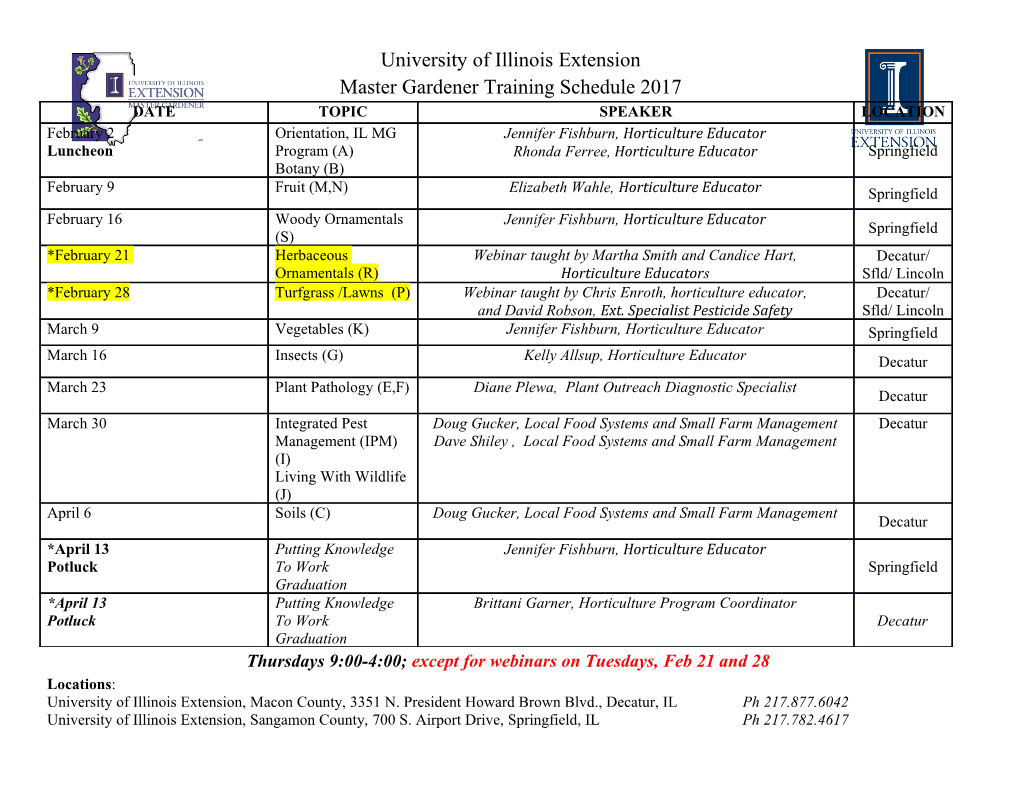
Performance Enhancement of Abrasive Waterjet Cutting Performance Enhancement of Abrasive Waterjet Cutting Proefschrift ter verkrijging van de graad van doctor aan de Technische Universiteit Delft, op gezag van de Rector Magnificus prof. dr. ir. J.T. Fokkema, voorzitter van het College voor Promoties, in het openbaar te verdedigen op maandag 19 mei 2008 om 10.00 uur door Vu Ngoc PI Master of Engineering Hanoi University of Technology, Vietnam Geboren te Thai Binh, Vietnam Dit proefschrift is goedgekeurd door de promotoren: Prof. Dr.-Ing. habil B. Karpuschewski toegevoegd promotor: dr. ir. A.M. Hoogstrate Samenstelling promotie commissie: Rector Magnificus voorzitter Prof. Dr.-Ing. habil B. Karpuschewski Otto-von-Guericke-Universität Magdeburg, promotor Dr. ir. A.M. Hoogstrate TNO Science and Industry, toegevoegd promotor Prof. dr. ir. J.R. Duflou Katholieke Universiteit Leuven Prof. Dr.-Ing. H. Louis Leibniz Universität Hannover Prof. dr. ir. A.J. Huis in ‘t Veld Universiteit Twente Prof. dr. U. Staufer Technische Universiteit Delft Prof. dr. M.A. Guitierrez De La Merced Technische Universiteit Delft, reservelid ISBN: 978-90-9023096-2 Printed by PrintPartners Ipskamp, Rotterdam, The Netherlands. Copyright © 2008 by Vu Ngoc Pi All rights reserved. No part of this publication may be reproduced, utilized or stored in any form or by any means, electronic or mechanical, including photocopying, recording or by any information storage and retrieval system, without permission from the copyright holder. iv Dedicated to my wife Hoang Thi Tham Acknowledgement First of all, I would like to express my deep and sincere gratitude to Prof. Dr.-Ing. habil. Bernhard Karpuschewski, my promoter, for his guidance, consideration, and critical review of the present thesis. I would like to give sincere appreciation to Dr. ir. André Hoogstrate, my adjunct supervisor, for his useful discussion, for his detailed and constructive comments, and for his important support throughout this work. Then I would like to express my special thanks to Dr. Mohamed Hashish (Flow International Cooperation), Dr. Jey Zeng (OMAX Corporation), Dr. Eric Chalmers (AccuStream Inc.), Dr. Greg Mort (KMT Waterjet Systems Inc.), Dr. Andreas Höfner (GMA Garnet (Europe) GmbH), and Prof. Deng Jianxin (Shandong University), for their discussions, documents, and encouragement. Furthermore I would like to thank Paolo Golfiotti, my Italian MSc student, for his helping in the abrasive recycling experiments. Not to forget I would like to record my gratitude to the staff members of the department of Precision and Microsystems Engineering, especially Associate Prof. Marcel Tichem, Dr. Sebastiaan Berendse, Harry Jansen and Marli Guffens, for their supports of my works. My work is a cooperation between the Delft University of Technology and the Vietnamese Government. The work is supported by Training Scientific and Technical Cadres in Institutions Overseas with the State Budget (Project 322) and the Management Centre for International Cooperation (CICAT). I would like to give my appreciation to all members of CICAT and 322, especially Dr. Paul Althuis, Veronique van der Varst, Willemijn van der Toorn, and Ngoc Lien, for their helps and encouragement. I would like to thank all my colleagues and friends in and outside TU Delft for their encouraging and helping. Very special thanks to Tolga Susuzlu for his help in my experimental work and to