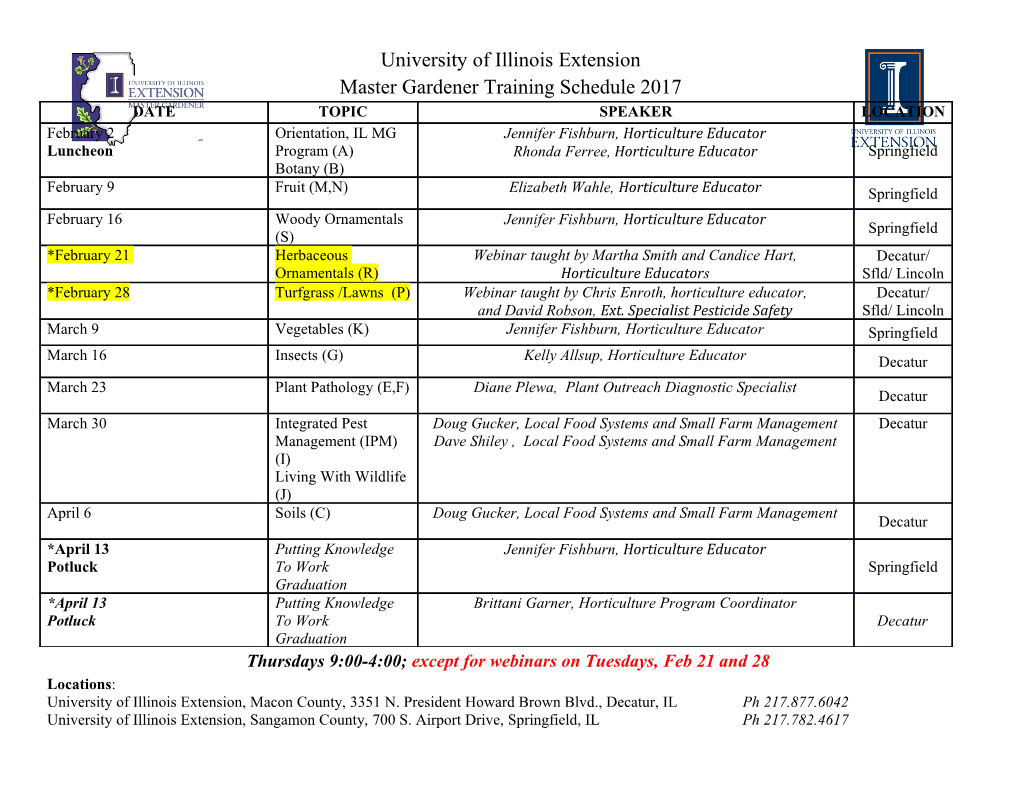
From: AAAI Technical Report SS-94-04. Compilation copyright © 1994, AAAI (www.aaai.org). All rights reserved. System Reliability and Risk Assessment: A Quantitative Extension of IDEF Methodologies AndrewKusiak, Intelligent Systems Laboratory, Departmentof Industrial Engineering Nick Larson, Intelligent SystemsLaboratory, Deparlmentof Industrial Engineering The University of Iowa, Iowa City, Iowa 52242-1527 1. Introduction for information analysis (IDEF1), dynamic analysis Evaluating system reliability requires modeling the (IDEF2), and process modeling (IDEF3). interaction of resources, information, and material within This paper presents procedures for integrating system the system. Such a model must consider quantitative data reliability and risk assessment techniques with IDEF0and describing the reliability of each element of the system, as IDEF~modeling. The paper is motivated by the need to well as logical data describing the relationship between increase the value of IDEF0 and IDEF3 models by individual components. For example, a manufacturing incorporating quantitative data, thus, extending model use system may assemble products X, Y, and Z, on machines to applications such as risk assessment. By extending the M1, M2, and M3, respectively, and package the products power of existing IDEF models, process modeling will on a fourth machine, M4. Therefore, three different become more attractive to managementand evolve as a relationships exist between the componentsof the system, powerful tool for reengineering design and manufacturing one for each product. If the reliability of each machine systems. differs, the system reliability will differ dependingon the product. Similarly, the reliability of the system as a whole 2. Definitions of System Reliability and Risk will be affected by the production levels of products X, Y, Assessment and Z. Reliability maybe defined as the ability of an item Given the example above, with only three products and (product, system, etc.) to operate under designated operating four machines, it becomes apparent that determining conditions for a designated period of time or number of systemreliability requires a significant amountof data and cycles (Modarres, 1993). An item’s reliability is often a structured modeling methodology. Furthermore, to measuredby the probability it will perform without failure obtain an accurate assessment of system reliability, it is given a set of conditions. The following expression is a necessary to include additional data describing information probabilistic representationfor reliability. and material componentsof the system; such as inspection procedures, assembly specifications, parts, and R(t) = P(T > tlc~, c2, ...) (1) subassemblies. Systemreliability describes the likelihood of success or failure in the operation of a system. Risk assessmentis In (1), t is the period of time for the item’s operation, a technique for identifying scenarios that lead to problems T is the time to failure of the item, R(t) is the reliability of in a system, determining the likelihood of each scenario, the item, and Cl,C2 .... are the conditions under whichthe and the evaluating the consequenceof each scenario, i.e., item is operating. Thevariable t is often referred to as the the problem. Although quantitative approaches to risk mission time. In practice, T is a random variable assessmentemploy the principles of system reliability, the representing the time-to-failure of the item, and Cl,C2 .... identification, quantification, and evaluation of risk is a are implicitly considered. Furthermore, fit) mayrepresent more comprehensive modeling activity. Therefore, risk the probability density function of the randomvariable T. assessmentprojects are well suited for the tools developed The probability that the item fails prior to time t is defined for process modelingand analysis. in (2). In 1978, the United States Air Force selected SADT (Structured Analysis and DesignTechnique) as the language to support the Integrated Computer Aided Manufacturing P(T < t) = I~ f( O)dO = F(t), for t>0 (2) (ICAM) program. SADTactivity modeling was adopted by the ICAMprogram and revised by Sofrech, Inc. to Since F(t) denotes the probability the item will fail develop the ICAMDefinition Methodology (IDEF0). prior to time t, it is formally the unreliability of the item. Ross (1985) states that "thousands of people from hundreds Thus, the reliability of the item is determinedby (3). of organizations working on more than one hundred major projects" proceeded to use the methodology for system definition and design, as well as project management. R(t) = 1- F(t)= It’f(O)dO (3) IDEF0introduced manufacturing to techniques that were developed for computer system and software engineering A system is a collection of entities (i.e., information