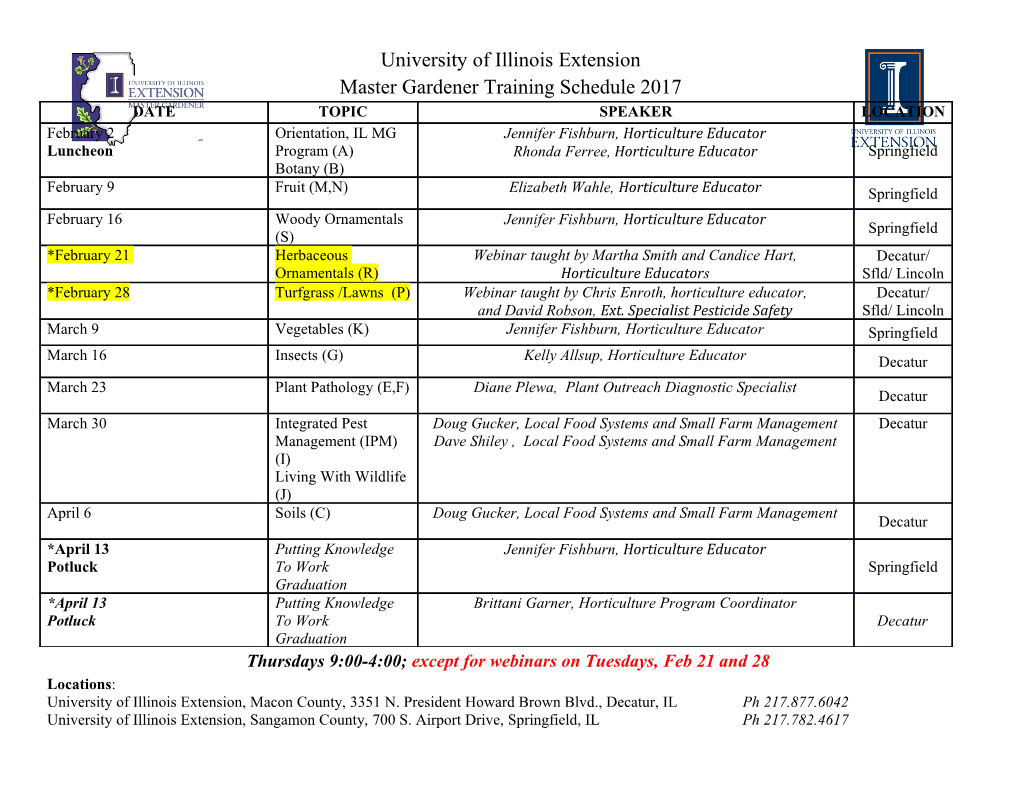
Review of Standard Microfabrication Technologies Ali Darvishian November 2019 Essential microfabrication steps: Wafer preparation Photolithography Film deposition/formation Etching/removal Dicing/packaging Essential microfabrication steps: Wafer preparation Photolithography Film deposition/formation Etching/removal Dicing/packaging Wafer preparation The surfaces of the wafers are not usually clean so before staring to use them, there is a need for a preparation step. This step can include soaking wafers in a solution. For example for silicon wafers: • They can be soaked in piranha solution for 15 min. • After that, they will be imported to a BHF solution for a short time (20s) to remove any oxide on the surface! • Then, they will be washes with DI water. • At the end, they will be dehydrated! Essential microfabrication steps: Wafer preparation Photolithography Film deposition/formation Etching/removal Dicing/packaging Photolithography The process of printing a given 2D pattern onto a thin film layer! It needs mask and photoresist! Mask permits exposure of only defined regions to the incident radiation • Typically made of a glass plate (soda lime or quartz glass) that is transparent to UV light • The pattern of interest is created on the glass using a thin (<1μm) metal film such as chromium (Cr) or gold (Au) • The mask plate has the pattern of interest repeatedly printed on it Photolithography Photoresist (PR) is a polymer whose chemical properties change when it is exposed to incident radiation, typically UV light. Note that PR cannot be exposed to temperatures above about 200°C because it burns (note that this is a polymer like plastic). Photolithography PR is typically in liquid form. It can be spun onto a silicon wafer at speeds of a few thousand RPM’s. Photolithography This spinning process creates a uniform film thickness in the range of 1-10’s of microns. After application, the PR is baked at 80-120°C to remove the solvents Photolithography The PR can be then developed in a “developer” like the standard photographic process! Two different results can be obtained depending on the type of PR used: • Positive PR: This type of PR is removed in the developer solution only in areas that have been exposed to UV radiation • Negative PR: This type of PR is hardened in the developer solution in areas that have been exposed to UV radiation. + - Photolithography Essential microfabrication steps: Wafer preparation Photolithography Film deposition/formation Etching/removal Dicing/packaging Film deposition/formation MEMS and ICs consist of a combination of many thin layers of different materials that are formed on top of one another in succession. Therefore, the basic process steps of forming very thin films (~1μm) of many different materials (insulators, semiconductors, and metals) are critical. Film deposition/formation • Film deposition • Oxidation • Doping Film deposition/formation Film deposition • Physical Vapor Deposition (PVD) • Chemical Vapor Deposition (CVD) Film deposition/formation Physical Vapor Deposition (PVD) The material is placed in a vacuum chamber, and the material is transformed into a gas phase (using different techniques). Atoms of the material leave the source and land on the wafer (sometimes referred to as the target). Film deposition/formation Physical Vapor Deposition (PVD) PVD is typically used to deposit most metals and some insulating and semiconductor films. It is