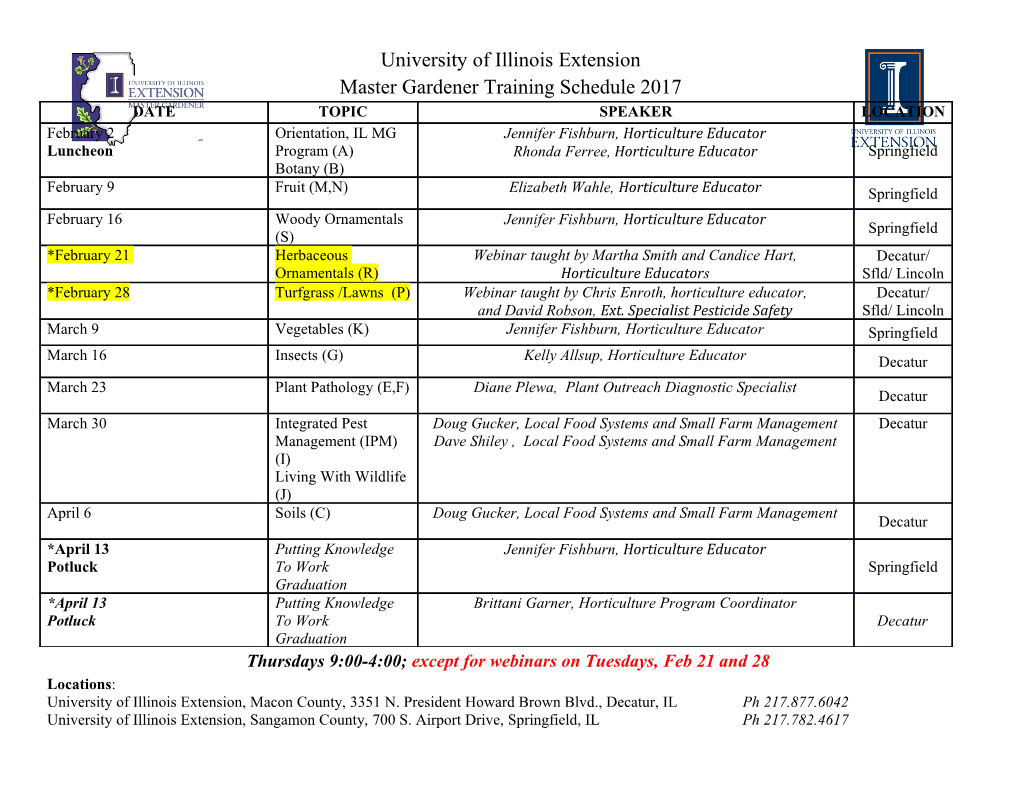
Versatile Hall magnetometer with variable sensitivity assembly for characterization of the magnetic properties of nanoparticles Jefferson F. D. F. Araujo1*, Daniel R. P. Vieira1, Fredy Osorio1, Walmir E. Pöttker 2, Felipe A. La Porta2, Patricia de la Presa 3,4, Geronimo Perez 5 and Antonio C. Bruno1 1Physics Department, Pontifical Catholic University of Rio de Janeiro, Rio de Janeiro 22451-900, Brazil 2Federal Technological University of Paraná, Laboratory of Nanotechnology and Computational Chemistry, Avenida dos Pioneiros 3131, 86036-370, Londrina, PR, Brazil 3Institute of Applied Magnetism, UCM-ADIF-CSIC, A6 22,500km, 28230 Las Rozas, Spain 4Material Physics Department, UCM, Ciudad Universitaria, 28040 Madrid, Spain 5Materials Metrology Division, National Institute of Metrology, Standardization and IndustrialQuality (Inmetro), Av. Nossa Senhora das Graças, 50, Xerém, CEP: 25250-020, Duque de Caxias, RJ, Brazil *Corresponding author: [email protected] Abstract A Hall magnetometer with variable sensitivity is constructed to measure the magnetic properties of magnetic nanoparticles manufactured by different methods. This novel magnetometer can also be used to measure bulk materials and samples in liquids. The magnetometer is constructed with two commercial Hall-effect sensors in an acrylic structure, which serves as the support for a micrometer and the circuit board with the sensors. For operation, the magnetometer it acquires a complete magnetization curve in a few minutes. If has a magnetic moment sensitivity of 1.3 × 10-9 Am2 to sensitivity of 493 mV/mT, the sensitivity can be adjustable in the range of 10 to 493 mV/mT. Its performance is tested with magnetic nanoparticles. As an application example, we estimate the mean diameter of the nanoparticles using the magnetic curves. The results are compared with those obtained by other techniques, such as transmission electron microscopy (TEM), X-ray diffraction (XRD) and dynamic light scattering (DLS). The magnetization results are also compared with those obtained by independent commercial magnetometers, which reveals errors of approximately ±0.31 Am2/kg (i.e., 0.6%) in the saturation region. 1 1. Introduction Extensive studies on magnetic properties of diverse advanced materials have been performed to analyse physical phenomena and evaluate their potentials for engineering applications [1-5]. The Curie temperature, saturation magnetization, remanent magnetization, coercive field, and magnetic anisotropy are among the most important parameters of magnetic materials, determining their applicability. Several magnetometers, including those based on a superconducting quantum interference device (SQUID) [6], magneto-optical Kerr effect [7-8], alternating gradient [9], vibrating samples (VSM) [10], and the Hall effect [11,12], with different sensitivities and costs, have been designed and successfully used. Also, magnetic nanoparticles have a large potential for biomedical applications [13-15]. With the progress in the applications of magnetic materials in several fields of nanotechnology, particularly in the last decades, the interest in magnetometers increases. The extensive studies have led to the development of high-quality devices with a wide range of sensitivities. However, most of these magnetometers are expensive and thus unaffordable for use in