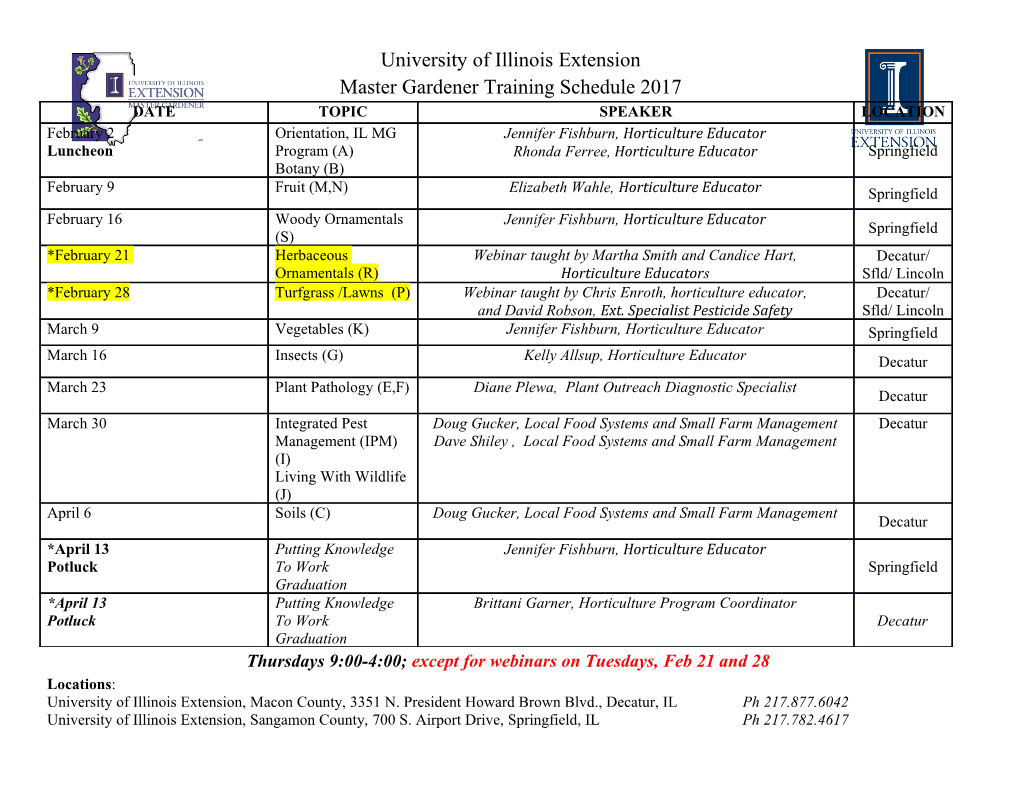
A computational lifetime prediction of a thermal shock experiment. Part I: thermomechanical modelling and lifetime prediction Sébastien Amiable, Stéphane Chapuliot, Andreï Constantinescu, Antoine Fissolo To cite this version: Sébastien Amiable, Stéphane Chapuliot, Andreï Constantinescu, Antoine Fissolo. A computational lifetime prediction of a thermal shock experiment. Part I: thermomechanical modelling and lifetime prediction. Fatigue and Fracture of Engineering Materials and Structures, Wiley-Blackwell, 2006, 29, pp.175-182. 10.1111/j.1460-2695.2006.0976.x. hal-00111460 HAL Id: hal-00111460 https://hal.archives-ouvertes.fr/hal-00111460 Submitted on 9 Jul 2019 HAL is a multi-disciplinary open access L’archive ouverte pluridisciplinaire HAL, est archive for the deposit and dissemination of sci- destinée au dépôt et à la diffusion de documents entific research documents, whether they are pub- scientifiques de niveau recherche, publiés ou non, lished or not. The documents may come from émanant des établissements d’enseignement et de teaching and research institutions in France or recherche français ou étrangers, des laboratoires abroad, or from public or private research centers. publics ou privés. A computational lifetime prediction of a thermal shock experiment. Part I : thermomechanical modelling and lifetime prediction S. AMIABLE1, S. CHAPULIOT2, A. CONSTANTINESCU1 andA.FISSOLO2 1Solid Mechanics Laboratory – CNRS UMR 7649, Department of Mechanics – Ecole Polytechnique, 91128 Palaiseau cedex, France, 2DM2S/SEMT, CEA Saclay, 91191 Gif sur Yvette cedex, France ABSTRACT The SPLASH experiment has been designed in 1985 by the CEA to simulate thermal fatigue due to short cooling shocks on steel specimens and is similar to the device reported by Marsh in Ref. [1]. The purpose of this paper is to discuss the mechanical and the fatigue analysis of the experiment using results from FEM computations. The lifetime predictions are obtained using a modified dissipated energy with a maximal pressure term and agree with the experimental observations. The numerical analysis of the mechanical state shows an important evolution of the triaxiality ratio during the loading cycle. Further comparisons and discussions of the fatigue criteria are provided in the second part of the paper (Part II)2. Keywords 304 stainless steel; finite element; low-cycle fatigue; plasticity; thermal fatigue; thermal shock. NOMENCLATURE A = elastic 4th order tensor c, k = thermal capacity and conductivity E, ν = young’s modulus and Poisson’s coefficient J2 = second invariant of the deviatoric stress tensor P = hydrostatic pressure p = cumulated plastic strain q = thermal flux r = heat source T = temperature field TF = triaxiality factor u = displacement field Wp = dissipated energy density per cycle σ, ǫ = equivalent stress and strain ranges ǫ, e = strain tensor and its deviatoric part ǫe, ǫp = elastic and plastic strain tensors ρ = volumic mass σ Y = elastic limit σ, s = stress tensor and its deviatoric part assessment methods are generally based on design rules INTRODUCTION provided by different codes (see for example Ref. [3]). A series of industrial structures like turbines, engines, nu- These rules stem from closed-form solutions and exper- clear or classical thermal plants are subject to thermome- imental