most practical to deposit metal films using these techniques. Films ranging in thickness from 10Å to several microns can be deposited. The longer the deposition goes the thicker the film gets. Film deposition/formation Physical Vapor Deposition (PVD) Three basic techniques can be used to go from the solid material into a gas phase: • Evaporation • Sputtering • Ion beam deposition Film deposition/formation Physical Vapor Deposition (PVD) Evaporation The material to be deposited is placed in a vacuum chamber, it is somehow heated so it melts and evaporates. The vapor phase molecules land on the target wafer and form a thin film. Two basic approaches to evaporation are: – Thermal evaporation – Electron-beam (E-beam) evaporation Film deposition/formation Physical Vapor Deposition (PVD) Evaporation Thermal evaporation Thermal evaporation is the easiest of all and requires the simplest system. The film to be deposited is placed inside a crucible inside a vacuum chamber. The crucible is heated until the material evaporates. Film deposition/formation Physical Vapor Deposition (PVD) Evaporation E-beam evaporation In e-beam evaporation, the material is heated and melted using a high-energy electron beam. With e-beam, higher temperatures can be achieved. Therefore, a wider range of materials can be deposited. Most materials used in the IC industry these days, use e-beam evaporation. Film deposition/formation Physical Vapor Deposition (PVD) Evaporation Evaporation in general does not have a very good step coverage and the process is “line of sight”, as illustrated below: Film deposition/formation Physical Vapor Deposition (PVD) Sputtering A plasma is generated by applying a RF signal 5-15kV in a pressure range of 10-100 mTorr. The gas used is typically Ar. • The plasma creates Ar ions and electrons. • Ar ions bombard the source knocking off source atoms. • The source atoms get deposited on the substrate (target). Film deposition/formation Physical Vapor Deposition (PVD) Sputtering Features: • Wide variety of materials, including metals, insulators, and semiconductors • One can deposit multiple materials in a single pump down (meaning we do not need to break vacuum for next material) since multiple sources can be placed in the same chamber. • The films are deposited with better step coverage than e-beam so there is film continuity going over steps. Film deposition/formation Physical Vapor Deposition (PVD) Ion beam deposition It is also possible to create source atoms Source by bombarding the source with an ion beam. Ion beam The ion beam is collimated (formed into a narrow column), accelerated and then impinged upon the source. Source atoms are then knocked off and land on the substrate. Target wafer Film deposition/formation Physical Vapor Deposition (PVD) Ion beam deposition Features: • Good cleanliness and control • Both deposition of material and etching can be done at the same time. The ion beam can be directed towards the substrate to accomplish etching. • Multiple ion beams can be used to achieve deposition and etching. Film deposition/formation Film deposition • Physical Vapor Deposition (PVD) • Chemical Vapor Deposition (CVD) Film deposition/formation Chemical Vapor Deposition (CVD) Chemical vapor deposition is used to deposit thin films from a gas phase. It usually requires temperature in excess of 300°C, so this is higher temperature processes than the PVD techniques discussed before. CVD techniques are mostly used to deposit thin