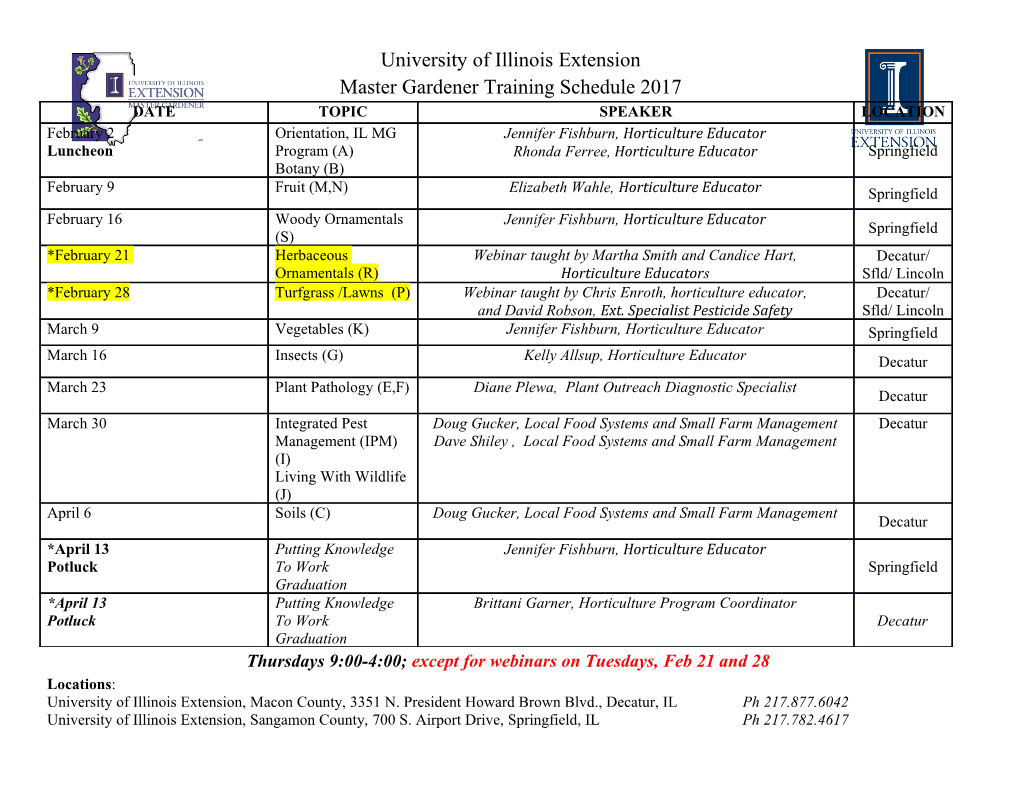
micromachines Article Effects of Anisotropy on Single Crystal Silicon in Polishing Non-Continuous Surface Guilian Wang 1,2, Zhijian Feng 1,2, Yahui Hu 1,2, Jie Liu 1,2 and Qingchun Zheng 1,2,* 1 Tianjin Key Laboratory for Advanced Mechatronic System Design and Intelligent Control, School of Mechanical Engineering, Tianjin University of Technology, Tianjin 300384, China; [email protected] (G.W.); [email protected] (Z.F.); [email protected] (Y.H.); [email protected] (J.L.) 2 National Demonstration Center for Experimental Mechanical and Electrical Engineering Education, Tianjin University of Technology, Tianjin 300384, China * Correspondence: [email protected] Received: 19 June 2020; Accepted: 29 July 2020; Published: 30 July 2020 Abstract: A molecular dynamics model of the diamond abrasive polishing the single crystal silicon is established. Crystal surfaces of the single crystal silicon in the Y-direction are (010), (011), and (111) surfaces, respectively. The effects of crystallographic orientations on polishing the non-continuous single crystal silicon surfaces are discussed from the aspects of surface morphology, displacement, polishing force, and phase transformation. The simulation results show that the Si(010) surface accumulates chips more easily than Si(011) and Si(111) surfaces. Si(010) and Si(011) workpieces are deformed in the entire pore walls on the entry areas of pores, while the Si(111) workpiece is a local large deformation on entry areas of the pores. Comparing the recovery value of the displacement in different workpieces, it can be seen that the elastic deformation of the A side in the Si(011) workpiece is larger than that of the A side in other workpieces. Pores cause the tangential force and normal force to fluctuate. The fluctuation range of the tangential force is small, and the fluctuation range of the normal force is large. Crystallographic orientations mainly affect the position where the tangential force reaches the maximum and minimum values and the magnitude of the decrease in the tangential force near the pores. The position of the normal force reaching the maximum and minimum values near the pores is basically the same, and different crystallographic orientations have no obvious effect on the drop of the normal force, except for a slight fluctuation in the value. The high-pressure phase transformation is the main way to change the crystal structure. The Si(111) surface is the cleavage surface of single crystal silicon, and the total number of main phase transformation atoms on the Si(111) surface is the largest among the three types of workpieces. In addition, the phase transformation in Si(010) and Si(011) workpieces extends to the bottom of pores, and the Si(111) workpiece does not extend to the bottom of pores. Keywords: single crystal silicon; anisotropy; polishing; non-continuous surface 1. Introduction The single crystal silicon has a basically complete lattice structure with different properties in different directions. In order to better understand the mechanical and chemical properties of single crystal silicon, it is necessary to fully understand their properties in each crystallographic orientation. Previous studies have shown that the influence of anisotropy on the processing of materials is mainly reflected in the accumulation of materials, elastoplastic properties, and phase transformation during the processing [1–4], which often play a decisive role in the quality of materials. For porous crystalline materials, the effect of crystallographic orientations on machining is more complicated. Because of Micromachines 2020, 11, 742; doi:10.3390/mi11080742 www.mdpi.com/journal/micromachines Micromachines 2020, 11, 742 2 of 16 the special geometric structure, the bearing capacity of porous materials will be reduced, and it is difficult to obtain an ideal surface using traditional processing methods [5–9]. Therefore, grasping the structural and property differences caused by the anisotropy of the porous crystalline material during the processing is crucial for selecting the process parameters to obtain an ideal processing surface. Different crystallographic orientations bring various structures and peculiar mechanical properties, which widen the application of crystal materials. However, it also causes many problems in processing and manufacturing. In order to obtain crystals with higher precision and better mechanical properties, many scholars have done extensive research on the anisotropy of crystals. Filippov et al. [10] studied the influence of crystallographic orientations and azimuth indenter orientations on indentation hardness and modulus by Vickers indentation on (100), (110), and (111) surfaces of single crystal aluminum. Tang et al. [11] compared the anisotropic behavior of crystals with experimental results and found