applications. Additional IDEFtechniques were developed and material) and resources (i.e., machines and workers) 88 whichinteract to performa set of activities in a given techniques for determining system reliability and process. Successfulcompletion of the process is dependent integrating risk assessment and IDEFmodels. Section 5 uponproper completionof the individual activities in the discusses issues related to risk assessment, such as process. Therefore, it is necessary to model the developing quantitative risk modelsbased on IDEF0and relationship betweenvarious items (entities and resources), IDEF3. as well as the reliability of individualitems to assess the reliability of the system. Complexmanufacturing systems 3. Fundamentals of IDEF0 and IDEF3 producemany different products through manydifferent IDEF0was developedfor modelinga wide variety of sequences of manufacturing activities. The system systems which use hardware, software, and people to reliability is a function of the activities performedand, perform activities (U. S. Air Force, 1981). An IDEF0 thus, is product dependent.Therefore, if the production modelconsists of three components,diagrams, text, and a volumeof a product exhibiting low systemreliability is glossary, all cross-referencedto each other. Thebox and increased,the reliability of the entire manufacturingsystem arrow diagramsare the major componentsof the model. In will decrease. At this point, the necessity for evaluating a diagram, a box represents a function and an arrow system reliability in a manufacturingsetting becomes represents an interface. A box is assigned an active verb obvious. phrase to represent the function. Aninterface maybe an Manyof the commontechniques for modelingsystem input, an output, a control, or a mechanism,and is reliability are difficult to applyto complexmanufacturing assigneda descriptivenoun phrase. Inputs (I) enter the box systems with multiple product types. Therefore, the fromthe left, are transformedby the function, and exit the principles of such tools are moreuseful whenapplied to boxto the right as an output(O). A control (C) enters modelingschemes developed for manufacturingsystems, top of the box and influences or determinesthe function such as IDEF0and IDEF3.Also, the task of evaluating performed. A mechanism(M) is a tool or resource which system reliability in a manufacturingsetting is more performsthe function. Theinterfaces are generallyreferred attractive if performedas a componentof a risk assessment to as the ICOMs(see Figure 1). study. Risk is a measureof the probability and severity of adverse effects (Lowrance,1976). Several types of risk Control (C) associated with project planningand software development have been cited in the literature, see Angand Gay(1993) and Chittister and Haimes (1993). The following manufacturingrisks are generalized from those cited in variousengineering disciplines. Input(I) Output (0) 1. Requirementsrisk. Theconcept of whatthe FUNCTION productis intendedto accomplishis not accurate. 2. Technicalrisk. Theproduct does not adhereto the requirementsset forth by its design. 3. Schedulerisk. Theproduct will not be completed by the deadlineset forth by productionplanning. 4. Costrisk. Theproduction cost will overrunits budget. Mechansim(M) 5. Networkrisk. The mechanismfor linking various productionactivities will not performas intended. Figure 1. IDEF0function box and interface arrows Risk assessmentis a process that attempts to answer three questions: (1) Whatcan go wrong?(2) Whatis Eachdiagram has betweenthree and six function boxes likelihood that it will go wrong? (3) What are the placed on a diagonal. Theboxes each have a specific node consequences?(Kaplan and Garrick, 1981). Basedon these numberand are connectedby all relevant interfaces. Each questions,(4) is a quantitativedefinition of risk, whereSi box on the diagrammay be decomposedinto a lower level is a scenario of eventsthat leads to a problem,Pi is the of detail. This feature restricts the amountof information that maybe containedin the modelon a single level. The likelihood of scenario i, and Ci is the consequenceof resulting diagramsform a hierarchy of informationwhich scenarioi. is summarizedin a nodetree. IDEF0provides a structured representation of the R = {Si, Pi, C~} i =1, 2 ..... n (4) functions,information, and objects whichare interrelated in a manufacturingsystem. IDEF3was created specifically to This section has provided definitions of system model the sequence of activities performed in a reliability and risk assessment. Section 4 discusses manufacturingsystem. AnIDEF3 model enables an expert 89 Reject proposal Evaluate Negotiate Award contract Accept Figure 2. IDEF3process flow diagram(Mayer et
Details
-
File Typepdf
-
Upload Time-
-
Content LanguagesEnglish
-
Upload UserAnonymous/Not logged-in
-
File Pages6 Page
-
File Size-