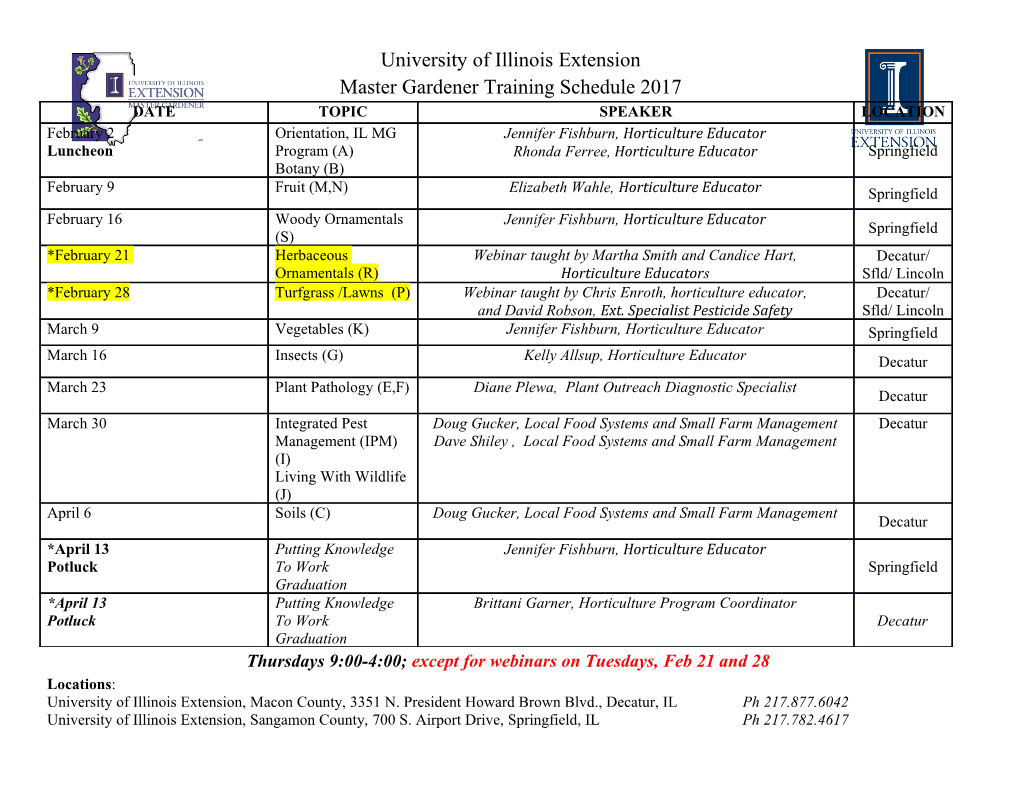
Purdue University Purdue e-Pubs International Compressor Engineering Conference School of Mechanical Engineering 1974 Calculation of the Hydrodynamic Lubrication of Piston and Piston Rings in Refrigeration Compressors H. Kruse Technical University Hannover Follow this and additional works at: https://docs.lib.purdue.edu/icec Kruse, H., "Calculation of the Hydrodynamic Lubrication of Piston and Piston Rings in Refrigeration Compressors" (1974). International Compressor Engineering Conference. Paper 101. https://docs.lib.purdue.edu/icec/101 This document has been made available through Purdue e-Pubs, a service of the Purdue University Libraries. Please contact [email protected] for additional information. Complete proceedings may be acquired in print and on CD-ROM directly from the Ray W. Herrick Laboratories at https://engineering.purdue.edu/ Herrick/Events/orderlit.html CALCULATION OF THE HYDRODYNAMIC LUBRICATION OF PISTON AND PISTON RINGS IN REFRIGERATION COMPRESSORS Dr. H. Kruse, Professor of Refrigeration Engineering Technical University Hannover I Germany 1. INTRODUCTION The calculation of the lubricating condi­ refrigeration compressors,the pistons of tions of a piston is, compared with a slid­ which'can be more lubricated in comparison ing bearing,much more difficult,because the to internal cqmbustion engines, because configuration of the oil film and the operat­ at least with oil soluble refrigerants the ing conditions are much more complicated. lubricating oil is not lost, but is circu­ Whereas the profile of the oil film in jour­ lated back'into the compressor, In spite of nal bearings can be described by eccentric the assumption of fluid friction, the com­ circles, that of a piston is essentially of plexity of the problem has led to the situ­ a more complicated form (Fig.1), ation where h¥drodynamic calculations for oistons (4) lS), and piston rings (6),(7), {a),(9),(1oJ,have been made almost exclu­ sive~y separately. Since however the two components form an interacting unit,it seems reasonable not to consider them separately in the calculation of the lubrication conditions. Eilon and Saunders (11) although assuming the unit of piston and piston rings, apply the hydrodynamic lubrication film theory only to the piston ring, Although they re­ gard the piston clearance as filled with oil and friction-producing, they do not take into account a hydrodynamic production of pressure in the lubrication film. 2. CALCULATION OF PISTON LUBRICATION Here, as already indicated by the author Fig,l Configuration of the oil film between (12) the hydrodynamic calculations are used piston and liner for the common lubrication film on the pist­ The shape of the oil film there is deter­ on and piston rings, which are derived from mined on the one hand by the surface profile the general Reynolds Differential Equation of piston and piston rings which are mathe­ for lubrication films, matically difficult to describe, on the other 3 hand by their position in the cylinder, a~(h ii> + ~(h 3 ~) = 6D(U -U )~~ + 12DV (1) whereby the piston rings are radially and 1 2 axially moveable in the ring groove relative Since there is no analytical solution avail­ to the piston. able for this