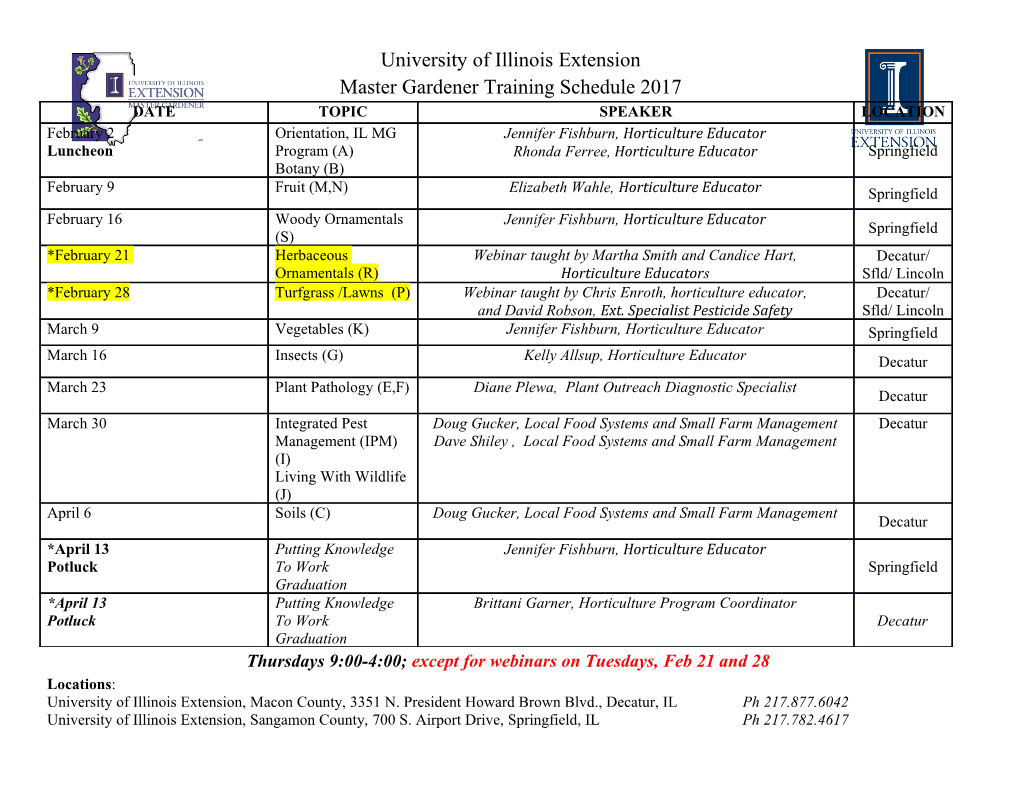
Journal of The Electrochemical Society OPEN ACCESS Review—Electronic Circuit Systems for Piezoelectric Resonance Sensors To cite this article: Jong-Yoon Park and Jin-Woo Choi 2020 J. Electrochem. Soc. 167 037560 View the article online for updates and enhancements. This content was downloaded from IP address 167.96.158.82 on 03/02/2020 at 16:09 Journal of The Electrochemical Society, 2020 167 037560 Review—Electronic Circuit Systems for Piezoelectric Resonance Sensors Jong-Yoon Park1 and Jin-Woo Choi1,2,*,z 1School of Electrical Engineering and Computer Science, Louisiana State University, Baton Rouge, LA 70803, United States of America 2Center for Advanced Microstructures and Devices, Louisiana State University, Baton Rouge, LA 70803, United States of America Piezoelectric mass sensors have been widely studied for a variety of applications as a biological or chemical sensing transducer. With an increasing range of application areas and performance requirements for fast measurement time, higher resolution and accuracy, and compact system size, different measurement electronic systems have also been investigated to fulfill the performance requirements. Selecting a proper type of measurement electronics is critical to develop an optimized sensing system for practical applications. In this review, we cover different types of measurement electronics configurations including impedance-based measurement, oscillator-based measurement, and ring-down technique. Also, we provide an overview of the recent advances of each measurement electronics configuration for piezoelectric resonator sensors. Finally, the pros and cons of each measurement electronic configuration are compared and discussed. © 2020 The Author(s). Published on behalf of The Electrochemical Society by IOP Publishing Limited. This is an open access article distributed under the terms of the Creative Commons Attribution Non-Commercial No Derivatives 4.0 License (CC BY- NC-ND, http://creativecommons.org/licenses/by-nc-nd/4.0/), which permits non-commercial reuse, distribution, and reproduction in any medium, provided the original work is not changed in any way and is properly cited. For permission for commercial reuse, please email: [email protected]. [DOI: 10.1149/1945-7111/ab6cf7] Manuscript submitted November 1, 2019; revised manuscript received January 13, 2020. Published February 3, 2020. This paper is part of the JES Focus Issue on Sensor Reviews. Piezoelectric mass sensing techniques have been widely studied odd harmonics (N = 1, 3, 5,…). The Sauerbrey’s equation is and developed as a mass sensor for various applications, such as applicable to cases of rigid, uniform, and thin-film deposits.13,14 volatile chemical detections,1,2 DNA sequence mismatch,3 protein Early applications of QCM were limited to measuring gas-phase binding,4,5 and so on. Piezoelectric mass sensors have been showing analytes such as volatile organic compounds,15,16 environmental their strong potential especially for biomolecular recognition be- pollutants,17 and gas-phase chromatography detectors.18 cause they provide advantages like real-time monitoring, label-free Applications of QCM have further been expanded, particularly to detection, quantitative/qualitative information, and their affordable biomolecular detections, by introducing QCM in liquid media in the cost compared to the labeling techniques with fluorescent markers, 1980s.19–21 In those papers, they demonstrated the actuation of a radioactive species, and so on.6 quartz crystal resonator (QCR) in high damping media and the Recent advances show that piezoelectric mass sensors have been relationship between frequency shift and mass change in such studied beyond their mass sensing ability by monitoring power conditions. The relationship in liquid media, also known as the dissipation with different harmonics. For instance, monitoring of Kanazawa and Gordon’s equation, is expressed in the equation power dissipation, which is represented as a quality factor or Q below. factor in resonators, provides additional information about binding fi ⎛ ⎞3 molecules and allows the capability of distinguishing speci c 3 rh 2 7,8 2 ⎜ L L ⎟ molecules having the same molecular mass. D=-F f0 ⎜ ⎟ []2 Technological innovations and breakthroughs commonly follow ⎝ prqq m ⎠ novel findings in natural phenomena. The history of piezoelectric ρ η devices started after the Curie brothers discovered the piezoelectric where L and L are the density and viscosity of a liquid medium, effect (or reverse piezoelectric effect) on quartz in 1880.9 Other respectively. studies found that a certain cutting orientation of a quartz crystal QCM has become one of the most common piezoelectric mass plate could provide better frequency stability from temperature sensing tools. A typical QCM is fabricated with two gold electrodes