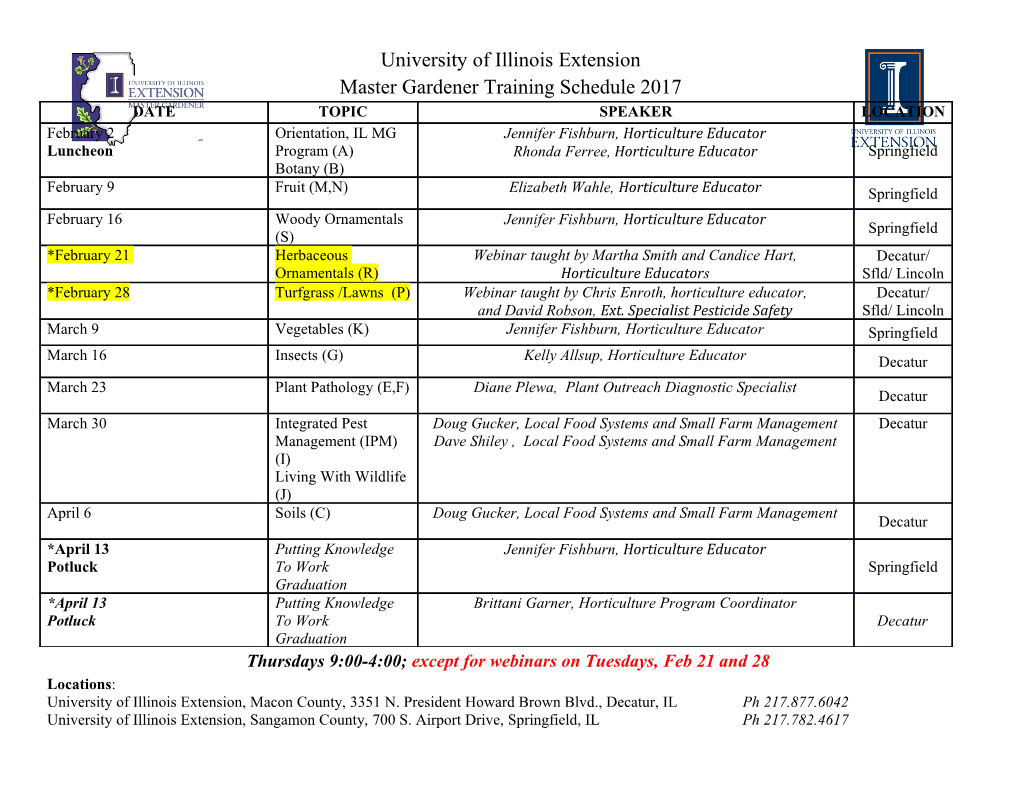
Chapter 9 Diffusion Bonding: Influence of Process Parameters and Material Microstructure Thomas Gietzelt, Volker Toth and Andreas Huell Additional information is available at the end of the chapter http://dx.doi.org/10.5772/64312 Abstract Diffusion welding is a solid joining technique allowing for full cross-section welding. There is no heat-affected zone, but the whole part is subjected to a heat treatment. By diffusion of atoms across the bonding planes, a monolithic compound is generated. The process takes place in a vacuum or inert gas atmosphere at about 80% of the melting temperature and is run batch-wisely. Hence, it is rarely used despite its advantages to achieve holohedral joints and is widespread in the aerospace sector only. The quality of a diffusion-welded joint is determined by the three main parameters bonding temperature, time, and bearing pressure. The difficulty tailoring the process is that they are interconnected in a strong nonlinear way. Several additional factors may influence the result or may change the material, e.g. surface roughness and passivation layers, all kinds of lattice defects, polymorphic behaviour, and formation of precipitations at grain boundaries, design of the parts to be welded and its aspect ratio as well as mechanical issues of the welding equipment. Hence, experiments are necessary for almost each special part. In this chapter, an overview about the experience of diffusion welding is given. Influences are discussed in detail and conclusions are derived. Keywords: diffusion welding, diffusion bonding, lattice defects, grain growth, precip‐ itation, sensitization, passivation layer © 2016 The Author(s). Licensee InTech. This chapter is distributed under the terms of the Creative Commons Attribution License (http://creativecommons.org/licenses/by/3.0), which permits unrestricted use, distribution, and reproduction in any medium, provided the original work is properly cited. 196 Joining Technologies 1. Introduction Diffusion welding is the only welding technique by means of which full cross-sectional welds, also of internal structures, can be obtained. Normally, there is no liquid phase and the monolithic compound is formed completely under solid-state conditions. For the conditions to be appropriate, mechanical properties across the joined part are compa‐ rable to the bulk material. Due to heating of the whole parts, no distinct heat-affected zone (HAZ) is formed. However, properties are changed compared to the as-delivered conditions of the material. This may cause problems in some cases. For diffusion welding, special and expensive equipment is required: the parts have to be mated at high temperatures by applying high forces depending on the size and cross-sec‐ tion to be welded under a vacuum or inert gas environment. Equipment and parts are heat‐ ed mostly indirectly by radiation. To limit thermal stress, the heating rates are restricted to some 10 K/min. The welding process takes place in vacuum and cannot be performed on site. Mating surfa‐ ces must be free of any impurities and have a low surface roughness without deep scratch‐ es. Joining of multiple layers is possible in one step. Diffusion welding is always accompanied by a certain deformation of the parts. This defor‐ mation depends mainly on bonding temperature, bonding time and bearing pressure. Unfortunately, influences of temperature and bearing pressure are non-linear, making it difficult to predict the deformation of a new design. Additionally, secondary impacts on deformation and the quality of joining may be due to specific geometric parameters, e.g., the aspect ratio, the number of layers, the micro-structure of the material itself and surface layers. Recently, thin coatings of other metals, forming a temporary liquid phase (TLP) by passing a eutectic composition, or multiple layers of different metals of nanometre thickness exploiting the enormous interfacial energy of such compounds were investigated. In contrast to conventional welding techniques, such processes are highly complex. The process has to be optimised for each material and even for different compositions of alloys depending on the geometry. For this reason, application of diffusion welding is limited to the aerospace industry or special applications where other welding techniques fail. For ex‐ ample, large- and thin-walled titanium sheets are joined to reinforcing structures and inter‐ nal cooling channels for injection moulding tools and nozzles of rocket engines. Unfortunately, not all the information necessary for reproducing the results, e.g., material, procedure of sample preparation and process parameters, is given in the literature. For joining micro-structured components, additional aspects must be taken into account. The aim of this chapter is to summarise knowledge on diffusion welding in conjunction with the fundamental processes taking place inside of the micro-structure of a material. For this, lattice defects are discussed according to their dimensionality. Diffusion Bonding: Influence of Process Parameters and Material Microstructure 197 http://dx.doi.org/10.5772/64312 2. Micro-structure of