equation, there are two pos­ As regards the operating conditions,the var­ sible methods for the calculation: iable gas pressure acting on the lubricant 1. Simplification of the problem, so that a film and the quantitatively unknown filling analytical solution is possible, and of the clearance between piston and liner 2, nonanalytical methods by changing this with oil,presents the greater complexity of equation into a difference equation and the problem,which leads to the question,to solving it with the help of a digital com­ what extent the theory of hydrodynamic lu­ puter. brication is at all applicable. To begin with the first method was used,as From measurements of internal combustion basically the same physical fundamentals re­ engines(!), (2), {3), boundary friction oc­ main and influence of the various geometrical and operational parameters on the lubrication c~rs in the region of dead centers at piston rlngs, whereas qver a wide range of the pi­ conditions of the piston can be studied more ston stroke liquid friction takes place. clearly and with less calculating effort, as Concerning the piston in scientific publi­ by an approximate solution through a calcu­ cations in general, the conclusion of a lation programme which demands a large memo­ greater degree of fluid friction is drawn ry and calculation time, from the slight wear, Later,in addition,such an nonanalytical so­ These assumptions can especially be made for lution was used to study parameters which 72 could_not be dealt with by simplified cal­ prof~le ~hrough the surface lines parallel culatlon methods, and to confirm to what ex­ a~d lncllned_to the cylinder wall results in tent t~ey :auld be considered by means of F~g,2 Df a plston section with one piston approxlmatlon_through an analytical solution, rlng, In order to Slmplify the Reynolds Differen­ tial Equation (1) it was at first assum~d y as with the other authors mentioned (4) (s) ( 6 ) , ( 7 )t ( 8 ) that ' ' a) the p~ston ~aves coaxially in the cylin­ der Wlth unlform velocity U2 = U and also the assumptions generally made are valid that ' b) the viscosity n in the lubricating film is constant, c) the cylinder is circular cylindrical, if d) the cross section of the piston is circu­ lar, and -U e) the piston rings posess an equal radial '-+---- A -------< pressure distribution over the circumfe­ rence, Fig,2 Sliding element of the piston Foran analytical solution of the Reynolds Differential Equation the lubricant film Here the real piston profile could be ap­ height configuration ~etween the liner and proximated not just by one but by a number the piston ring is described by straight li­ of straight lines of various positive a~d negative inclination rnA , in the same way nes parallel and inclined to the cylinder as ~he s~rfa:e o~ the piston ring also has wall with an inclination m, varlous lncllnatlons mB and m , ~iston ring pro~iles are also often approx­ 0 Between the piston and piston ring region l~ated mathematlcally by parabolic expres­ there occurs a step in the lubricant film, s:ons, yet wedg7 surface statementsas in (7) glVe results whlch agree more with measured Lord R~y~eigh (13) first proposed step sha­ values, ped sl:dlng elements for bearings, Although an real sliding