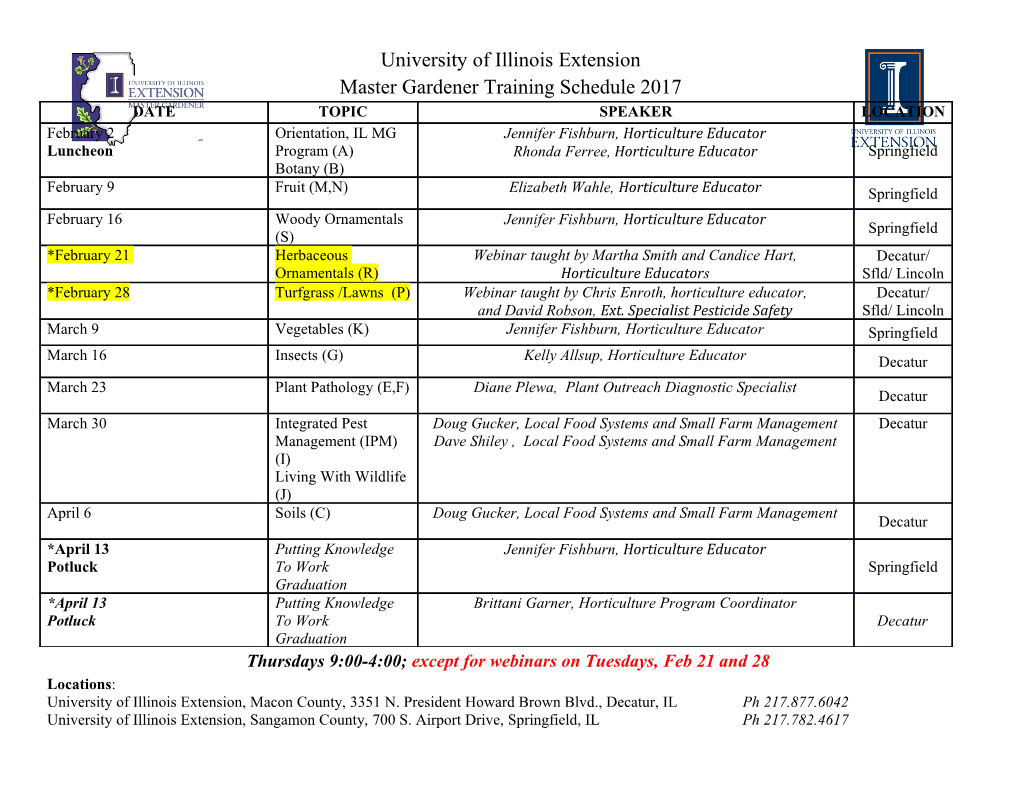
Advances in Intelligent Systems Research, volume 165 International Conference on Modeling, Simulation, Optimization and Numerical Techniques (SMONT 2019) Design and Error Analysis of The Linkage Type Steering Mechanism for Multiple Wheel Heavy Vehicle Chunguo Zhou*, Tao Hua, Huiwu Wang and Xiuyu Wang School of Mechanical and Precision Instrumental Engineering, Xi’an University of Technology, Xi'an, China, Zip: 710048. *Corresponding author Abstract—In this paper, the steering system dimension of II. THE DESIGN OF CENTER-ARM-LINKAGE-TYPE STEERING multiple wheel heavy vehicle which is composed of center-arm MECHANISM linkage type steering mechanism has been designed. The steering mechanism of the vehicle is composed of five axles of Watt-II A. Steering Principle and Composition of Multi-wheel center-arm six-bar mechanism. The vehicle is designed to meet Steering Mechanism the steering requirements. Based on the Ackerman principle of vehicle steering, the mathematical model of steering mechanism As heavy-duty vehicles with multiple wheel and large load, is established, and the precise steering angle is determined. Then want to make the move when the steering wheel to keep the corresponding calculation program has been written by using rolling contact with the ground without sliding, wheel MATLAB software, and the Broyden’s iterative algorithm has deflection must satisfy the Ackerman Principle[3,4] (as Figure been used. The each bar dimensions of the center-arm six-bar I). In other words, The front wheel alignment angle of mechanism has been obtained through cyclic approximation. Finally, the kinematics simulation and error analysis of the steering mechanism are carried out, and the results show that the steering mechanism can meet the steering requirements of the vehicle. Keywords—heavy vehicle; six bar mechanism; dimension design; Ackerman principle I. INTRODUCTION With the development of our economy, special vehicles and engineering vehicles gradually to the development direction of large-scale and heavy-duty, most of these vehicles FIGURE I. THE CORNER RELATION OF INSIDE AND OUTSIDE CAR have more than two steering axles. The more the number of WHEE axles, the more difficult for vehicle steering and getting through in complex curve road, its steering performance have directly effect on vehicle agility, manipulate stability and use economy, so it has very real significance to research multi-shaft vehicles. Optimal steering process requires all wheels to be in a pure rolling state without sliding, or only little slippage; or else large slippage can aggravate wheel’s wear and tear. Reasonable steering mechanism can reduce steering resistance and achieve the purpose of light steering. This article aim at the research on the multi-axle Watt-II center-arm six-bar steering mechanism for heavy