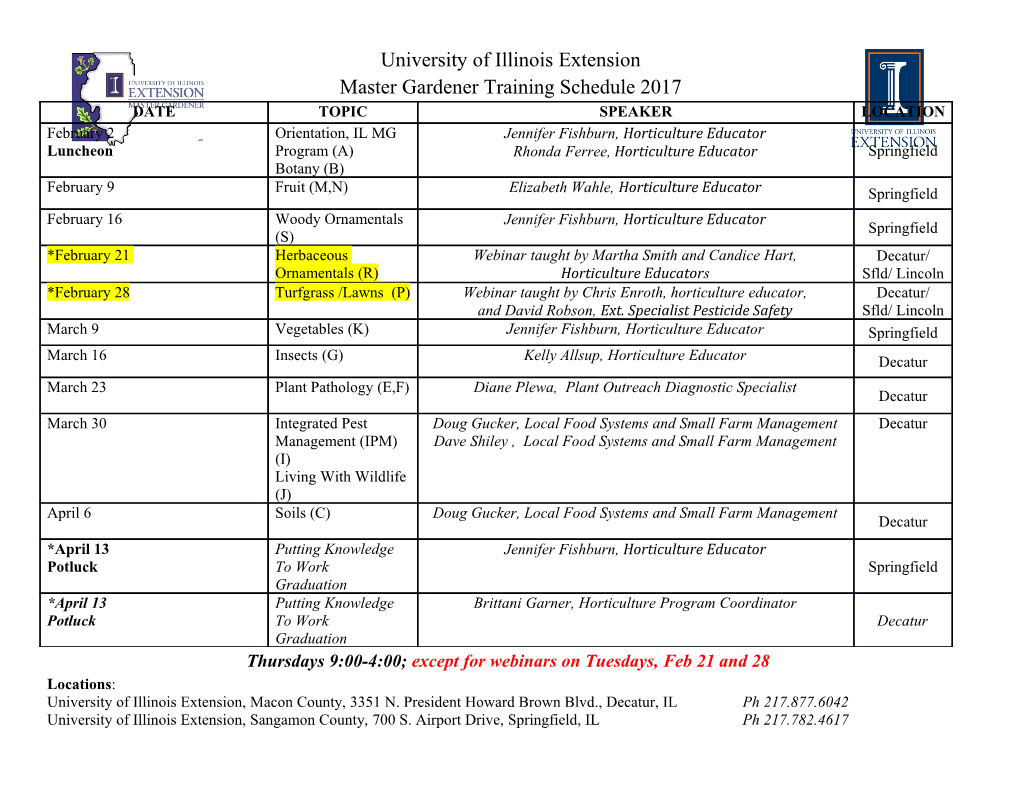
Indian Journal of Engineering & Materials Sciences '- " Vol. 1, October 1994, pp. 273-278 ' ., , -, ' Theory of abrasive wear mechanism for FRP composite Navin Chand", B Majumdarb & M Fahim" "Regional Research Laboratory (CSIR), Bhopal 462 026, India bGovernment Science College, Raipur 492 010, India In fibre reinforced composites,residual thermal stressis build up becauseof a difference in thermal expansioncoefficients of the fibre and matrix. After abrasionprocess cooling takes place from high temperature.During this changein temperatureeach pan of heterogeneouscomposite system undergoes a different thermal contractionor expansionstrain giving rise to microstructuralresidual stresses. Spring network model has been used to define the abrasivewear mechanismin glassfibre reinforced polymer f composites.A theoritical wear equationis derived from the combinationof residual stressand fracture toughness. Studies on wear mechanism of the fibre reinforced Model formulation polymer composite involve understanding of the Curtin and Scherl3 have studied brittle failure complex and undefined structure of composite, by using Spring network model. This model con- mainly composed of two heterogeneous materials. sists of different nodes connected to each other These studies assume significance in view of the with linearly elastic springs that have failure strain greater tribological importance of to these materi- associated with them. By varying the spring par- also Much investigations have been devoted tow- ameters, viz., spring equillibrium length, force con- ards the tribological studies of FRP materialsl-16. stant and displacement at which failure occurs, the Reinforcement of fibres complicates the structure disorder can be introduced in the system. of solid as a whole. This makes the problem cum- In case of FRP composite, the spacing between k bersome in investigating the mechanism responsi- the fibres is not uniform which always happen in ble for the wear of reinforced materials. Most of actual composite and hence a system is proposed the studies are concentrated on the sliding wear in which the disorder is supposed to be created in characteristics of glass fibre reinforced polymer the unstrained size of the element of the fibre. The composites7-9.Literature on abrasive wear studies approach is based on the fact that in initial stage of polymer composites is comparatively scarce when the material is removed, the spring constant and most of the work relates on either short or through which the molecules are attached is differ- continuous fibre reinforced compositeIO-12. ent from that of the material which is worn out in In this paper, abrasive wear mechanism of very the next subsequent stage, thereby, allowing dis- high weight fraction woven glass cloth reinforced order by virtue of spring parameters which vary polymer composites has been Teported. An at- from spring to spring in either correlated or un- tempt has also been made to analyse the genera- correlated manner. tion of residual stress during experiment and its Physically the whole picture is like that the ir- distribution in fibre reinforced polymer composite reducible material region which has been worn out in which molecules are assumed to be connected during the process exhibits distributed disorder. A with elastic springs. The wear mechanism on the spring snapping force law has been used because basis of Spring network model in FRP composites of the fact that these springs are not actually has also been defined. Stress intensity factor, K1C meant to represent interatomic bonds. is calculated based on the proposed concept. Since it is being assumed that fibres are not Moreover, a new relation between K1C and wear equally spaced in FRP composite, therefore, a volume is established proved that K IC depends on topological disorder appear just as in any real sys- particle size. tern. Conventionally, the topological disorder is .~-,,--"C 274 INDIAN J. ENG. MATER SCI.,OcrOBER 1994 not unimportant but spring to spring disorder ac- Moreover, the spherically symmetric nature of re- counts for all the disorder polymer composite. sidual stress makes it clear that the removal of the During the first 100 cycles of the experiment, material from bulk matrix consequently effects the " described elsewherel4, which takes about three mi- remaining residual stress fields in the vicinity. nutes, a small amount of material is worn out. It is Since disorder in the residual stress appears in the certain that the local temperature of the material scale of interparticle spacing the spring between which is in contact with abrasive paper will in- each particle and its neighbours can be identified crease. Due to this thermal gradient within the po- with microstructural features. Any failure of the lymer network a stress will be generated which physical region between neighbouring particles may be taken as one of the possible source of dis- would