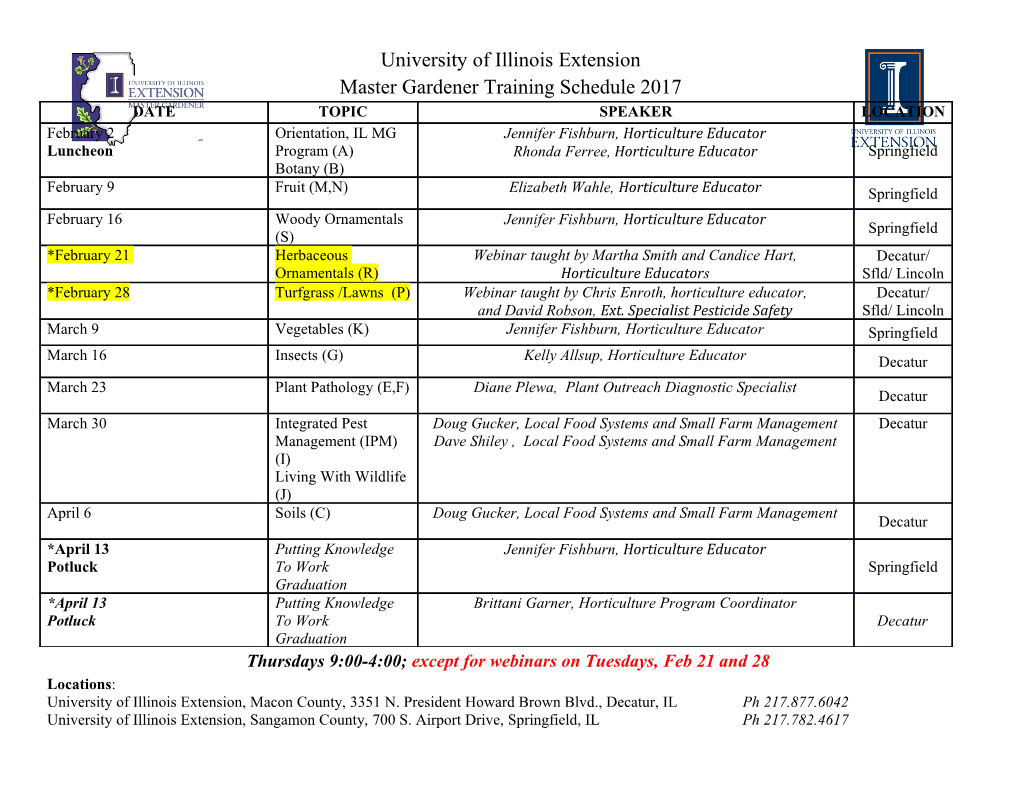
NOVYI MIR Research Journal ISSN No:0130-7673 An Experimental Investigationof Etching Depthfor Photochemical Machining of Brass Avinash D. Sapkal1, Abhay A. Utpat2Bandu Kamble3 1M. Tech student 2 Professor3 Research Scholar SVERI’s College of Engineering, Pandharpur [email protected], [email protected],[email protected] ABSTRACT Photochemical machining (PCM) is a process used to fabricate sheet metal components using a photoresist and etchants to corrosively machine away selected areas. It is one of the least well known and important non-conventional process. Un-conventional machining processes have extensively been used in the manufacture of geometrically complex machine components from engineering material which are not possibly or economically shaped by conventional machining process. This paper focuses on parametric optimization for photochemical machining (PCM) of brass. The control parameters have been selected as etching temperature, and etching time. PCM has been carried out using ferric chloride as etchant. Surface roughness and edge deviation should be less, while etching depth is desired high. The aim of the study is to analyze the effect of control parameters on response measures, that is, surface roughness, etching depth and optimization of parameters considering different weight percentage for each performance measure. For satisfying this multi-objective condition, overall evaluation criteria (OEC) have been used by assigning different and equal weight percentage to response measures. Keywords -Photo Chemical Machining, Photo tool, etching, Varying etching parameters, overall evaluation criteria (OEC). 1. INTRODUCTION The photo chemical machining process goes by many names, including photo chemical machining, photo chemical etching, chemical milling, chemical etching, photo etching, even the abbreviation “PCM.” All of these names describe the same process. The PCM industry currently plays a vital role in the production of a variety of precision parts viz. micro fluidic channels, silicon integrated circuits, copper printed circuit boards and decorative items. The efforts carried out by earlier authors in respect of Photochemical Machining are explained in next paragraphs. Diehard kapp-schwoerer et al. [1] gave the effect of liquid type photoresist for photochemical machining.in this article different photoresist types will be described, and he focuses on liquid photo imageable etch resists to produce functional or decorative metal parts. David M. Allen et al. [2] gave the PCM as the state of art, the PCM roadmap and its examples. This paper examines newly-developed products made by PCM especially relevant to Micro engineering, Micro fluidics and Microsystem Technology, economically aspects and current challenges requiring research within the PCM industry. Andrew R. Barron et.al. [3] focused on the chemical compositions or constituents and photochemical mechanics of photoresist materials. The idea about positive and negative type photoresist composition and its reactions with UV light is explained. Also given the comparison between positive photoresist and negative photoresist. S. S. Wangikar .[4] parametric optimization for photochemical machining Volume 5, Issue 9, 2020 Page No: 1 NOVYI MIR Research Journal ISSN No:0130-7673 (PCM) of brass and german silver. Two-dimensional simulation model of etching was developed, and the experimental analysis of the process parameters on micro-geometry was investigated Photochemical machining (PCM) is one of the commonly used non-traditional machining processes in which the photographic and chemical etching techniques are employed. The process starts by printing the shape of the part onto optically clear and dimensionally stable photographic film. The "photo tool" consists of two sheets of this film showing negative images of the parts (meaning that the area that will become the parts is clear and all of the areas to be etched are black). The two sheets are optically and mechanically registered to form the top and bottom halves of the tool. PCM is also known as etching, photochemical machining, wet etching, photo etching, photochemical milling etc. The process is start with by creating required design called as photo tool in AutoCAD software and printed it on transparent sheet of plastic for etching.N. D. Misal[5] The photoresist is applied on metal surfaces. The design is kept in photoresist and exposed it by using high intensity ultraviolet light. The pattern is transferred on photoresist and It will be visible after development. The manufacturing process creates features by dissolving away the metal parts in etching process. There is no use of cutting tool for manufacturing of components, due to this the stresses and other defects normally arises from metal cutting is absent in the final part of PCM. The major steps involved on PCM is given below Preparation of phototool Selection of basemetal Preparation of workpiece Photoresistcoating Developing Etching Stripping andinspection N. D. Misal [6] In PCM depth can be achieved by less and more exposing of samples. The less and more intensity of light will be got by passing light in photo tool. The