vehicle with multiple wheel[1,2], which aims to promote a kinematic point of view to improve the dimension of the center-arm-linkage-type six bar mechanism in order to improve the steering performance of the heavy vehicle with 1- toggle arm 2- center-arm 3- linkage 4- tension rod K- body width multiple wheel. FIGURE II. THE FIVE SHAFTS OF WATT-II CENTER-ARM SIX BAR MECHANISM Copyright © 2019, the Authors. Published by Atlantis Press. This is an open access article under the CC BY-NC license (http://creativecommons.org/licenses/by-nc/4.0/). 219 Advances in Intelligent Systems Research, volume 165 automobile that is equal to zero, walking system is rigid, car aabb j 1 j 1 driving course under the premise of no lateral force, during the D 11j D 11 13j whole turning process all the wheels must be make circular 11 motion around the same instantaneous center on the ground, ccdd the steering angle of the wheel should satisfy the following j D 1 j 1 13j D 15j formula: 11 11 cot cot K L (1) cos(ggjj ) sin( ) 0 Dgg sin( ) cos( ) 0 In this paper, a steering device composed of a five-axle 11jjj Watt-II center-arm six-bar mechanism is taken as an object of 001 study(as Figure II). The six-bar mechanism used in the steering device is Watt-II, the five six-bar mechanisms cos( j ) sin( j )c0 x [1 cos( j )] c0 y sin( j ) connected by five rod, the first rod is connected to steering D sin( ) cos( )c [1 cos( )] c sin( ) power to realize multi-wheel steering of heavy-duty 1j 3 j j0 y j0 x j vehicles[5,6]. When the vehicle is steering, tension rod 4 0 0 1 drived by steering rocker, through the linkage 3 drive toggle arm to rotate, so that multi-wheel vehicle turn around the same cos(hhjj ) sin( ) 1 cos( h j ) center to meet the Ackerman principle. Dhhh sin( ) cos( ) sin( ) 15jjjj B. Mathematical Model of Center-arm Six-bar Steering 00 1 Mechanism Establishment of two dimensional coordinate system for To solve the value of b1x, b1y, c0y, put the above equations the center-arm six-bar mechanism(as Figure III). Take a0 as into type(2), obtained: the origin, assume that the body width is unit length "1"[7], then the coordinate points of the six bar mechanism are: a0(0, 0), a (0, a ), b (b , b ),c (0.5, c ), c (1-b , b ), d (1, a ), E 111j cos(jj )FG sin( j ) j 1 1y 1 1x 1y 0 0y 1 1x 1y 1 1y b0(1, 0), if we can know a1y, b1x, b1y, c0y, then E 222j cos(jjjj )GG sin( ) a0,a1,b1,c1,d1,b0,c0 have been fixed, so the dimension of the Watt-II-center-arm-linkage-type six-bar mechanism can be fixed. As a1y is fixed-length which has been determined in GF12j jjj G 21 F advance, so just solve the value about b1x, b1y, c0y. cos( j ) E 12j FEFjjj 21 (3) E GEG sin( ) 12j jjj 21 j E 12j FEFjjj 21 2 2 in type(3), according to , obtained: cos (j ) sin ( j ) 1 22 2 (4) ()()()0EG1j 2 j EG 21 jj GF 12 jj GF 21 jj EF 12 jj E 2 j F 1 j FIGURE III. THE CENTER-ARM SIX BAR MECHANISM