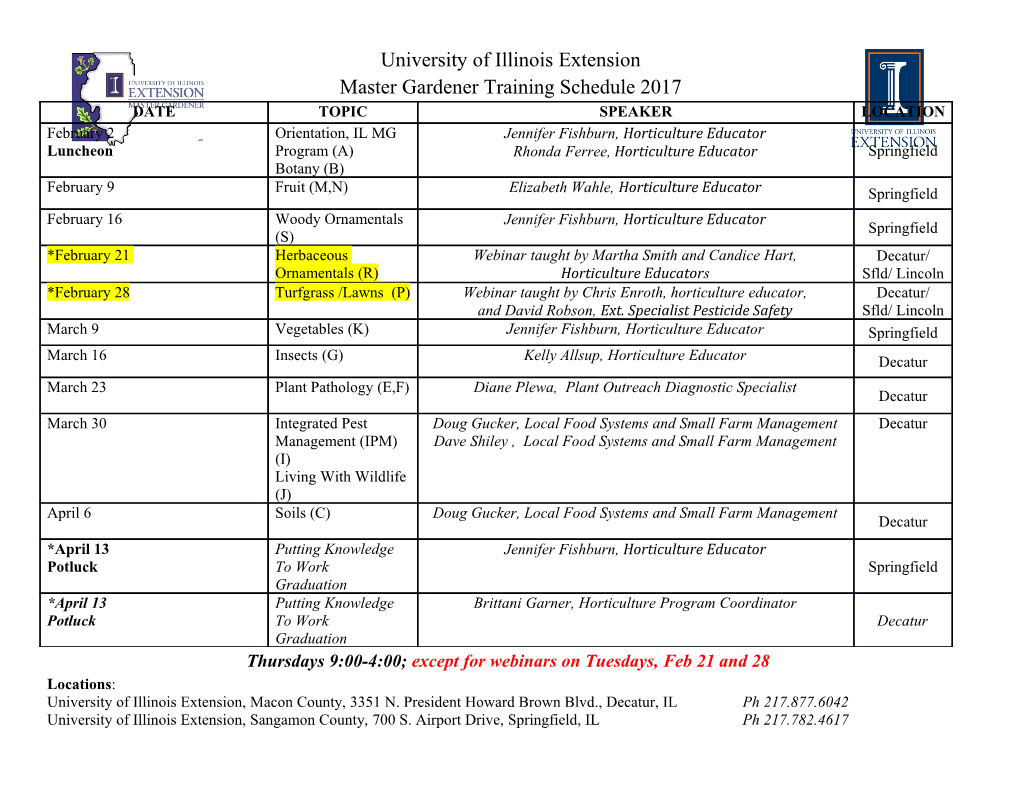
Instructor Engr. Muhammad Shahzad (Assistant Professor) Mining Engineeering Department University of Engineering & Technology Lahore The practice of minerals processing is as old as human civilization. Minerals and products derived from minerals have formed our development cultures from the flints of the Stone Age man to the uranium ores of Atomic Age. METSO 3 Contents Section 1: CRUSHING Exp. # 1) “Machine Study of Laboratory Jaw Crusher and to perform a crushing test on the given sample, and to analyze the product for reduction ratio” Exp. # 2) “Machine Study of Laboratory Roll Crusher and to perform a crushing test on the given sample, and to analyze size distribution in the product by sieve analysis” Exp. # 3) “Machine Study of Laboratory Hammer Mill and to perform a crushing test on the given sample, and to analyze size distribution in the product by sieve analysis” Section 2: GRINDING Exp. # 4) “Machine Study of Laboratory Disc Mill and to perform a grinding test on the given sample, and to analyze size distribution in the product by sieve analysis” Exp. # 5) “Machine Study of Laboratory Rod Mill and to perform a grinding test on the given sample, and to analyze size distribution in the product by sieve analysis” Exp. # 6) “Machine Study of Denver Laboratory Ball Mill and to perform a grinding test on the given sample, and to analyze size distribution in the product by sieve analysis” Section 3: SIZING Exp. # 7) “Machine study of a double-deck vibratory screen & hummer electromagnetic screen and determining their performance by a screening test on the given sample”. Exp. # 8) “Machine study of a Laboratory centrifugal hydro classifier and to find its cut size under the given conditions”. Section 4: GRAVITY CONCENTRATION Exp. # 9) “Machine Study of a Laboratory type Mineral/Coal Jig and to perform a gravity separation test on the given sample” Exp. # 10) “Machine Study of a Concentrating Shaking Table and to perform a gravity separation test on the given sample” Exp. # 11) “Machine Study of a Humphrey’s Spirals and to perform a gravity separation test on the given sample” (Coal/Metallic Minerals) Section 5: FROTH FLOTATION Exp. # 12) “To study the principle and operation of Laboratory Flotation Machine, and to perform a froth flotation test on a coal sample and to determine its separation efficiency” 4 5 6 Experiment No. 1: 1.1. Objectives The main objectives of this experiment are to study the various parts of Laboratory Jaw crusher with special emphasis on their functions, to perform a crushing test on a given sample, to analyze the product by sieve analysis and to calculate its reduction ratio by feed size and product size measurement. 1.2. Apparatus/Materials • Laboratory Jaw Crusher • Vernier Caliper • Rock sample for crushing • Sieve set (26.67, 18.85, 13.33, 6.70, 2.36 and 0.85 mm) • Ro-Tap Sieve Shaker • Torsion Balance 1.3. Procedure • Study each part of the machine and know the function of every component • Switch on the machine and study the movement of the moving jaw and the variation of set with motion. • Measure the side of the gape and adjust the set with the help of a lead lump and meter rod or coarse sieve and record measurements. • Examine the feed, measure the largest lump either with a meter rod or coarse sieve as the case may be and record it. • Feed the machine and crush the entire sample. • Perform sieve analysis on the product by using coarse sieve set as given in 1.2. • Calculate the reduction ratio of the machine. 