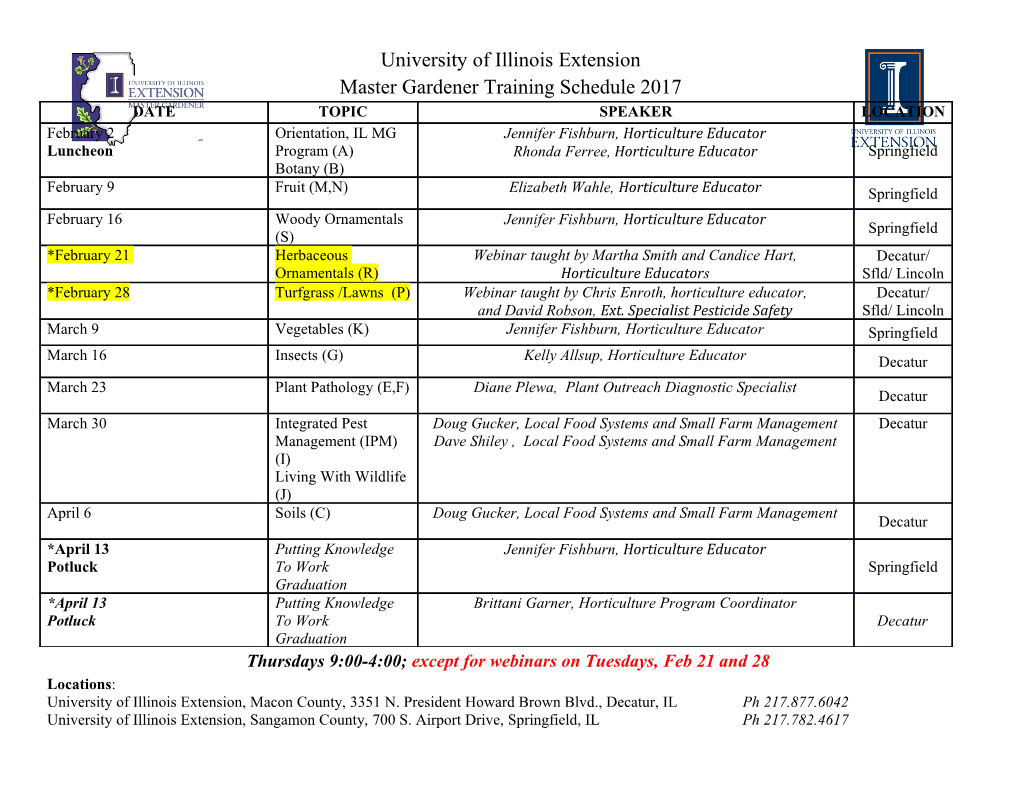
Arch. Comput. Meth. Engng. Vol. 11, 2, 143-186 (2004) Archives of Computational Methods in Engineering State of the art reviews Computational Methods for Tension-Loaded Structures Thouraya Nouri-Baranger Centre de M´ecanique Universit´e Claude Bernard Lyon 1, France E-mail: [email protected] Summary This paper deals with tension loaded structures made of coated woven fabric, cables and rigid frames such as mats and hoops. It describes in details a general framework for modelling and numerical simulation of their mechanical behavior. Several methods, developped in these last decades, are presented and compared. The principal particularity of these structures is that they derive their stiffness and their stability from the surface geometry and tensile stress field coupling. This particularity is combined with nonlinearities which can be due to possible large deflections, material law behavior and local instabilities due to wrinkling effects. In addition, a great number of design parameters must be taken into account in order to optimize the mechanical behavior of the structure. Therefore, the design and the analysis of such structure are complex and involve extensive computational costs. The principal steps of the analysis process are: form-finding, structural response of the structure to loads, cutting pattern and optimization. In this work, after a short description of the methods developed in this field as well as a critical comparison, new approaches are proposed. 1INTRODUCTION A growing number of architectural structures are today protected by fabrics that are ten- sioned over structures such as plywood, concrete and metal. The most significant membrane structures include the Haj Terminal at Jeddah (Saudia Arabia) whose roof extends over a 430000 m2 surface, the arenas of Nˆımes (France) and Zaragoza (Spain) and the Mil- lennium dome− in Greenwich (United Kingtom). Textile materials have enabled architects to design new shapes erstwhile impossible to achieve with standard materials. However, besides the aesthetic considerations, these techniques offer several advantages: the struc- tures are lightweight, are able to cover large surfaces with no ground attachments, are deployable, convey natural light and can easily be adapted to existing structures. Several engineers and architects have been singled out for their work on these types of structures since the beginning of the twentieth century. These pioneers include Otto Frei [19] and Kasuo Ishii [31]. Owing to specification requirements and thermal and acoustic properties of textile materials, these structures are limited to public and standard industrial buildings with no special requirements. For example: sports & leisure facilities,train stations and airport terminals, exhibition halls, industrial facilities. Tensile fabric structures present a nonlinear mechanical behaviour under various ex- ternal loads. The flexibility of the fabric and the tensile requirement lead to a coupling between the surface shape representing the roof and the prestress loads required to keep the fabric taut. The fabric is an orthotropic composite and the free-form surface is obtained from plane fabric cutting patterns. The design, engineering analysis and implementation of a tensile fabric structure calls for elaborate procedures requiring a certain number of spe- cific tools. Several CAD tools have been developed since the 1980’s. The following is a list of some of these: Easy software [23], Archimedes software [63], Meftx software [17], Tensys software [81], Artex software [80] and MecTex [53]. All these tools follow the same global approach except Artex, which only deals with purely geometrical design aspects and does c 2004 by CIMNE, Barcelona (Spain). ISSN: 1134–3060 Received: October 2003 144 Thouraya Nouri-Baranger not provide an engineering analysis. The design and analysis of the mechanical behaviour of such structures goes through four major steps: 1. Definition of an initial geometrical design conform to functional, architectural and aesthetic aspects (generally dictated by the architect). 2. Definition of a stable equilibrium state for the above-mentioned geometry and deter- mination of an initial state of stress to keep the tensioned structure in equilibrium. 3. Modeling of the mechanical behaviour of the structure under external loads and anal- ysis of the rupture criterion. 