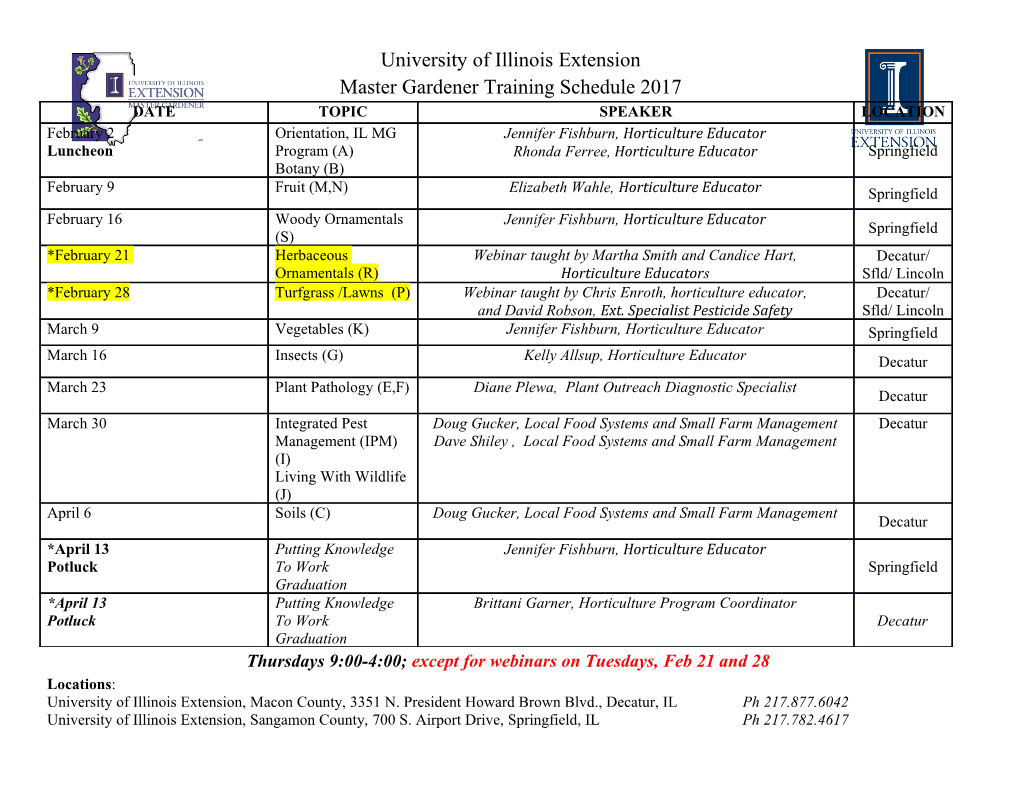
HYDRAULIC FRACTURE MODEL SENSITIVITY ANALYSES OF MASSIVELY STACKED LENTICULAR RESERVOIRS IN THE MESAVERDE FORMATION, SOUTHERN PICEANCE BASIN, COLORADO by Dr. Christopher A. Green A thesis submitted to the Faculty and the Board of Trustees of the Colorado School of Mines in partial fulfillment of the requirements for the degree of Master of Science (Petroleum Engineering). Golden, Colorado Date_____________________ Signed: ______________________________ Dr. Christopher A. Green Approved: ______________________________ Dr. Jennifer L. Miskimins Thesis Advisor Golden, Colorado Date_____________________ ______________________________ Dr. Craig W. Van Kirk Professor and Head, Department of Petroleum Engineering ii ABSTRACT The study area straddles the Colorado River and Interstate 70 in Garfield and Mesa counties, northwestern Colorado. The producing interval of the Mesaverde formation is a 1700 to 2000 ft thick laminated sequence of siltstones, shales and tight sandstones with a coaly interval at the base. The main producing interval is a non-marine reservoir, which exhibits a high degree of heterogeneity, both vertically and horizontally. A significant amount of work has previously been undertaken in the Piceance basin, at the multi-well experiment (MWX) site. A geologic characterization of the Mesaverde group established that the production was predominantly from the fluvial point bar sand bodies, with extremely low matrix permeabilities (<0.0001 mD). Subsequent geologic and geophysical work carried out in the nearby Rulison field established that there was an abundant system of micro-scale natural fractures and a less frequent system of macro- scale fractures. In common with most tight gas reservoirs, hydraulic stimulation is required to interconnect the dual-fracture system with the wellbore to maximize well production. Well costs are typically $1.25 MM and between 40 and 50% of the total cost may be due to the well stimulation treatment. Therefore, there is a need to optimize the process. Limited success has been achieved using ordinary techniques and a pseudo-three- dimensional model (P3D). This study uses a fully three-dimensional (3D) simulator, GOHFER, to develop a model of a hydraulically fractured well. This research uses a simulator to investigate input parameters, and from the results critical inputs are identified for realistic model development. For the study, input data from sixteen wells were analyzed for the type of data available and the quality of the data. A single well was selected for simulation which had available standard logs as well as mini-fracture iii analysis of all the reservoir sands identified by the operator. A comparison well was analyzed to help assess and validate the quality of the input data. The study used log-derived input data to define the rock elastic properties (Young’s modulus, Poisson’s ratio and Biot’s constant), porosity and lithology, using standard log ASCII (.las) files. The derived properties were compared to previous data from the MWX experiments and then used to help create an accurate lithologic representation of the reservoir. However, the physical properties of rocks are affected by in-situ stress and this was determined using small volume hydraulic fracture analysis, which has previously been used in the Mesaverde by Warpinski and Teufel (1989). This study details the results of fifty-six tests analyzed in both the study well and an adjacent well, for comparison with one another as well as with historical data from the MWX site. A number of cases were then run using GOHFER, and the resulting model compared to microseismic measurements, taken during the treatment. The microseismic information indicates where shear slippage is occurring and provides a means of calibrating the simulator outputs to actual fracture geometry to obtain a matched model. The original hydraulic fracture model run using these data was found to have similar containment to the field data, without any changes being necessary to the stresses in bounding layers. This would suggest that the log-derived stress differences of the reservoir sands and the bounding shale layers are captured in the initial analyses. Sensitivity analysis of critical inputs is detailed in the study, and the results indicate that total stress and Young’s modulus are the primary controlling factors of the simulator outputs. The sensitivity analysis results are similar to those from previous research (Miskimins, 2002; Warpinski et al, 1998) whereby stress, or more precisely stress contrasts, and Young’s modulus were shown to play a major role in determining hydraulic fracture dimensions. The other inputs analyzed: permeability, Poisson’s ratio and pore pressure were found to be secondary factors controlling fracture growth. The largest difference overall occurred