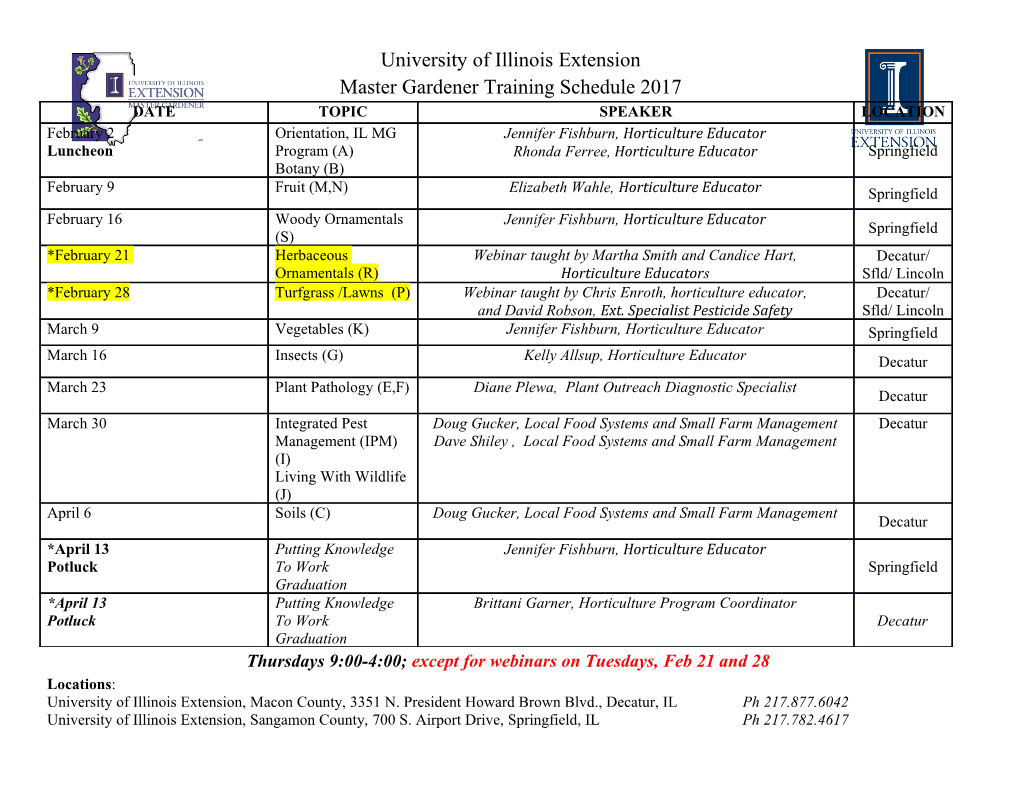
International Journal of Mechanical Sciences 65 (2012) 157–167 Contents lists available at SciVerse ScienceDirect International Journal of Mechanical Sciences journal homepage: www.elsevier.com/locate/ijmecsci Models of the cutting edge geometry of medical needles with applications to needle design Peidong Han n, Demeng Che, Kumar Pallav, Kornel Ehmann Department of Mechanical Engineering, Northwestern University, 2145 Sheridan Road, Evanston, IL 60208, United States article info abstract Article history: Tissue cutting by a needle is greatly influenced by the geometry of its cutting edges. Yet, there are very Received 13 May 2012 few results in the technical literature that address the issues surrounding the relation between needle Received in revised form tip and cutting edge geometry and its cutting/insertion force. In the present paper, general mathema- 20 August 2012 tical models of the included and inclination angles of a needle’s cutting edge are formulated since they Accepted 25 September 2012 exert a profound influence on cutting behavior. Specific models for various tip geometries are Available online 3 October 2012 developed to investigate four types of needle tips including one-plane, asymmetric three-plane, Keywords: symmetric multi-plane, and symmetric three-curved-surface needles. The results show that the cutting Tissue cutting edge of the one-plane needle has a very undesirable configuration. Asymmetric three-plane needles, Medical needle design such as the lancet and back bevel tip needles, can significantly improve the configuration of the cutting Cutting edge geometry edge. Back bevel tip needles, in turn, offer even more desirable cutting edge geometry than lancet tip Needle insertion needles. In evaluating the cutting edge angles of multi-plane needles, it was shown that the included angle is limited by its tip geometry. To resolve this problem a needle formed by three curved surfaces was proposed. It was found that this new design has significant potential for reducing patient trauma as well as target accuracy during needle insertion. The proposed general approach provides the foundation for designing medical needles with specific cutting edge properties. & 2012 Elsevier Ltd. All rights reserved. 1. Introduction critical to the success of the procedure. Additionally, the studies by Egekvist et al. [5,6] and Arendt-Nielsen et al. [7] have shown that the Medical needles are the most commonly used medical devices needle insertion force is positively correlated with the frequency and and are widely used in minimally invasive percutaneous proce- intensity of pain and trauma. For example, the insertion force is dures such as injection, regional anesthesia, blood sampling, significantly higher for 27G needle insertions compared to 30G biopsy and brachytherapy. These procedures require inserting a needle insertions. Correspondingly, 53% of insertions with the 27G needle to a target inside the body for either drug delivery or tissue needles caused pain and 39% of insertions with 30G needles caused sample removal. Brachytherapy is a medical procedure to place pain. In [8], the bluntness of the needle tip has been found to be radioactive seeds inside or near the tumor using a needle for related to the increased pain in subcutaneous injections. Thus, cancer treatment. The success of this procedure depends on the needles with lower insertion forces are important to reduce the pain accurate placement of the seeds. However, inserting a needle and trauma experienced by the patients during the procedure. deforms the tissue and displaces the target causing placement Needle insertion is essentially a tissue cutting process. The errors [1,2]. Substantial practice is needed to avoid placement force of tissue cutting by a needle greatly depends on its cutting errors by compensating for tissue deformation and target edge geometry. Prior to studying the cutting edge geometry of a displacement caused by the needle tip force and friction. It has been needle, one may begin by examining a blade with a straight shown by Alterovitz [2–4] that without preoperative planning cutting edge that is defined by its included angle y and the cutting placement errors may be as large as 26% of the prostate diameter edge radius also referred to as the ‘‘roundness’’ of the cutting edge, resulting in damage to healthy tissue and failure to kill cancerous as illustrated in Fig. 1(a). Maximal knife sharpness is obtained with a cells. A practical approach to reducing the placement error is to small included angle and a small radius for the cutting edge [9]. minimize the needle insertion force. Thus, a needle that creates The knives with a small included angle, such as surgical scalpels and lower insertion forces and smaller displacements of the target is straight razors, are extremely sharp but fragile. On the contrary, knives that