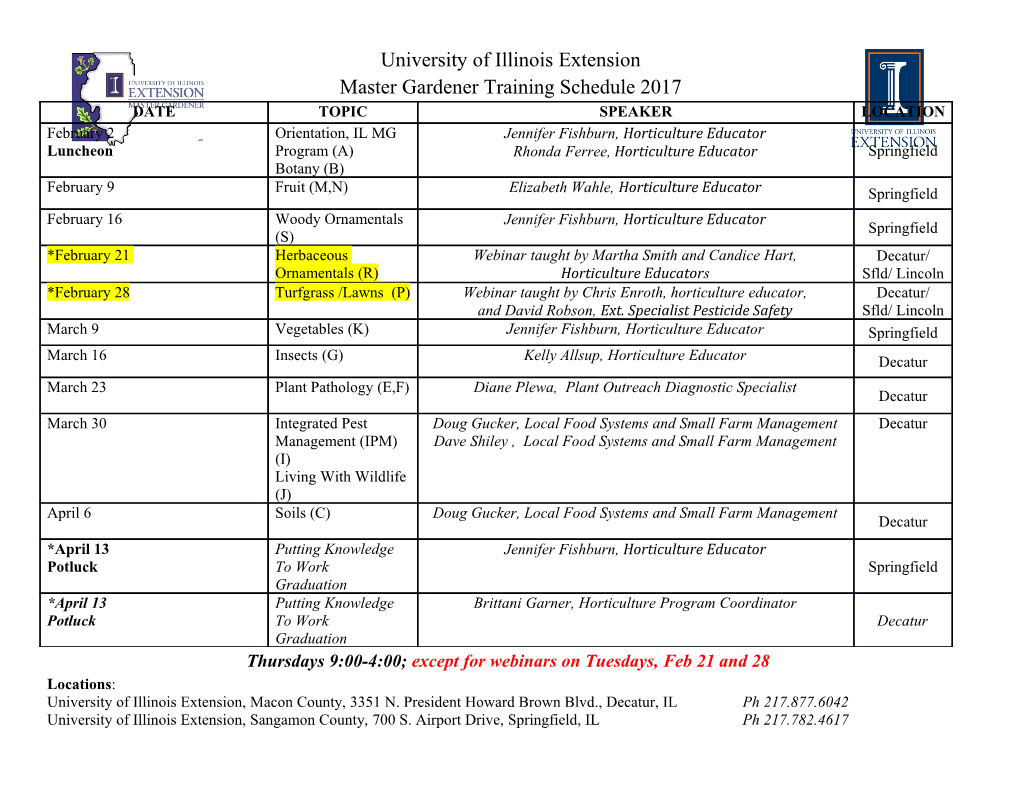
1 Determination of Coefficient for Transformation Plasticity in Terms of Three-Point Bending System∗ Kenichi OSHITA∗∗, Shigeru NAGAKI∗∗, Shinichi ASAOKA∗∗∗ and Katsuyuki MOROZUMI∗∗∗∗ To determine the transformation plasticity coefficient, a three-point bending system is employed and the large deflection due to transformation plasticity in bending is analyzed un- der the simplified assumption that transformations occur uniformly across the cross-section of a beam. It is shown that the deflection due to transformation plasticity is similar to that due to elastic deformation, and simple relationships are also derived between the ratio of the maximum deflection to the elastic deflection and material constants (transformation plasticity coefficient K and Young’s modulus E). Experiments are carried out for a slender bar speci- men, which is loaded in a three-point bending system, and the austenized specimen is cooled so that martensite transformation accompanied by transformation plasticity occurs and the profile and maximum value of the deflection of the specimen are measured. The measured profiles of deflection agree very well with the theoretical results. This proves the validity of the proposed method. The transformation plasticity coefficient is also determined by the proposed method. Key Words: Plasticity, Transformation Plasticity, Constitutive Equation, Three-Point Bend- ing System many materials. 1. Introduction Recently, Tutumi et al. have clearly shown experi- In the stress and transformation analyses of heat- mentally that the deflection due to transformation plastic- treatment and welding, the importance of accurately tak- ity occurs in bending a slender bar specimen, which was ing the effect of the transformation plasticity into ac- then employed to identify the transformation plasticity co- ffi (10) count is pointed out(1) – (4) and many studies on this com- e cient . Moreover, Inoue et al. proposed a method for ffi position rule have been carried out(5) – (7). For example, determining the transformation plasticity coe cient using (1) the material constant of transformation plasticity, that is, a four-point bending system . It seems that it is easy for the transformation plasticity coefficient, is obtained from a four-point bending system to theoretically treat test re- ffi the temperature-deflection curves obtained under a ten- sults and that the transformation plasticity coe cient ob- sile load(8), (9). However, an experimental method of accu- tained using this system is extremely precise because the rately measuring transformation plasticity coefficient us- distributions of bending moment and stress are uniform. ing a simple device has not been established yet and reli- However, three-point bending tests are simpler and easier able data on this parameter are still limited at present in to perform than four-point bending tests. In the present paper, we propose a method for the easy determination ffi ∗ Received 1st April, 2004 (No. 02-1470). Japanese Orig- of the transformation plasticity coe cient in terms of the inal: Trans. Jpn. Soc. Mech. Eng., Vol.69, No.684, A three-point