for the advanced parameters analysis and showed their importance in the final matching process, even after other critical input data has been iv analyzed and validated. Most importantly, the sensitivity analysis indicated that the often used process of ‘net surface pressure matching’ to derive a valid simulator model can lead to significant discrepancies, when compared to a constrained, matched model. v TABLE OF CONTENTS Page ABSTRACT ................................................................................................................ iii TABLE OF CONTENTS .......................................................................................... vi LIST OF FIGURES ................................................................................................... x LIST OF TABLES ..................................................................................................... xiv DEDICATION ............................................................................................................ xvi ACKNOWLEDGEMENTS ...................................................................................... xvii CHAPTER 1: INTRODUCTION ...................................................................... 1 1.1 Research Objectives ....................................................................................... 3 1.2 Research Contributions .................................................................................. 4 CHAPTER 2: LITERATURE REVIEW ......................................................... 6 2.1 Piceance Basin ............................................................................................... 6 2.1.1 Geology ........................................................................................ 8 2.1.2 Stratigraphy .................................................................................. 11 2.1.3 Natural Fracture Production ......................................................... 16 2.1.4 Piceance Basin Cumulative Production and Reserves ................. 17 2.1.5 Piceance Well Spacing ................................................................. 17 2.1.6 Piceance Basin Field Production .................................................. 17 2.1.7 Gas Source and Trapping ............................................................. 21 2.1.8 Mesaverde Reservoir Characterization ........................................ 22 2.2 Hydraulic Fracturing ...................................................................................... 22 2.3 Rock-Mechanical Properties .......................................................................... 24 2.4 Fracture Containment ..................................................................................... 33 2.5 Fracture Analysis Techniques ......................................................................... 36 2.5.1 Class 1 – Direct Far-Field Techniques ....................................... 36 vi 2.5.2 Class 2 – Direct Near-Wellbore Techniques .............................. 37 2.5.3. Class 3 - Indirect Fracture Techniques ....................................... 40 2.6 Mini-Fracture Analysis ................................................................................. 40 2.7 Fracture Geometry Modeling ....................................................................... 43 2.7.1 2D Models .................................................................................. 43 2.7.2 P3D Models ................................................................................ 44 2.7.3 3D models ................................................................................... 45 CHAPTER 3: MODEL INPUT DEVELOPMENT ....................................... 46 3.1 3D Simulation Software History .................................................................. 50 3.2 Study Wells/Model Development ................................................................ 53 3.3 General Case Development .......................................................................... 54 3.3.1 Young’s Modulus (E) ................................................................. 58 3.3.2 Poisson’s Ratio ........................................................................... 60 3.3.3 Biot's Constant ............................................................................ 60 3.3.4 In-Situ Stress .............................................................................. 61 3.3.4.1 Mini-Hydraulic Fracture Tests ............................................... 62 3.3.4.2 Process Zone Stress ................................................................ 72 3.3.4.3 Total Stress ............................................................................. 74 3.3.5 Permeability
Details
-
File Typepdf
-
Upload Time-
-
Content LanguagesEnglish
-
Upload UserAnonymous/Not logged-in
-
File Pages221 Page
-
File Size-