require a tough edge usually have a large included angle. Typical values of the included angle are about 151 for razor blades n Corresponding author. Tel.: þ1 84 7467 0712. and veneer cutting knives, 20–301 for microtome knives and 30–401 E-mail address: [email protected] (P. Han). for kitchen knives [9]. Typical radii of cutting edges are 5 mmfora 0020-7403/$ - see front matter & 2012 Elsevier Ltd. All rights reserved. http://dx.doi.org/10.1016/j.ijmecsci.2012.09.014 158 P. Han et al. / International Journal of Mechanical Sciences 65 (2012) 157–167 Bevel tip needle stylet Edge bevel Bevel tip needle cannula Bevel cutting edge Lancet point needle stylet Back bevel needle stylet Edge bevel Motion Back bevel needle cannula Work Cutting edge radius Trocar tip needle stylet Franseen tip needle cannula Conical tip needle stylet 2 1 Fig. 2. Examples of needle tips. Motion Motion Surprisingly little research has been carried out related to the Work Work modeling of the needle cutting edge geometry and to investigate how the cutting edge geometry influences the penetration force of a Fig. 1. (a) cross-section of a blade showing the included angle y and cutting edge needle. Studies have been conducted to investigate the effects of radius; (b) plan view of cutting with inclination angle l; (c) illustration of the cutting process (a¼rake angle, b¼setting angle, z¼relief/clearance angle); and needle tip geometry on the penetration force and needle sharpness (d) the cutting process at b¼01. [14–20]. In these works needle tip geometry was defined only by the bevel angle, the angle between the bevel ground surface and the needle longitudinal axis, which does not directly reveal any specific scalpel and 17 mm for a new safety razor blade (34 mmwhen information about the cutting edges. The needle sharpness was worn) [9]. Another important factor in cutting is the inclination judged by the penetration force encountered during passing through angle l, which describes the angle of the cutting edge relative to the tissue. However, little is known about how sharpness and penetra- cutting direction, as illustrated in Fig. 1(b). It has been shown by tion force are directly influenced by tip geometry. Moore et al. Atkins [10–12] that the cutting force exerted by a sharp object [21–23] have used the customary cutting tool geometry approach depends on the slice/push ratio k given by k¼(speed parallel to widely used in metal cutting theory to model the hollow biopsy cutting edge/speed perpendicular to the cutting edge). An increase needle tip. The emphasis of their work was on the determination of in the slice/push ratio reduces the cutting force. When the cutting the variation of the inclination and rake angles along the needle edge is inclined at an inclination angle l, the slice/push ratio is given cutting edge. For a biopsy cannula, where the cutting edge is by k¼tan l. An increase in the inclination angle increases k, leading generated by the intersection of the needle side surface and the to a lower cutting force. For a general cutting process, three other bevel plane (rake face), one rake angle together with the inclination basic angles are important: the rake angle (a), the clearance/relief angle and edge radius properly describes the cutting edge. However, angle (z), and the setting angle (b), as shown in Fig. 1(c). The cutting in case of a multi-plane needle stylet where the needle cutting edge surface of the blade is the rake face. The rake angle is the angle of is formed by the intersection of two bevel surfaces, one rake angle the rake face with respect to the perpendicular to the cut surface. together with the inclination angle and edge radius does not The clearance/relief angle is the angle between the second face of adequately represent the cutting edge geometry. Until now, no work the blade and the cut surface. Hence, yþaþz¼901. It can be seen has been reported on modeling the cutting edge of a needle stylet. that the rake angle and clearance/relief angle depend on the setting In this paper, the cutting edge geometry of a needle is defined angle. Tissue cutting by a scalpel or a needle is a process where the by the included angle, the inclination angle, and the cutting edge tool cuts by penetration into the tissue. This type of cutting has a radius, as is defined for a blade. The radius of a cutting edge setting angle b¼01,asshowninFig. 1(d), where both the edge depends on the manufacturing processes including the machin- bevels act as rake faces. Hence, yþa1þa2¼1801.Asymmetricblade ing, deburring, and coating processes, while the included angle has a1¼a2. For a blade with only one side beveled and the other side and inclination angle of a needle’s cutting edge are determined by remaining flat, a2 is equal to 901, hence yþa1¼901.
Details
-
File Typepdf
-
Upload Time-
-
Content LanguagesEnglish
-
Upload UserAnonymous/Not logged-in
-
File Pages11 Page
-
File Size-