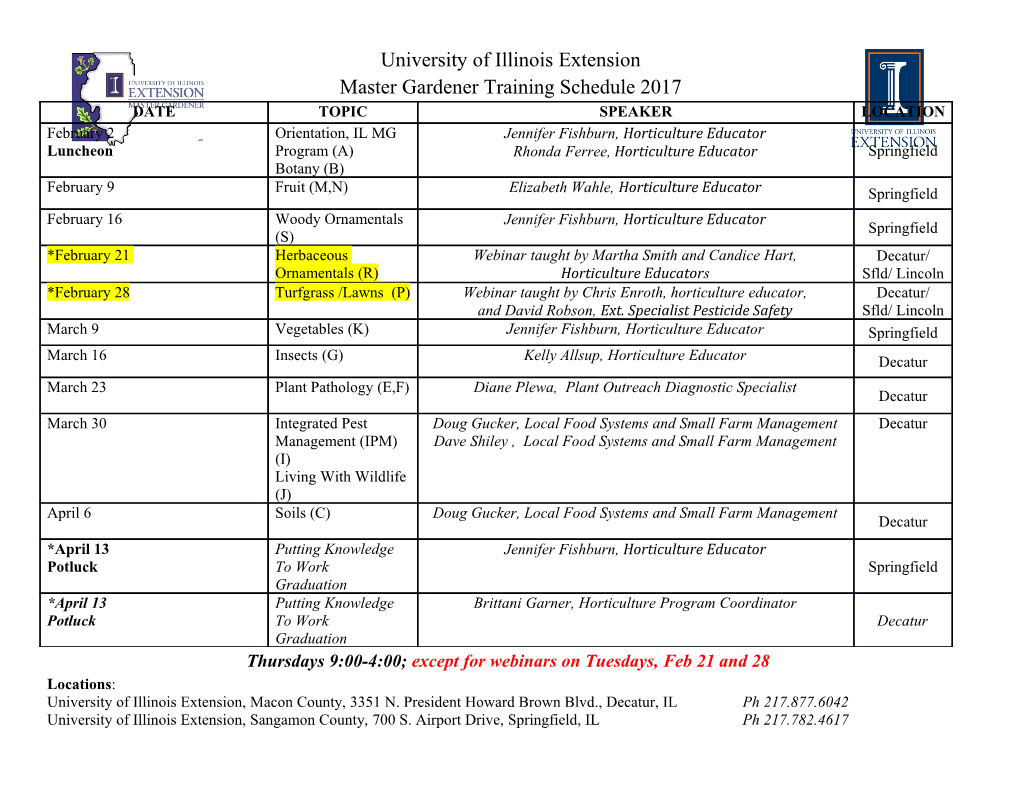
applied sciences Article Comparison of Wear Performance of Austempered and Quench-Tempered Gray Cast Irons Enhanced by Laser Hardening Treatment Bingxu Wang 1,2,*, Gary C. Barber 2, Rui Wang 2,3 and Yuming Pan 2 1 Faculty of Mechanical Engineering and Automation, Zhejiang Sci-Tech University, #928 No.2 Street, High Education Zone, Hangzhou 310018, China 2 Department of Mechanical Engineering, School of Engineering and Computer Science, Oakland University, Rochester, MI 48309, USA; [email protected] (G.C.B.); [email protected] (R.W.); [email protected] (Y.P.) 3 College of Modern Science and Technology, China Jiliang University, Hangzhou 310018, China * Correspondence: [email protected] Received: 30 March 2020; Accepted: 26 April 2020; Published: 27 April 2020 Abstract: The current research studied the effects of laser surface hardening treatment on the phase transformation and wear properties of gray cast irons heat treated by austempering or quench-tempering, respectively. Three austempering temperatures of 232 ◦C, 288 ◦C, and 343 ◦C with a constant holding duration of 120 min and three tempering temperatures of 316 ◦C, 399 ◦C, and 482 ◦C with a constant holding duration of 60 min were utilized to prepare austempered and quench-tempered gray cast iron specimens with equivalent macro-hardness values. A ball-on-flat reciprocating wear test configuration was used to investigate the wear resistance of austempered and quench-tempered gray cast iron specimens before and after applying laser surface-hardening treatment. The phase transformation, hardness, mass loss, and worn surfaces were evaluated. There were four zones in the matrix of the laser-hardened austempered gray cast iron. Zone 1 contained ledeburite without the presence of graphite flakes. Zone 2 contained martensite and had a high hardness, which was greater than 67 HRC. Zone 4 was the substrate containing the acicular ferrite and carbon-saturated austenite with a hardness of 41–27 HRC. In Zone 3, the substrate was tempered by the low thermal radiation. For the laser-hardened quench-tempered gray cast iron specimens, three zones were observed beneath the laser-hardened surface. Zone 1 also contained ledeburite, and Zone 2 was full martensite. Zone 3 was the substrate containing the tempered martensite. The tempered martensite became coarse with increasing tempering temperature due to the decomposition of the as-quenched martensite and precipitation of cementite particles. In the wear tests, the gray cast iron specimens without heat treatment had the highest wear loss. The wear performance was improved by applying quench-tempering heat treatment and further enhanced by applying austempering heat treatment. Austempered gray cast iron specimens had lower mass loss than the quench-tempered gray cast iron specimens, which was attributed to the high fracture toughness of acicular ferrite and stable austenite. After utilizing the laser surface hardening treatment, both austempered and quench-tempered gray cast iron specimens had decreased wear loss due to the high surface protection provided by the ledeburitic and martensitic structures with high hardness. In the worn surfaces, it was found that cracks were the dominant wear mechanism. The results of this work have significant value in the future applications of gray cast iron engineering components and provide valuable references for future studies on laser-hardened gray cast iron. Keywords: gray cast iron; austempering; quench-tempering; laser surface hardening; wear loss Appl. Sci. 2020, 10, 3049; doi:10.3390/app10093049 www.mdpi.com/journal/applsci Appl. Sci. 2020, 10, 3049 2 of 12 1. Introduction Gray cast iron (GI) is a common ferrous material with the presence of graphite flakes in the matrix. It has been reported that GI has high machinability, high vibration adsorption, and high castability. In industry, GI has been widely utilized in the production of gears, guide rails, and cylinder liners for diesel engines [1–3]. These GI engineering parts frequently are required to withstand direct surface contacts with applied pressure and relative movement. Superior wear resistance is required to ensure good working performance and long service life. Thus far, surface-hardening treatments and heat treatments are considered as the common strengthening methods to improve the anti-wear performance of ferrous mechanical components [4–6]. Austempering heat treatment has received considerable attention in the past two decades due to the formation of a unique ausferritic structure with high strength–weight ratio, fracture toughness, ductility, and good tribological performance [7–10]. In the austempering heat treatment, fully austenitized cast iron is quickly transferred to a salt bath furnace and maintained for a certain time period. The austempering temperatures should