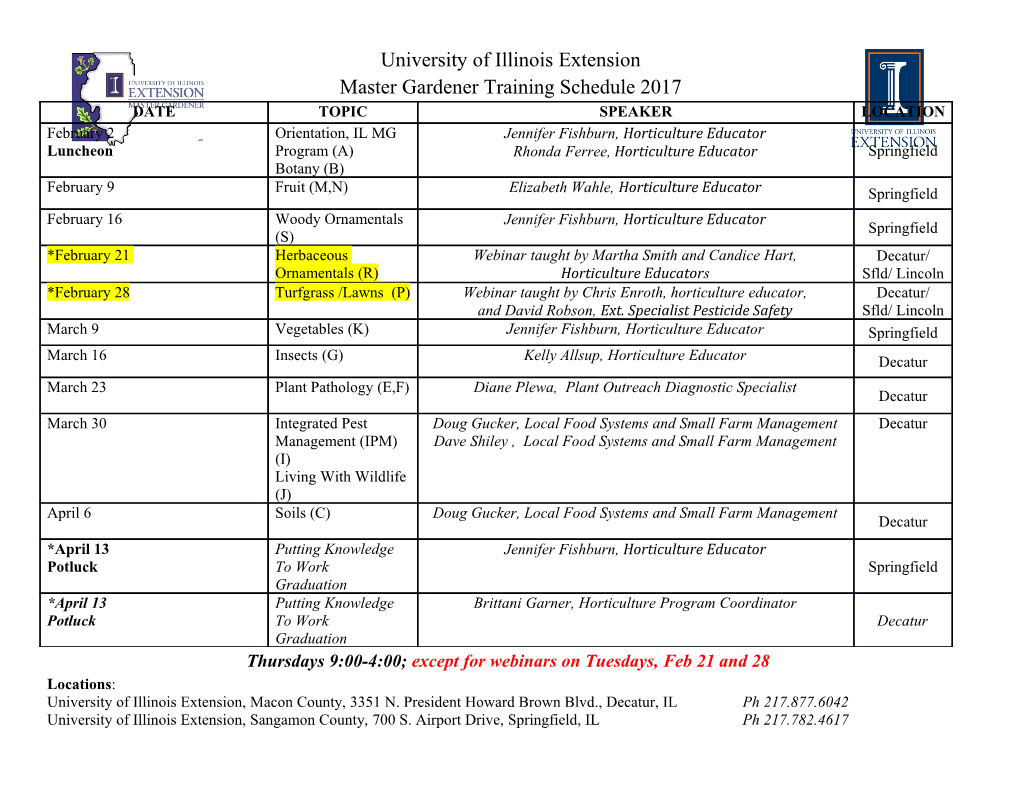
Mullite Preparation from Kaolin Residue M.I.Brasileiro1;D.H.S.Oliveira2;H.L.Lira3;L.N.L.Santana3;G. A.Neves3; A.P.Novaes4 J.M. Sasak5 1Universidade Federal de Campina Grande, UFCG/DEQ – PB, Departamento de Engenharia Química - Aprígio Veloso, 820 – CEP 58109-970 – Campina Grande, PB, Brasil. 2UFCG/DEMa/PIBIC/CNPq – Departamento de Engenharia de Materiais, PB, Brasil. 3UFCG/DEMa - Departamento de Engenharia de Materiais, PB, Brasil. 4SENAI – CTCmat/Criciúma – SC, Brasil. 5UFC – Universidade Federal do Ceará, CE, Brasil. Keywords: kaolin waste; alumina; ball-clay; mullite; sintering. Abstract: In the process of kaolin improvement to types of residue are generated and dispose in the environment. The first residue, about 70%wt, generated from the washing of the kaolin and the second generated residue from the improvement in sieve 200 mesh (0.074mm), of the remaining of the washed kaolin 30%. These residues can present excellent qualities to be used as raw materials rich in kaolinite. Kaolinite when is submitted to heat give two stable phases: mullite and crystobalite. The properties of mullite, such as, low thermal expansion, low dielectric constant and high mechanical resistance, make this material as a good candidate to be applied in electronic products and in structural high temperature uses. In this work, compositions with residue from kaolin, alumina and ball-clay were studied to obtain mullite. The compositions were established starting from proportion between silica and alumina to obtain mullite (2SiO2.3Al2O3). The samples were made by pressing processing with 27 MPa and sintering at temperatures of 1350 and 1500°C, with heating rate of 10°C/min. Through the results from chemical analysis of the formulated masses, it can be verified that the proportions of the oxides were close to the stoichiometric of the mullite and that the sintering, at studied temperatures, give the formation of mullite, and confirmed by the DRX analysis. The preliminary results showed that the compositions with low alumina content and submitted to a high temperatures, presented the best results. Introduction Mullite is a unique thermodynamically stable phase in the binary system Al2O3-SiO2 [1] and due to its excellent properties, such as, creep resistance at high temperature, chemical stability, low dielectric coefficient and low thermal expansion has called attention from several researchers [2,3]. As a mineral, mullite is rare in the nature [4] and the reserves are not sufficient to supply the crescent new applications. This is the reason for several researchers looking for process to obtain mullite from Al2O3-SiO2 or from some minerals that contain Al2O3 and SiO2 in their compositions [1]. An alternative material is study through calcination of a mix of kaolin residue, alumina and ball-clay, in an appropriate proportion of the oxides, taking in account the amount of SiO2 and Al2O3 to obtain mullite. In