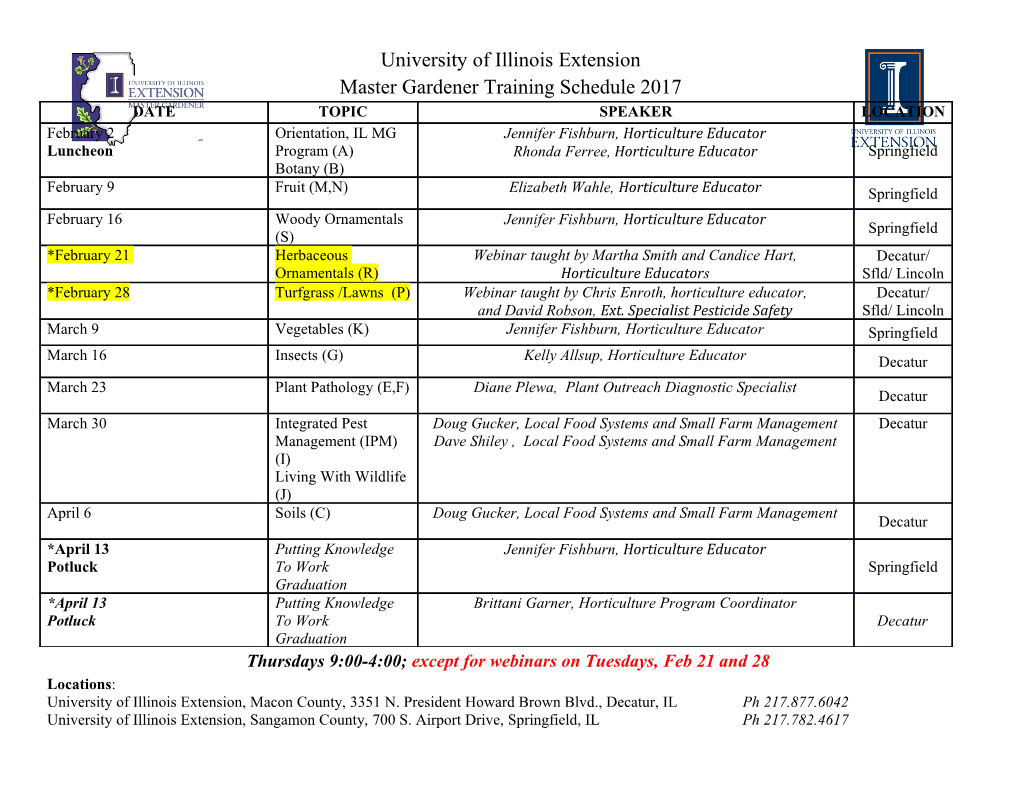
Application Note 53 January 1993 Micropower High Side MOSFET Drivers Tim Skovmand Portable electronic equipment, such as notebook and 5V palmtop computers, portable medical instruments and battery powered tools, are increasingly dependent upon DS1 VS DS2 efficient power management to meet the challenge of (12V) (12V) extracting more useful energy (time) from less battery IRLR024 G1LTC1155 G2 MTP3055EL volume and weight. One link in the power management chain which has 5V IN1GND IN2 5V received increasing scrutiny, as power supply efficiencies LOAD LOAD soar above 90%, is the logic controlled power switch. ON/OFF ON/OFF Large sections of a typical notebook computer system, for AN53 • TA01 example, are powered via topside or “high side” MOSFET Figure 1. High Efficiency Dual High Side Switch switches. These switches can become significant sources of power loss if not properly designed. driver is the most efficient means of powering complex At first glance, P-channel MOSFETs appear to be the electrical loads. Switch efficiencies in the 98% to 99%+ natural choice for high side switching. Unfortunately, the range are easily attained with practical and economic N-channel switches. RDS(ON) exhibited by most P-channels is prohibitively high. (Mother Nature has decreed that electron mobility MOSFET SWITCH SELECTION shall exceed hole mobility in silicon by about 2.5 times, so that a P-channel MOSFET with the same RDS(ON) and N-channel MOSFET switches fall into two main categories: voltage rating as its N-channel counterpart is roughly 2 to logic-level and standard. 3 times larger and more expensive.) Also, the gate drive for a P-channel switch is limited to the supply voltage which Logic-Level MOSFET Switches may not fully enhance the switch as the supply voltage Although there is some variation among manufacturers, drops. logic-level MOSFET switches are typically rated with VGS N-channel MOSFETs may seem less attractive because = 4.0V with a maximum continuous VGS rating of ±10V. they require a gate voltage higher than the power supply RDS(ON) and maximum VDS ratings are similar to standard voltage to become fully enhanced in high side switching MOSFETs and there is generally little price differential. applications. This limitation is eliminated by high side Logic-level MOSFETs are frequently designated by an “L” MOSFET drivers such as the LTC1155, which have built- and are usually available in surface mount packaging. in charge pumps to fully enhance N-channel switches. LOGIC-LEVEL STANDARD N-CHANNEL N-CHANNEL The LTC1155, dual micropower MOSFET driver, gener- MOSFET SWITCH MOSFET SWITCH ates 12V from a 5V rail to fully enhance logic-level N- channel switches with no external components required µ (see Figure 1). Further, the supply current is typically 85 A RDS (ON) RATED AT VGS = 4V. RDS (ON) RATED AT VGS = 10V. with the switch fully enhanced and 8µA with the LTC1155 MAX VGS = ±10V. MAX VGS = ±20V. AN53 • TA02 in the standby mode (both inputs off). This combination of Figure 2. Logic-Level and Standard N-channel low-drop N-channel