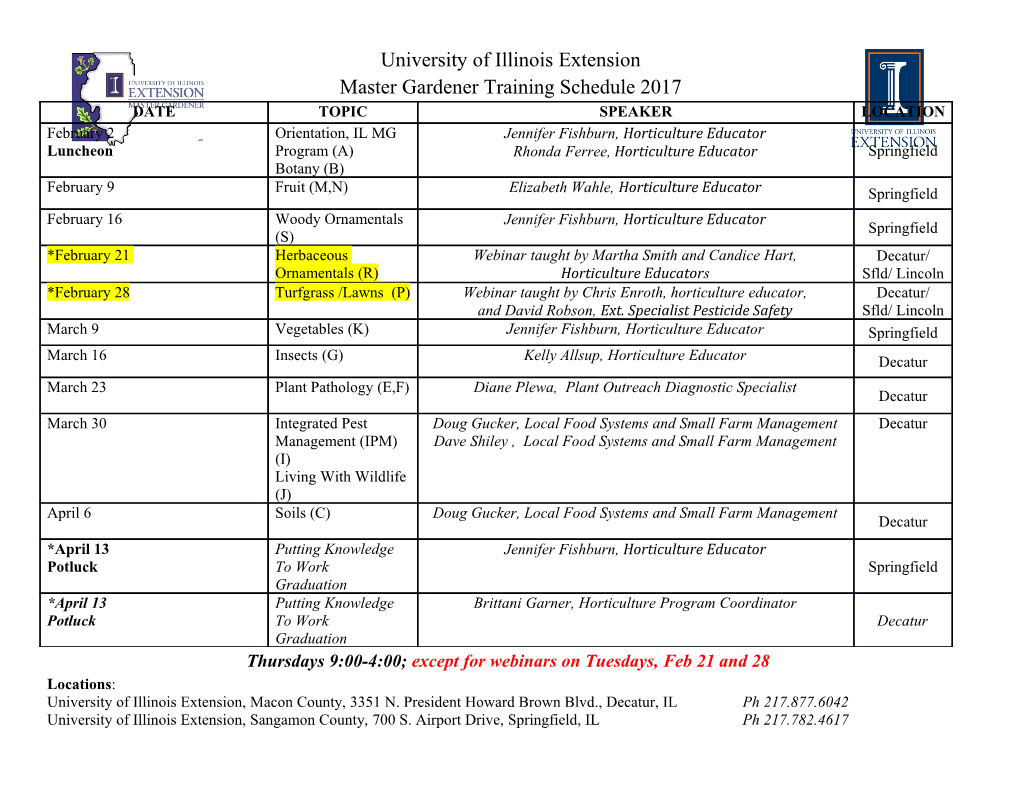
coatings Article Research on the Performance of Diamond-Like Carbon Coatings on Cutting Aluminum Alloy: Cutting Experiments and First-Principles Calculations Biao Huang 1, Er-geng Zhang 1,*, Qiong Zhou 1,*, Rong-chuan Lin 2 and Hao-ming Du 3 1 Shanghai Engineering Research Center of Physical Vapor Deposition (PVD) Superhard Coating and Equipment, Shanghai Institute of Technology, Shanghai 201418, China; [email protected] 2 School of Mechanical and Energy Engineering, Jimei University, Xiamen 361021, China; [email protected] 3 School of Materials Science and Engineering, Shanghai Dianji University, Shanghai 200240, China; [email protected] * Correspondence: [email protected] (E.-g.Z.); [email protected] (Q.Z.); Tel.: +86-21-60873356 (E.-g.Z. & Q.Z.) Abstract: The purpose of this study is to investigate the cutting performance of amorphous carbon (a-C) coatings and hydrogenated amorphous carbon (a-C:H) coatings on machining 2A50 aluminum alloy. First-principles molecular dynamics simulation was applied to investigate the effect of hydro- gen on the interaction between coatings and workpiece. The cross-section topography and internal structure of a-C and a-C:H films were characterized by field emission scanning electron microscopy and Raman spectroscopy. The surface roughness of the deposited films and processed workpiece were measured using a white light interferometer. The results show that the a-C-coated tool had the highest service life of 121 m and the best workpiece surface quality (Sq parameter of 0.23 µm) while the workpiece surface roughness Sq parameter was 0.35 and 0.52 µm when machined by the Citation: Huang, B.; Zhang, E.-g.; a-C:H-coated and the uncoated tool, respectively. Meanwhile, the build-up edge was observed on Zhou, Q.; Lin, R.-c.; Du, H.-m. the a-C:H-coated tool and a layer of aluminum alloy was observed to have adhered to the surface Research on the Performance of of the uncoated tool at its stable stage. An interface model that examined the interactions between Diamond-Like Carbon Coatings on H-terminated diamond (111)/Al(111) surfaces revealed that H atoms would move laterally with the Cutting Aluminum Alloy: Cutting action of cutting heat (549 K) and increase the interaction between a-C:H and Al surfaces; therefore, Experiments and First-Principles Al was prone to adhere to the a-C:H-coated tool surface. The a-C coating shows better performance Coatings 2021 11 Calculations. , , 63. on cutting aluminum alloy than the a-C:H coating. https://doi.org/10.3390/coatings 11010063 Keywords: amorphous carbon; hydrogenated amorphous carbon; coating; first-principles molecular dynamics; machinability; aluminum alloy Received: 22 December 2020 Accepted: 4 January 2021 Published: 7 January 2021 Publisher’s Note: MDPI stays neu- 1. Introduction tral with regard to jurisdictional clai- Lightweight materials such as aluminum alloys, of which the strength to weight ms in published maps and institutio- ratio is superior to that of steel, have been widely applied on automotive parts to reduce nal affiliations. their weight [1–4]. However, the surface roughness of aluminum alloy has a significant influence on the performance of mechanical parts as well as production cost [5]. With