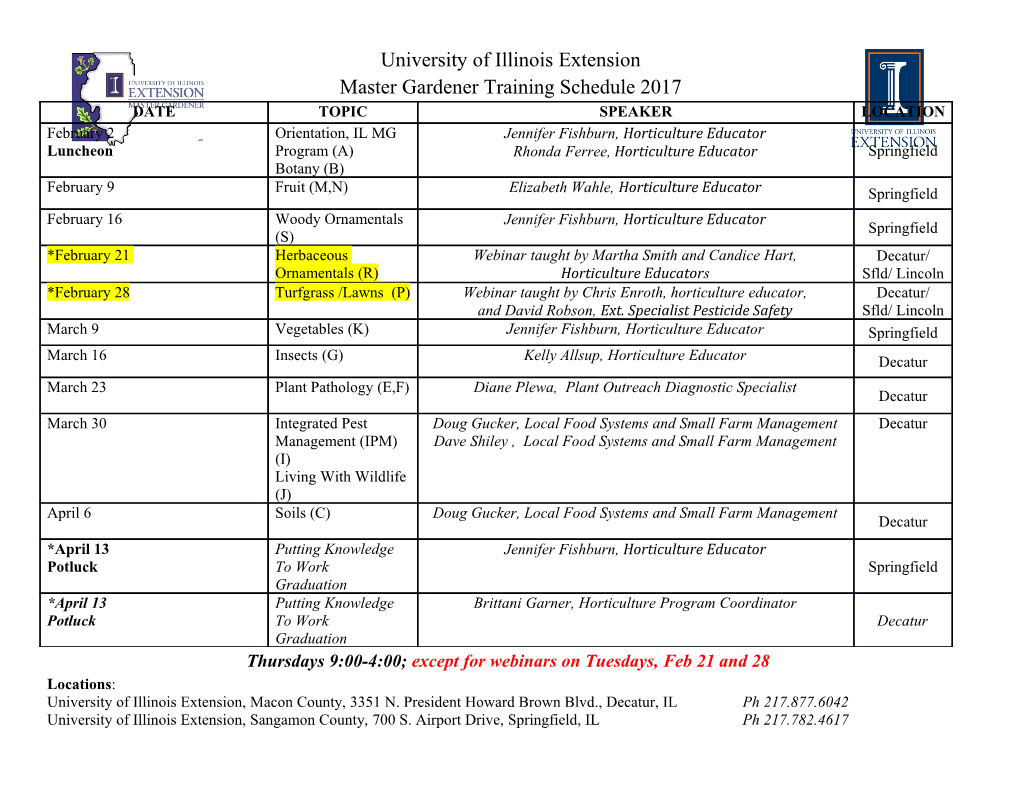
The drilling rig components. A mud tank is an open-top container, typically made of steel, to store drilling fluid on a drilling rig. They are also called mud pits, because they used to be nothing more than pits dug out of the earth. The tanks are generally open-top and have walkways on top to allow a worker to traverse and inspect the level of fluid in the tanks. The walkways also allow access to other equipment mounted on top. Recently, offshore drilling rigs have closed-in tanks for safety. The mud tank plays a critical role in mechanically removing destructive solids and sediment from costly land and offshore drilling systems.[1] A drilling rig normally has two tanks. A tank is sectioned off into compartments. A compartment may include a settling tank, sometimes called a sand trap, to allow sand and other solids in the drilling fluid to precipitate before it flows into the next compartment. Other compartments may have agitators, which are large fan blades stirring the fluid to prevent its contents from precipitating. The pipe work linking the mud tanks/pits with the mud pumps is called the suction line. This may be gravity fed or charged by centrifugal pumps to provide additional volumetric efficiency to the mud pumps. Shale shakers are devices that remove drill cuttings from the drilling fluid that is used for boring holes into the earth. Controlling the solids in drilling fluid is an important component of the cost of drilling, so research into improved shaker design is ongoing. Contents [hide] 1 Shale shaker design 2 Shaker Screen Panels 3 Causes of screen failure 4 Screen Panel Designation [edit] Shale shaker design Shale shakers typically consist of large, flat sheets of wire mesh screens or sieves of various mesh sizes that shake or vibrate the drill cuttings, commonly shale, across and off of the screens as the drilling fluid (mud) flows through them and back into the drilling fluid system. This separates the solid drill cuttings from the fluid so that it can be recirculated back down the wellbore. In oilfield industry, linear motion shale shakers are widely used. [edit] Shaker Screen Panels Shaker Screen Panel Screen panels play a major role by removing particles larger than the mesh size. Screen selection is critical since shaking is the primary stage in the removal of solids. Improper screen selection can lead to de-blinding[clarification needed], loss of drilling fluids, premature pump part failures, overloading of other solids removal equipment within the mud systems, decreased service life, reduced flow rate capacity, and serious problems in the wellbore. [edit] Causes of screen failure The causes of premature screen failure are:[citation needed] Personnel improperly trained on handling, storage, maintenance and installation of deck rubbers and screens Careless storage of screen panels prior to use Screens damaged before use from improper handling during installation Shaker screen not match very well to shale shaker Deck rubbers improperly installed Deck rubbers dirty, worn or missing Dried cuttings or drilling fluid left on screen during shutdown of shaker Personnel walking on screens or using the shaker as a work table Tools being dropped on screens Extremely high mud weights or heavy solids loading Defective or improperly manufactured screens Use of high pressure wash guns to clean plugged screens A mud tank is an open-top container, typically made of steel, to store drilling fluid on a drilling rig. They are also called mud pits, because they used to be nothing more than pits dug out of the earth. The tanks are generally open-top and have walkways on top to allow a worker to traverse and inspect the level of fluid in the tanks. The walkways also allow access to other equipment mounted on top. Recently, offshore drilling rigs have closed-in tanks for safety. The mud tank plays a critical role in mechanically removing destructive solids and sediment from costly land and offshore drilling systems.[1] A drilling rig normally has two tanks. A tank is sectioned off into compartments. A compartment may include a settling tank, sometimes called a sand trap, to allow sand and other solids in the drilling fluid to precipitate before it flows into the next compartment. Other compartments may have agitators, which are large fan blades stirring the fluid to prevent its contents from precipitating. The pipe work linking the mud tanks/pits with the mud pumps is called the suction line. This may be gravity fed or charged by centrifugal pumps to provide additional volumetric efficiency to the mud pumps. [edit] Mud tanks for solids control Mud tanks are the base of solids control equipment. Mud tanks for solids control systems are divided into Square tanks and Cone-shaped tanks according to the shape of the tank bottom. The body of the tank is made by welding the steel plate and section, using the smooth cone-shape structure or the corrugated structure. The mud tank surface and