MOSFET switch and micropower MOSFET VGS Ratings AN53-1 Application Note 53 Standard MOSFET Switches Each driver works with either logic-level or standard MOSFETs over a portion of the supply voltage range and Standard N-channel MOSFET switches are rated with VGS ± is designed to work with 12V VGS Zener clamp diodes = 10V and are generally restricted to a maximum of 20V. when the supply range exceeds 9V as shown in Figure 3. Again, there is some variation among MOSFET manufac- turers and individual data sheets should be consulted APPLICATIONS before making a final selection. (E.g., MOSFETs with ±30V maximum VGS ratings can be used without VGS voltage Powering Large Capacitive Loads clamps.) Electrical subsystems in portable battery powered equip- MOSFET/Driver Selector Guide ment are typically bypassed with large filter capacitors to reduce supply transients and supply induced glitching. If Table 1 is a guide which simplifies the selection of a not properly switched however, these capacitors may MOSFET switch and micropower driver for a particular themselves become the source of supply induced glitching. supply voltage range. A family of drivers, including a single, dual and quad, are available for operation in the For example, if a 100µF capacitor is powered through a 4.5V to 18V range. A related device, the LTC1153, elec- P-channel switch as shown in Figure 4, and the slew rate tronic circuit breaker, also operates in the 4.5V to 18V of the switch is 0.1V/µs, the current during start-up is: range. ISTART = C(dV/dt) The LTC1157, dual 3.3V micropower MOSFET driver, is = (100 x 10-6)(1 x 105) designed specifically for low voltage operation between 2.7V and 5.5V. Finally, the LTC1255, dual high side MOSFET = 10A driver, is designed to work in the 9V to 24V automotive and industrial range. Obviously, this is too much current for the regulator to supply and the output glitches by many volts! >9V (5.0V) SUPPLY >5.4V LT1121-5 GLITCH DS1 VS DS2 + + STANDARD STANDARD 0.1µF 1µF N-CHANNEL G1 G2 N-CHANNEL MOSFET MOSFET 12V* LTC1155 12V* P-CHANNEL SWITCH OUT >9V IN1GND IN2 >9V LOAD LOAD + CLOAD ON/OFF ON/OFF 100µF AN53 • TA04 * 1N5242B (THROUGH HOLE) OR MMBZ5242B (SURFACE MOUNT) ZENERS AN53 • TA03 Figure 4. Power Up Supply “Glitch” Produced by Fast Figure 3. Adding 12V VGS Clamps when VS > 9V Starting a Large Capacitive Load Table 1. MOSFET/Driver Selector Guide DEVICE DESCRIPTION SUPPLY RANGE USE LL FET USE STD FET STD FET & 12V CLAMP LTC1153 Electronic Circuit Breaker 4.5V – 18V 4.5V – 5.5V 5.5V – 9V 9V – 18V LTC1154 Single Micropower MOSFET Driver 4.5V – 18V 4.5V – 5.5V 5.5V – 9V 9V – 18V LTC1155 Dual Micropower MOSFET Driver 4.5V – 18V 4.5V – 5.5V 5.5V – 9V 9V – 18V LTC1156 Quad Micropower MOSFET Driver 4.5V – 18V 4.5V – 5.5V 5.5V – 9V 9V – 18V LTC1157 Dual 3.3V high Side/Low Side Driver 2.7V – 5.5V 2.7V – 4.0V 4.0V – 5.5V NA LTC1255 Dual Industrial MOSFET Driver 9V – 24V NA NA 9V – 24V AN53-2 Application Note 53 paralleled MOSFETs with 1k resistors to decrease the >5.4V LT1121-5 + + possibility of interaction between switches. 