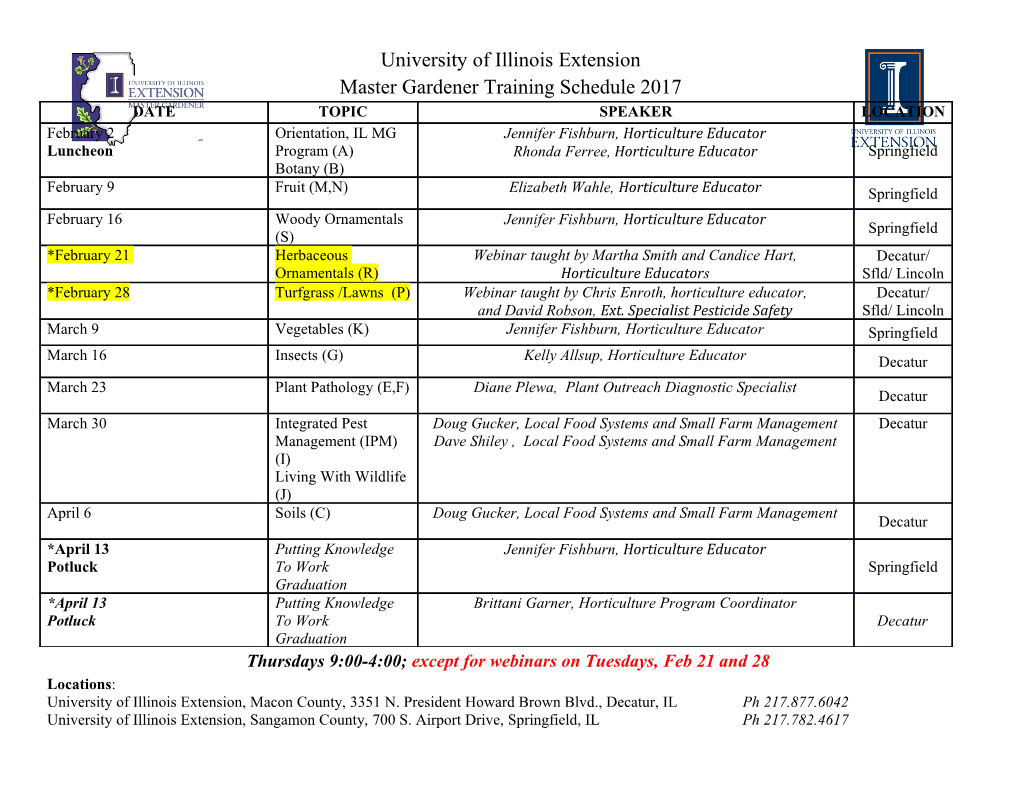
Operations Practice What high-reliability organizations get right Technology isn’t the only—or even the most important—reason high-reliability organizations outperform their peers. by Raffaele Carpi, Peter Claus, Imke Mattik, and Patrick Schulze © iStockphoto/Getty Images May 2019 As Industry 4.0 continues to advance with The three core business practices that breathtaking speed, unleashing new capabilities drive reliability at equally breathtaking speed, it’s all too easy We selected eight best-in-class reliability for business leaders to succumb to relying solely organizations from a cross-section of industries, on technology to drive operational improvement. based on internal reliability metrics (such as Automation, advanced analytics, digital percentage of downtime and overall reliability) and performance management, cloud computing, external performance benchmarks and industry machine learning—all offer powerful and game- awards for operational excellence. We then changing ways for organizations to achieve new interviewed in depth a dozen of their leaders from heights in operational performance. the reliability, operations, or maintenance functions to identify the organizations’ key characteristics and But the costs and effort these technologies and practices. platforms entail can often exceed their payoff. The expectations surrounding them, it turns out, As varied as our study sample was—it spanned are often inflated. Take, for example, advanced the mining, oil and gas, power generation and analytics-driven predictive maintenance. As a distribution, pharmaceuticals, airline, and military means of boosting reliability, it is not the panacea sectors—all the organizations adhere to three many think it is. Without engineers who are trained fundamental business practices (Exhibit 1). in data analysis and in developing solutions based on those analytics, companies cannot HROs implement robust reliability processes. possibly expect to realize the full potential of the All eight organizations follow strong reliability technologies. Often, there are simpler, more cost- processes across their operations, from the ground effective ways to accomplish the same goal. level up. In this respect, they stand out from the average reliability organization, whose processes Moreover, technology alone does not make for are either lacking specifics or inconsistently excellence in reliability. In industries that live by followed. the laws of science, leaders often underestimate the role of management processes and skills in For example, HROs clearly define the assets reliability-engineering success. critical to their operations, ensuring that the list is not merely well-understood but also considered in Research we conducted in a cross-section of decision making. They are skillful in disseminating predominantly heavy-asset industries reveals what the definitions and standards throughout their distinguishes high-reliability organizations (HROs) companies. They create equipment-reliability from the rest. These companies focus as much on strategies and execute them by strictly following the enablers—the rigorous processes, role clarity, preventative-maintenance schedules, closely and accountability systems—as they do on the monitoring equipment health, and identifying issues Industry 4.0 technologies. and proactively or promptly resolving them. Yet as essential as these enablers are, they’re still HROs also engage in root-cause problem solving to not enough. HROs also focus on talent: they put a determine underlying issues and implement holistic, premium on certain skills that other companies don’t, practical solutions. Their reliability engineers draw and they invest more in professional development. on a variety of data sources, tools, capabilities and Finally, HROs structure their organizations subject-matter expertise. according to how centralized the function and its accountability are. To be sure, advanced Another common practice among HROs is that technologies can deliver dramatic improvements, they all have robust systems in place for managing, but ultimately, it’s the human element that spells preserving, disseminating, and updating their success. 