variations.10,11 In modern electronics systems, a quartz crystal has separately deposited on both surfaces of a quartz disc. The resonance become an essential component providing stable reference clock frequency of commercially available QCM discs is usually ranging signals. In 1959, a quartz crystal was first used as a mass sensor from 5 MHz to 20 MHz. The thickness of QCM is a few hundred known as quartz crystal microbalance (QCM), when Sauerbrey micrometers and the diameter varies from a few millimeters to uncovered a linear relationship between the resonance frequency centimeters. While QCM devices usually have a high Q factor and shift of a quartz crystal and the mass of molecules attached on the show good stability at room temperature, sensitivity is limited by the 12 applicable thickness of a quartz slice determining a resonance crystal surface in vacuum or a gas medium. This relationship, also 22,23 known as the Sauerbrey’s equation, is described below. frequency (f0). In recent years, a film-bulk acoustic resonator (FBAR) has 2Nf 2 attracted increasing attention due to its higher sensitivity, lower D=-Fm0 ´D []1 cost, smaller size, and design flexibility. FBAR is a type of Ae rmqq piezoelectric resonators and utilizes a piezoelectric thin film instead where ΔF and Δm are the resonance frequency shift of the quartz of a bulk crystal, which allows miniaturization of a resonator-based sensor to have an array of multiple thin film resonators. For this, crystal and the change of the mass. f0 is the resonance frequency of FBAR has been applied to lab-on-a-chip systems24–27 and integrated the unloaded crystal. Ae is the effective surface area, ρq is the circuits.28 Additional information can be found in papers discussing density, and μq is the shear modulus of the crystal. N is the crystal’s various types of FBAR sensors.29,30 Piezoelectric resonance sensors require a measurement electronic *Electrochemical Society Member. system that can generate oscillation and measure the resonance zE-mail: [email protected] frequency shift. Journal of The Electrochemical Society, 2020 167 037560 The measurement techniques for piezoelectric mass sensors are stand for the motional effect of the resonator. Co and Cp represent usually categorized into impedance-based measurement, oscillator- the capacitance of a piezoelectric material and the parasitic based measurement, and ring-down analysis techniques. The im- capacitance when the resonator is connected to an external electrical pedance-based measurement system basically measures the elec- system. In the modified model in a liquid medium, LL and RL are trical impedance (or admittance) spectrum from the sensor by added to address the influence of the viscosity and the density of applying a sweeping frequency signal to the sensor. The resonance the liquid. LL causes a decrease in the resonance frequency of the frequency and the dissipation factor can be determined by analyzing piezoelectric resonator while RL decreases the Q factor of the the spectrum. On the other hand, in the oscillator-based measure- piezoelectric resonator. ment system, the sensor is actively interrogated in an oscillator In the BVD model shown in Fig. 1a, the impedance plot of the circuit. The oscillation frequency is usually measured by a frequency sensor has minimum and maximum impedance frequency points. counter and the power dissipation of the sensor can be monitored by The minimum impedance frequency or series resonance frequency gain control circuits adjusting the amplitude of the oscillating signal. (fs) represents the motional behavior of the sensor. The maximum In the ring-down analysis technique, the sensor is passively inter- impedance point is formed by the influence of the parallel * rogated by an excitation signal having a frequency near the capacitance (CO ) on the motional behavior of the sensor. The resonance frequency of the sensor. The excitation signal is applied maximum impedance frequency is commonly called a parallel to the sensor for a very short time and the decaying signal of the resonance frequency (fp). The estimated fs is very close to the actual sensor is monitored to determine the resonance frequency and motional series resonance frequency (MSRF) under a high Q factor 32 dissipation factor of the sensor. condition. fs and fp can be calculated by (3a) and (3b) below. The measurement techniques have been improved to fulfill increasing application areas and measurement requirements for 1 fs » []3a several decades. Since they have different operating principles, 2p LCmm each measurement system has different considerations to design the 1 electronics system and to improve its performance. Recent electronic f » []3b configurations have been
Details
-
File Typepdf
-
Upload Time-
-
Content LanguagesEnglish
-
Upload UserAnonymous/Not logged-in
-
File Pages17 Page
-
File Size-