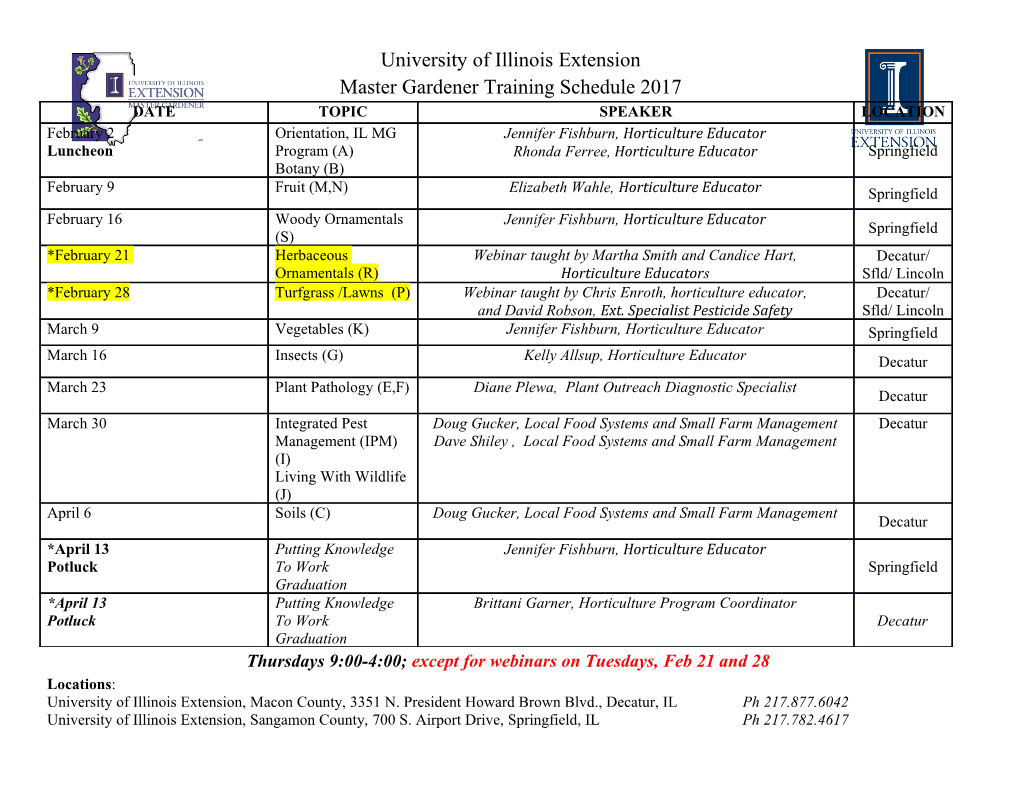
Gas exchange process for IC-engines: poppet valves, valve timing and variable valve actuation Topics Analysis of the main parameters influencing the volumetric efficiency in IC engines: - Valves and valve timing - Dynamic effects - Turbocharging Introduction At the end of each cycle, in an IC engine the burned gases have to be replaced by new charge of air/fuel and (often) recycled exhaust gases. The gas exchange process is quite complex since it involves many time-dependent phenomena, such as: unsteady and compressible flows, frictional losses, heat transfers, area changes and complex geometrical paths. During the gas exchange process, because of the cyclic operation of cylinders, the flows through each component are pulsating and strongly influenced by inertia effects and wave actions, and hence difficult to be analyzed. Layout of the intake and exhaust systems for a 4- stroke, TC, SI engine. Volumetric efficiency or filling coefficient Volumetric efficiency (ηv) or filling coefficient (λv), defined as: ma: trapped air mass per cycle mt: theoretical amount of mass that can fill the cylinder displaced volume ρa: air density at reference conditions V: cylinder displaced volume The filling coefficient measures the engine capability to fill its displacement with air. For this reason, it is defined as the ratio between the trapped air mass per cycle and the theoretical amount of mass that can fill the engine displacement at reference conditions. The actual air mass, ma, aspirated inside the cylinder at the end of the single cycle, is different from the ideal one mt, for different reasons: 1) Burned gases inside the combustion chamber Vc at the end of the exhaust process, have a pressure pr which is higher than the atmospheric pressure pa. Therefore, burned gases expand, at the beginning of the induction stroke, filling part of the displacement Vd (that, instead, should be filled by fresh charge). 2) Pressure inside the cylinder at the end of the induction stroke is lower than pa, because energy must be spent to overcome frictional losses along the induction system and to accelerate the fluid through the inlet ports. The inlet valve does not close at BDC (point 1), but somewhat later at the beginning of the compression stroke (point i), where is pi> pa. However, the available volume Vi for fresh charge is then lower than V1, hence the loss in filling is evident. 3) During the intake exchange process, heat is exchanged between the hot engine walls and the entering fresh fluid, increasing the temperature of the new charge and hence decreasing the air density inside the cylinder at the end of the induction process. 4) The gas exchange process is influenced by dynamic effects, due to unsteady flows and pressure wave actions, which can improve or hinder the cylinder filling, depending on whether the geometry of the induction system is tuned or not with available times. To overcome this limitation, some car engines use now induction systems of variable geometry with the rotational speed. 5) For reasons of simplicity, cost and reliability, the conventional engines are equipped with a fixed angular valve timing. This means that the crank angles of valve opening and closing does not vary with the engine rotational speed n. For this reason, times available for the exchange process decrease when the engine speed increases. Hence fixed timings (with fixed geometry) can be optimized just for a limited engine speed range. A first estimation of the filling coefficient (λv) can be achieved by applying the energy conservation to the intake process: which, after some manipulation, can lead to the following expression: Numerical fluid dynamic models are needed for more accurate predictions. Dependency of the volumetric efficiency from the engine speed: 1) CURVE A: Non- dependent speed effects (like fuel vapour pressure) drop ηv below 100% 2) CURVE B: Charge heating in the manifolds and cylinder drops curve A to curve B. It has a greater effect at lower engine speeds, due to the longer gas residence times. 3) CURVE C: Frictional flow losses increase as the square of the engine speed, and drop curve B to curve C. 4) CURVE D: At higher engine speeds, the flow into the engine during at least part of the intake process becomes chocked. Once it occurs, further increases in speed do not increase the flow rate significantly, so volumetric efficiency decreases sharply (curve C to curve D). 