the improvement of primary kaolin two types of residue are disposed in the environment. The first one, with 70%wt, are generated during the washing of the raw kaolin and the second, with 30%wt, are produced during the sieve process in a mesh 200 (0.074mm). The aim of this study is to obtain mullite from the residue produced by kaolin industry, alumina and ball-clay and to characterize by physical and mechanical properties of the produced mullite. Materials and Method Materials: In this work it was used a residue from primary kaolin industry supplied by Caulisa Industria S/A, a clay provided by Armil Minerios Ltda. and calcined alumina S4G, supplied by Alcan. Treatment and characterization of the raw materials: The residue and ball-clay were dried at 110ºC for 24 hours, until constant weight and passed in a sieve 200 mesh to submitted to chemical analysis and X-ray diffraction, using a Siemens/Brucker-AXS, with CuKα radiation. Formulation and characterization of the masses: The masses formulations were set up taking in account the silica and alumina content of the raw materials. The compositions were submitted to a sieve 100mesh (0.150mm) and characterized by XRD analysis and particle size by laser. Processing and characterization of the specimens: The masses were mixed with ethylic alcohol and dry at room temperature. After dry the lumps were crushed and passed through a sieve with 100 mesh. Powder compacts were formed by uniaxially pressing at 27 MPa. The final dimension of green compacts was 6.0x2.0x0.5cm3. The compacts were then sintered in an electrical oven at various temperatures from 1350oC to 1500oC for 1 h in air. The heating rate was 10oC/min. After sintering the specimens were submitted to measurement of the following properties: porosity, linear shrinkage, water absorption, apparent density and flexural rupture strength. The flexural strength of specimens was determined by the three-point bending technique, at a loading rate of 0.5 mm/min. The result is the average of five specimens. Results and Discussion The Table 1 present the chemical composition of the raw materials. From Table 1 it can be observed that the residue contain basically silica (57.11%) and alumina (40.67%), also ball- clay, with 66.14% of silica and 32.00% of alumina. According to Chen at al [5], the reaction, 2SiO2 + Al2O3 + 2H2O + 2 Al2O3 Æ 3 Al2O3 +2SiO2 + 2 H2O, is observed during the firing of kaolin+alumina. By this reaction it can assume that SiO2 from kaolin can react completely with alumina to produce mullite and in the case of the residue it is necessary an excess of alumina to reach with all the silica. Table 1 – Chemical composition of the raw materials. Raw materials % SiO2 % Al2O3 % Fe2O3 % Na2O % K2O Kaolin residue 57.11 40.67 0.04 0.53 1.65 Ball- clay 66.14 32.00 1.85 - - Alumina 0.04 99.4 0.04 0.37 0.23 The Table 2 presents the compositions studied in this work. The Table 3 presents the results for particle size distribution