studies of the last decades and as such are not chanical cycling leading to fatigue. The actual design and always appropriate to design, for example when the stress path is multiaxial during the cycle. Correspondence: A. Constantinescu. E-mail: andrei.constantinescu@lms. The finite element method provides a powerful tool polytechnique.fr for the mechanical analysis of structures, but its success 1 is determined by a series of factors: correct constitu- in Ref. [7] on a 316L stainless steel and in Ref. [8] for tive law and boundary conditions, computational burden. 304L stainless steel. Moreover the results present often multiaxial stress–strain The basic concept of the experimental rig is similar to the paths which are difficult to interpret with respect to clas- one reported by Marsh in Ref. [1]. During the test, a par- sical criteria defined in uniaxial context, and therefore fur- allepipedic specimen (200 × 30 ×20 mm3) is continuously ther work is needed to adapt the fatigue criterion for these heated by Joule effect at the maximum temperature T max cases. and then cyclically cooled by water sprays on small spots The purpose of this work is to provide a fatigue analysis (approximatively 10 ×5mm2) on two opposite faces. At of the SPLASH test rig. The experiment imposes thermal the end of the water spraying, the minimal temperature shocks to a heated specimen by spraying cold water on T min is reached in the locally quenched zones. A photo it and leads under certain conditions to crack initiation. and a schematic plot of the SPLASH test facility are rep- Certain features of the experiment are important spatial resented in Fig. 1. and temporal gradients of the mechanical fields involved. The temperature variation characterizing the test is de- The originality of this work is two-fold. On the one fined as the difference between maximal and minimal tem- hand, it adapts and interprets classical numerical tech- perature, T max and T min, respectively, at the centre of the niques to obtain a precise thermomechanical analysis of quenched zone: the SPLASH experiment. On the other, it provides a novel discussion of low cycle thermomechanical fatigue crite- T = Tmax − Tmin (1) ria involving a varying triaxiality ratio during the loading cycle. The numerical method is presented in this paper The control of the temperature in the quenched zone and (Part I) and continues with the discussion of fatigue crite- in-depth different points has been measured with thermo- ria in the second part (Part II).2 couples on a mock specimen. Regarding previous studies on structures, we might men- The cycle starts from a homogeneous maximal tempera- tion the studies on cast-iron exhaust manifolds and alu- ture T max in the specimen. On local zones on two opposite minum cylinder heads4,5 where damage was supposed to faces, the cooling period of 0.25 s to the minimal temper- be uncoupled from the constitutive behaviour. A dissi- ature T min is caused by the water spray. Finally, the cycle pated energy criterion has been used for lifetime pre- continues with the heating up period of 7.5 s to T max by dictions based on the mechanical fields computed on the Joule effect. During the heating, the maximal temperature plastic shakedown cycle. For exhaust manifolds and cylin- T max is uniformly reached over the specimen. der heads, the