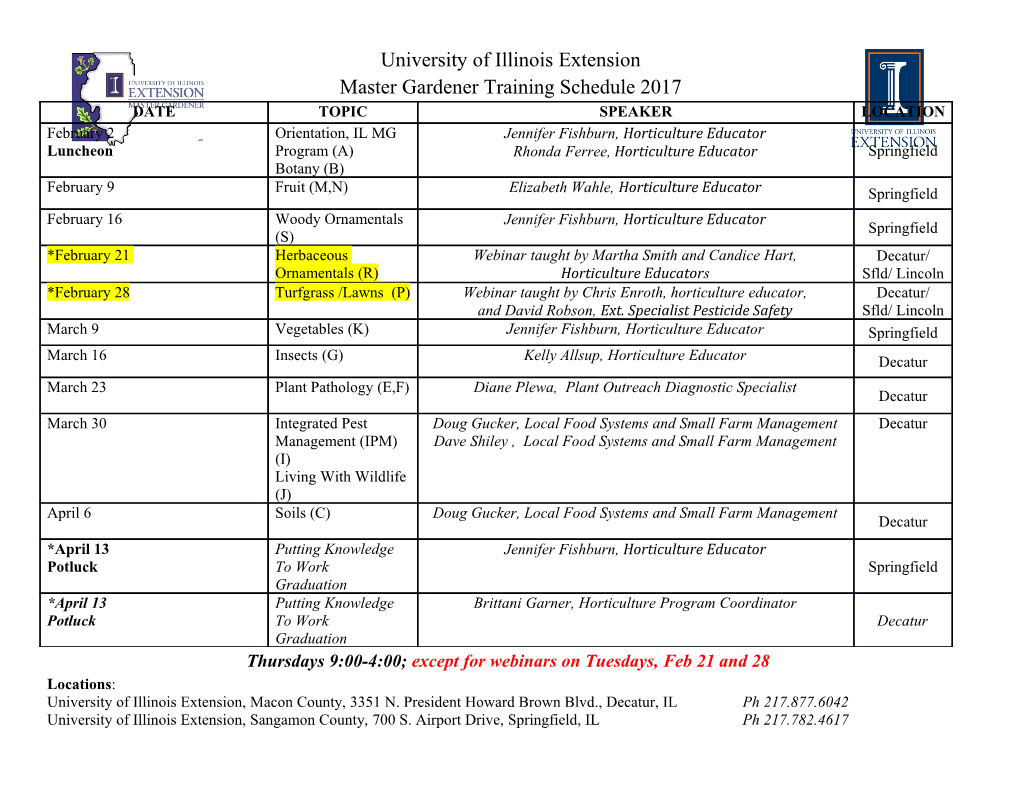
DOT/FAA/AR-00/22 Corrosion and Corrosion Fatigue Office of Aviation Research Washington, D.C. 20591 of Airframe Materials July 2000 Final Report This document is available to the U.S. public through the National Technical Information Service (NTIS), Springfield, Virginia 22161. U.S. Department of Transportation Federal Aviation Administration NOTICE This document is disseminated under the sponsorship of the U.S. Department of Transportation in the interest of information exchange. The United States Government assumes no liability for the contents or use thereof. The United States Government does not endorse products or manufacturers. Trade or manufacturer's names appear herein solely because they are considered essential to the objective of this report. This document does not constitute FAA certification policy. Consult your local FAA aircraft certification office as to its use. This report is available at the Federal Aviation Administration William J. Hughes Technical Center's Full-Text Technical Reports page: actlibrary.tc.faa.gov in Adobe Acrobat portable document format (PDF). Technical Report Documentation Page 1. Report No. 2. Government Accession No. 3. Recipient's Catalog No. DOT/FAA/AR-00/22 4. Title and Subtitle 5. Report Date CORROSION AND CORROSION FATIGUE OF AIRFRAME MATERIALS July 2000 6. Performing Organization Code 7. Author(s) 8. Performing Organization Report No. Dr. Robert P. Wei 9. Performing Organization Name and Address 10. Work Unit No. (TRAIS) Lehigh University Dept. of Mechanical Engineering & Mechanics 19 Memorial Drive West 11. Contract or Grant No. Bethlehem, PA 18015 92-G-0006 12. Sponsoring Agency Name and Address 13. Type of Report and Period Covered U.S. Department of Transportation Final Report 6/15/92 – 9/30/99 Federal Aviation Administration Office of Aviation Research 14. Sponsoring Agency Code Washington, DC 20591 ACE-100 15. Supplementary Notes The FAA William J. Hughes Technical Center COTR was Dr. Thomas Flournoy. 16. Abstract This report summarizes research performed under Grant 92-G-0006 and complementary programs sponsored by the Air Force Office of Scientific Research under Grants F49620-96-1-0245 and F49620-98-1-0198. The objectives of these programs are (1) the development of a basic understanding of the processes of localized corrosion and corrosion fatigue crack nucleation and growth in high strength aluminum alloys used in airframe construction, (2) the formulation of kinetic models for these elemental processes, and (3) the integration of these models into probabilistic models that can provide guidance in formulating methodologies for service-life prediction and airworthiness assessment. The research showed that localized pitting corrosion acts as crack nuclei and causes early crack nucleation and the onset of fatigue crack growth. It can significantly reduce the service lives of structural components. Fundamental understanding of these targeted mechanisms and measurements of their kinetics of evolution are summarized. A simplified, probability model, based on this understanding, was developed and used to demonstrate the feasibility of translating laboratory data into predictions of the evolution and distribution of damage of aircraft in service. Agreement between model predictions and distribution of damage in the lower wing skin of an aircraft that had been in commercial service for 24 and 30 years illustrates the efficacy of this approach. It confirms the importance of incorporating the impact of localized corrosion into the structural reliability and airworthiness assessment methodologies. 