bending system and experimentally discuss the (2003), pp.1230–1235 (Received 13th December, 2002) validity of this method. ∗∗ Department of Mechanical Systems Engineering, Tokyo University of Agriculture and Technology, 2–24–16 Naka- 2. Analysis cho, Koganei-city, Tokyo 184–8588, Japan. In bending tests, to determine the transformation plas- E-mail: [email protected] ffi ∗∗∗ Pioneer Display Products Co., Ltd., 15–1 Nishinotani, ticity coe cient, a constant load (moment) is applied to Washizu, Hukuroi-city, Shizuoka 437–8511, Japan a heated slender bar specimen, which is cooled. Deflec- ∗∗∗∗ Nihon ESI K.K., 45–18 Oyama-cho, Shibuya-ku, Tokyo tion is then measured at the center of the specimen dur- 107–0062, Japan. E-mail: [email protected] ing cooling. It is assumed that neither restraint nor force JSME International Journal Series A, Vol. 48, No. 1, 2005 2 axially exist in this specimen, which is simply supported occurs, where the volume fraction of the generated phase during test. In this section, the procedure of this analytical is defined as ξ. Furthermore, Young’s modulus E and the method is discussed and then it is shown that the transfor- coefficient of linear expansion α are equal in each phase, mation plasticity coefficient can be obtained by examining and β and T are the expansion coefficient due to trans- maximum bending deflection experimentally. formation and the temperature, respectively. In the present 2. 1 Basic equation in bending study, since the applied load is small so as not to cause The analysis of the bending of a one-dimensional plastic deflection, it seems that the plastic strain rateε ˙ p is beam is in accordance with the following relation. Under equal to 0. the assumption of Euler-Bernoulli bending theories, strain The constitutive equation on transformation plasticity ε is given by is defined by Greenwood-Johnson’s relation(11) η ε = (1) ε˙tp = 2K (1−ξ)ξσ,˙ (10) R and strain rateε ˙ by where K is the transformation plasticity coefficient. Substituting each strain rate component [Eqs. (7) – R˙ ε˙ = − η, (2) (11)] into the total strain rate [Eq. (6)], we obtain R2 where R and η are the radius of curvature and the distance σ˙ = E{ε˙ −αT˙ −βξ˙ −2K(1−ξ)ξσ˙ }. (11) from a neutral plane, respectively. Under the assumption Since this stress rate should fulfill Eq. (5) at a given cross- that the slope of a beam is very small ( dy/dx 1), if the section, profile of deflection is defined by y = y(x) at a given time, we can approximate the radius of curvature using E{ε˙ −αT˙ −βξ˙ −2K(1−ξ)ξσ˙ }ηdA= 0. (12) A 2 1 = − d y If each material’s constant is independent of temperature 2 . (3) R dx and the position of the specimen, Eq. (12) becomes On the other hand, considering the equilibrium state of moment in a given cross-section, the bending moment εη˙ dA−α T˙ηdA−β ξη˙ dA A A A becomes − − = = 2K (1 ξ)ξση˙ dA 0. (13) M σηdA, (4) A A where A and M are the cross-sectional area of the beam In the experiment, it is assumed that the specimen is and the bending moment, respectively. Furthermore, when so small that the change in temperature occurs uniformly the applied load is constant, the bending moment rate be- across its cross-section during cooling, the transformation, therefore, occurs uniformly across the cross-section of the comes specimen. Then, the second and third terms of the above M˙ = ση˙ dA= 0. (5) equation become first-order moments around the neutral A plane, which are equal to 0. Meanwhile, if the speci- 2. 