1.4. Specifications of Laboratory Jaw Crusher The specifications of laboratory jaw crusher are given in Table 1.1. Table 1.1: Specifications of Laboratory Jaw Crusher Name Denver Blake Jaw Crusher Motor 5hp Motor RPM 1440 Crusher RPM 325 – 375 Face Of Flywheel 3 ¼ “ Movable Jaw Depth 14” Fix Jaw Depth 12” Width Of Jaw Plate 6” 7 Crusher Designed Capacity 600 lbs/hr Flywheel Diameter 18” Max: Feed Size (Gape) 5”×6” Size Of Set close ½ʺ open 1 ¼ ʺ 1.5. Observations and Calculations 1.5.1. Feed Size Sr. No. Length (mm) Width (mm) Height (mm) 1.5.2. Product Sieve Analysis Cumulative Mass Sr. Sieve Aperture Size Individual Mass Percentage No. Passing Retaining Geometric mean Measured Percentage Passing Retaining 1 2 3 4 5 6 7 1.5.3. Reduction ratio Determine the reduction ratio by the following relation: 80% 푃푎푠푠푖푛푔 퐹푒푒푑 푆푖푧푒 푅푒푑푢푐푡푖표푛 푅푎푡푖표 = 80 80% 푃푎푠푠푖푛푔 푃푟표푑푢푐푡 푆푖푧푒 1.6. Graphs 1. Draw graph of cumulative passing and retaining mass percentage against aperture size (geometric mean) and determine cut size, d10, d25, d50, and d75. 2. Draw log-normal plot between aperture size (geometric mean) and cumulative passing mass percentage and determine the standard deviation. 3. Express Gaudin-Schuhmann distribution on graph and determine the constants involved. 4. Express Rosin-Rammler distribution on graph and determine the constants involved. *Note: Read Topic 2.2. “Particle Size Distribution” in “Mineral Processing Design and Operation” by A. Gupta and D. S. Yan 1.7. Discussions Discuss the results and the information deducted from sieve analysis in details. 1.8. Conclusions Give concluding remarks about the experiment and its results. 8 1.9. Related Theory [References: Mineral Processing Technology by B. A. Wills (7th Edition-2005) & Mineral Processing Design and Operation by A. Gupta and D. S. Yan (1st Edition-2006)] 1.9.1. Introduction Jaw crushers are used as primary crushers, or the first step in the process of reducing rock. They crush primarily by using compression. The distinctive feature of this class of crusher is the two plates which open and shut like animal jaws. The jaws are set at an acute angle to each other and one jaw is pivoted so that it swings relative to the other fixed jaw. Material fed into the jaws is alternately nipped and released to fall further into the crushing chamber. Eventually it falls from the discharge aperture. 1.9.2. Types There are three basic types of jaw crusher as shown in Figure 1.1. Figure 1.1:1 Types of Jaw Crushers 1.9.2.1. Blake Type Jaw Crusher The Blake crusher was patented by Eli Whitney Blake in 1858. The swing jaw is fixed at the upper position. The Blake type jaw crusher has a fixed feed area and a variable discharge area. A. Double Toggle Blake Crusher In the double toggle jaw crushers, the oscillating motion of the swing jaw is caused by the vertical motion of the pitman. The pitman moves up and down. The swing jaw closes, i.e., it moves towards the fixed jaw when the pitman moves upward and opens during the downward motion of the pitman. This type is commonly used in mines due to its ability to crush tough and abrasive materials. 