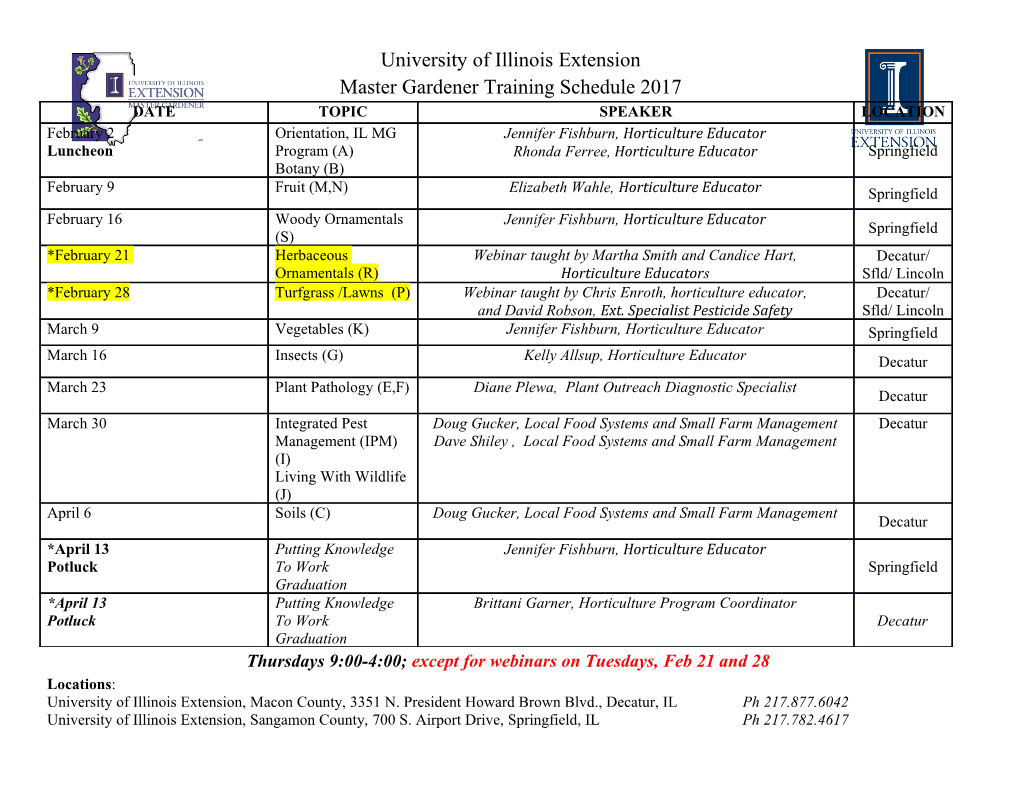
Microstructure and Mechanical Properties of Ductile Die-cast Al-Mg-Si-Mn Alloys A thesis submitted for the degree of Doctor of Philosophy By Douglas Watson Department of Mechanical, Aerospace and Civil Engineering College of Engineering, Design and Physical Sciences Brunel University London, Uxbridge, Middlesex UB8 3PH United Kingdom October 2015 Supervision: Dr. Shouxun Ji Prof. Zhongyun Fan Abstract Aluminium alloys have been seen a dramatic increase in transport manufacturing in past two decades. This is primarily driven by the achievement of effective weight-savings, increased vehicle fuel efficiency and reduced CO2 emissions in transport. One of the significant progresses in most recent years has been in the application of aluminium-intensive car body structure, in which the manufacturing of thin wall castings with improved ductility is one of the critical issues. High pressure die casting (HPDC) is a fast and economical near-net shape manufacturing method to produce thin wall components. Therefore the application of HPDC process to make thin wall structural components for aluminium-intensive car body structure is one of the most challenges in recent development. However, the currently available die cast aluminium alloys are unable to fulfil this requirement because of the insufficient ductility, which is essential for joining castings with sheets and extruded parts. This has become critical in further development and extensive acceptance in car manufacturing industry. Generally, the mechanical properties of die castings are determined by alloy composition, defect levels and microstructure in the castings. In the present study, the significant achievement is the development of Al-Mg-Si-Mn alloy for HPDC process to provide improved ductility in die castings in order to satisfy the requirement of mechanical properties, in particular ductility for the application in automotive body structure. Starting from the thermodynamic analysis and CALPHAD (Computer Coupling of Phase Diagrams and Thermochemistry) modelling of Al-Mg-Si system for solidification and phase formation, the alloy composition was optimised using international standard tensile samples to review the effect of various alloying elements on the mechanical properties. Another achievement is the understanding of the solidification and microstructural evolution, the relationship between the microstructure and mechanical properties, and the strengthening mechanisms in the developed alloy. The solidification behaviour in the shot sleeve and in the die cavity was examined for the formation of the primary α-Al phase, eutectic Al-Mg2Si phases in the alloy. The morphology, size and size distribution of the primary α-Al phase were characterised under different solidification conditions. The growth morphology of the primary α-Al phase formed in the shot sleeve and in the die cavity was analysed using the Mullins- i Sekerka instability theory and the growth rate of eutectic Al-Mg2Si phases during solidification was calculated using Jackson-Hunt theory. Still another achievement is the study of the effect of Mn and Fe on the morphology, size and distribution of various Fe-rich compounds in the Al-Mg-Si alloy produced by HPDC process. The assessment was associated with the mechanical properties of yield strength, ultimate tensile strength and elongation with different Fe and Mn contents. CALPHAD modelling of multi-component Al-Mg-Si-Mn-Fe and Al-Mg-Si-Fe systems was studied to find out the effect of Fe impurity in the Al-Mg-Si alloy. The precise accumulation of iron during HPDC using fully recycled materials was examined to predict the maximum cycles to produce castings with required mechanical properties. The strengthening mechanism and the relationship between the microstructure and mechanical properties are explored in the alloy made by secondary materials. Furthermore, the effect of nickel on the microstructure and mechanical properties of the die-cast Al-Mg-Si-Mn alloy was also studied in association with the formation of Ni-rich intermetallics during solidification in the die-cast Al-Mg-Si-Mn alloy containing different Ni contents. The final achievement is the understanding of the repeatability of die castings made by the new alloy with industrial scale components. The tensile properties of standard samples that were obtained directly from HPDC process and made by the machined die castings at different locations were further assessed for the reproducibility of casting components made by the Al- Mg-Si-Mn alloy. The distributions of yield strength, ultimate tensile strength and elongation of the tensile samples were analysed by the average values with standard deviations and by the Weibull statistical model with three parameters. The correlations between the mechanical properties and the microstructural features, porosity