Dr. Thieu Quang Tuan and Jeroen Derkx for their review of my thesis. Also, thanks to Nguyen Thanh Hoan for his help by taking pictures of my experimental setup. Also I would like to give my appreciation to Prof. Nguyen Dang Binh, Associate Prof. Phan Quang The, Associate Prof. Nguyen Dang Hoe and Associate Prof. Vu Quy Dac from the Thai Nguyen University of Technology, for their support and encouragement. i Last but not least, I would like to thank my mother, my mother-in-law, my sister and brothers, for their love and their encouragement. Thanks to my nephew Vu Quang Dien for his help by designing the cover of my book. I would like to thank my wife, Hong Tham, for her love, patience, enormous support, review of my thesis, and finally for taking care of our children. I also would like to thank my daughters, Thu Trang and My Hanh, for their love and back up. Delft, May 2008, Vu Ngoc Pi ii Summary Abrasive Waterjet (AWJ) Machining is a recent non-traditional machining process. Major part of this technology is a very high-pressure beam of water and abrasives, which is used for machining. The typical water pressure ranges from 300 to 380 MPa and the typical beam diameter varies between 0.6 and 1.2 mm. This technology is widely used in industry for cutting difficult-to-machine- materials, milling slots, polishing hard materials, cleaning contaminated surfaces, etc. AWJ machining has many advantages, e.g. it can cut net-shape parts, no heat is generated during the cutting process, it is particularly environmentally friendly as it is clean and it does not create dust. Although AWJ machining has many advantages, a big disadvantage of this technology is its relatively high cutting cost. Consequently, the reduction of the machining cost and the increase of the profit rate are big challenges in AWJ technology. To reduce the total cutting cost as well as to increase the profit rate, this research focuses on performance enhancement of AWJ cutting with two possible solutions including optimization in the cutting process and abrasive recycling. The first solution to enhance the AWJ cutting performance is the optimization of the AWJ cutting process. As a precondition, it is necessary to have a cutting process model for optimization. In order to use that model for this purpose, several important requirements are given. The most important requirement for such a model is that it can describe the “optimum relation” between the optimum abrasive mass flow rate and the maximum depth of cut. To develop a cutting process model which can be used for the AWJ optimization, many available models have been analyzed. Since the most important requirement for a process model (see above) can be obtained from Hoogstrate’s model, an extension of this model is carried out. The extension model consists of three sub-models including pure waterjet model, abrasive waterjet model and abrasive-work material interaction model. The pure waterjet model enables to determine the energy transfer from pressurized water to the pure waterjet. The abrasive waterjet model is used to calculate the energy transfer from pure waterjet to the abrasive particles. The abrasive– work material interaction model is used to identify the relation between the work material characteristics, the abrasive characteristics and the cutting efficiency in the process of removing work material chips by using the kinetic energy of abrasive particles. The extension cutting process model is