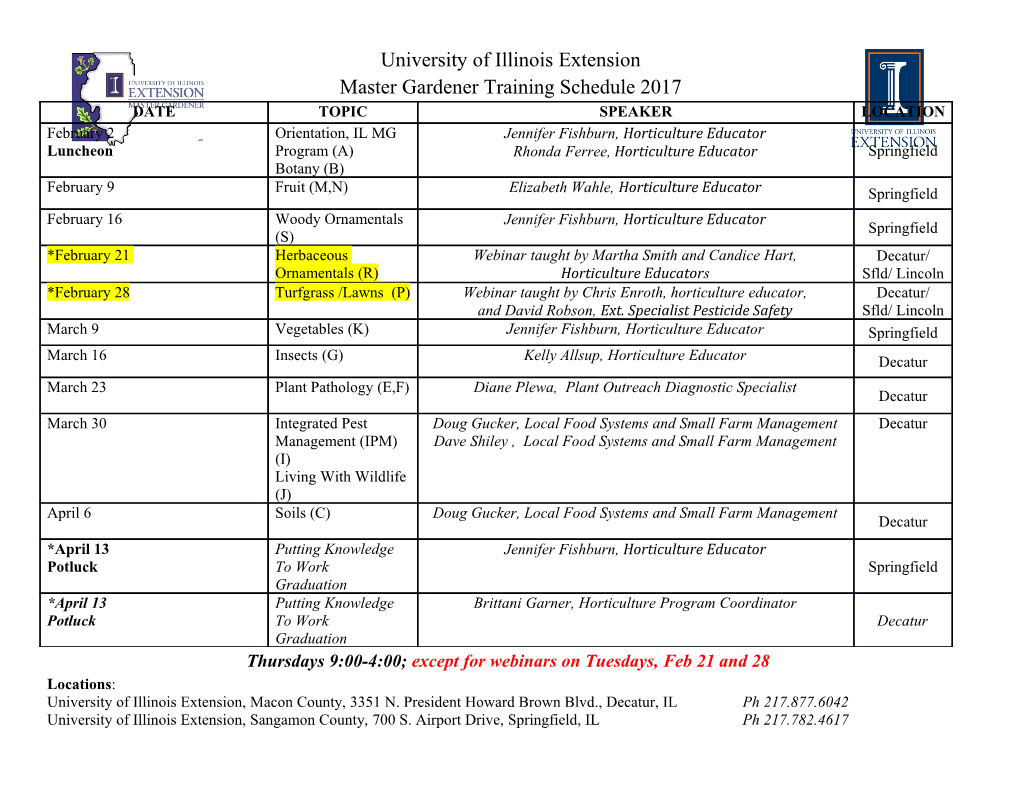
Two-Component Aliphatic Polyurea Coatings for High Productivity Applications Beau Catcher Tunnel in North Carolina protected with polyurea for fast-track renovation (Mirror image shown here). Photos courtesy of Bayer Corporation his article decribes the development of a new class of aliphatic polyurea polymer systems. These systems are based on the reac- tion of polyaspartic ester compounds (a type of secondary aliphat- ic amine with aliphatic polyisocyanate). Polyaspartic ester-based polyurea topcoats are non-yellowing and exhibit good outdoor weathering and long pot life. The moderately fast reactivity, com- Tbined with the relatively low viscosity of the polyaspartic ester compounds, al- By Carl Angeloff, P.E., lows for a broader range of applications in two-component coatings. Edward P. Squiller, Ph.D., Additionally, it is possible to use the polyaspartic ester technology in combi- and Kurt E. Best, nation with polyurethane technology to form polyurethane/polyurea hybrids. This may be advantageous when trying to achieve the highest levels of coating Bayer Corporation chemical resistance and/or owner-specific properties. Characteristics of Polyaspartic Esters and Their Chemistry The development of polyaspartic esters is fairly recent, with the initial work be- ing reported in 1990. Zwiener, et al., first showed the applicability of polyaspar- tic esters as co-reactants for polyisocyanates.1,2 This O O Polyaspartic patented technology3 was initially used in two-compo- RO OR nent polyurethane solvent-borne coating formulations be- Ester Products RO X OR N N cause the polyaspartic esters are excellent reactive dilu- O H H O ents for high-solids polyurethane coatings. They can be X Raw Materials blended with hydroxyl functional polyester and polyacry- Diamine Maleate Designation late co-reactants, thus allowing for reduction of volatile cycloaliphatic DEM A organic compounds (VOC) in relatively high solvent-con- CH2 taining coating systems.4,5 H3C CH3 More recent developments have concentrated on PACM DEM B achieving low or near-zero VOC-containing polyurea coat- CH2 ings where the polyaspartic ester is the main component CH3 2-methylpentane DEM C of the co-reactant for reaction with a polyisocyanate. Be- diamine cause of the moderately fast curing feature, these coatings can offer productivity improvements, along with high- HDA DEM D build, low-temperature curing, and abrasion and corro- Fig. 1: Structures of polyaspartic esters sion resistance.6 42 JPCL August 2002 Reactivity Table 1: Gel Time Reactivity Data for Aliphatic A polyurea can be defined as a reaction Polyurea Clears Based on HDI Trimer product of an aliphatic or aromatic iso- cyanate component, which is composed Polyaspartic Gel Time Gel Time Ester @ 72 F (22 C) @ 32 F (0 C) of amine-terminated polymer resins A 40 min. Did not test and/or amine chain extenders. B 20 min. 23 min. Polyaspartic esters have a unique re- activity with polyisocyanates because of C 1–2 min. 2 min. their unique chemical structure. It is D 1–2 min. Did not test possible to provide a whole family of products based on structural variations cyanate based on HDI (hexamethylene diisocyanate). that result in different reactivity with a It is interesting to note the catalytic effect of water on polyisocyanate (Fig. 1). the gel times of polyaspartic ester/aliphatic polyisocyanate The unique