films of insulators and semiconductors, such as: – SiO2 – Si3N4 – Polycrystalline and amorphous silicon – Some metals such as W Film deposition/formation Chemical Vapor Deposition (CVD) A number of CVD techniques are available and include: – Low-Pressure CVD (LPCVD) – Plasma-Enhanced CVD (PECVD) – Atmospheric Pressure CVD (APCVD) … Film deposition/formation Chemical Vapor Deposition (CVD) Low-Pressure CVD (LPCVD) The pressure is usually in the range of several 100mTorr The deposition temperatures are usually in the range 700- 900°C Film deposition/formation Chemical Vapor Deposition (CVD) Low-Pressure CVD (LPCVD) Typical gases used and the reactions that produce the desired films are: SiH4 + N2 + N2O ====> SiO2 + N2 + H2O (for silicon dioxide) SiH4 + N2 + NH3 ====> Si3N4 + N2 + H2 (for silicon nitride) SiH4 + N2 ====> Si + N2 + H2 (for polycrystalline Si, Poly-Si) Film deposition/formation Chemical Vapor Deposition (CVD) Low-Pressure CVD (LPCVD) Features: • The deposited films are typically of very high quality and uniformity • The deposition rates are in the range of a few tens of Å per minute • Because of the low-pressure environment, the gas species usually reach all areas, even narrow gaps and channels, and the film is quite conformal. This also causes the film to be deposited everywhere on the chamber walls. Therefore, the chambers need to be cleaned rather frequently Film deposition/formation Chemical Vapor Deposition (CVD) Plasma-Enhanced CVD (PECVD) The energy required for the reaction is provided through a plasma. An RF field is used to excite a plasma over the substrate to aid in the gas decomposition process. Deposition temperatures here are in the range 300-400°C. This is an important difference with LPCVD, and is one of the principal advantages of PECVD. Film deposition/formation Chemical Vapor Deposition (CVD) Plasma-Enhanced CVD (PECVD) Features: • The lower deposition temperature allows PECVD films to be deposited over metal films, and over substrates such as GaAs that cannot withstand high temperature processing. • PECVD film quality is not as high as LPCVD films. • A variety of films, including oxide, nitride, poly-Si and amorphous Si, and doped oxides and nitrides can be deposited using PECVD. • Deposition rates vary in the range 10-100 nm/minute, depending on the temperature, pressure, flow rates, etc. Film deposition/formation • Film deposition • Oxidation • Doping Film deposition/formation Oxidation Si, like many other materials, reacts with oxygen, and forms a very stable and high quality dielectric, silicon oxide SiO2. This ability to form a high quality dielectric is perhaps one of the most important properties that has enabled Si to become the material of choice for integrated circuits (IC’s). SiO2 has a wide range of uses in both ICs and MEMS. At room temperature the silicon oxidation process is extremely slow. Therefore, a high-temperature process is used to facilitate silicon oxidation in a timely manner. Film deposition/formation Oxidation The volume of oxide formed is 2.2 times the volume of silicon used in the process. Film deposition/formation Oxidation High-Temperature Oxidation Wafers are first cleaned and then placed inside a furnace whose temperature can be controlled accurately (better than 1°C). A carrier gas (typically nitrogen) is flown through the furnace.
Details
-
File Typepdf
-
Upload Time-
-
Content LanguagesEnglish
-
Upload UserAnonymous/Not logged-in
-
File Pages77 Page
-
File Size-