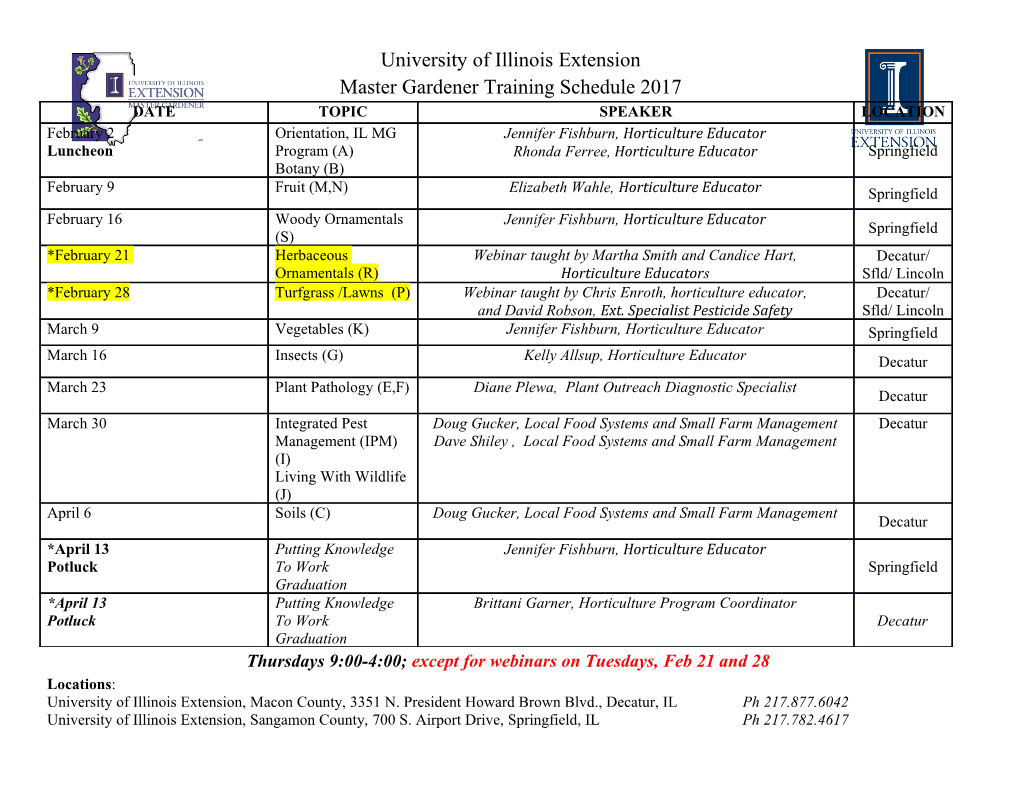
.- LEXINGTON LABORATORIES, INC. Cambridge e Mass. 02140 DEVELOPMENT OF PIGMENTS FOR THERMAL CONTROL COATINGS by Philip S. Schaffer - Lexington Laboratories, Inc. David W. Jones - Lexington Laboratories, Inc. GPO PRICE $ Contract Number NAS8-20162 CFSTI PRICE(S) $ (908-20-02-0147) Hard copy (HC) 5 m Microfiche (MF) /< 5% ff 653 July 65 George C. Marshall Space Flight Center National Aeronautics and Space Administration Huntsville e Alabama 35812 April, 1966 > VI - (PAGES1 / 5 (CODE) z J3-774f/ (NASA CR OR TMX OR AD NUMBER1 LEXINGTON LABORATORIES, INC. Cambridge, Mass . 02140 ' DEVELOPMENT OF PIGMENTS FOR THERMAL CONTROL COATINGS FINAL =PORT by Philip S. Schaffer - Lexington Laboratories, Inc. David W. Jones - Lexington Laboratories, Inc. Contract Number NAS8-20162 (908-20-02-0147) George C. Marshall Space Flight Center National Aeronautics and Space Administration Huntsville, Alabama 35812 April, 1966 FOREWORD This is the final report on the program, "Development 1 e of Pigments for Thermal Control Coatings", conducted for George C. Marshall Space Flight Center, National Aeronautics 1- and Space Administration, under Contract No. NAS8-20162 I covering the period from 17 June 1965 to 16 December 1965. The principal investigator for this program was Philip S. Schaffer; the research engineer was David W. Jones. W. B. Campbell was instrumental in initiating the program and provided consultation through a portion of the work. The program originated from prior Lexington Laboratory studies aimed at producing A1203 whiskers and powders by gas phase reactions . Reproduction in whole or in part is permitted for any r purpose of the United States Government. ABSTRACT The feasibility of producing powders of alumina (A1203), zirconia (Zr02) , silica (Si02), titania (Ti02), zinc oxide (ZnO) and zinc titanate (ZnTiO ) by homogeneous nucleation in 3 the vapor phase was determined. The general reaction used, whereby a metal chloride was initially formed by flowing a controlled amount of chlorine gas over a metal source, then reacted with controlled amounts of carbon dioxide and hydrogen gases, is shown: (9) + xC02(g) + xH2(g) MO (s) + xCO(g) + 2XHCl(g) Mc12x TX Appropriate growth parameters for the individual materials were determined , although optimum process variables for obtaining particular particle sizes were not established. Samples prepared did not have unusual radiation stability, but the capability of producing powders of extremely uniform particle size and of controlled composition was demonstrated. c TABLE OF CONTENTS Page No. 3.1 Alumina (A1203) Powder Preparation. ... 7 3.2 Alumina (A1203) Powder Characteristics. 8 3.3 Zirconia (Zr02) Powder Preparation.. .. 12 3 -4 Zirconia (Zr02) Powder Characteristics. 14 3 Silica (Si0 ) Powder Formation. 14 -5 2 ... ... .. 3.6 Silica (Si02) Powder Characteristics.. 18 3.7 Zinc Oxide (ZnO) Powder Preparation .... 20 3.8 Zinc Oxide (ZnO) Powder Characteristics 22 3 -9 Titanium Dioxide (Rutile, Ti02) Powder Formation.....................,......,. 27 3.10 Ti02 Characteristics................... 28 3.11 Zinc Titanate (ZnTiO ) Powder Formation 28 3 3.12 Zinc Titanate Characteristics.......... 34 4.0 CONCLUSIQNS................................. 