metals and the impact of lattice defects on diffusion welding 2.1. Atoms in the lattice of metals To minimise the energy of a system, isolated metal atoms tend to arrange in a regular lattice at positions according to the annihilation of attractive and repulsive forces (Figure 1). The positions are well-defined and specific of each metal. Hence, they can be used, e.g., for determining the composition of an alloy by means of WDX (wavelength dispersive X-ray). When forming a compound, atoms split up into positively charged atomic nuclei, while valence electrons are transferred to the so-called electron gas and can move freely within the lattice. Consequently, metals are good conductors of heat and electricity. Figure 1. Equilibrium of attractive and repulsive forces in the metallic lattice [1]. 2.1.1. Thermal expansion Depending on the thermal energy of the whole system, the positively charged atomic nuclei oscillate around their position, leading to a thermal expansion (Figure 2). According to Grüneisen's rule, linear expansion is in the range of 2% and volumetric expansion is 6–7% up to the melting point of a metal [1]. Hence, the melting point can be used to estimate the thermal coefficient of expansion. Below the melting temperature, the oscillation amplitude is about 12% of the lattice constant [2]. Figure 2. Thermal oscillation of atoms. 198 Joining Technologies 2.1.2. Thermal activation, diffusion, polymorphism and zero-dimensional lattice defects With increasing thermal oscillation, not only the amplitude increases but also the energy of collisions between atoms. Gradually, some atoms are facilitated to leave its lattice sites and a vacancy is left leading to a punctual stress state (Figure 3). With increasing temperature, an exponentially increasing number of atoms is displaced from the lattice sites and the density of vacancies is considerably enhanced (Eq. (1)): næ-D U ö cV = * exp.ç ÷ (1) Nè RT ø Figure 3. Vacancy in the lattice causing punctual stress. where cV is the concentration of vacancies (cm−3), n is the number of vacancies, N is the number of sites in the metallic lattice, U is the energy of formation of vacancies (for metals 80–200 J/ mol), R is the gas constant (J/mol*K) and T is the temperature (K). Vacancies are regular lattice sites not occupied by an atom. Due to a missing atom, the surrounding atoms tend to fill the gap and the lattice is distorted at this point, representing a zero-dimensional defect. According to [3], the density of vacancies is 10−12 at room temperature and increases to 10−4 below the melting temperature. Vacancies strongly facilitate the diffusion of atoms between different sites of the lattice and, hence, concentration facilitates the formation of a monolithic compound during diffusion welding. As a consequence, the coefficient of diffusion increases exponentially with temper‐ ature (Eq. (2)). An increase in bonding temperature by 20 K may result in a doubling of the diffusion coefficient, thus illustrating the strong non-linear influence of temperature on diffusion welding: æ-DU ö DD= 0 *exp.ç ÷ (2) èRT ø Diffusion Bonding: Influence of Process Parameters and Material Microstructure 199 http://dx.doi.org/10.5772/64312 2 2 where D is the diffusion coefficient (m /s), D0 is the frequency factor (material constant) (m /s) and U is the energy of formation of vacancies (J/mol). The number of vacancies versus temperature can be plotted as a logarithmic function, the so- called Arrhenius plot (Figure 4). Figure 4. Arrhenius plot. The density of vacancies increases with a logarithmic dependency with temperature. Depending on the real micro-structure of technical materials, different types of diffusion can be distinguished corresponding to different activation energies for different lattice defects. Straight lines for different diffusion paths can be plotted for surface, grain boundary and volume diffusion, respectively (Figure 5). For diffusion welding, grain boundary diffusion predominates at low and medium temperature. As the cross-section of grain boundaries is related to the volume and the density of vacancies increases exponentially, volume diffusion becomes predominant at high temperature. Figure 5. Different modes of diffusion of atoms versus temperature [1]. 200 Joining Technologies At the same time, grain growth takes place at high temperatures, which minimises the interfacial energy of the system. If the material shows no polymorphic transformation or the grain boundaries are not pinned by insoluble intra-granular precipitations (e.g., for ODS alloys), diffusion welding will be accompanied by grain growth. Technical materials are no pure metals, but also contain other sorts of atoms, e.g., alloying elements like manganese, chromium or carbon for steel. Similar to vacancies, these atoms are integrated into the basic lattice as zero-dimensional defects. If they form the same type of lattice (e.g., cubic face-or cubic space-centred), and if the difference in atomic radii is less than 15%, they can occupy regular sites of the host lattice [4].
Details
-
File Typepdf
-
Upload Time-
-
Content LanguagesEnglish
-
Upload UserAnonymous/Not logged-in
-
File Pages22 Page
-
File Size-