effect of hydrostatic pressure could be ne- Due to the short cooling period and the localized spatial glected. However, this is not the case for the present work distribution of temperatures, the experimental device is and we discuss this point in the next sections and in the capable of reproducing high temperature gradients. The ◦ −1 second part (Part II) of the paper. Other studies6 proposed cooling rate is of approximatively ≈ 600 Cs and the ◦ −1 to couple the constitutive law with damage in order to es- spatial gradient reaches about ≈ 100 Cmm . However timate the lifetime of crossed specimen in a biaxial strain- the affected zone is confined to some square millimeters controlled experiment and the authors obtained compa- at the surface and to about two millimeters in depth. rable results from coupled and uncoupled models. This The experiment can be assimilated to a local quenching method has its computational drawbacks as it imposes to of the specimens and leads to a small localized plastic zone. compute all cycles. After about 100 000 cycles, an evolving crack network ap- This paper presents in the first section a description of pears. The evolution of the crack network has been deter- the SPLASH experiment. It continues with the descrip- mined by optical microscopy at regular time intervals and tion of the used 304L stainless steel and the main as- an extended report is available in Ref. [8]. sumptions of the modelling. The FEM analysis and the computational results are presented in section ‘The ther- MATERIAL PROPERTIES AND MODELLING momechamical analysis’. The last section discusses the ASSUMPTIONS lifetime predictions using a criterion involving dissipated energy density of the cycle and maximal pressure. The steel studied here is a 304L type austenitic stainless steel with standard material composition as displayed in Table 1. Some classical elastoplastic and thermal proper- THE SPLASH EXPERIMENT ties in the considered temperature range of 20–300 ◦C are The SPLASH experiment is a thermomechanical fatigue given in Table 2. We shall not mention viscosity as it is experiment designed by the CEA in order to induce crack generally accepted that creep at this temperature can be networks by a cool-down shock. A series of results re- neglected for this steel (see the constitutive law in section garding fatigue experiments have already been reported ‘The mechanical analysis’). 2 Fig. 1 SPLASH specimen. Fig. 2 Evolution of the global load in isothermal uniaxial experiment under fixed strain range. Table 1 Chemical composition (wt%), 304L stainless steel CMnSiCrNiMoS P CuAl B NFe 304 0.031 1.48 0.55 19.4 8.6 0.23 0.003 0.028 0.17 0.025 0.0015 0.058 Bal. Table 2 Material properties, 304L stainless steel −1 3 E(GPa) α(K ) νρ(Kg/m ) k(W/m/K) CP (J/Kg/K) 20 oC 196 15.9 10−6 0.3 7800 18 550 350 oC 172 17.8 10−6 0.3 −− − 304L stainless steel has an impressive ductility in fatigue of 304L stainless steel. However, this would conduct to experiments. In isothermal uniaxial fatigue experiments heavy numerical burden because we should compute all in Ref. [9], it can withstand up to 104–105 cycles under the cycles to the final failure. an imposed strain amplitude ǫ ≈ 0.4–1.0%.
Details
-
File Typepdf
-
Upload Time-
-
Content LanguagesEnglish
-
Upload UserAnonymous/Not logged-in
-
File Pages10 Page
-
File Size-