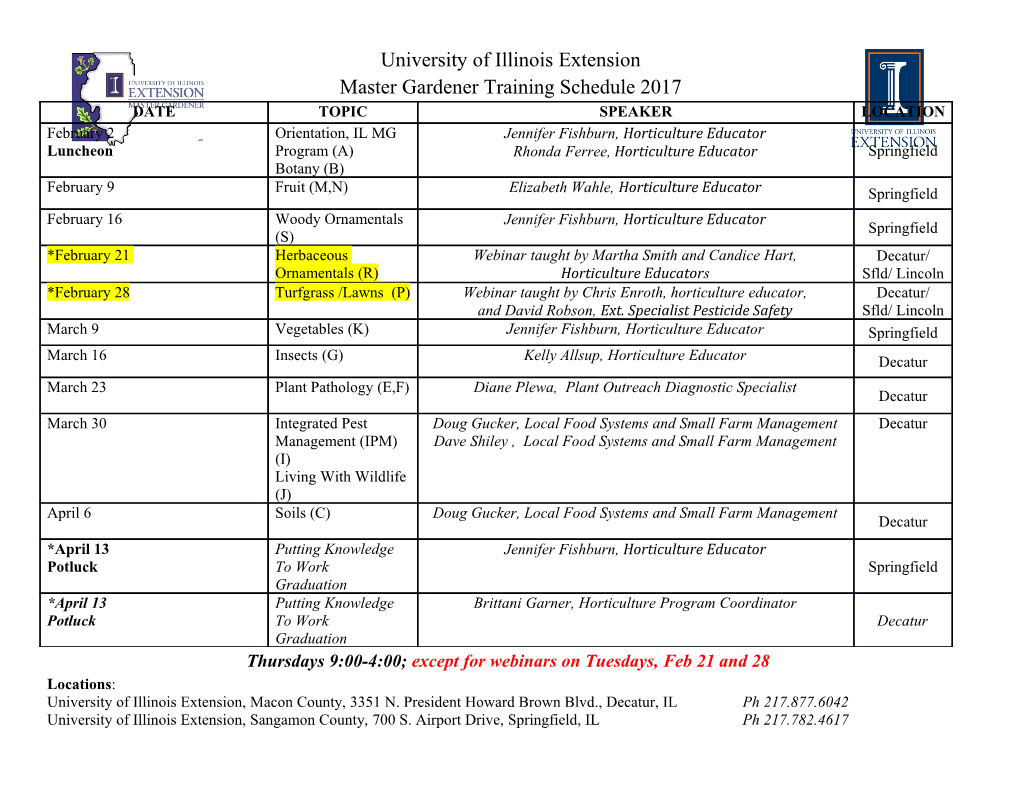
Effect of Experimental Parameters on Forming Prince Rupert’s Drops for Maximum Strength and Toughness Introduction Engineering Goal Discussion Glass is a transparent, amorphous solid with a high The goal of this project was to determine which parameter during formation has the greatest effect on the The increase in strength is hypothesized to be a glass transition temperature, refractive index, and maximum strength and toughness of the drop, and manipulate it so that the drop exhibits such characteristics to byproduct of the plastic coating formed by the superheated strength. When heat treated, glass can form internal the greatest extent. PVA around the drop, whilst the decrease is predicted to be stresses that increase its strength by a large magnitude. A subsequent goal was to determine which specific concentrations, by volume, of PVA contaminant will yield a result of surpassing a threshold of PVA:Water ratio Heat treated glass drops were first developed 400 years the drops with the greatest strength and toughness. affecting the formation of pressures in the drop, and the ago and were popularized by Prince Rupert of Batavia, possibility of PVA contamination within the drop. hence the name. The drops are made by quenching By carefully examining the footage found in Figure 6, it molten glass in water, resulting in a tadpole shaped bead Fabrication and Testing was concluded that when pressure is applied on the head, with a long tail. the point of failure occurred in the center of the bulb and The head of the drop can withstand extreme pressure; propagated towards the tail as illustrated in the graphic in Sample Preparation Testing Figure 8 and shown in a picture of the drop under cross- however, the drop explodes into tiny fragments when the polarization in Figure 9. Attempts were made to calculate tail is snipped. The reason for this peculiar behavior is Prince Rupert's Drops are fabricated by melting glass stirring Mechanical testing of drops made in varying PVA the forces within each drop but remain inconclusive due to the stresses that form inside the drop. The outer layer of rods over a hot flame and allowing the molten glass to drop into concentrations required a compression tester beyond the load the obstruction from glass dust. In contrast, it was observed the drop is under extreme compression while the inner a beaker of distilled water. The instantaneous and enormous cell capacity of the one in our laboratory. Further testing was that a drop snipped at the tail will fracture at the point of layer is under extreme tension. The compressive pressure change in temperature forms pressures inside the drop which completed at a nearby research institution using a Tinius Olsen compression tester and NAC HX-3 slow motion camera, penetration initially and then propagate towards the center gives the drop its strength while the tension on the inside results in a bead that has enhanced strength and toughness. recording at a rate of 25,000 frames per second. of the bulb letting us conclude that the point of failure is the is what causes the drop to explode when the outer layer is The first phase of sample preparation was control drops that had no parameter changes. The second phase was focused on origin of the explosion. penetrated. investigating various contaminants added to the distilled water. During compression testing, it was noticed that Initial mechanical testing showed that the addition of PVA to Figure 2: Tinius Olsen specimens with air bubbles inside fractured at an earlier The goal of this research is to manipulate the Compression tester with parameters of formation of a Prince Rupert’s Drop to the distilled water during drop formation exhibited the most a PVA contaminated stress than drops without air bubbles. To better understand create a specimen with superior strength and toughness. interesting results. To that end, the final phase of the study Prince Rupert Drop the fracture behavior, Finite Element Analysis (FEA) of the investigated the effects of adding PVA concentrations ranging It is predicted that stronger formations of glass can be drops was performed to study the effect of an air bubble from 2% to 70% by volume to the formation solution. applied in the field of tempered glass manufacturing. inside the Prince Rupert’s Drop. Figure 10 shows the Von- Applications include vehicle windows, mobile devices Figure 1: The picture Mises stress of the drop during compression. The drop was screens and many other uses where the glass must be on the left is a control modeled as a sphere for ease of computation. The FEA Prince Rupert’s Drop Figure 3: Materials analysis supported our testing data and confirmed that very resistant to changes in structure whilst maintaining Testing Rig with Tinius with no contaminants drops without air bubbles were stronger than the drops a high compressive strength under high