9 B. Single Toggle Blake Crusher In the single toggle jaw crushers, the swing jaw is suspended on the eccentric shaft which leads to a much more compact design. The swing jaw, suspended on the eccentric, undergoes two types of motion- swing motion towards the fixed jaw due to the action of toggle plate and vertical movement due the rotation of the eccentric. These two motions, when combined, lead to an elliptical jaw motion. This motion is useful as it assists in pushing the particles through the crushing chamber. This phenomena leads to higher capacity of the single toggle jaw crushers but it also results in higher wear of the crushing jaws. These type of jaw crushers are preferred for the crushing of softer particles. A comparison between two can also be seen in Figure 1.2. It shows the difference in the movement and the method of operation. Figure 1.2: Comparison between Single and Double Toggle Blake Type 1.9.2.2. Dodge Type Jaw Crusher In the Dodge type jaw crushers, the jaws are farther apart at the top than at the bottom, forming a tapered chute so that the material is crushed progressively smaller and smaller as it travels downward until it is small enough to escape from the bottom opening. The Dodge jaw crusher has a variable feed area and a fixed discharge area which leads to choking of the crusher and hence is used only for laboratory purposes and not for heavy duty operations. 1.9.2.3. Universal Jaw Crusher This jaw crusher continuously reduces material as it passes through the crushing chamber with its aggressive force feed action as the moveable jaw compresses inward and downward. The sharp primary blow at the top of the chamber reduces material instantly, while a secondary crushing action at the bottom further reduces material to the predetermined output size. Universal Jaw Crushers offer a compressive stroke that is nearly equal at both the top and bottom of the chamber, producing more spec material at a lower cost per ton. 10 1.9.3. Construction Main Frame The main frame is often made from cast iron or steel, connected with tie-bolts. It is often made in sections so that it can be transported underground for installation. Fully stress relieved after fabrication. Jaws The jaws are usually constructed from cast steel and are fitted with replaceable manganese steel liners, which are bolted in sections on to the jaws so that they can be removed easily and reversed periodically to equalize wear. One jaw is move able and other one is fixed. Cheek Plates These are fitted to the sides of the crushing chamber to protect the side main frame from wear. These are also made from manganese steel and have the similar life to the jaw plates.
Details
-
File Typepdf
-
Upload Time-
-
Content LanguagesEnglish
-
Upload UserAnonymous/Not logged-in
-
File Pages66 Page
-
File Size-