low-budget laboratories. In this study, we present a different measurement approach for the magnetization curves using a magnetometer based on Hall-effect sensors with variable sensitivities. It enables to measure in a cylindrical format (sample holder in cylindrical format), samples bulk, liquids, microparticles and nanoparticles with mass in the range approximately 900 μg and 40 mg without the need to change sensors or measurement systems. In this system, we use equipment normally accessible to most laboratories, including an electromagnet, current source, and data acquisition module. A particular advantage of this approach is that the magnetometer can be rapidly assembled and disassembled. Therefore, the equipment can also be used in other experimental configurations. The core of the magnetometer consists of an acrylic plate, which acts as 2 a support for the sensors, micrometer, and the sample holder. In most magnetometers, a magnetic dipole model is usually used to obtain the moment of the sample. However, when the sample is near the sensor, as in the assembled magnetometer, the sample geometry cannot be neglected. Therefore, the dipole model commonly used to obtain the magnetic moment of the sample introduces significant errors [16]. The model is improved by considering the geometry of the sample holder to more accurately estimate the magnetic moment of the sample. We test the magnetometer with magnetic nanoparticles fabricated using the co-precipitation method. This method is fast and versatile, and allows the obtaining of a great variety of magnetic nanoparticles presenting a great number of advantages, such as small reaction time, obtaining particles with few agglomerations, low cost, large quantities and still allows us to control size and distribution of the obtained nanoparticles, through the variation of parameters such as pH [1,11-12]. The mean diameter of the magnetic cores of the nanoparticles is estimated through the magnetic curves, and compared with those obtained using other techniques, such as transmission electron microscopy (TEM), X-ray diffraction (XRD) and dynamic light scattering (DLS). The prepared samples weigh a few tens of milligrams. 2. Magnetometer probe design There are only a few basic components used in the structure of the magnetometer the electromagnet, direct current (DC) source, and Hall-effect sensor. All of the parts necessary to assemble the magnetometer are shown in Fig. 1, which include the following components: (a) acrylic structure (200 mm (length) x 72 mm (width) with slot dimensions of 86 x 45 mm2), which serves as a support for the micrometer and as the base where the sensors are mounted; (b) a micrometer, which aligns sensor 1 with respect to the magnetic field applied by the electromagnet; (c) a cylindrical arm (14 mm (diameter) x 75 mm 3 (length)), connected to the micrometer; (d) acrylic piece (45 x 45 x 22 mm3), which is connected to the arm and has two perpendicular grooves, one of them is used to fasten the Hall devices (45 x 8 mm2) connected to the cylindrical arm, while the other is used for the sample holder; (e) circuit board (8 x 32 x 2 mm3), where two Hall-effect sensors (AD-AD22151, Analog Devices, Inc.) are mounted; (f ) acrylic piece (5.0 x 3.0 x 30 mm3), which is the sample holder used to accommodate samples in a cylindrical cavity with a diameter of 3.0 mm and length of 3.0 mm; and (g) the poles of the electromagnet (diameter: 40 mm). The sample sensor is connected to the micrometer at the cylindrical arm (see Fig. 1.