36 5.0 ~FERENCES......................~.......~..~ 37 6.0 ACKNO~G~T.............................. 38 7 0 APPENDIX: Tabulated Powder Preparation Conditions Used in These Investigations ................... 39 LIST OF FIGURES Page No. Figure 1: Schema tic Diagram of Homogeneous Nucleation Apparatus .................. 4 Figure 2: Particle Size Distribution of Homo- geneously Nucleated Alumina Powder (A1203 - 1) ........................... 10 Figure 3: Photomicrograph of A1203 - 5 Powder Sample ................................ 11 Figure 4: Photomicrograph of (ZrO2) Powder Sample ................................. 15 Figure 5: X-ray Diffraction Pattern of Zr02 Powder Sample ......................... 16 Figure 6: Photomicrograph of Si02 Powder Sample. 19 Figure 7: Photomicrograph of ZnO Powder Sample.. 23 Figure 8: Photomicrograph of ZnO Whiskers....... 26 Figure 9: Photomicrograph of Ti02 Powder Sample. 29 Figure 10: Photomicrograph of Ti02 Fibers and Platelets............................. 30 Figure 11: Photomicrograph of ZnTi03 and Ti02 Powder Sample ......................... 32 Figure 12: X-Ray Diffraction Pattern of ZnTi03 and Ti02 Powder Sample ................ 33 c W -iv- . LIST OF TABLES Page No. TABLE 1: Conditions for the Formation of A1 0 Po~er......................... 8 23 TABLE 2: A1 0 Powder Characteristics......... 8 23 TABU 3: Qualitative Spectrochemical Analysis. 9 TABLE 4: Conditions for the Production of Zr02 P~er.......................... 13 TABLE 5: Characteristics of Zr02 Powder. .. 14 TABLE 6: Qualitative Spectrochemical Analysis of Zr02 P~er....................... 17 TABLE 7: Conditions for the Production of Si02 Powder............................... 18 TABLE 8: Characteristics of Si02 Powder .. 20 TABLE 9: Qualitative Spectrochemical Analysis of Si0 System 21 2 ....................... TABLE 10: Conditions for the Production of ZnO Po~ers.............................. 22 TABLE 11: Qualitative Spectrochemical Analysis of ZnO Powder........................ 24 TABLE 12: Tensile Strength of Vapor-Deposited ZnO ~iskers......................... 25 TABLE 13: Conditions for the Homogeneous Nucleation of Ti02 Powder............ 27 TABLE 14: Spectrochemical Analysis of Titanium ~~l................................ 28 TABLE 15: Conditions for the Production of ZnTi03 Powder........................ 31 TABLE 16: Qualitative Spectrochemical Analysis of ZnTi03 Powder..................... 35 -V- 1.0 INTRODUCTION The objective of this program was to study the feasi- bility of producing a variety of oxide pigments by vapor- phase reaction that would be available for space-stable thermal-control coatings. Powders for this application should possess a low ratio of solar absorptance to infrared emittance and also exhibit high stability to electromagnetic radiation encountered in the space environment. The per- formance of a pigment may be affected by such variables as particle size, particle size distribution, purity and degree of crystal perfection. Thus, these factors have received particular attention. The formation of powders by homogeneous nucleation from vapor phase reactions offers several advantages over other methods of preparation. These include (a) control of impurity species and