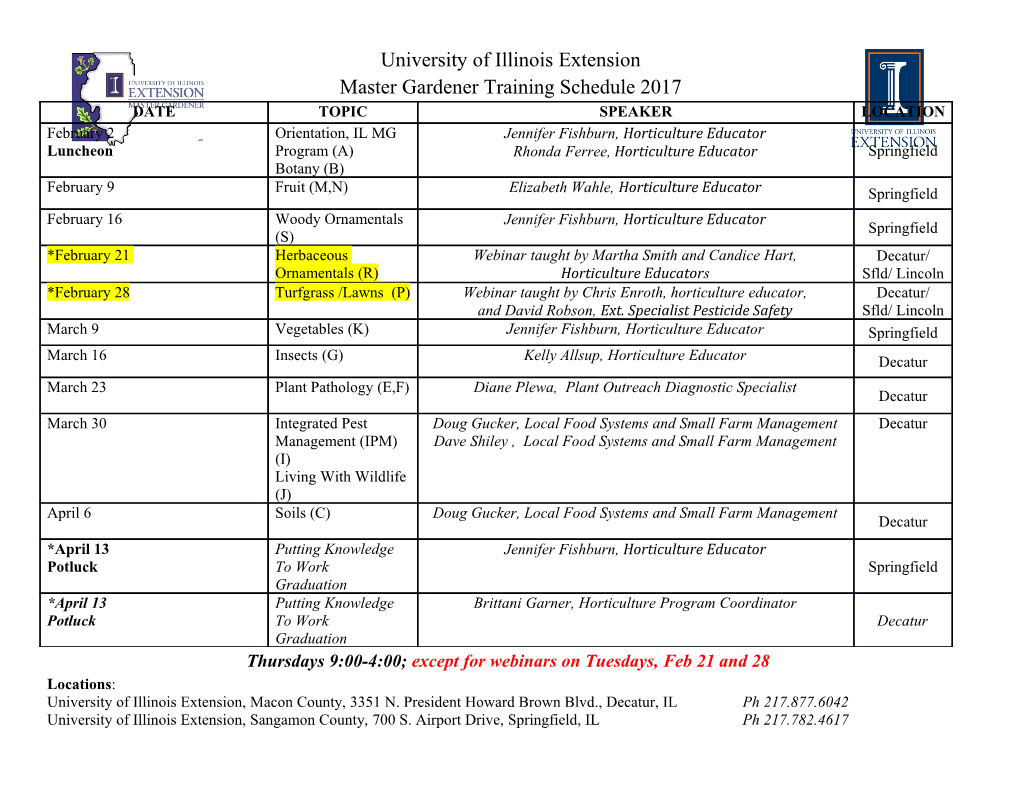
IPT 23 2007 30/8/07 10:15 Page 82 Ingredients, Formulations & Finishing Closed Vial Technology A new technology for the aseptic filling of injectable drugs employs a closed vial – eliminating the need for processes such as washing, depyrogenation and sterilisation, and offering improved sterility assurance and security of supply. By Benoît Verjans at Aseptic Technologies Benoît Verjans has a PhD in Biochemistry, a MBA from the University of Brussels and completed a postdoctoral programme at the University of Cambridge, UK. He has worked at UCB Pharma in International Marketing, at McKinsey and Co as a Consultant, mainly in the pharma sector, and as CEO of 4AZA Bioscience, a start-up from the University of Leuven, developing new immuno-modulating drugs. He is currently Commercial Director of Aseptic Technologies, responsible for developing sales of the closed vial technology worldwide. He is on the Editorial Board of Pharmaceutical Technology Europe and a member of ISPE. The aseptic filling of injectable drugs has always been THE CLOSED VIAL very challenging for the pharmaceutical industry. Contamination accidents, despite being rare, are still The closed vial is a container made of five elements: recorded among the 20 billion injections and infusions made every year in the world. In a recent market study, The Vial Body six per cent of hospital professionals in Europe and the Cyclo-olefin copolymer (COC) is used for this part of US reported that they had already faced at least one the container. This polymer was selected because of its incident of contaminated vials. In recent years, the excellent barrier and transparency properties, making it authorities have taken a radical turn to strongly one of the most popular plastics for containers in the support the most advanced aseptic filling technologies, pharmaceutical industry. The vial bodies are produced by such as the use of isolators. The use of classical injection moulding for the smaller vials, or by injection processes in an ISO5 class A cleanroom are, however, blow-moulding for vials exceeding 3ml in volume. becoming more and more challenged due to the risks from the presence of the operator close to the open The Stopper containers. The emphasis on the quality of aseptic A thermoplastic elastomer with particular laser absorbance filling has also been increased with a recent request properties was selected to enable laser re-sealing. With laser- from the authorities to withdraw preservative agents heating, melting of the elastomer occurs and the two sides whenever possible from injectable products. This of the puncture trace fuse to restore the closure integrity. article reviews a new filling technology that has initially been developed to further increase vial quality The Top Ring for the patient, but also to simplify the filling process This ring secures the closure integrity of the assembly of the for the manufacturer when compared with the classical vial body and stopper with non-return right-angle snap-fits. glass vial. In addition, new features have been introduced to secure the supply chain, such as on-line The Bottom Ring coding by RFID or laser-coding. This ensures very good stability of the vial and a firm hold during piercing and needle withdrawal. The closed vial technology is based on a vial provided clean and sterile with the stopper already in place. The Cap Thanks to this container design, the most complex filling The polyethylene cap protects the piercing area by steps associated with the classical open vial – such as vial keeping it under Class 100 until use by the health washing, stopper washing and hot air tunnel sterilisation professional. This last feature, obtained by a circular rib – are eliminated. The filling is performed by means of a pressing onto the stopper surface, avoids contamination needle piercing the stopper and dispensing the liquid; of the stopper surface during vial storage. after needle withdrawal, the puncture trace is immediately re-sealed with a laser to restore the integrity The manufacture of the vials is also completely of the closure. innovative as they are moulded and stoppered by robots 82 Innovations in Pharmaceutical Technology IPT 23 2007 30/8/07 10:15 Page 83 in a cleanroom Grade A/ISO 5. The manufacturing Figure 1: Layout of the filling line with a capacity up to 36,000 vials per hour process comprises the following steps: N The vial bodies and stoppers are moulded at the same time in two moulds installed in a cleanroom Filling needles Grade A/ISO 5 N Immediately after mould opening, two robot arms Laser pick up the vial body and stopper, and bring them Loading table in front of each other. The assembly is performed by simple pressure of the two elements E-beam N The vials, now being closed, are then transferred by one of the robot arms to an adjacent Capping clean room Grade C/ISO 8 where the addition of top and bottom rings is performed