17. Key Words 18. Distribution Statement Corrosion, Corrosion fatigue, Pitting, Localized corrosion, This document is available to the public through the National Crack nucleation, Fatigue crack growth, Life prediction, Technical Information Service (NTIS) Springfield, Virginia Probability modeling, Airframe materials, Aluminum alloy, 22161. 2024-T3 alloy 19. Security Classif. (of this report) 20. Security Classif. (of this page) 21. No. of Pages 22. Price Unclassified Unclassified 69 Form DOT F1700.7 (8-72) Reproduction of completed page authorized PREFACE Individuals who have contributed to the Phase II effort include Dr. Robert P. Wei, Principal Investigator (fracture mechanics and materials science); Dr. D. Gary Harlow (probability modeling); Dr. Ming Gao (materials science); Dr. Kuang-Chung Wan (Ph.D. 1996, Applied Mechanics); Dr. Chi-Min Liao (Ph.D., 1997, Materials Science and Engineering); Dr. Evan J. Dolley, Jr. (Ph.D., 1999, Mechanical Engineering and Mechanics); Mr. Baekho Lee (M.S., 1999, Mechanical Engineering and Mechanics); Ms. Svetlana Oshkai (M.S. candidate in Mechanical Engineering and Mechanics); Ms. Julie DeMoyer and Mr. Jeffrey Zoleta (undergraduates in Mechanical Engineering and Mechanics), and Ms. L. D. Domanowski (undergraduate from Bucknell University). Ms. Domanowski was supported by a summer internship provided by the P.C. Rossin College of Engineering and Applied Science at Lehigh University. iii ACKNOWLEDGEMENTS This research was supported by the Federal Aviation Administration under Grant 92-G-0006 with complementary support by the Air Force office of Scientific Research under Grants F49620-98-1-0198 and F49620-96-1-0245. The authors wish to acknowledge the Air Vehicles Directorate of the US Air Force Research Laboratory for providing sections of the wing panels from the CZ-184 aircraft used in this investigation; the Boeing Company, Information, Space & Defense Systems for making the data available to us; and Joe Luzar of Boeing-Wichita for his technical assistance and helpful discussions. L.D. Domanowski was supported by a summer internship provided by the P.C. Rossin College of Engineering and Applied Science at Lehigh University. iv TABLE OF CONTENTS Page EXECUTIVE SUMMARY xiii 1. BACKGROUND AND OBJECTIVES 1-1 2. TECHNICAL APPROACH 2-1 3. LOCALIZED (PITTING) CORROSION 3-1 3.1 Constituent Particles 3-1 3.2 Pitting Corrosion 3-2 3.3 Electrochemical Measurements 3-8 3.4 Mechanistic Models 3-13 4. TRANSITION FROM PITTING TO FATIGUE CRACK GROWTH 4-1 5. FATIGUE CRACK GROWTH 5-1 5.1 Chemically Short-Crack Behavior 5-1 5.1.1 2024-T3 Aluminum Alloy 5-1 5.1.2 7075-T651 Aluminum Alloy 5-1 5.2 Impact of Chemically Short-Crack Behavior on Fatigue Life 5-4 5.2.1 7075-T651 Aluminum Alloy 5-4 5.2.2 2024-T3 Aluminum Alloy 5-7 6. MODELING AND INSIGHT 6-1 6.1 Effect of Pitting Corrosion on Fatigue Life 6-1 