2 What high-reliability organizations get right Exhibit 1 Principle 1: High-reliability organizations follow three fundamental business practices. reliability knowledge base—including both done when they need to get done. Period.” HROs reliability analysis and reliability design standards. employ systematic methods to carry out root-cause For instance, these companies effectively share problem solving on the front lines. learnings from every reliability event, and update their equipment-design standards and work They define roles clearly and institutionalize processes accordingly to ensure the event is knowledge. not repeated. Finally, HROs hold other functions Roles and responsibilities are clearly defined and accountable to execute the reliability processes well understood by operational leaders as well as they’ve put in place. all those with whom they work: the plant managers, maintenance leaders, operators, technicians, One manager from an energy company noted supply-chain managers, and so forth. Each member that his organization eschews advanced reliability of the organization has a clear understanding of the techniques or “fancy predictive maintenance role they play in driving reliability, so the guidelines models,” relying instead on traditional root-cause for dealing with and engaging personnel are thus problem solving and defect-elimination approaches unambiguous. A leading pharmaceutical company to get results. Another interviewee, a former US in our research, for example, rotates personnel— Naval submarine officer, put it plainly: the reason including reliability engineers—to give them a there’s rarely a failure of critical equipment “is firsthand understanding of the critical roles in the two-fold: the design is robust, and things just get organization and how they interact What high-reliability organizations get right 3 “The design is robust, and things just get done when they need to get done. Period.” – Former US military officer They set accountability at the executive level levels with those of their competitors. Salaries at and delegate it down. the HROs—average, as well as the low and high HROs believe accountability resides at the top. end of pay scales—were 15 percent higher than To ensure that, they set executive compensation those of their peers (Exhibit 2). HROs also reward according to reliability-specific metrics and high performance; several we interviewed have outcomes. These organizations establish clear developed specific key performance indicators corporate reliability standards and communicate (KPIs) for performance-based compensation and them well: for example, they’re included in bonuses. capability models and reliability metrics, which are tracked publicly on scoreboards. In addition, HROs The fact that HROs pay better is hardly surprising: discuss outcomes at all levels of the organization, in any industry, offering a higher salary is an from the frontline control room to the boardroom. obvious way to attract top talent. But it is by no At a major power generation company, executive means the only way. Nor does it guarantee talent sponsorship is considered a key success factor. retention or reliability success. “Senior executives really bought into frontline support for reliability and communicated its HROs prize communication and problem- importance for our business clearly and frequently.” solving skills. They appreciate that technical expertise alone is not enough for a first-rate reliability HROs put people first engineer. Knowing how to solve problems and HROs recognize that it takes more than technical how to communicate—up, down, and across expertise to make a great reliability engineer. the organization, in ways that earn trust and Our research revealed that to attract and retain support—are critical skills. In fact, HROs rank the best and the brightest, HROs follow three communication and problem-solving among the specific talent-management practices: they five most critical skills in job candidates. pay higher salaries, emphasize communication and coordination skills relevant to the reliability HROs recognize the importance of being able engineer’s role as cross-functional problem solver, to communicate equally well with the frontline and provide well-defined career options and paths. and management; their engineers are adept at translating technical issues into laymen’s HROs offer higher pay than their peers. terms that their non-technically trained peers We analyzed two years’ worth of job postings from can understand. Effective problem solvers are the companies in our sample, comparing their pay solid conceptual thinkers who can understand a 4 What high-reliability organizations get right Exhibit 2 problem or condition by identifying patterns and HROs create attractive paths for career connections that reveal which underlying issues advancement. to address. They’re also leaders: HROs give more Reliability engineers typically follow one of three weight to leadership skills than the more than 70 main career tracks, each with different rates of other organizations in our comparison set (Exhibit 3). retention (Exhibit 4). Creativity and rigor in problem solving are always — Field-based engineer to operations manager: valuable, particularly at a time when organizational Entry-level personnel with technical degrees complexity is growing and the
Details
-
File Typepdf
-
Upload Time-
-
Content LanguagesEnglish
-
Upload UserAnonymous/Not logged-in
-
File Pages10 Page
-
File Size-