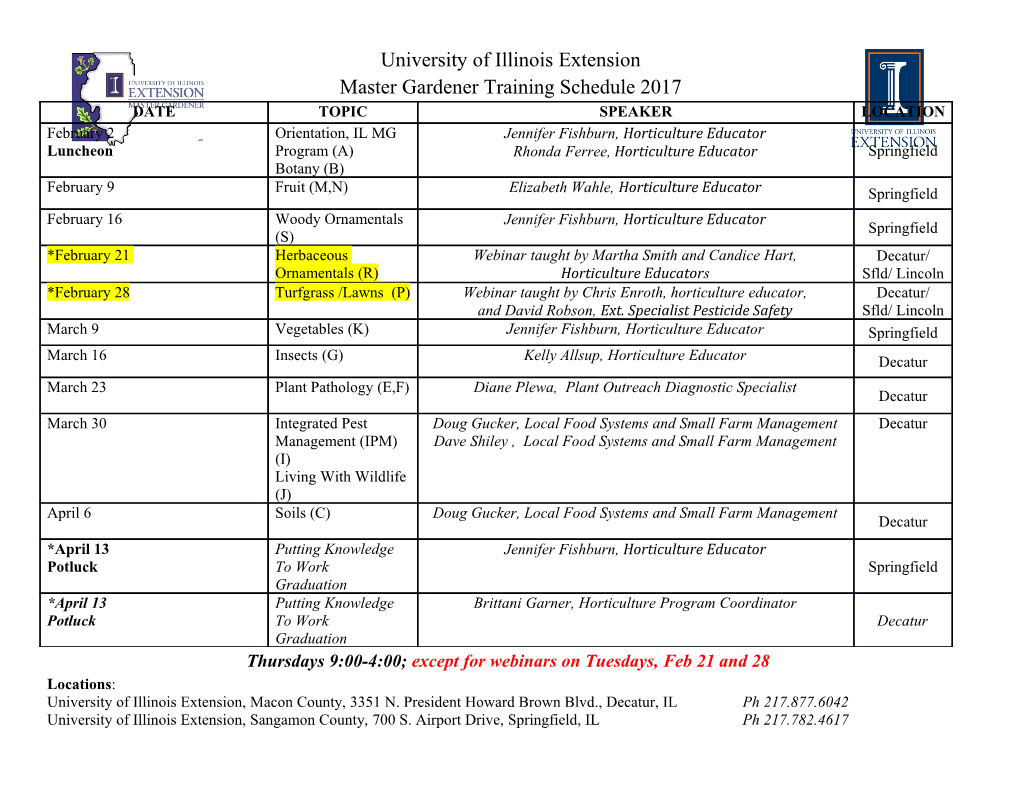
Copper Alloys in Seawater: Avoidance of Corrosion Copper Alloys in Seawater: Avoidance of Corrosion Roger Francis Copper Development Association Publication No 225 February 2016 About the Author Roger Francis has been a corrosion engineer for over 35 years and, for a significant amount of that time, has been involved in investigations and research into copper alloys. This has covered a wide range of environments but over half of the work has addressed performance in marine environments. He has been a chair of the Marine Corrosion Forum, a Director of NACE International, and has been a UK representative on the European Federation of Corrosion Working Party 9 (Marine Corrosion). Acknowledgements: Copper Development Association would like to acknowledge the assistance of Chris Dilnot, John Galsworthy, Christos Kapsalis, Maik Macziek, Carol Powell, Bernd Sagebiel, Ladji Tikana and Steven Van Hoose in the production of this publication. Copper Development Association is a non-trading organisation that promotes and supports the use of copper based on its superior technical performance and its contribution to a higher quality of life. Its services, which include the provision of technical advice and information, are available to those interested in the utilisation of copper and copper alloys in all their aspects. The Association also provides a link between research and the user industries and is part of an international network of trade associations, the Copper Alliance™. Disclaimer Whilst this document has been prepared with care, we can give no warranty regarding the contents and shall not be liable for any direct, incidental or consequential damage arising out of its use. For complete information on any material, the appropriate standard should be consulted. Copyright © 2016. Copper Development Association Cover page image: Copper-nickel fittings for a seawater piping system (©KME Germany) 2 | COPPER ALLOYS IN SEAWATER: AVOIDANCE OF CORROSION Contents Tables and Figures Summary ............................................................ 4 Tables 1.0 Alloys ........................................................5 Table 1 Nominal Composition of Copper Alloys Discussed in the Guide ......................................................5 2.0 Information .............................................6 Table 2 Safe Velocities for Copper-nickel Tube and Pipe ...7 Table 3 Maximum Weld Bead Protrusion for Copper-nickel Piping ..........................................................7 3.0 Velocity ....................................................7 Table 4 Recommended Safe Chlorine Dosing for some Copper Alloys ......................................................................13 4.0 Temperature ..........................................10 Table 5 Alloy Groupings for Galvanic Corrosion in Seawater at Ambient Temperature.............................14 5.0 Pollutants ...............................................11 Figures 5.1 Sulphide .................................................................................11 5.2 Ammonia ...............................................................................12 Figure 1 90/10 copper-nickel piping on a marine chemical tanker ....................................................................4 6.0 Fouling and Chlorination .................... 13 Figure 2 90/10 copper-nickel tubing in an oil cooler .............4 Figure 3 Erosion corrosion of 90/10 copper-nickel 7.0 Coupling to Other Alloys ..................... 14 after the weld on a weld neck flange due to excessive flow velocity ......................................................8 8.0 Start-up ................................................ 15 Figure 4 Diagram showing syphonic air release .......................9 Figure 5 Severe erosion corrosion of 25.4 mm od 66/30/2/2 Cu-Ni-Fe-Mn in a dump condenser 9.0 Quality .................................................. 16 due to syphonic air release ..............................................9 9.1 90/10 Copper-nickel .........................................................16 Figure 6 Pitting attack of 90/10 copper-nickel due to 9.2 Nickel Aluminium Bronze ...............................................16 sulphide in the seawater ................................................11 9.3 Heat Exchanger Tubing ...................................................16 Figure 7 Ammonia induced attack of 90/10 copper-nickel heat exchanger tube ...........................12 Figure 8 Erosion corrosion of a scratch on an 10.0 Conclusion ............................................ 17 aluminium brass condenser tube due to excessive chlorination .....................................................13 11.0 References ............................................ 