structural feature of the mixtures (Table 3). It is a dramatic effect that can be used polyaspartic ester is a sterically crowded to further tailor the pot life/dry time of a given system. environment around the nitrogen. Addi- This also has the potential to provide the unusual combi- tionally, the ester portion of the structure nation of rather long pot life and fast dry time: the dry provides inductive effects. These features time of a coating system can be decreased dramatically be- both act to slow down the reaction of the cause of humidity in the atmosphere. amino group of the polyaspartic ester compound and the isocyanate group of a polyisocyanate. Practically speaking, Polymer Film Properties slower reaction speed between the isocyanate and an Coating films derived from polyaspartic esters and a com- aliphatic diamine results in longer gel times, and thus, a mon aliphatic polyisocyanate crosslinker, the isocyanurate longer application window. trimer of HDI, are hard, color-stable, and weather- and The reaction speed of abrasion-resistant. Addi- the polyaspartic ester Table 2: Gel Time Reactivity Data for Aromatic tionally, they can be for- compound and the Polyurea Clears mulated to provide good polyisocyanate can be corrosion protection prop- altered by changing the Polyaspartic Gel Time Gel Time erties on steel. Ester Aromatic Polyisocyanate* @ 72 F (22 C) @32 F (0 C) structure of the polyas- Some film properties of B MDI Prepolymer 16% NCO 1 min. partic ester. For exam- 4 min. clear coatings are illustrat- MDI Prepolymer 8% NCO ple, as we decrease the B 5 min. Did not test ed in Table 4. In general, steric crowding in the C MDI Prepolymer 8% NCO <0.5 min. ca. 0.5 min. the data show that these structure of the polyas- B TDI Prepolymer 3% NCO 40–60 min. >90 min. coatings are of moderate partic ester (going C TDI Prepolymer 3% NCO 5 min. 9 min. tensile strength and, as ex- down the column in * The MDI prepolymers are high in 2,4-isomer content and based on polypropylene oxide-based pected, of very low elonga- Fig. 1), the reaction polyols. Solvent-free, linear isocyanate prepolymer based on toluene diisocyanate (TDI); monomeric tions. Once again, the TDI content is less than 0.5%. speed with a given iso- aliphatic polyisocyanate cyanate increases. Thus, the polyaspartic ester compound used in these gel studies is an HDI-based adduct with a designated A is slower reacting than compound B, etc. 1,000 cps (@ 25 C) viscosity product with an NCO con- Some specific data illustrating the gel times of different tent of 20.5%. Other commercially available HDI-based polyaspartic ester products and a polyisocyanate are shown in Table 1. Additionally, it is possible to blend Table 3: The Catalytic Effect of Water on polyaspartic ester products to obtain mixtures with inter- Reactivity* mediate gel times. For comparative purposes, we also conducted these gel Polyaspartic Gel Time tests with some aromatic polyisocyanates, both MDI Ester Water Content (%) @ 72 F (22 C) (diphenylmethane diisocyanate)- and TDI (toluene diiso- B 0.08 65 min. cyanate)-based prepolymers/adducts. These data are B 0.12 31 min. shown in Table 2. The time to gel is, as expected, much B 0.17 21 min. shorter for the mixtures of aromatic MDI polyisocyanates * Polyurea clears based on an HDI-based polyisocyanate adduct: NCO 21.5%, and polyaspartic esters compared to the aliphatic polyiso- viscosity ca. 3000 cps @25 C (77F) JPCL August 2002 43 products with higher functionalities and viscosities 160 may vary the tensile/elongation data somewhat. 