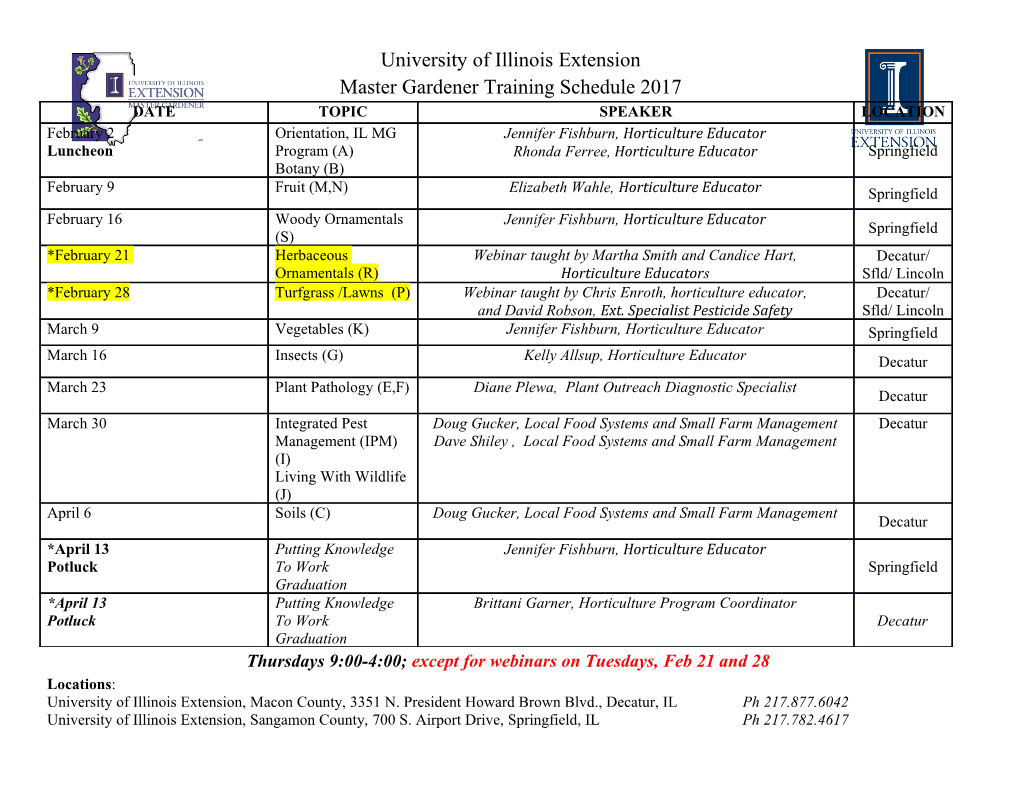
Journal of Alloys and Compounds 764 (2018) 582e590 Contents lists available at ScienceDirect Journal of Alloys and Compounds journal homepage: http://www.elsevier.com/locate/jalcom Diffusion bonding between TZM alloy and WRe alloy by spark plasma sintering * Zhi Yang a, 1,KeHua, c, 1, , Dawei Hu b, d, Cuiliu Han a, Yinggang Tong b, d, Xinyu Yang a, ** Fuzhi Wei b, d, Jiuxing Zhang a, , Yan Shen b, d, Jian Chen b, d, Xiaogang Wu a a School of Materials Science and Engineering, Hefei University of Technology, Hefei 230009, China b Beijing Institute of Control Engineering, Beijing 100190, China c National Engineering Research Center of Powder Metallurgy of Titanium & Rare Metals, Guangdong Institute of Materials and Processing, Guangzhou 510650, China d Beijing Engineering Research Center of Propulsion Technology, Beijing 100190, China article info abstract Article history: Successful solid-state diffusion bonding was achieved between TZM alloy and WRe alloy without in- Received 11 February 2018 terlayers using spark plasma sintering (SPS) in the temperature range of 1300e1600 C for 30 min. Both Received in revised form the TZM and WRe alloys recrystallized during the bonding process. There were no intermetallics, dis- 14 May 2018 continuities, microcracks, or pores, and sufficient diffusion occurred in the TZM/WRe joint bonded at Accepted 11 June 2018 1500 C for 30 min. The TZM/WRe joint bonded at 1500 C for 30 min exhibited excellent mechanical Available online 12 June 2018 properties (shear strength of 498 ± 32.5 MPa and tensile strength of 475 ± 19.8 MPa) and thermal shock performance. The fracture morphology after shear and tensile test was both characterized as mixed Keywords: Spark plasma sintering transgranular cleavage and intergranular rupture. The TZM/WRe joint (1500 C/30 min) was free from Diffusion cracks and maintained high strength after experiencing repeated thermal shock 1500 times, and this was Interfacial microstructure due to negligible residual thermal stresses and further diffusion in the TZM/WRe interface during the Mechanical property thermal shock process. Thermal shock © 2018 Elsevier B.V. All rights reserved. 1. Introduction [5e9]. However, effective utilization of WRe alloy (especially when the alloy contains a high Re content) is limited by its high cost and Titaniumezirconiumemolybdenum (TZM) alloy has been high density. Developing reliable techniques for joining WRe alloys widely used in aerospace fields in applications such as the exhaust to other metals (e.g., TZM alloy) is therefore indispensable for valve of torpedo engines, rocket nozzles, gas pipelines, and nozzle expanding the application of these alloys in the field of aerospace. inserts, because of its high melting point, large elastic modulus, Conventional diffusion bonding, fusion welding, and brazing are small thermal expansion coefficient, good thermal conductivity, commonly used to join refractory alloys [10e13]. However, these strong corrosion resistance, and excellent high-temperature me- methods have different limitations. Conventional diffusion bonding chanical properties [1e4]. Tungstenerhenium (WRe) alloy is requires high temperature and long dwell time, and it is thus both currently considered to be an important engineering material for time- and energy-consuming. In fusion welding, new alloys or ultra-high