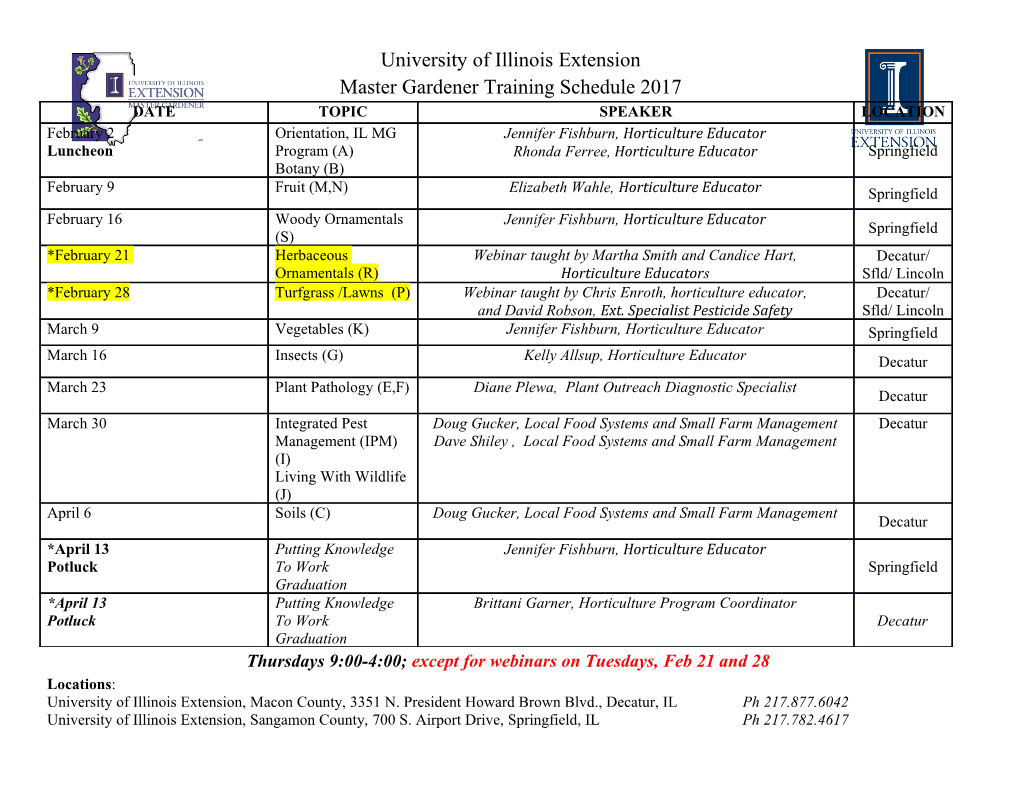
Materials Research, Vol. 1, No. 1, 29-38, 1998. © 1998 Matemathical Description of Solidification Cooling Curves of Pure Metals Arno Müller Porto Alegre - RS, Brazil; e-mail: [email protected] Received: March 11, 1998; Revised: May 16, 1998 The introduction of an ‘‘incubation time’’ to the Schwarz classical mathematical description of metals solidification, resulted in a new model called Modified Schwarz Model. By doing so it was possible to identify and quantify the ‘‘delay time’’ that separates the two heat waves traveling independently in a casting during the solidification: the Supercooled / Superheated Liquid and the Solid / Liquid. The thermal shock produced in the initial stage of the undercooling generation process, can be used as an important parameter in the forecasting of the solidification’s behavior of pure metals and alloys, when changing mold’s materials, pouring and ambient tempera- tures. The hypercooling proneness degree of metals and alloys, can also be calculated. Keywords: solidification, thermal analysis, mathematical modeling, thermal shock, cool- ing curves 1. Introduction extraction, the liquid temperature falls bellow its solidifi- cation temperature. Schwarz1, presented an exact mathematical solution for The temperature distribution in the liquid metal and in the Stefan’s problem applied to the solidification of metals the mold in a semi-infinite metal-mold system, with an in semi-infinite systems, having a perfect thermal contact unidirectional heat extraction, without thermal resistance at the metal /mold interface and without convection. at the metal-mold interface can be calculated through the His model that was mostly applied to the solution of general solution presented by Schwarz to the problem problems of the heavy steel industry of the 30’s, can easily (Fig. 1): be used to calculate thermal gradients, solidification veloci- ties, cooling rates, etc., at any point of a metal-mold system. x However, cooling curves calculated with his Model, Tn( ,t) = An + Bn erf ( ) (1) 2 Ö``a3 t cannot reproduce the recalescence and, or, the arrest tem- perature, two very important parameters that are used to The constants An and Bn , can be calculated from the monitorate many foundry procedures. boundary conditions: At, x = 0: 2. The Solidification Process described by the Modified Schwarz Model (MSM) ’ ’ T3(0, t) = A3 = Ti’ = const. (2) The reason why the Schwarz model cannot be used to describe cooling curves lies in his basic assumption that At, x = + ¥: undercooling generation and nucleation mechanisms, as a T’ = T = T + B’ (3) unique process. 3(+a, t) p i’ 3 2,3 To solve that problem, the MS Model , proposes that the or: solidification process will proceed in two separated stages: B’ = Tp - Ti’ = const. (4) 2.1. First stage: generation of the undercooling 3 In pure metals the Undercooling is generated exclu- Therefore, introducing (2) and (4) in (1), it can be sively by heat diffusion, when by effect of thermal heat written: 30 Müller Materials Research ’ x T3(x, t) = Tf = Ti’ + (Tp - Ti’) erf ( ) = const (13) 2 Ö``a3 t which means: x’’ = const = f (14) 2 Ö``a2 t and, therefore x‘ = 2 f’ Ö``a3 t (15) Consequently (13): Figure 1. Undercooling, superheated / supercooled liquid interface and Tf = Ti’ + (Tp - Ti’) erf (f’) (16) the resulting cooling curve created by a thermal shock in a liquid metal against a cooler mold, before the nucleation’s start. Considering (12) and (16), it can also be written: (Tf - Ti’) Umax ’ x erf (f’) = = = T (x, t) = Ti’ + (Tp - Ti’) erf ( ) (5) 3 (Tp - Ti’) (Tp - Tf + Tf - Ti’) 2 Ö``a3 t Umax 1 For the mold, adopting similar boundary conditions, it = = (16a) Umax + S S - 1 can be written: Umax ½x½ or, T1(x, t) = Ti’ - (Ti’ - T0) erf ( ) (6) 2 Ö``a t 1 (1 - M S*) erf (f’) = (17) At x = 0, the heat balance, is given by: (1 - S*) dT1 dT3 from where, f‘ can be calculated. l1 ½x = 0 = l3 ½x = 0 (7) dx d’x The undercooling, defined as: ’ or: U(x, t) = Tf - T3(x, t) (18) Ti’ - T0 Tp - Ti’ Are dynamic, changing with time and position, and l1 = l3 (8) considering (5) can be expressed by: Ö``p a1 t Ö``p a3 t or: ½x½ U(x, t) = Tf - [Ti’ + (Tp - Ti’) erf ( ) ] (19) 2 Ö``a3 t b1 (Ti’ - T0) = b3 (Tp - Ti’) (9) It is maximum at x = 0, where: Making now: Umax = U(0, t) = Tf - Ti’ = const (20) b3 M = (10) or, in the non-dimensional form: b1 (8) becomes: Tf - Ti’ U*max = (21) Tf - To Ti’ - T0 = M (Tp - Ti’) (11) that can also be written (12), as: and, finally: (Tf - T0) - M S U*max = (22) M Tp + T0 (Tf - T0) (M + 1) Ti’ = (12) M + 1 And, considering that: 2.1.1. l / l Isotherms T - T The propagation parameters of a Supercooled Liquid / S* = p f (23) T - T Superheated Liquid Interface (l /l), located at x = x‘ and, f 0 T = Tf, can be calculated applying the general Eq. (5), to Eq. (16), can finally be written as: the boundary conditions: 1- M S At, (x = x‘): U*max = (24) M + 1 Vol. 1, No. 1, 1998 Solidification Cooling Curves of Pure Metals 31 This development, shows that the Supercooling gener- ment, of the l / l and s / l interfaces, measured by a ated by the collision of two semi-infinite thermal systems thermocouple placed in the ingot at a fixed distance X from without phase transformations, depends exclusively on: the the metal - mold interface. metal’s Superheating Degree (S*), the Initial Mold Tem- The interfaces travel speeds inside the ingot, change perature (T0) and the Heat Extraction Capacity of the with the value of f‘, f, which are influenced differently by metal-mold system (M). S*, as can be seen in Figs. 2 and 4. 2.2. Second stage: nucleation and growth of the solid The l / l interface is the first to reach the thermocouple and it will do it after a time t1 displacing itself, according After an incubation time t0 , the nucleation will begin to: in the undercooled liquid at the places where the supercool- ing is higher. X = 2 f’ Ö``a3 t1 (31) The liberated latent heat of solidification propagates as Due to the incubation time (Fig. 3), the s / l interface a heat wave and will be dissipated in two ways: will come later on, after a time t , derived from an equation 1. to the mold, through the undercooled metal that lies 2 of the type: between the