levels and fracture morphology were investigated for the different types of samples. It was found that three-parameter Weibull analysis was capable of analysing the reproducibility of die cast components and the scattering of tensile properties was mainly due to the presence of porosity and non-uniform microstructure in the die-castings. ii Acknowledgement I would like to thanks Dr. Shouxun Ji at Brunel University London for his unlimited support and guidance from experimental design and microstructure characterisation and scientific understanding of this topic, Professor Zhongyun Fan at Brunel University London for his encouragement during my undergraduate studies, Dr. Mark White at Jaguar Land Rover for giving opportunities to fulfil my goals. This research is supported by EPSRC under LiME research centre and TSB, UK. I also thank my colleagues at BCAST, Dr. Hailin Yang, Dr. Wenchao Yang, Dr. Feng Yan, Dr. Yun Wang for helps in the HPDC experiments and materials characterisation, Dr. Feng Gao for help in CALPHAD calculation, Mr. Camello Nunez, Mr. Peter Lloyd and Mr. Stephen Cook for help in running and maintaining the machines, Mr. Matthew Ralph for the help in administration. Finally, my gratitude to my family for their support and understanding through the period of study. iii Table of Contents Abstract .................................................................................................................................................... i Acknowledgement ................................................................................................................................. iii Table of Contents ................................................................................................................................... iv Chapter 1 Introduction ........................................................................................................................... 1 1.1 Background and Challenges ..................................................................................................... 1 1.2 Research Objectives ................................................................................................................. 4 1.3 Outline of Thesis ...................................................................................................................... 5 Chapter 2 Literature Review .................................................................................................................. 7 2.1 High Pressure Die Casting (HPDC) ......................................................................................... 7 2.2 Improvement in HPDC........................................................................................................... 10 2.3 Solidification in Cold Chamber HPDC .................................................................................. 13 2.4 Defects Formed in HPDC ...................................................................................................... 16 2.5 Aluminium Alloys Available in HPDC Process .................................................................... 18 2.6 Al-Si Alloys ........................................................................................................................... 21 2.7 Al-Si-Cu Alloys ..................................................................................................................... 22 2.8 Al-Si-Mg Alloys ..................................................................................................................... 24 2.9 Al-Mg Alloys ......................................................................................................................... 25 2.10 Fe in Aluminium Alloys ....................................................................................................... 26 2.11 Ni in Aluminium Alloys ....................................................................................................... 27 2.12 Repeatability and Weibull Analysis ..................................................................................... 27 2.13 Scope of the Current Research ............................................................................................. 29 Chapter 3 Experimental Details ........................................................................................................... 31 3.1 Melt Preparation ..................................................................................................................... 31 3.2 High Pressure Die Casting ..................................................................................................... 35 3.3 Microstructure Observation and Analysis .............................................................................
Details
-
File Typepdf
-
Upload Time-
-
Content LanguagesEnglish
-
Upload UserAnonymous/Not logged-in
-
File Pages176 Page
-
File Size-