the increasing requirement for enterprises to reduce production costs, it is necessary to improve the processing quality of aluminum alloy to meet the higher demand for these Copyright: © 2021 by the authors. Li- censee MDPI, Basel, Switzerland. materials. The application of low friction and anti-adhesion coatings on cutting tools This article is an open access article for machining aluminum alloys is one of the most widely used strategies to achieve low distributed under the terms and con- surface roughness. ditions of the Creative Commons At- The deposition of coatings on cutting tools is becoming popular because they have tribution (CC BY) license (https:// shown excellent chemical inertness, anti-adhesion, friction resistance, and self-lubrication creativecommons.org/licenses/by/ properties. Hydrogenated amorphous carbon (a-C:H) is such a coating and has been used 4.0/). extensively to form low surface roughness [6]. However, the low thermostability of a-C:H Coatings 2021, 11, 63. https://doi.org/10.3390/coatings11010063 https://www.mdpi.com/journal/coatings Coatings 2021, 11, 63 2 of 11 coating is the main drawback for dry and high-speed cutting applications. Hydrogen atoms were desorbed from an a-C:H coating at about 300 ◦C in the studies by Robertson [7], Tallant et al. [8], and Pei et al. [9]; thus, the structure of an a-C:H coating changes above 300 ◦C. This is because the C–H bond vibrates violently and then breaks under the action of thermal radiation; hence, the coating loses its surface chemical inertness and the surface energy increases. Softy/lubricating coatings (ZrN + MoST, MoZrN + MoST, and CrTiAlN + MoST) are also used to improve the surface roughness in dry cutting [10,11]. However, few of them have practical application in dry cutting. Sugihara et al. [12] developed a cutting tool with a micro-stripe textured surface to ensure an excellent anti-adhesive property in both wet and dry cutting. Nizar et al. also proposed a technique to improve the anti-adhesion by controlling the micro-texture of the cutting tool [13]. The micro- texture could reduce the contact area during the cutting process and provide storage for the lubricant; therefore, the surface roughness could be reduced, but the costs would increase dramatically. Another way to improve the surface roughness of aluminum alloy is to add coolants to most cutting processes as a lubricant to reduce friction and help chip removal [14,15]. However, the use of coolants is harmful to the environment and human health. In recent years, numerous studies have addressed the tribological behavior of an amorphous carbon (a-C) coating against aluminum. A low coefficient of friction (≤0.16) and low wear rates of the a-C coating were observed against aluminum in an atmospheric environment and the a-C coating exhibited great lubricity as well [16–19]. Moreover, the thermal stability of the a-C coating was 450 ◦C, which was predicted by first-principles calculation in an oxygen atmosphere [7,20]. These studies show that the a-C coating’s thermal stability and tribological behavior against aluminum alloy are superior to that of the a-C:H coating. In light of these findings, the surface roughness of the workpiece and service life of the a-C coating tool, the a-C:H coating tool, and the uncoated tool when dry cutting aluminum alloy are compared in this paper. The work of adhesion and interaction energy between the cutting tool and aluminum surface was estimated by the first-principles calculation. The predictions of atomistic simulations at the interfaces were analyzed together with the results of the cutting experiments to elucidate the effect of hydrogen on the performance of carbon coatings against aluminum alloy surfaces. 