140 The aliphatic polyureas based on polyaspartic es- ters yield hard, tough coatings that are clear and for 120 the most part bubble-free, making them suitable for Hard Dry thin-film coating applications, more so than elas- 100 tomeric membranes. This is because the hard 80 block/soft block nature of the aliphatic polyaspartic ester-based polyureas is expected to be very different Minutes 60 than typical aromatic polyureas, which are based on Set-to-Touch 40 MDI prepolymers and polyether backbones. 20 Table 4: Property Data for Aliphatic Polyurea 0 Clear Films Based on HDI Trimer 1.0 3.0 5.0 7.0 9.0 11.0 13.0 Polyaspartic Grains Water/Cubic Ft Ester Tensile (psi) Elongation A 6,875 4% Fig. 2: Effect of ambient moisture on dry times of fast-curing aliphatic B 6,650 4% polyurea topcoat C 2,290 23% cal reactions needed to form a polymeric film. If solvents D 1,800 84% are present in the coating, increasing temperature also works to speed up solvent flash-off, thus resulting in faster drying of a coating. Curing Characteristics of Polyurea Coatings Humidity, on the other hand, normally has minor ef- Based on Polyaspartic Esters fects on the curing characteristics of solvent-borne and The curing characteristics of polyaspartic ester-based solvent-free coatings. The curing characteristics of polyurea coatings are somewhat different than traditional aliphatic polyurea coatings based on polyaspartic esters, polyurethane coatings. They have a curing profile that however, exhibit a rather dramatic dependency on hu- shows a dependency on both temperature and humidity. midity, which in a catalytic manner accelerates the cur- Generally, higher temperatures accelerate the curing ing/drying process (Fig. 2). This provides the opportunity speed of coatings by increasing the kinetics of the chemi- to develop some unique fast cure coatings with relatively long pot life, thus fulfilling special curing performances Table 5: Curing Characteristics of Fast-Curing and productivity requirements. Polyurea Topcoat (Acrylic) The effect of temperature and humidity on the dry times of the polyaspartic ester-based polyurea coating are pre- Relative Temp. sented in Table 5. A traditional polyurethane topcoat, e.g., Humidity F(C) Dry Time (Minutes) acrylic polyurethane, is also presented (Table 5A) for com- 40% RH 45(7) Set to touch: 225; tack free: 465; hard dry: 1020 parison purposes; as expected, it does not show much of a 90% RH 45(7) Set to touch: 45; tack free: 105; hard dry: 180 dry time dependency related to humidity in this study. 65% RH 45(7) Set to touch: 45; tack free: 60; hard dry: 115 40% RH 95(35) Set to touch: 30; tack free: 60; hard dry: 90 Fast-Curing, Corrosion Protection Coating System 90% RH 95(35) Set to touch: 10; tack free: 15; hard dry: 20 Coating films derived from polyaspartic esters and a com- mon aliphatic polyisocyanate crosslinker, the isocyanate trimer of HDI, are hard, color-stable, and weather- and Table 5A: Curing Characteristics of a Traditional abrasion-resistant—all good characteristics for use as a top- Polyurethane Topcoat (Acrylic) coat in a corrosion-resistant coating system on steel.
Details
-
File Typepdf
-
Upload Time-
-
Content LanguagesEnglish
-
Upload UserAnonymous/Not logged-in
-
File Pages6 Page
-
File Size-