photo tool is made up by printing different on a transparent sheet or stress paper. the light passing through photo tool. The light coming out from different is depending on the characteristic of photo tool. A. R. Saraf [7] The energy content of light is varying with colour by colour, which results in less and more harden of photoresist material. the etching process is mainly depending on a development of photoresist material. Less developing results in less etching and more developing results in more etching. Kamble, B [8]The application of PCM has widely been used in the manufacturing of thin, flat and complex metal parts (i.e. lead frames, colour TV masks, sensors, heat plates, printed circuit boards) in electronics, precision engineering and decorative industries in the past forty years. Now a days PCM industry plays important role in production of varieties of precision parts, decorative components and to develop microfluidic channels, microfilters, copper printed circuit boards etc. Misal, N. D[9] gave use of grey-based Taguchi method for optimization of the PCM process parameters in etching with consideration of multiple output parameters is reported. In this new approach, the grey relational analysis is adopted to solve the PCM process. A grey relation grade obtained from the grey relational analysis is used as the performance characteristic. The optimal Volume 5, Issue 9, 2020 Page No: 2 NOVYI MIR Research Journal ISSN No:0130-7673 process parameter is determined by using parameter design proposed by the Design of Experiment.Abhay A. Utpat [10] gave the study of Depth of etching in photochemical machining byvarying temperatureand timeof etching. The objective was to study theeffect ofthese parameters and find relation between them. Further various researchers have reported photochemical machining for fabrication of microchannels, heat sinks, grooved textures in bearings and characterization of various materials [11-18]. The photoresist used PCM has two types given below. Positivephotoresist Negativephotoresist In negative photoresist part which is dark in photo-tool is removed and remaining part of photo-tool become hard and in positive photoresist inversely like negative photoresist the part which is dark is remain hard and other part will become softer and that non harden part is removed. Fig.1 Types of photoresist 2. METHODOLOGY 2.1 Materialselection The material used for this study is a brass, because it is more elastic than copper and Aluminumand have to study on machining parameters of Brass. The size of specimen used is 40 mm x40 mm x1.5mm (W×L×T). PCM was carried out for flat surfaces of Brass, then it did for objects of Brass.Fecl3 is used as etchant and negative photoresist for experiments. 2.2 Experimentalprocedure 2.2.1 CreatingPhoto tool Photochemical machining process is carried out by using a photo tool. The photo tool is an AutoCAD drawing with detailed dimensions of the required shape which is then printed on a tress paper or transparentpaper Fig.2 Photo toolinAutoCAD Volume 5, Issue 9, 2020 Page No: 3 NOVYI MIR Research Journal ISSN No:0130-7673 2.3 Preparation ofworkpiece. After preparing the photo tool the Stainless-steel material is cut into required size. The first task is to clean the workpiece. The cleaning of the surface is done firstly by polishing the surface with a sand paper and then cleaning it by thinner (trichloroethylene or acetone). This step is done to make the surface of workpiece free from foreign particles, debris, dust, grease, oil and other contaminants. Because of polishing and cleaning with thinner it gets easier to have a good adhesion of photoresist with the metalsurface. 2.4 Coating of workpiece. After cleaning the workpiece, a thin layer of photoresist is applied on the metal surface. The negative type photo resist was used for experimentation. The characteristic of negative photoresist is it get harden when UV light is incident on it. The properties of negative photoresist for different colors is different, it depends on the energy content of light coming out from colored phototool. Fig.3 Photoresist and Developing Solution 2.5 UV Exposure. In three-dimensional photochemical Machining, it is necessary to expose material (base metal) in all directions, the etching can be takes place in all directions. The 2D Exposure machine is designed in such a way that in can expose the specimen in all direction. The 1 KW power UV light bulb is used for exposing the sample. It radiates the intensity 1800 microwatt per centimeter square at 25 cm distance. In traditional machining i.e. in 2D PCM process the samples are exposed in only one direction. The generated photo tool is put on the coated workpiece and exposed to UV source for 90seconds. Fig.4 Exposure machine Volume 5, Issue 9, 2020 Page No: 4 NOVYI MIR Research Journal ISSN No:0130-7673 2.1DevelopmentPhase. The developing solution is the mixture of sodium carbonate and water. After UV exposure the specimen is held in the developer for 90 seconds, which results in the formation of impression on workpiece.
Details
-
File Typepdf
-
Upload Time-
-
Content LanguagesEnglish
-
Upload UserAnonymous/Not logged-in
-
File Pages9 Page
-
File Size-