that the extended anisotropic Drucker yield criterion can accurately simulate the anisotropy of FCC (face-centered cubic), BCC (body-centered cubic), and HCP (hexagonal close-packed) metals. Armstrong et al. [12] conducted stress calculations on the (111) and (100) surfaces of α-iron, and discovered the dislocation reaction mechanism of enhanced strain hardening during the process of the nano-indentation. Kitsuya et al. [13] studied crystallographic orientations on some metals, and the crystal plasticity analysis based on the information obtained from experiments showed that the anisotropy of mechanical properties is greatly affected by the crystallographic orientations. Bürger et al. [14] tested the shear creep behavior of nickel-based single crystal superalloys and found that the shear deformation in the [112] loading direction is much faster than that in the [011] loading direction on the (110) surface. Zhan et al. [15] reported the mechanical deformation of the single crystal Ti2AlC MAX phase using microcolumn compression tests with a series of crystallographic orientations, and found that non-classical crystallographic slip is caused by the strong dependence of crystallographic slip on both the analytical shear stress and the stress perpendicular to the slip plane. Frydrych et al. [16] studied the yield stress, hardened texture, and twin anisotropy of AZ31B extruded bars, and concluded that the twinning activity mainly affects the mechanical response through texture changes. Xie et al. [17] studied the removal mechanism of single crystal copper in the close-to-atomic scale by molecular dynamics, and simulated the influence of anisotropy on cutting force and material distribution of the surface. It was found that the minimum chip thickness can be reduced to a single atomic layer in an atomic scale using rounding tools for mechanical cutting. Frodal et al. [18] studied three aluminum alloys with different grain structures and crystal textures, and found that effects of yield strength and work hardening depend on plastic anisotropy. Pogrebnjak et al. [19,20] studied two kinds of nano-multilayer films CrN/MoN and TiN/SiC through experiments, and found that the preferred crystallographic orientation will change under different voltages. Meanwhile, the effect of temperature on the physicochemical and functional properties of the TiN/SiC multilayer film was explored. The research results are consistent with the first principle MD (molecular dynamics) calculation of the TiN/SiC heterostructure. The above studies on metals and alloys show that the anisotropy of crystals will have a significant impact on the yield strength, work hardening, and shear slip dislocation of metals and alloys. Reasonable selection of crystallographic orientations can effectively optimize the processing of metals and alloys, and improve the processing quality. Unlike metals and alloys, some studies have found that hard and brittle crystal materials are prone to cracks and chipping during the processing, and the crystallographic orientation is closely related to the generation of cracks during the processing of brittle materials. In order to overcome the influences of the anisotropy on the processing of hard and brittle materials, it is imperative to study the anisotropy of hard and brittle materials. Meng et al. [21] focused on the influences of crystallographic anisotropy on 6H-SiC slip deformation and nanomachining performance, and made important contributions to understand the microdeformation and nanomachining processes of 6H-SiC. Cang et al. [22] observed obvious elastic anisotropy in glass and found that the elastic anisotropy shows a strong correlation with molecular orientations. Chen et al. [23] did some research on cutting SiO2 and found that (100) [00-1] crystallographic orientation has a large range of damage extension, Micromachines 2020,, 11,, 742x 33 of of 16 new phase is generated in the (111) [-101] crystallographic orientation. Nagai et al. [24] discussed the (110)formation [1–10] mechanism crystallographic of U-shaped orientation diamond has the smallest grooves damage based range,on the and experimental a new phase results, is generated and insuccessfully the (111) [-101] obtained crystallographic a U-shaped orientation.diamond trench Nagai wi etth al. vertical [24] discussed {111} sidewalls the formation for power mechanism devices. of U-shapedLiu et al. diamond[25] analyzed grooves the based internal on thereasons experimental for the results,anisotropy and successfullyof the frictional obtained force a when U-shaped the diamond slided trench on with the vertical diamond, {111} which sidewalls was mainly for power caused devices. by amorphous Liu et al. [25defects,] analyzed
Details
-
File Typepdf
-
Upload Time-
-
Content LanguagesEnglish
-
Upload UserAnonymous/Not logged-in
-
File Pages16 Page
-
File Size-