(c)), so that it can be rotated and placed as perpendicular as possible to the electromagnet before each measurement. In this setting, the sensor senses as low as possible magnitude of the electromagnet's applied field. This system is placed between the poles of the electromagnet and connected to a data acquisition board, through a filter (SR560 low-noise preamplifier, Stanford Research Systems), and to a computer. A program was written in LabView® to control the current source and receive data from the two sensors (in volts) during the measurement procedure. A voltage of 5.0 V DC was applied to circuit; under these conditions, the sensors have adjustable sensitivities of 10 to 493 mV/mT. The sensor has an active area of 0.20 x 0.20 mm2. As shown in Fig. 1, the magnetometer was tested by attaching it to an acrylic plate between the poles of the electromagnet (3470 GMW, Inc.). This plate contains two AD22151 Hall-effect sensors (sensor 1 measures the induced field of the sample, while sensor 2 measures the field applied by the electromagnet). With a pole diameter of 40- mm, this electromagnet can generate a field of 1.0 T at a pole gap of 10 mm and current of 5.0 A. Using our magnetometer probe, an entire magnetization curve, with approximately 60 points, is generated in less than 15 min. A thermocouple connected to 4 the pole at the sensor position detected no change in temperature during the measurement period, even at 1.0 T. However, the AD22151 Hall sensor has a sensitivity drift error smaller than +1% over a wide temperature range. We retained the sensitivity temperature compensation setting at its factory default, which is typically -500 ppm/°C; no water cooling is required to operate the electromagnet at this level. In addition, at this pole gap (width of the acrylic plate), the generated magnetic field is homogeneous, which the homogeneity is suitable for the as-prepared sample sizes. b e a f c d g Fig. 1. Components of the constructed magnetometer: (a) Acrylic structure [200 mm (length) x 72 mm (width) with slot dimensions of 86 x 45 mm2]; (b) Micrometer; (c) Cylindrical arm [14 mm (diameter) x 75 mm (length)]; (d) Acrylic piece (45 x 45 x 25 mm3) connected to the arm; (e) Circuit board (8 x 32 x 2 mm3), where two AD22151 Hall-effect sensors are mounted; (f) Acrylic sample holder (5.0 x 3.0 x 30 mm3); (g) electromagnet pole (diameter: 40 mm). The internal structure of the AD22151 Hall sensor a contains Wheatstone bridge, where the sensitivity values are related to the resistances used to close the operating 5 circuit, as indicated in Table 1. The resistors are placed on a board connected to the acquisition unit (model 34970A, Agilent), where the user can select the resistors used to close the circuit. This resistance change procedure using the acquisition unit was automated and coupled in a program written in LabView®. The values shown in the second column of Table 1 are the results of the calibration of the Hall sensors, i.e., the results of the analysis used to determine the voltage produced when the sensor responds to a field of a known magnitude.
Details
-
File Typepdf
-
Upload Time-
-
Content LanguagesEnglish
-
Upload UserAnonymous/Not logged-in
-
File Pages20 Page
-
File Size-