metal-mold interface and the solidification front; X = X0 + 2 f Ö``a2 t2 (32) 2. to the undercooled liquid lying in the front of the s / l interface, through the negative gradient that will be cre- where, X0 can be calculated b the boundaries conditions: ated. For, t = t0: The Solidification parameters have been quantified by the Schwarz , for positive, zero and negative gradients of X = -X0 + 2 f Ö``a2 t0 (33) the liquid, so that one can use his equations1: The solid phase thickness, varies with time, as: X0 = 2 f Ö``a2 t0 (34) and, therefore: x = 2 f Ö``a2 t (25) The temperature distribution in the solid can be ex- pressed by: Tf - Ti x T2(X, t) = Ti + erf ( ) (26) erf (f) 2 Ö``a2 t A new metal-mold interface temperature will be estab- lished and expressed by: M Tf + T0 erf (f) Ti = = const (27) M + erf (f) where, f, can be obtained solving the following heat Figure 2. Schematic representation of the variation of f and f‘, as a function of S*, for a given metal-mold system. Their behavior is different balance at the S / L interface: because they are described by different mathematical expressions. S* 1 ( - ) exp - (f2) + fÖ``p Lf* = 0 (28) erfc (f) M + erf (f) where, for this particular case: T ’ - T S* = i f (29) Tf - T0 The thermal profile of the liquid in front of the S / L interface is given by: Tp - Tf x T3(X, t) = Tp - erf ( ) (30) erfc (f) 2 Ö``a3 t 2.2.1. Delay and incubation times Figure 3. Influence of the incubation time t0 on the Delay time (t2 - t1) Considering that solidification is a two step process, it and on the equations describing the L / L and S / L interfaces propagation follows that a cooling curve is the result of the displace- inside a metal ingot during solidification. 32 Müller Materials Research Figure 4. Maximum and apparent undercoolings, superheated / supercooled liquid (l /l), solid / liquid (s / l) interfaces, incubation time (t0) and the resulting cooling curve created by a thermal shock in a liquid metal against a cooler mold, after the nucleation’s start. X = 2 f Ö``a2 t0 + 2 f Ö``a2 t2 (35) nation of low heat extraction capacity molds (M > 10: sand molds) and high pouring temperatures. And if the thermal properties of the liquid and the solid Semi-infinite ingots, like the Schwarz ones, would not are the same (a = a ), and considering that (31) and (35) 2 3 solidify in this condition, but the real ones solidify because must be equal, it can be written: the heat flux is not unidirectional. 2 f Ö``a2 Ö````t2 +` t0 = 2 f’ Ö``a3 Ö``t1 (36) They loose temperature evenly, introducing all the liq- uid smoothly into the undercooled stage, until the local f Ö````t2 +` t0 = f’ Ö``t1 (37) Nucleation temperature is attained (TN). Because the gra- dients in the liquid are so low, the nucleation chances are 2 2 f (t2 + t0) = f’ t1 (38) quite the same for all points in the casting, and will produce a random Nucleation pattern and an arrest temperature will f2 t - f’2 t t = 2 1 (39) appear in the cooling curve (Fig.
Details
-
File Typepdf
-
Upload Time-
-
Content LanguagesEnglish
-
Upload UserAnonymous/Not logged-in
-
File Pages10 Page
-
File Size-