TURN RIGHT in this type: Suppose that when the vehicle turns, the rotation angle of E 2[ M ( c b ) N ( c b )] a0a1,b0d1 and the center-arm are gj, hj, θj. when vehicle turn a 1 j 1j 0 x 1 x 1j 0 y 1 y corner, make a1, b1, c1, d1 turn to aj, bj, cj, dj. The design equation of the mechanism is equal length constraint equation F1 j 2[ N1j ( c 0 x b 1 x ) M1j ( c 0 y b 1 y )] of a1b1,c1d1[8]: E2 j 2[ M2j ( c 0 x c 1 x ) N2j ( c 0 y c 1 y )] ()()()()a b2 a b2 a b2 a b 2 jx jx jy jy 1x 1 x 1y 1 y (2) F2201201jjxxjyy 2[Nc ( c ) Mc ( c )] 2 2 2 2 ()()()()cjx d jx cjx d jy c1x d 1 x c1y d 1 y 2 2 2 2 2 2 Gab1j()()()() 1 y 1 y ab1x 1 x cb0x 1 x bc1y 0 y NM1 j 1 j j =2, 3, 4, 5…… 222222 Gcd21111010122j ()()()()yy cdcc xx yy ccNM xx j j in this type: which: 220 Advances in Intelligent Systems Research, volume 165 M1j a 1 x cos( gj ) a1 y sin( gj ) c0 x harc32 cot[cot( g ) ( kl )] harc cot[cot( g ) ( kl )] N1j a 1 x sin( gj ) a1 y cos( gj ) c0 y 43 22 2 (5) M2 j d1x cos( hj ) d1 y sin( h j ) 1 cos(hj ) c0 x FEGEGGFGFEFEFjjjjjjjjjjjjj()()()1 2 21 12 21 12 2 1 By type(4) obtained: N2j d 1 xsin( h j ) d1 y cos( hj ) sin( hj ) c0 y Fj=0, j=2, 3, 4…… (6) Type(4) is non-linear equations set without unknown trigonometric functions, which can be solved with selecting Type(6) is non-linear equations set without unknown the appropriate initial value. trigonometric functions, convert the type (6) to the following The unknown number θj which is the angular displacement system of linear equations: of the member c0b1c1 is included in the displacement matrix [D ],its number is (j-1). In Figure III coordinate system, a b Fc20yxyy Fb 21 Fb 21 c 0 F2 1j3 0 0 Fc F b Fb b F as unit length, then b0=(1,0), a1=(0,a1y), b1=(b1x,b1y), d1=(1,d1y), 30yxyx 3 1 31 1 3 Fc40yxyy Fb 41 Fb 41 b 1 F4 c0=(0.5,c0y).Then in type (2),the unknown number include (7) b1x,b1y ,c1x,c1y,d1y,c0y and θj, the number of unknown number is U=6+(j-1)=j+5, the number of design equation is V=2(j-1). Let Express the above as: Aδ=-F, A is Jacobian matrix. The U=V, so j=7. That is to say seven exact points of given Broyden iterative method[12,13] is used to obtain the exact function can be realized by the Watt-II center-arm six-bar value of the above calculation, the calculation of the above mechanism designed in this paper[7]. process can be implement through the preparation of the corresponding MATLAB programs, the flow chart of III. BROYDEN ITERATIVE METHOD BASED ON MATLAB MATLAB programming is as follows(as Figure IV). The value of (gj,hj) in equations set(4) is determine by Chebyshev theorem[9]. As the heavy-duty vehicle at low By programming, some of the calculated results are speeds are usually for large angle, assuming the wheel angle obtained(as Table I).
Details
-
File Typepdf
-
Upload Time-
-
Content LanguagesEnglish
-
Upload UserAnonymous/Not logged-in
-
File Pages7 Page
-
File Size-