6.1.1 Modeling and Initial Comparison 6-1 6.1.2 Further Verifications 6-3 6.1.3 Probabilistic Analysis 6-5 6.2 A Mechanistically Based Probability Approach: Probabilities of Occurrence and Detection 6-6 7. PROBABILITY MODELING AND ANALYSIS OF J-STARS TEARDOWN DATA FROM TWO B707 AIRCRAFT 7-1 7.1 Modification of the Mechanistically Based Probability Model 7-2 v 7.2 PoO and Statistical Analysis of J-STARS Teardown Data 7-3 7.3 Estimation of Multisite Damage (MSD) 7-7 7.4 Metallographic Examinations of Damage and Implications 7-8 7.5 Statistical Analyses of the Lower Left Wing Skin of CZ-184 Aircraft 7-12 8. SUMMARY 8-1 9. REFERENCES 9-1 APPENDIX A Presentations and Publications From the Program vi LIST OF FIGURES Figure Page 2-1 Schematic Diagram of the Development of Corrosion and Corrosion Fatigue Crack Growth 2-1 2-2 Flow Diagram Showing the Overall Processes for Corrosion and Fatigue Damage 2-2 3-1 SEM Micrograph Showing Pitting Induced by Constituent Particles in a 2024-T3 Aluminum Alloy 3-2 3-2 SEM Micrograph of the Cross Section of Severe Corrosion Pits in a 2024-T3 Aluminum Alloy (TS) Surface Along With an Inset Showing the Appearance of the Corresponding Pits on the LS Surface 3-3 3-3 SEM Microfractographs of Fatigue Fracture Surface of a 2024-T3 Alloy Showing a Severe Corrosion Pit as the Crack Nucleus: Viewed (a) Normal and (b) at 45° to the Fracture Surface 3-4 3-4 SEM Micrographs Showing Severe Pitting in a 2024-T3 Aluminum Alloy After 500 Hours in 0.5M NaCl Solution at Room Temperature: (a) the LS Surface After Chemical Cleaning and (b) the Corresponding 3D Replica 3-4 3-5 SEM Micrographs of the Epoxy Replica of a Severe Corrosion Pit in 2024-T3 Aluminum Alloy: (a) Plan (Bottom) and (b) Elevation (Side) View Relative to the Original Pit 3-5 3-6 TEM Micrograph of 7075-T651 Aluminum Alloy Showing Oxide Left Behind by Particle-Induced Corrosion: (a) Residual Oxide and (b) Reconstructed Image Showing Position of Original Particle 3-6 3-7 Low- and High-Magnification TEM Micrographs Showing a Al2Cu Particle and its Environs in a 2024-T3 Aluminum Alloy: (a) Before and (b) After 180-min. (Cumulative) Immersion in 0.5M NaCl Solution at Room Temperature 3-7 3-8 TEM Micrographs Showing an Al2CuMg Particle and its Environs in a 2024-T3 Aluminum Alloy: (a) Before and (b) After 15-min. Immersion in 0.5M NaCl Solution at Room Temperature 3-8 3-9 Relationship Between Cathode-to-Anode Area Ratio and Current Densities of Alloy A-Al Couple in Neutral 0.5M NaCl Solution 3-9 3-10 Relationship Between Cathode-to-Anode Area Ratio and Current Densities of Alloy B-Al Couple in Neutral 0.5M NaCl Solution 3-10 3-11 Relationship Between Cathode-to-Anode Area Ratio and Current Densities of Alloy A-Al Couple in 0.5M NaCl + 0.07M AlCl3 Solution (pH ≅ 3.5) 3-10 vii 3-12 Relationship Between Cathode-to-Anode Area Ratio and Current Densities of Alloy B-Al Couple in 0.5M NaCl + 0.07M AlCl3 Solution (pH ≅ 3.5) 3-11 3-13 Conceptual Models of Particle-Matrix Interactions (Local Corrosion) for (a) a Cathodic and (b) an Anodic Particle 3-14 3-14 Schematic Diagram of a Conceptual Model for Pitting
Details
-
File Typepdf
-
Upload Time-
-
Content LanguagesEnglish
-
Upload UserAnonymous/Not logged-in
-
File Pages79 Page
-
File Size-