attainment of high purity levels, (b) control of particle size by blending for optimum concentrations relative to the light input spectrum and (c) low defect concentration since mechanical size reduction is not required and powders are formed isothermally. In the present study no attempt was made to prepare large quantities of pigment materials nor to attain particular levels of purity. The major goal was to determine the breadth of the techniques applicability to a variety of materials and to determine its advantages and disadvantages relative to other methods of powder preparation. -1- 2.0 TECHNICAL BASIS The technical basis for the method used lies in the experimental observation that in a flowing stream of reactant gases from which a solid oxide phase is precipitated, the morphology of the solid -formed (powder, bulk crystal, platelet or whiskerjis determined by temperature, supersaturation, gas composition, pressure and flow conditions 1-4 . For an overall reaction such as: it is believed that the actual gas phase reaction is of the general form: followed by condensation: Gas reaction equilibrium is achieved rapidly relative to con- densation and nucleation of the solid phase. Thus the gas phase reaction equilibrium constant is given by: 36 'CO 'HCl '02 'Al20 K= 32 P C023P H2 'AlC13 -2- For non-equilibrium condensation, the tendency for nucleation and condensation depends on the supersaturation ratio of the species involved in the condensation process: ( Po2 '~1~0)actual 36 -1 ['CO 'HCl =K ) equil. 32 ('02 'Al20 PC023P H2 'A1C13 Thus, by controlling the temperature, the total system pressure and the gas composition, (which determine K), the supersaturation can be controlled. For homogeneous nucleation a high value of the super- saturation ratio is required, but once this necessary level is achieved the nucleation process occurs rapidly5 . When nuclei are formed, they grow at a rate which is determined by the supersaturation ratio and by the kinetics of the specific surface reactions and deposition processes involved. The length of time that particles are allowed to grow, and thus their final size can be controlled by the reactant gas velocity which is determined by furnace dimensions, tempera- ture, pressure and flow rates. Detailed knowledge of the actual reaction mechanisms involved is not known, but the direction in which changing process variables affects results can be predicted and is the technical basis for an empirical study of the feasibility of applying the method to a number of systems. The vapor train and furnace assembly used for these oxide powder growth studies is shown schematically in Figure 1. Reactant gases, chlorine (99.5% purity), pre-purified hydrogen (99.9% purity), carbon dioxide (99.5% purity) , and C. P. carbon monoxide (99.5% purity) were passed through -3- To atmosphere or + vacuum pump Homogeneous nucleation zone Metal chloride gas Halide generator ( lnconel) Figure 1: Schematic Diagram of Homogenous Nucleation Apparatus. -4 - anhydrous calcium sulfate drying chambers - Hydrogen was also passed through a catalytic purifier to remove oxygen.
Details
-
File Typepdf
-
Upload Time-
-
Content LanguagesEnglish
-
Upload UserAnonymous/Not logged-in
-
File Pages47 Page
-
File Size-