0.1µF 1µF Bidirectional Switch Sometimes it is necessary to use “back-to-back” MOSFET IN VS switches to completely isolate the power source from the load, or from another power source, when the switch is EN DS turned off. This is the case when the supply voltage is LTC1154 R1 R2 100k 1k higher or lower than the load voltage when powered by a STATUS G MTP3055EL secondary source. + OUT GND SD C1 A switched battery application, as shown in Figure 6, 0.33µF + CLOAD 100µF illustrates a bidirectional (fully isolated) switch. When the AN53 • TA05 wall unit power supply is connected to VIN, the load is disconnected from the battery by a fully isolated switch Figure 5. Slew Rate Reduction Network for Powering “Large” Capacitive Loads which allows the load voltage to fluctuate above or below the battery voltage without forcing current into the battery The start-up current can be substantially reduced by or pulling current out of it. reducing the slew rate at the gate of an N-channel switch The bidirectional battery switch shown in Figure 7 illus- as shown in Figure 5. The gate drive output of the LTC1154, trates how the LTC1154 drives two “back-to-back” low single micropower MOSFET driver, is passed through a simple RC network, R1 and C1, which substantially slows VIN the slew rate of the MOSFET gate to approximately 1.5 x 6V-18V 10-4V/µs. Since the MOSFET is operating as a source follower, the slew rate at the source is essentially the same S1 + as that at the gate, reducing the start-up current to 4-10 + µ LOAD approximately 15mA which is easily managed by CELLS 100 F the system regulator. R2 is required to eliminate the possibility of parasitic MOSFET oscillations during switch AN53 • TA06 transitions. Also, it is good practice to isolate the gates of Figure 6. Switched Battery Application VIN 6V-18V D1 Q1 Q2 1N5817 135,6,7,8 R4 + 100k 2Si9956DY 4 4-10 + C1 CELLS R2 IN V LOAD 10k S 100µF D2 D3 1N5242 1N4148 R1 EN DS 1k LTC1154 STATUS G R3 91k GND SD AN53 • TA07 Figure 7. Bidirectional Switch Using Two “Back-to-Back” MOSFETs AN53-3 Application Note 53 RDS(ON) N-channel MOSFETs, Q1 and Q2, to fully discon- Bootstrapped Operation nect the battery from the load immediately after the wall The circuit shown in Figure 9 should be used if mi- unit power supply is connected to V . The two body IN cropower standby operation is required. The standby diodes in Q1 and Q2 are also connected “back-to-back” supply current is reduced to < 30µA by increasing the and therefore no current can flow through the switch when value of R1 from 3k to 330k and adding a “bootstrap” the gate drive is removed. network, R2 and D2, from each switch output to the supply The LTC1154 ENABLE input senses when the wall unit pin. In this way, the extra supply current is provided only voltage exceeds 3V and inverts the action of the switch so when the switch is turned ON. The supply current drops that the two MOSFETs are turned off when the wall unit back to 30µA when the switch is turned OFF and the power supply is connected.
Details
-
File Typepdf
-
Upload Time-
-
Content LanguagesEnglish
-
Upload UserAnonymous/Not logged-in
-
File Pages16 Page
-
File Size-