surface profile on These ldeas were later taken up-by Archi­ pistons and piston rings can be better dealt bald_for thrust (~4) apd later for journal bearlngs and_are lntended here to be applied wi~h.by approxim~tion calculations by des­ crlblng the lubrlcant film configuration as t? the step ln the lubrication gap of a points in a height_array, however here they plston. By application of the equation (3) for each ought to be approxlmated by mathematical section A,B,C and D qnd the integration equations, in order to make clearer the in'­ taking int? account the boundary qonditi~ns fluence of the geometric parameters on the that the all film pressuresat both ends cor­ lubrication conditions, respond to the ambient pressure and should Under.the above mentioned conditions, the be equal at the boundaries of each region, t~o rlght ~and parts of both sides of equa­ one gets as a result the equations giving tlon (1) dlsappear, so that for the one di­ the load capacity and frictional forces for­ mensional problem without side leakage and the oil film pressure p and the shear stres­ radial movement it is simplified into equa­ ses T. tion (2) The film pressures in the different sections A,B,C,D are as follows d <h 3 • .2.l?.d ) = 6 n u£12 (2) dX X dX PA 1)) = rnA6nU(hc~- 2 ai JL)-(JL-a2 a a (6) and reads after integration 1 1£ = 6 ufi - h dx n hT"" ( 3) P = .§.!J.1!(hcl - ..L)-c..L - JL)) (7)- Aa2 rnA 2 af a~ a 1 a 2 Here h is an integration constant which = 6 nu ( h ( 1 1 ) 1 1 ) PB ffi2i)'Z- b2 -(b- b)+ PA 2 (B) stands for the thickness of the lubrication B 1 1 a film at which the pressure gradient in the lubrication film is _i!J.Qh..l. 1 1 1 PBb2 - mB (2<bf - b~)-(b - b >) (g) 2 .2.2- 1 dx - 0 Pc = PAa 2 +, PBb 2 6nUh~~(D + C - x) (10) so that with e~uatt~n ~ 4) for the oil flow h- - __ .£12. (4) qx = 2 12n dx = 6 nu < h 1 + 1 ) PD (11) when h = ,fi mD 2'd"' - d 2h fi.Q qx = 2 ( 5) whereby additionally Gilmbels boundary con­ the "medium film thickness" h represents a d~tion dp/dx = 0 is applied at the cavita­ rate of oil flow relative to half velocity tlon of the oil film in region D as a result of the film diverging.This equation states of the piston. that the oil film pressure constantly turns The approximation of the real sliding surface 73 into the ambient pvessure here,The shear n,U,and PE as operating conditions,along stresses are as follows with changing gas pressures on both sides 4 h of the lubricating film and the partial fil­ (12) 1=nUCb - 3ET) (13) ling of the lubrication gap with oil,which further influence the lubrication conditions, Pnuc.!!. - 31i...> (14) 1;:nuci - 3~d- > (15) For the investigation of these various in­ c c2 d fluencing factors the derived equations were with the integration constant fi as the rate progammed and the individual parameters were of relative oil flow, by equalizing of the varied1>,in order to ascertain theiv effect pressures Pc and p "at x=D oil 0 resulting to on flow, pressure and friction in the equation (10): lubrication gap of a piston of D=85 mm 0, chosen as an example,The initial values of calculation were: · Lengths: Thickness: (16) .
Details
-
File Typepdf
-
Upload Time-
-
Content LanguagesEnglish
-
Upload UserAnonymous/Not logged-in
-
File Pages9 Page
-
File Size-