more accurate than the original one and it is capable to iii optimize AWJ systems. The influence of many process parameters such as the water pressure, the abrasive mass flow rate, the nozzle diameter, the abrasive particle diameter etc. have been taken into account. By modeling the work material coefficient, the extension model can be used for various work materials. Also, by giving a model for the abrasive material coefficient, the model can be applied for several most common abrasive types. Up to now, there has not been a model for the prediction of AWJ nozzle wear. Therefore, modeling the nozzle wear rate has been carried out and a model for the wear rate of nozzles made from composite carbide has been proposed. The model can be used in the optimization problems as well as in the calculation of the AWJ cutting regime. Based on the extension cutting process model, two types of optimization applications have been carried out. They are related to technical problems and economical problems. The optimization problems have been solved in order to determine the optimum exchange nozzle diameter and the optimum abrasive mass flow rate for getting different objectives including the maximum depth of cut (for technical problems), the minimum total cutting cost and the maximum profit rate (for the economical problems). From the results of these considerations, regression models for determining the optimum nozzle exchange diameter and the optimum abrasive mass flow rate for various objectives have been proposed. In AWJ machining, there are many cutting process parameters. Therefore, the ways to select other process parameters optimumly have also been investigated. The procedure for the determination of an optimum cutting regime then is given. The other solution to enhance the cutting performance is abrasive recycling. In the present study, GMA garnet, the most popular abrasives for blast cleaning and waterjet cutting, has been chosen for the investigation. The recycling of GMA abrasives has been investigated on both technical side and economical side. On the technical side, the reusability and the cutting performance of the recycled and recharged abrasives have been analysed. The influence of the recycled and recharged abrasives on the cutting quality was studied. Also, the optimum particle size of recycled and recharged abrasives for the maximum cutting performance has been detected. On the economical side, first, the prediction of the cost of recycled and recharged abrasives was done. Then, the economic comparisons for selecting abrasives have been carried out. In addition, the economics of cutting with recycled and recharged abrasives have been studied. Several suggestions for an abrasive recycling process which promises a more effective use of the grains have been proposed. By optimization in the cutting process and by abrasive recycling, the cutting performance can be increased, the total cutting cost can be reduced, and the profit rate can be enlarged considerably. Consequently, the performance of AWJ cutting can be enhanced significantly. iv Samenvatting Abrasief waterstraal snijden (AWS) is een recent, niet conventioneel verspaningsproces. Het is een technologie waarbij een waterstraal onder hoge druk, gemengd met abrasief, gebruikt wordt voor de verspaning van diverse materialen.
Details
-
File Typepdf
-
Upload Time-
-
Content LanguagesEnglish
-
Upload UserAnonymous/Not logged-in
-
File Pages209 Page
-
File Size-