be controlled within the range between the temperatures at which pearlite and martensite form. Quench-tempering heat treatment is a conventional heat treatment to increase the strength and hardness of cast irons and steels. During the quench-tempering process, the as-quenched martensite decomposes to tempered martensite with the precipitation of cementite particles or islands. Additional tempering can decrease the amount of retained austenite and release the internal residual stress caused by the rapid cooling rate in the quenching step [11,12]. The wear properties of GI have been significantly improved by the use of austempering and quench-tempering heat treatments. Balachandran et al. [8] investigated the wear resistance of hypereutectic gray cast iron after receiving austempering and quench-tempering heat treatments. The austempered gray cast iron (AGI) had the best wear performance, which was related to the Transformation induced plasticity (TRIP) effect, and the quench-tempered gray cast iron (QTGI) had moderate wear resistance, which was attributed to fine carbides. Sarkar et al. [10] determined the effects of austempering heat treatment on the microstructure, wear, and mechanical properties of AGI alloyed with copper. The amount of retained austenite increased, the hardness and tensile strength decreased, and the ductility and wear depth increased with higher austempering temperature. Laser surface hardening treatment is an effective approach to lower the wear loss and extend the fatigue life of cast iron and steel components. During the laser-hardening process, the top surface of cast irons or steels is heated above Acm or the eutectic critical temperature to transform the original microstructure into an unstable austenite or liquid state. Then, the top surface in the fully austenitized or liquid state is cooled by air and self-quenches to the adjacent cold substrate. Currently, laser surface hardening treatment is often applied to small components with complicated geometry [13–16]. Joshi et al. [17] applied laser glazing treatment to GI. The surface hardness was significantly improved due to the far-from equilibrium phase transformation. It was experimentally observed that the central fusion regions containing dendritic structure and cementite plates, and the heat-affected region containing bainite with graphite flakes was formed after laser glazing. Liu et al. [18] investigated the effects of surface temperature and scanning speed on the characteristics of the hardened layers of gray cast iron such as microstructure and hardness profile by using a high-power diode laser. It was found that a homogeneous microstructure with hardness ranging from 700 HV to 800 HV was formed in the laser-hardened zone, which was not dependent on the temperature and scanning speed. In addition, a deep hardened zone was produced when using high temperature and low scanning speed. In addition, they pointed out that overlapping areas around 16.7%–20.8% of the hardened track width was found, which would degrade the surface hardness because the martensite was tempered. Since the austempering, quench-tempering, and laser surface hardening treatments were frequently utilized to strengthen the cast irons and steels, it is vital to understand the coupling influence of traditional heat treatment and surface treatment on the phase transformation and wear properties of GI specimens. In the present study, the roles of laser surface-hardening treatment on the microstructure and wear resistance of AGI and QTGI specimens were investigated. A reciprocating sliding wear test Appl. Sci. 2020, 10, x FOR PEER REVIEW 3 of 12 Appl.the Sci.microstructure2020, 10, 3049 and wear resistance of AGI and QTGI specimens were investigated.3 of 12A reciprocating sliding wear test configuration was utilized to determine the wear performance. The wear performance of AGI and QTGI with and without laser-hardening treatment was compared configuration was utilized to determine the wear performance. The wear performance of AGI and QTGI under equivalent macro-hardness values. The phase transformations in the laser-hardened regions with and without laser-hardening treatment was compared under equivalent macro-hardness values. and heat-affected regions were determined using an optical microscope. The macro-hardness and The phase transformations in the laser-hardened regions and heat-affected regions were determined micro-hardness profiles were measured by using a Rockwell hardness tester and a Vickers hardness using an optical microscope. The macro-hardness and micro-hardness profiles were measured by using tester. The worn surfaces were analyzed by utilizing a scanning electron microscope (SEM) to find a Rockwell hardness
Details
-
File Typepdf
-
Upload Time-
-
Content LanguagesEnglish
-
Upload UserAnonymous/Not logged-in
-
File Pages12 Page
-
File Size-