2 Constitutive equation of transformation plas- men, which is symmetric to the neutral plane, is cooled ticity uniformly from the upper and lower-surfaces despite the Let us consider the constitutive equation in uniaxial transformation occurring nonuniformly, it can be consid- stress problem in which only bending stress is applied. ered that the rate of change in temperature T˙ becomes an Here, the process in which the specimen is subjected to even function of the distance from the neutral plane η. elastic loading and then cooled under constant loading is Similarly considering that the rate of volume fraction ξ˙ discussed. In general, the total strain rateε ˙ is calculated by also becomes an even function of η, the second and third the sum of elasticity, plasticity, thermal expansion, trans- terms of Eq. (13) become 0. Finally, the equation of equi- formation expansion and transformation plasticity(5). librium for moment can be written as ε˙ = ε˙e +ε˙ p +ε˙T +ε˙ ph +ε˙tp (6) εη˙ dA−2K(1−ξ)ξ˙ σηdA= 0. (14) Here, elastic strain rate, thermal expansion strain rate and A A transformation plastic strain rate are respectively repre- 2. 3 Profile of deflection sented by In this section, the profile of deflection is considered σ˙ as follows: Assuming the deflection y, which is a function ε˙e = (7) E of the position x and the time t from loading (i.e., cooling ε˙T = αT˙ (8) start time), is written as ε˙ ph = βξ.˙ (9) y(x,t) = δ(t)g(x) (15) As an example, it is assumed that a type of trans- (the validity of this assumption is experimentally dis- formation from the austenite phase to the martensite phase cussed later), Series A, Vol. 48, No. 1, 2005 JSME International Journal 3 0 ≤ g(x) ≤ 1 (16) For a simply supported beam with a span of l sub- e jected to three-point bending, the applied load W at its δ ≤ δ(t) ≤ δmax, (17) center, a nondimensional function of the deflection g(x), where δe and δ are the maximum elastic deflection and max is expressed as final maximum deflection, respectively, and g(x) can be W x3 3 l2 considered a function of the dimensionless deflection in- = − − 1 − 1 − g(x) x x, (26) duced by the maximum deflection. Then we obtain E I 12 6 2 16 d2y d2g(x) where = δ(t) . (18) dx2 dx2 0ifx < 0 x = (27) Using Eq. (3), the radius of curvature can be expressed as x if x ≥ 0 1 d2g(x) ffi = −δ(t) (19) 2. 4 Transformation plasticity coe cient R dx2 Considering g(l/2) = 1 in Eq. (26), the transformation and in the derivative form as plasticity coefficient K can be expressed by 2 2 d 1 2 dδ d g(x) 48I 1 R˙ = −R = R . (20) K = δ − . (28) dt R dt dx2 Wl3 max E From Eqs. (19) and (20), the integration of the first terms That is, since the shape of the beam and the applied load in Eq.
Details
-
File Typepdf
-
Upload Time-
-
Content LanguagesEnglish
-
Upload UserAnonymous/Not logged-in
-
File Pages6 Page
-
File Size-