of the powders for each composition. From of the Table 3, it can observed that particle size distribution is very similar for the compositions I and II. The compositions III and IV present particle size lower than for the compositions I and II, this is due to the ball-clay with a high content of particle size lower than 2µm. Table 2 – Compositions of the specimens (% wt) Compositions Kaolin Residue Ball clay Alumina I 74.12 - 25.88 II 66.38 - 33.62 III 69.00 4.00 27.00 IV 67.00 7.00 26.00 Table 3 – Particle size (µm) for different composition 10% of 50% of 90% of 100% of Composition particles particles particles particles below below below below I 1.74 16.60 42.78 71.00 II 1.74 14.74 41.17 71.00 III 1.07 7.42 36.18 90.00 IV 1.26 8.44 36.72 71.00 Table 4 present the chemical compositions of the formulated masses. It can be observed a high content of silica and alumina that is excellent to obtain mullite. Table 4 – Chemical composition (%) of the formulated pastes Specimens SiO2 Al2O3 Fe2O3 Na2O K2O TiO2 L.O.* Composition I 39.25 49.72 0.36 0.26 3.27 0.06 6.92 Composition II 34.80 55.22 0.32 0.21 2.94 0.05 6.32 Composition III 38.91 50.36 0.42 0.24 3.13 0.10 6.69 Composition IV 40.91 47.97 0.42 0.23 3.25 0.12 6.94 *L.O.- Loss of ignition Figures 1, 2, 3, and 4 present the XDR patterns of the compositions (I, II, III e IV) fired at different temperatures. Composition II M - Mullite Composition I M - Mullite C - Cristoballite 5000 A - Alumina A - Alumina C - Cristoballite 4500 Q - Quartz M Q - Quartz M 4000 M M M M A M 3500 M A M A A M M A M M M M A A 1500°C M M MM A 3000 M M M A M 1500°C MM M M M M A A M M A 2500 M A M MA A M M M A MA C M M M M M M A 1450°C M M MM 2000 1450°C M M M M A A A M A A M M A 1500 A M M A M M M M M 1400°C C M M M M M M M C M A M 1400°C M M M MM M 1000 M A Q A M C M A A A AM A M M 500 M QM M MM A A M M M C M 1350°C M MM M 1350°C M M M MM M 0 0 102030405060 0 102030405060 20 degrees 20 degrees Fig.1: The DRX patterns of the composition Fig.2: The DRX patterns of the composition I for different temperature. II for different temperature. Composition III Composition IV M - Mullite 5500 M - Mullite 5500 C - Cristoballite C - Cristoballite 5000 5000 A - Alumina 5000 A - Alumina M Q - Quartz Q - Quartz 4500 4500 M A M M 4000 M 4000 AM M M M MA A 3500 A A 3500 M M M M M M MA 1500°C M MM M 1500°C A M M MM 3000 M 3000 A A M M A A M M M 2500 A M A 2500 M M M M A M A 1450°C M M M M M M M C M M M M 2000 A 2000 1450°C M M M MAM M A A M C M M M M A 1500 1400°C M M MM M 1500 A A M A C M M M 1400°C M M M M M M M 1000 M A A A 1000 M A A A A M Q M M M M Q M M M A 500 C 500 C M M M M M 1350°C MM M M M MM M 1350°C M M 0 0 0 102030405060 0 102030405060 20 degrees 20 degrees Fig.3: The DRX patterns of the composition Fig.4: The DRX patterns of the composition III for different temperature.
Details
-
File Typepdf
-
Upload Time-
-
Content LanguagesEnglish
-
Upload UserAnonymous/Not logged-in
-
File Pages6 Page
-
File Size-