17 Figure 9 Effect of chlorine on the corrosion of a 90/10 copper-nickel pipe coupled to one of 6% Mo austenitic stainless steel ...........................14 12.0 Appendix ............................................... 18 Figure 10 Corrosion of nickel aluminium bronze pipe 12.1 Ferrous Sulphate Dosing ................................................18 along seam weld due to residual beta-phase ........16 12.1.1 Role of Ferrous Sulphate .............................18 12.1.2 Dosing Practice ................................................18 12.2 Appendix References ........................................................18 COPPER ALLOYS IN SEAWATER: AVOIDANCE OF CORROSION | 3 Summary Copper alloys have been widely used in seawater and related brines, such as in thermal desalination plants, for many years, generally with excellent results. They are commonly used for piping, valves, pumps and heat exchanger tubing, but have found many other applications. Figure 1 shows copper-nickel piping on a chemical tanker, while Figure 2 shows copper-nickel tubing in an oil cooler. Such oil coolers have been in use for 10 to 15 years without problems. Figure 1 - 90/10 copper-nickel piping on a marine chemical tanker (Courtesy of Eucaro Buntmetall) Figure 2 - 90/10 copper-nickel tubing in an oil cooler Occasionally there are failures due to corrosion, and in many cases these could be avoided by following some simple design recommendations, by selecting an alternative copper alloy, or by using a simple preventative strategy. This document covers the most common types of corrosion and shows simple methods to avoid them. If these are implemented at the design stage, it can save a large expenditure after a corrosion failure. This guide has been written principally for marine, mechanical and other engineers who have to select materials of construction but do not have a corrosion background. 4 | COPPER ALLOYS IN SEAWATER: AVOIDANCE OF CORROSION 1.0 Alloys The most commonly used copper alloys in seawater are copper-nickel alloys and nickel aluminium bronzes (NAB). The former are mainly used for piping, fittings and heat exchanger tubing, while NAB are commonly used for pumps and valves, although they can be used for other components, such as propellers and fasteners, where higher strength is required. Other alloys are sometimes used in seawater, such as aluminium brass, the tin bronzes and the gunmetals. However, their use is more limited, although they have some applications and they are discussed at relevant places in the text. The nominal compositions of all the alloys discussed in the text are shown in Table 1. The compositions and mechanical properties are described in more detail in reference (1) and the effects of composition on corrosion are discussed in references (2) and (3). The alloys will mostly be referred to by the common names listed in Table 1. Table 1 - Nominal Composition of Copper Alloys Discussed in the Guide Type EN No Common Name Nominal Composition (wt %) (UNS No) Cu Ni Fe Mn Al Zn Sn Pb Other Wrought CW352H (C70600) 90/10 Copper-nickel Rem 10 1.7 1 CW354H (C71500) 70/30 Copper-nickel Rem 30 0.7 0.7 CW353H (C71640) 66/30/2/2 Cu-Ni-Fe-Mn Rem 30 2 2 CW702R (C68700) Aluminium Brass 78 2 Rem 0.4 As CW712R (C46400) Naval Brass 61 Rem 1 CW307G (C63200) Nickel Aluminium Bronze Rem 4.5 4 9 Cast CC333G (C95800) Nickel Aluminium Bronze Rem 4.5 4 9 CC482K (C92400) Admiralty Gunmetal Rem 2 10 1.5 CC480K (C90700) Phosphor Bronze Rem 10 0.2 P CC491K (C83600) G2 Gunmetal Rem 5 5 5 CC492K (C92410) LG4 Gunmetal Rem 2 7 3 Rem = Remainder COPPER ALLOYS IN SEAWATER: AVOIDANCE OF CORROSION | 5 2.0 Information When designing any component or system that will be in contact with seawater, or brine, it is important to obtain information about the conditions, which will help in selecting the best alloy and any corrosion preventative measures that may be advisable. The information required when using copper alloys is described below. • Composition: The water composition is not required in detail. Copper alloys have been used successfully over a wide range of chloride concentrations from 1,000 mg/L or less to 50,000 mg/L (in MSF [multi-stage flash] desalination plants). The pH is important and copper alloys are best used in the range 6.5 to 9.1. The pH of seawater is typically in the range 7.8 to 8.2, but incursions of freshwater or chemical additions may drive the pH to unacceptably low values. • Temperature: The corrosion of copper alloys is not affected much by temperature and they have been used in seawater from 0 to 70°C. They have also been used to 110°C for brine heater tubes in MSF desalination plants (3). • Solids: If there are suspended solids in the seawater, the corrosion rate of all copper alloys can be increased. In general, the metal loss increases
Details
-
File Typepdf
-
Upload Time-
-
Content LanguagesEnglish
-
Upload UserAnonymous/Not logged-in
-
File Pages20 Page
-
File Size-