pressure. It has in solution while the Olsen compression tester and NAC HX-3 with air bubbles. been observed that the use of PVA (Polyvinyl Acetate) as one the right is a Prince Rupert’s Drop slow motion camera a contaminant in the formation solution allows for a that was formed in a second protective barrier that will increase the surface 5% PVA solution. Cross-Polarization area and reduces the overall pressure on the drop when compressed. In order to visualize the stresses formed in the glass Results during formation, drops were placed in between two cross- Preliminary Testing polarizing films. The pictures taken with these films were then Data Analysis compared to a key (Figure 9.), and it was determined that the Prince Rupert’s Drops are intriguing due to their extreme blue areas represented glass in tension and the red areas represented glass in compression. These pictures illustrated toughness. It was suspected that changing the environment in Typical stress strain curves that the glass on the inside of the drop was under tension, which the drops are formed can lead to variations in their are shown in graph in Figure while the outer glass was under compression. toughness. Multiple drops were produced, using different on the left. Note that the contaminants in the solution such as salt, sugar, syrup, oil, specimen dropped into a 50% ethanol, and PVA. Factors such as the temperature of the PVA solution has a much solution, the material of the glass, and the flame used were kept larger stress and strain (and constant. Each of these drops was tested using a PASCO toughness) than the specimen materials tester. Although most did surpass the load cell, drops that only had 30% PVA. Also made in PVA solutions and Ethanol solutions exhibited greater note that both of these strength. The Ethanol contaminated drops were completely samples were superior in elongated and bulged, whilst the PVA drops had a layer of performance to the glass Figure 8. *http://junq.info/?cat=6 Figure 9 plastic which was predicted to increase their strength. The control. The average values of layer of plastic produced was slightly decomposed . It clouded the maximum compressive the overall clarity of the glass. At this point it was decided to strength and toughness for Finite Element Analysis delve further into the PVA contaminated drops by contacting a the different specimens tested research facility. are listed in the Table . Finite Element Analysis of the As the %PVA in solution drops tested the effect of an air increased towards 50% the bubble inside a Prince Rupert’s overall compressive strength Drop. This was done because it and toughness of a drop was noticed that drops with air increased as seen in the bubbles inside of them were graphs of Figures 4 and 5. weaker than drops without air Any further addition of the PVA contaminant to the bubbles. Drops with larger air Figure 10. Figure 4: Graph of the maximum compressive strength Figure 5: Graph of the maximum toughness versus solution resulted in a sharp bubbles were relatively weaker. versus %PVA %PVA decrease in strength. The finite element analysis results agreed with our observation that The strongest drop tested had an Ultimate Compressive Strength of 300,00 PSI (Pounds-Per-Square-Inch) and a drops without air bubbles were toughness of 6,000,000 PSI. This makes the compressive strength of our strongest drop to be a third as strong as materials such as diamond and Tungsten Carbide, the strongest man-made material. It should also be noted that the average Ultimate stronger and the drops with bigger Figure 11: Dented aluminum plate (left) and PASCO materials tester (right). Compressive Strength of 50% PVA solution drops was 200,000 PSI. The Ultimate Compressive Strength of Gorilla Glass is air bubbles were relatively weaker. greater than or equal to 850 Mpa, which is equivalent to 123,000 PSI and a fracture toughness of 0.69 Mpa, which is equivalent However, the actual values of References to 100 PSI. This means that our strongest drops had greater strength than Corning Ware’s chemically hardened Gorilla Glass 5. compression in the finite element analysis did not correlate to our ● Brodsley, Laurel, et al. “Prince Rupert's Drops.” Notes and Records of real world values. This is because the Royal Society of London, vol. 41, no. 1, 1986, pp. 1–26. JSTOR, Video Analysis our program does not model the JSTOR, www.jstor.org/stable/531493. fracture behavior of ceramics and Figure 11. ● W. Johnson, S. Chandrasekar, Rupert's glass drops: Residual-stress glasses under pressure. measurements and calculations and hypotheses for explaining disintegrating fracture, In Journal of Materials Processing Technology, Volume 31, Issue 3, 1992, Pages 413-440, ISSN 0924-0136, https://doi.org/10.1016/0924-0136(92)90292-Z.
Details
-
File Typepdf
-
Upload Time-
-
Content LanguagesEnglish
-
Upload UserAnonymous/Not logged-in
-
File Pages1 Page
-
File Size-