4. Definition and optimization of the fabric cutting patterns to determine the shape of the structure. The fabric is a material where only tensile stress can be generated. It naturally does not have any elastic stiffness with bending nor with compression. It is therefore essential to stretch the fabric allowing it to respond to bending loads but also to impede direct response to compression stress through the appearance of wrinkles. Therefore the geometrical shape of a tensile structure and the stress state of the membrane are closely related and cannot be dealt with separately as there is coupling between the loads and the geometry. Therefore the execution order of these steps cannot be pre-established and successive iterations between certain geometrical shapes are required in order to reach favourable results. The result should comply with safety standards, feasibility studies and should take into account the membrane boundary conditions. 2THEFABRIC The technical fabric used in architecture is a multi-layer composite comprising the woven fabric and the coating. The result is a flexible composite with a woven reinforcement and securing a macroscopically periodic structure. This fabric is made up of interwoven threads (high tenacity polyester or fiberglass) which follow two perpendicular directions, the warp and weft. The type of cloth, taffeta or satin used determines the geometry of the basic shape. The coating ensures impermeability as well as the strength and weldability of the fabric. The coatings most used are as follows: PVC (polyvinyl chloride), Teflon (polytetrafluorethylene) and Silicon. The macroscopic behaviour of the coated fabric presents a nonlinear geometry in view of the weaving and coating operations. In practice, fabric behaviour rules can only be perceived realistically after specific tests have been carried out on samples [49]. Parallel to these tests, theoretical models can also lead to the numerical determination of the behaviour rules [42]. This type of method assumes an exact appreciation of the basic shape geometry and awareness of the rheological properties of the fibers and coating. The following is a list of influences or parameters, which characterize the mechanical behaviour of the fabric: the density, or number of threads per unit length according to each warp and weft • direction. the contraction which describes the fact that the weaving is more or less slack and • therefore that a warp and weft yarn alteration step is conducted during the 1st loading stage. The contraction phase is assimilated when the fabric is first tensioned and corresponds to a 0.5% to 5% deformation according to the weaving. Computational Methods for Tension-Loaded Structures 145 The hysteresis phenomena characterizes the invariability of the first deformations. • This phenomena has been the subject of many papers including [9]. For clearer understanding, our models only include the values obtained by averaging the stress curve-biaxial tension study results. See [13], [63] and [9] Once the fabric has been tensioned, we can consider that it has near linear character- istics. This is the model used by most authors carrying out research on the mechanical analysis of tensile fabric structures. The fabric is a very thin flexible material, it does not resist to compression stress and only has bending strength if it is pre-taut. There- fore, to represent the behaviour of the fabric a two-dimensional elastic membrane model is used. The weaving does not generally present a weaving symmetry therefore we used a two-dimensional orthotropic model. The main orthotropic directions are the warp and weft. The elastic stiffness matrix is formulated in these orthotropic axes as : E ν E w fw w 0 (1 νwf νfw) (1 νwtνtc) C = ⎡ −νwf Ef −Ef ⎤ (1) 0 ⎢ (1 νwf νfw) (1 νwf νfw) ⎥ ⎢ − − ⎥ ⎢ 00Gwf ⎥ ⎣ ⎦ where w and f refer to the warp and weft directions, Ew, Ef are Young ’s modulus, νwf is Poisson’s ratio and Gwf is the shear modulus. In any point of reference with an θ angle with regard to orthotropic directions, the elastic stiffness matrix is characterized as follows: t C = TθCT( θ) (2) − c2 s2 cs 2 2 − Tθ = s c cs (3) ⎡ 2cs 2cs c2 s2 ⎤ − − ⎣ ⎦ where c =cos(θ)ands =sin(θ), Tθ is the rotation matrix. 3 FORM FINDING OF AN INITIAL SURFACE IN EQUILIBRIUM STATE Unlike certain flexible structures such as sails which are kinematically undetermined, we studied configurations where it was essential to stretch the fabric in order to obtain signif- icant bending stiffness while avoiding slack and the appearance of wrinkles (the kinematic condition is lifted following the geometric stiffness set by the prestress). The prestress state required depends on the limits with the rupture of the materials, the boundary conditions of the structure, the shape required and the external loads. A tensile structure presents a nonlinear mechanical behaviour in response to any kind of loads. This nonlinearity is geo- metric and mainly related to large displacements and prestress. The strain field is assumed to remain within acceptable limits for minor disturbances. Hence, the above assumptions must be taken into account to formulate the initial equilibrium state of the
Details
-
File Typepdf
-
Upload Time-
-
Content LanguagesEnglish
-
Upload UserAnonymous/Not logged-in
-
File Pages44 Page
-
File Size-