2. Experimental Details 2.1. Multilayer Films Deposition The a-C film and a-C:H film were prepared on a cemented carbide milling tool (D8 × 75 mm2) and a YG10-grade cemented carbide (16 × 16 × 2.5 mm3) substrate. Before film deposition, a standard pretreatment must be followed to achieve good bonding performance. Initially, the substrates were sprayed with Al2O3 (220#–260#) under 1.5 Pa gas pressure for 2 min, then polished with a cotton wheel (3500 r/min) for 3 min, and cleaned using ethanol for 10 min and deionized water for 5 min. Later, the substrates were dried with nitrogen gas flow. The tungsten carbide samples were used to characterize the microstructures and thickness of the coatings. The a-C:H coatings were prepared by a C2H2 and Ar gas mixture in a plasma discharging system while the a-C coatings were prepared by applying the pulsed magnetron sputtering technique. In the a-C:H coatings deposition system, a single, high-purity (99.9%) titanium target was pre-sputtered for approximately 10 min to remove impurities and deposited onto the substrates for 15 min as an underlayer with a current of 120 A and bias of −80 V. Then, the Ti-C:H functional gradient layer was deposited with a Ti target current of 80 A and a C2H2 flow of 50 sccm for 10 min. Subsequently, the a-C:H layer was deposited with a C2H2 flow of 65 sccm for 30 min. In a pulsed magnetron sputtering system, one titanium target and one graphite target were used to prepare the a-C coating. High-purity argon gas with a flow rate of 35 sccm was supplied continuously to maintain the process pressure of 0.3 Pa. Firstly, the substrates were etched under the bias voltage of −500 V for 20 min, then the surface was activated Coatings 2021, 11, 63 3 of 11 and the oxide layer on the surface was removed. Secondly, the Ti underlayer was deposited onto the substrates with the Ti target frequency of 15 Hz and a current of 3.1 A for 20 min. Thirdly, the Ti-C layer was deposited with a Ti target current of 3.1 A and a graphite target current of 1.2 A. This process continued for 6 min and the frequency of Ti/graphite was 15 Hz. Subsequently, the amorphous carbon layer was deposited by sputtering one graphite target at the same frequency of 15 Hz for 60 min with a current of 1.2 A. 2.2. Characterization Techniques The thickness of films was analyzed using a field emission scanning electron micro- scope (FE-SEM) (FEI inspect f50, Thermo Fisher Scientific, Hillsboro, OR, USA). The surface morphologies of films and workpieces were evaluated by a white-light interferometer (Contour GT-K0, Bruker, Billerica, MA, USA), and the measurement was carried out at room temperature (22 ± 3 ◦C) and 35–50% RH.
Details
-
File Typepdf
-
Upload Time-
-
Content LanguagesEnglish
-
Upload UserAnonymous/Not logged-in
-
File Pages11 Page
-
File Size-