possibly lead to debonding of the interface order. This fact seems to be logical because there between particle and matrix. This phenomenon are clear evidences of the presence of residual would lead to cracking in the physical system stresses in a variety of composite materials. Con- which reflects non concentrated load transfer as clusively, Spring network model has been used to needed for Spring model in case of FRP compo- understand in detail the spatial variations of resid- site. A spring failure would then represent a de- uaI stresses that are expected during abrasion of bonded partIcle with a crack arrested in the inters- FRP composite. titial matrix region possibly in a lower residual During the second phase of experiment, the stress site during the removal of material. reinforced polymer matrix gives rise to residual In the Spring network model system it has been -..J stress as the polymer composite cools down by an assumed that physical disorder dominates over the amount of i\ 1; compared to room temperature or topological disorder because it leads to an open initial temperature of the composite. During this path for the study of microstructural features. In second phase, there will be a volume mismatch addition, the effects of topological disorder on a given by, partial basis can be studied by spring disorder i\ vi .model in a regular lattice network system. ~=i\a'i\T ...(1) In order to understand and interpret micros- tructural features on the basis of the springs in ne- which can be calculated using simple elasticity the- twork ~odel, resid~al stress dis!ri~ution is int~o- orylS, where i\a is actually related to mismatch duced I~tO the. sl?nng ~haract~r!st~cs by allowmg between coefficients of thermal expansion of the fo! spatIal varI~tI?nS I.n eqwllibn~ len~, '0 matrix material and the remaining second phase Wl~OUt ~y vanatlons m th~ elastiCIty or failure particles in a polymer composite. ~tr~, .Er, m. the present physlcal.syste~. Ea.ch sp~- For the material used in the present study with- mg m Isola~on has no stres~ on It. This s~nng will ~ in the limit of experimental error for equal moduli have a resIdual stres~ dunng the abrasIv~ wear of glass fibre and resin matrix, stress fields can be process ~hen. c?nstramts of. the surroundmg ne- calculated where tangential stress field a is given twork SprIng IS Imposed on It. Consequently, any by TR variation in the equillibrium spring length, '0' ref- , lects that the distributions of interparticle spacings, aTR = --~ 2 ...(ii) particle size and shapes and to some extent orient- 2(Rlro) ations related to the applied stress. Also the net h . th uillib . I gth f h . R residual stress acting on a spring in present ne- w, ere ~ 0 IS e eq num en 0 t e SprIng ' twork system predommantly. depends upon, 0 va- "I IS the radIus of sphencal partIcle bemg removed I f th ' ghb .. ..ues 0 e nel ounng SprIngs w hicae h t th same from the matnx and ao IS equal to, tIme.. IS a dd ..Itlon al d .Isor der p h YSIC. all Y present .m ao=E'i\a'i\.T ...(iii) the real polymer composite due to the closed proximity of other stressed particle. During the process of abrasive wear, firstly the Any variation in the distributed '0 values or re- stress applied is symmetric in nature, secondly, the sidual strain can be measured on the basis of Er, .. removal of the material always takes place along during deformation induced wear process. If the the same wear track and henceforth symmetric. As variations in '0 is characterised by distributed dis- such the distribution of the residual stress within order in i\,o and are small compared with Er then the bulk matrix after each phaSe of varying mode the distributed disorder is fairly unimportant be- would be symmetric in nature. Otherwise, cracks cause as soon as the first spring falls, the neigh- ;. in the bulk matrix would have been observed bouring springs can not support the transferred which is not seen in case of FRP composite. load during the removal of the material from the -.~' I ' J" : CHAND etal.: ABRASIVE WEAR MECHANISM OF FRP COMPOSI1E 275 bulk, even if they have some residual compressive is comprised of two material states, fibre makes stress, and the network fails completely. Alternat.. one material state while resin forms second state. ively, if variations in r 0 are comparable to f f then These two states represent two different material the distributed damage will be nucleated at low phases. applied stresses but no global failure occurs. At H Vs is volume of the solid, Vv is the volume of higher applied stresses crack propogation might be voids present in the composite, V is the volume visible and during this process the ultimate failure of fibres and V is the volume of p~lymer then to- must be sensitive to the complete full distribution tal volume, Vof pcoItlposite is given by, of residual strains.
Details
-
File Typepdf
-
Upload Time-
-
Content LanguagesEnglish
-
Upload UserAnonymous/Not logged-in
-
File Pages6 Page
-
File Size-