temperature structural applications because it has many coarse grains may form in the molten pool, where microcracks are favorable properties, such as high melting temperature, high prone to generate under a tensile stress, and this leads to lower recrystallization temperature, high strength, good plasticity, low tensile strength. During brazing, the melting point of the brazing vapor pressure, and low brittle-ductile transition temperature filler metal is lower than that of the parent materials. Hence, at elevated temperature, the mechanical properties of the brazing joint may not meet application requirements. Spark plasma sin- tering (SPS) is a new method for the rapid consolidation of powders * Corresponding author. School of Materials Science and Engineering, Hefei using strong, pulsed DC current flowing through powders or dies to University of Technology, Hefei 230009, China. ** Corresponding author. generate joule heat, and it is characterized by a rapid heating rate, E-mail addresses: [email protected] (K. Hu), [email protected] (J. Zhang). short sintering time, and low energy consumption [14e16]. In 1 Contributed equally to this work. https://doi.org/10.1016/j.jallcom.2018.06.111 0925-8388/© 2018 Elsevier B.V. All rights reserved. Z. Yang et al. / Journal of Alloys and Compounds 764 (2018) 582e590 583 À recent years, this method has been used to join metallic or ceramic 100 C$min 1. The TZM/WRe joints were cooled at a cooling rate of À materials/parts via atom diffusion on the bonding interface approximately 15 C$min 1 from the bonding temperature to [17e19]. Herein, we call it “SPS-assisted diffusion bonding” to 600 C; this was then followed by the furnace cooling to room distinguish it from conventional diffusion bonding. Compared with temperature. conventional diffusion bonding, an additional electric field is introduced during SPS-assisted diffusion bonding. Under the elec- 2.2. Performance evaluation and microstructure analysis tric field, the electrical migration effect can accelerate the atom diffusion rate [20,21], and this contributes to improving the per- Thermal shock performance of the TZM/WRe joint was evalu- À formance of joints. Although there are an increasing number of ated in vacuum (residual cell pressure 1.0  10 2 Pa) using a high papers related to SPS-assisted diffusion bonding of the same or frequency inductive localized heating system. The TZM/WRe joint dissimilar materials, there are few reports in the literature about was cyclically heat-treated at 1200 C for a duration of 5 min for À systematic studies on diffusion bonding of TZM and WRe alloys via 1500 cycles. The heating rate was approximately 500 C$min 1, and À the SPS method. In the present paper, TZM/WRe joints are suc- the cooling rate was approximately 50 C$min 1. Room tempera- cessfully diffusion-bonded using the SPS method. The effects of ture shear tests were performed with a specially designed jig using diffusion bonding temperature on the microstructure and perfor- a CMT5115 testing system. Test pieces with dimensions of 4L mance of TZM/WRe joints are studied in detail. mm  2W mm  3T mm (L, W, and T represent length, width, and thickness, respectively) were machined from the bonded alloys, À and a constant loading speed of 0.5 mm min 1 was used in the 2. Experimental procedure shear tests. Fig. 3 shows a schematic diagram of the shear test. Room temperature