5) The induction ram effect, at higher engine speeds, raises curve D to curve E. Late inlet valve closing, which allows advantage to be taken of increased charging at higher speeds, results in a decrease of ηvat low engine speeds due to backflow (curves C and D to F). Finally, intake and/or exhaust tuning can increase the volumetric efficiency (often by a substantial amount) over part of the engine speed range, curve F to G. Poppet Valves In a four-stroke engine, the most significant flow restriction, along all the intake and exhaust systems, is usually located in the poppet valves. For this reason, the flow through these engine components has to be analyzed. Modern four-stroke engines usually control the opening and closing of the intake and exhaust ports of the cylinders by poppet valves. They offer: - Minimum fluid-dynamic losses - High sealing ability and good reliability while subjected to high accelerations (and hence inertia forces). The quantity of heat absorbed by the valve when heat is released from the products of combustion amounts roughly to 70% by conduction through the valve head when it is closed, and 30% by conduction through the fillet underside of the valve when it is open and the exhaust gas is escaping through the exhaust port. When the valve is closed, about 76% of the total heat input from the heat released by combustion is transferred by conduction to the cylinder head coolant by way of the valve seat, and only 24 % of the total heat input to the valve is conveyed through the valve stem to the cylinder head coolant via the valve guide. High operating temperatures due to incorrect ignition timing and mixture strength raise the valve head temperature until the valve head becomes the focal point for pre-ignition. A portion of the valve head then becomes the point of ignition which again leads to further heating of the valve head until eventually the valve seat distorts. Consequently, the poor seating of the valve during the combustion phase provides an escape route for some of the burning gases and, as a result, causes excessive local overheat and burning in the valve rim and seat region. If large quantities of combustion products accumulate around the valve seat they will eventually become dislodged due to the repeated valve closing impact, some of the break-away deposits will then provide exit passages for the burning gases. The partial radial tunnelling around the valve seat when it is closed will therefore cause the valve seat to overheat as the gas escapes, since the heat flow path around the head is interrupted. This may result in severe carburization and oxidation of the valve seat surface, and ultimately it may burn a semiconcave groove into and around the valve seat. The name 'guttering' is derived from the top face contour of house guttering. Flow coefficient Flow through a valve is mainly influenced by the available area and the pressure head across cylinder and pipe. The valve flow area (both exhaust and intake) is rapidly varying with time, or better it is a function of crank angle θ, which is proportional to time, for a given shaft rotational speed ω. The pressure upstream the valves changes continuously with time, therefore the flow through the valve results highly unsteady. It is also turbulent, and some useful information can be drawn from flow tests in steady-state conditions. The figure illustrates the main device used in these flow tests. Direct flow (from the manifold to cylinder): through the actual port-valve group (or a preliminary model), air is aspirated by a fan located in the cylinder, to simulate the piston effect. Reverse flow (from the cylinder to the pipe): in this case, the fan is pressuring the cylinder. In both cases, the lift is kept constant and, at steady flow conditions, actual air mass flow rates are measured, for different valve lifts and pressure heads Δpv across the valve. To derive more general information about the flow, that may be extended to other engines operating at similar fluid-dynamic conditions, the measured actual air mass flow rate values are made dimensionless by dividing them by the ideal mass flow rates that would pass through a reference area Avref under the same Δpv in an iso-entropic expansion. This is the valve flow coefficient C: ma = measured air mass flow rate mid = ideal air mass flow rate that would pass through a reference area Avref under the same Δpv in an iso-entropic expansion. Avref = is the reference area, set to be constant and equal to the inner seat area: The flow coefficient for fully turbulent flow is independent on Re. where a01 is the total speed sound in 1 and the compressible flow function is: m* is the critical or sonic mass flow. The flow coefficient includes not only the typical losses of the actual flow (friction, heat exchange, energy dissipation, etc.), but also effects of continuous change in geometric flow area. Since the flow is fully turbulent, the effect of Δpv is negligible, and typical values of C are usually plotted as function of l/dv (non-dimensional valve lift). C is increasing with l/dv since the geometric flow area increases, but it do not reach values near unity because the ideal flow rate is referred to Avref, that is greater than the actual one, even at lmax.
Details
-
File Typepdf
-
Upload Time-
-
Content LanguagesEnglish
-
Upload UserAnonymous/Not logged-in
-
File Pages9 Page
-
File Size-