passages are made of slip resistant steel plate and expanded steel plate.The mud tanks are made of the side steel pipe, all of the structure can be folded without barrier and pegged reliably. The surface of the tank is equipped with a water pipeline for cleaning the surface and equipment on the tank, it uses soaked zinc processing for the expanded steel plate. The ladder is made of channel steel to take responsibility the body, the foot board is made of expanded steel plate. The two-sided guard rail are installed the safe suspension hook. The mud tank is designed the standard shanty to prevent the sand and the rain. The pipeline is installed in the tank to preserve the warm air heat. Mud tank quantity depends on mud process capacity requirements. Especially for mud storage, suitable for mud pump, drilling rig, etc. A mud pump is a reciprocating piston/plunger device designed to circulate drilling fluid under high pressure (up to 7,500 psi (52,000 kPa) ) down the drill string and back up the annulus. Mud pumps come in a variety of sizes and configurations but for the typical petroleum drilling rig, the triplex (three piston/plunger) mud pump is the pump of choice. Duplex mud pumps (two piston/plungers) have generally been replaced by the triplex pump, but are still common in developing countries. Two later developments are the hex pump with six vertical pistons/plungers, and various quintuplex's with five horizontal piston/plungers. The advantages that these new pumps have over convention triplex pumps is a lower mud noise which assists with better MWD and LWD retrieval. The "normal" mud pump consist of two main sub-assemblies, the fluid end and the power end. The fluid end produces the pumping process with valves, pistons, and liners. Because these components are high-wear items, modern pumps are designed to allow quick replacement of these parts. To reduce severe vibration caused by the pumping process, these pumps incorporate both a suction and discharge pulsation dampener. These are connected to the inlet and outlet of the fluid end. The power end converts the rotation of the drive shaft to the reciprocating motion of the pistons. In most cases a crosshead crank gear is used for this. Parts of mud pump: 1.housing itself. 2.liner with packing. 3.cover plus packing. 4.piston and piston rod. 5.suction valve and discharge valve with their seats. 6.stuffing box (only in double-acting pumps). 7.gland (only in double-acting pumps). An electric motor is an electromechanical device that converts electrical energy into mechanical energy. Most electric motors operate through the interaction of magnetic fields and current- carrying conductors to generate force. The reverse process, producing electrical energy from mechanical energy, is done by generators such as an alternator or a dynamo; some electric motors can also be used as generators, for example, a traction motor on a vehicle may perform both tasks. Electric motors and generators are commonly referred to as electric machines. Electric motors are found in applications as diverse as industrial fans, blowers and pumps, machine tools, household appliances, power tools, and disk drives. They may be powered by direct current, e.g., a battery powered portable device or motor vehicle, or by alternating current from a central electrical distribution grid or inverter. The smallest motors may be found in electric wristwatches. Medium-size motors of highly standardized dimensions and characteristics provide convenient mechanical power for industrial uses. The very largest electric motors are used for propulsion of ships, pipeline compressors, and water pumps with ratings in the millions of watts. Electric motors may be classified by the source of electric power, by their internal construction, by their application, or by the type of motion they give. The physical principle behind production of mechanical force by the interactions of an electric current and a magnetic field, Faraday's law of induction, was discovered by Michael Faraday in 1831. Electric motors of increasing efficiency were constructed from 1821 through the end of the 19th century, but commercial exploitation of electric motors on a large scale required efficient electrical generators and electrical distribution networks. The first commercially successful motors were made around 1873. Some devices convert electricity into motion but do not generate usable mechanical power as a primary objective, and so are not generally referred to as electric motors. For example, magnetic solenoids and loudspeakers are usually described as actuators and transducers,[1] respectively, instead of motors. Some electric motors are used to produce torque or force.[2] This article provides insufficient context for those unfamiliar with the subject. Please help improve the article with a good introductory style.
Details
-
File Typepdf
-
Upload Time-
-
Content LanguagesEnglish
-
Upload UserAnonymous/Not logged-in
-
File Pages30 Page
-
File Size-