by a fully automatic machine as washing and depyrogenation are not necessary, and the N The vials are packed in corrugated polyethylene vials are in a ready-to-fill state for supply to the boxes, and six boxes are doubled-wrapped in pharmaceutical manufacturer. polyethylene foils N The vials are gamma-irradiated at a minimum THE FILLING LINE of 25 kGray Filling of the vial is performed on a dedicated filling line This process provides vials with extremely high levels of equipped with specific technologies. As shown in Figure quality in terms of sterility and particle and endotoxin 1, the complete filling process – from delivered vials up contamination. Consequently, any additional steps such to filled and capped vials – comprises five steps. A revolution in aseptic filling: Crystal® technology The filling is carried out with a needle piercing the thermoplastic elastomer stopper which is then heat resealed at the penetration point by a laser beam. L Highest sterility assurance level L Simpler and cheaper process technology To conduct an aseptic filling trial with one of your products, please contact us. ASEPTIC TECHNOLOGIES Rue Camille Hubert 7-9, 5032 Les Isnes, Belgium Tel: +32 81 409 410 | Fax:+32 81 409 411 e-mail: [email protected] | www.aseptictech.com IPT 23 2007 30/8/07 10:16 Page 84 Loading Access Barrier System (RABS), with access only through The operator loads the vial from polyethylene gloves and rapid transfer ports. As the doors cannot be boxes using semi automatic opening opened, and direct access is forbidden for operators, a equipment; the risk of contamination by the high quality Grade A/ISO 5 environment is permanently operator is thus kept to an absolute ensured. For specific products – such as cytotoxics, minimum. radioactive products and other potent products – an isolator can be installed to protect the operator from Top Surface Sterilisation contamination by the product. Despite this, as the loading is a manual step, the risk of contamination as a result of human KEY BENEFITS error cannot be excluded. For this reason, an e- beam (beta-irradiation at 25 kGray) is used to Compared with the classical glass vial technology, the re-sterilise the most critical surface – that is, closed vial technology provides a number of key benefits; the top of the vial which will be in contact these can be classified into three major groups: with the filling needle during piercing. Immediately after this, the vials enter directly Better Sterility Assurance and Reduced Figure 2: Overview of through a barrier which maintains a Class 100 Particle Presence the filling process with environment during all filling operations. The most important benefit is an increase in quality for the needle wing located above the vials. During the patient in terms of both levels of sterility assurance filling, the needle wing Filling and particle presence. The higher sterility assurance level moves down to pierce Filling is performed by a 13 G needle which pierces the is obtained by keeping the vial continually closed, so that the vials. At the end, the wings move up stopper, dispenses the volume of liquid and exits by lifting there is no risk of contaminant penetration inside the vial and the vial is firmly (see Figure 2). The needle has a pencil point to eliminate resulting from exposure to the environment. By contrast, held by the bottom any coring effect in the stopper, and to minimise the the traditional glass vial is frequently exposed for periods generation of particles during piercing. The injection holes of more than 20 minutes between the sterilisation tunnel on the needles are located along the side and oriented at a and the stoppering station under HEPA filters; this 30º angle to allow a smooth flow of liquid coming into exposure is totally eliminated with the closed vial contact with the vial walls and not with the bottom. The technology. With regard to the presence of particles, the side wall of the needle is grooved in order to vent the over- full closed vial process generates very limited amounts of pressure generated during filling, ensuring that there is no particles, less than half the amount generated during a pressure increase inside the vial after the filling. classical glass vial filling process. Laser Re-Sealing Another advantage for the patient is provided by To fully restore the closure integrity, the re-sealing of the the newly designed capping technology. The entire pierced stopper is performed by a laser dispensing 6.3 stopper surface is protected by the circular rib located on watts during one second. This laser shot increases the the inner face of the cap, thereby creating additional temperature of the stopper surface to 165ºC to melt the closure integrity. material, which then fuses and restores the closure integrity on cooling down.
Details
-
File Typepdf
-
Upload Time-
-
Content LanguagesEnglish
-
Upload UserAnonymous/Not logged-in
-
File Pages4 Page
-
File Size-