tensile tests were performed using a CMT5115 2.1. SPS-assisted diffusion bonding process À testing system under a constant loading speed of 0.5 mm min 1. Tensile specimens with a gauge of hexagonal cross-section were Extruded TZM and WRe alloys, provided by Advanced Tech- prepared using EDM. Fig. 4 shows photos of the tensile testing bars. nology & Materials Co., Ltd. (AT&M), were selected for this study. In both the tensile and shear tests, three samples were tested for The main chemical compositions of these two materials are shown each process. Tensile and shear fracture morphologies were in Table 1. Fig. 1 shows the microstructures of the as-received TZM examined using field-emission scanning electron microscopy (FE- and WRe alloys. The as-received WRe alloy has a fibrous micro- SEM, Sigma, Zeiss, Germany). The hardness (HV ) was evaluated on structure, and the TZM alloy has a microstructure composed of a 3 a Digital Vickers hardness tester (XHVT-50Z, Shanghai Shangcai large number of carbide particles that are dispersed homoge- Tester Machine Co. Ltd., China) with a load of 3.0 kgf. neously in deformed grains. From both the TZM and WRe alloys, Cross-sections of the TZM/WRe joints before and after thermal work pieces were machined (via electrical discharge machining shock were cut perpendicularly and prepared via mechanical pol- (EDM)) into a cylindrical shape with dimensions of ishing and chemical etching for metallographic examination. The Ø11 mm  33 mm along the extrusion direction. Prior to diffusion etching agent was prepared by mixing a concentration of 25% bonding, the bonding surfaces of the work pieces were ground and ammonia water with a concentration of 30% hydrogen peroxide polished to produce a surface roughness (R ) that was lower than a solution in a ratio of 1:1. The microstructure was observed using FE- 0.05 mm. The work pieces were then cleaned with acetone in an SEM. Chemical composition and elemental intensity profiles of the ultrasonic bath for 10 min and then air-dried. chemical species (W, Mo, and Re) across the bonding interface were The TZM alloy and WRe alloy work pieces were assembled analyzed using energy dispersive X-ray spectrometry (EDS) following a top-to-bottom stacking sequence in a graphite die with attached to FE-SEM. The diffusion distances of W, Mo, and Re across an inner-diameter of 11.4 mm, and the work pieces were diffusion- the bonding interface were then determined on the basis of the EDS bonded via SPS (LaboxTM-300, Sinter Land Inc., Japan). Graphite profiles, and the final measurement results were each the average foils with a thickness of 0.2 mm were placed between the punches of ten tested values taken from different areas. and work pieces and between the die and work pieces for easy removal and for a significant reduction in temperature in- 3. Result and discussion homogeneity. In addition, the exterior of the die was covered with a porous graphite felt (thickness of ~5 mm), which was used as a 3.1. Microstructural and morphological analysis thermal insulator to reduce radiation loss and a possible temper- ature gradient [22]. A schematic diagram of the graphite die-work Successful solid-state diffusion bonding was achieved between pieces-punches assembly is shown in Fig.
Details
-
File Typepdf
-
Upload Time-
-
Content LanguagesEnglish
-
Upload UserAnonymous/Not logged-in
-
File Pages9 Page
-
File Size-