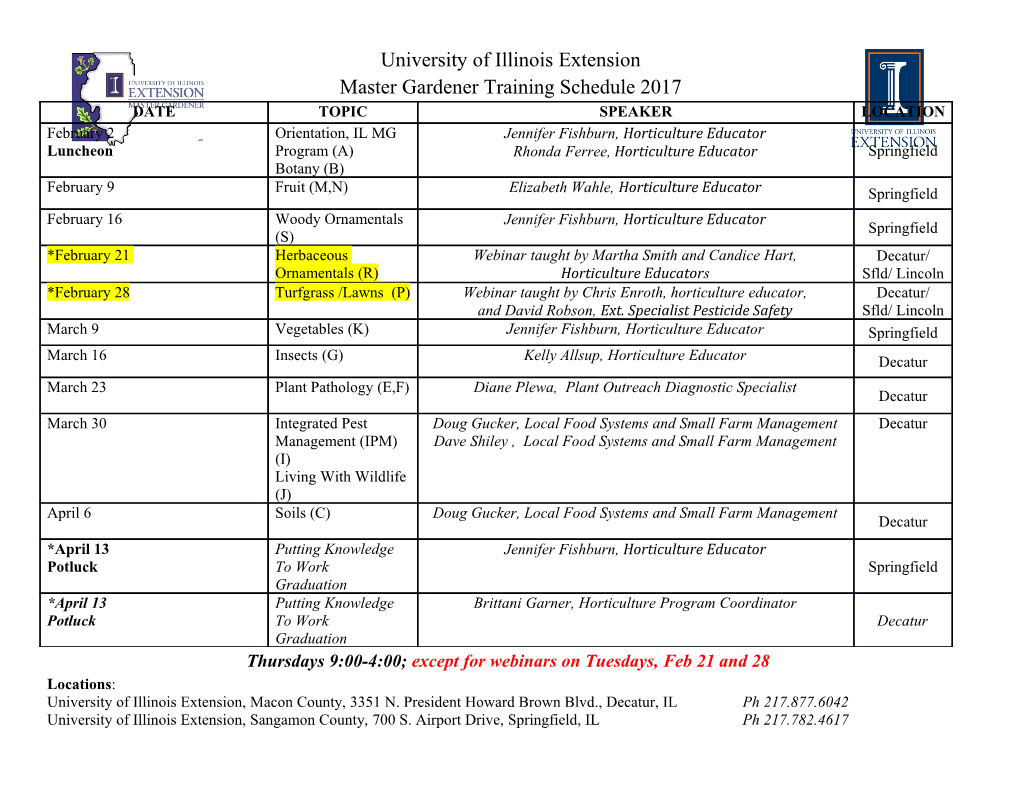
maxon sensor Technology – short and to the point Sensors Program End cap Electrical connections motor and encoder maxon offers a series of sensors. Their charac- – Digital MILE encoder PCB teristics are: – Digital EASY encoder MR sensor Digital incremental encoder – Digital MR encoder Graduated disk – Relative position signal suitable for – Digital Hall effect encoder Magnetic multi-pole wheel maxon sensor positioning tasks – Digital optical encoder Encoder housing – Rotation direction recognition – Speed information from number of pulses per – Analog DC Tacho Solid measure time unit – Analog Resolver Flange – Standard solution for many applications Sensor with housing DC tachometer Encoder fork coupler – Analog speed signal – Rotation direction recognition – Not suitable for positioning tasks Resolver – Analog rotor position signal – Analog speed signal – Extensive evaluation electronics required in the control system – For special solutions in conjunction with sinu- Magnetic principles Optical principle soidal commutation in EC motors On the magnetic Encoder a small multipole In the optical principle of the fork light barrier permanent magnet sits on the motor shaft. The (example: HEDL, HEDS, SCH16F, 2RMHF, changes in the magnetic fl ow are recorded Enc22) an LED sends light through a fi nely Digital Incremental Encoder by sensors and supplied to the electronics as resolved impulse disc, which is mounted on processed channel A and B. Magnetic encoders the motor shaft. The receiver (photo transistor) Encoder signals require a minimum of space. changes light/dark signals into corresponding For further processing in the controller, the electrical impulses that are amplifi ed and pro- MR encoder encoders deliver square-wave signals whose cessed in the electronics. pulses can be counted for exact positioning or – Sensor with magnetoresistive principle speed measurement. Channels A and B pick up – High counts per turn possible, Characteristics phase shifted signals, which are compared with thanks to interpolator – High number of pulses one another to determine the rotation direction. – Different number of pulses can be selected – Index channel and line driver possible All maxon positioning systems evaluate the – with/without index – Very high accuracy rising and falling signal edges. With regard to – with/without line driver encoder number of pulses, this results in a four MEnc times higher positioning precision. This is what is – Digital Hall sensors Inductive principle referred to as quadcounts. – 2 channels A and B A “home” pulse (index channel I) can be used – No line driver possible With inductive MILE encoders, a high-frequency as a reference point for precise determination of – Low number of pulses alternating fi eld is transformatively transmitted rotation angle. and thus angle dependant modulated, using a The line driver produces complementary signals EASY encoder – – - structured copper disk. A, B, I which help to eliminate interference on – Integrated circuit with Hall sensor and interpolator long signal lines. In addition, this electronic Characteristics – Counts per turn programmable from 1 to 1024 driver installed in the encoder improves signal – Very robust against magnetic and electrical – With index channel and RS422 line driver quality by steeper signal edges. fields as well as contamination QUAD encoder – Very high speeds possible – Digital Hall sensors – High precision. Interpolation errors are – 4 statuses per turn largely compensated for by a look-up table – Line driver not possible – Index channel and line driver available – Absolute interface (SSI) on request Representation of the output signal Schematic design of a Schematic design of an of a digital encoder magnetic encoder opto-electronic encoder BA 90° e Phase shift A,B A B I Sensor LED Mask Wheel 360° e Cycle plate Channel A N S Phototransistors Channel B N Motor Motor shaft Channel I shaft S Magnetic- Index puls width Rotor CW Phase shift of index pulse 38 Technology – short and to the point November 2014 edition / subject to change 1404_Technology.indd 38 20.11.14 11:13 maxon sensor Tips on encoder selection DC Tacho Principal features of the maxon incremental The following applies especially to In principle every maxon DC motor can be used encoder are: positioning systems: as a DC tacho. For motor-tacho combinations, – The number of pulses per revolution – The higher the number of pulses, the more we offer a DC tachometer, whereby the tacho (increments) precise the position that can be reached. rotor is mounted directly on the motor shaft. – The accuracy At 500 pulses (2000 quadcounts) an angle Characteristics – Use of an index channel resolution of 0.18° is achieved, which is – The output DC voltage is proportional to the – The use of a line driver usually much better than the precision of the speed thanks to the precious metal brushes – The maximum supported speed mechanical drive components (e.g. due to – AINiCo magnet for high signal stability with – The suitability for special ambient conditions gear play or elasticity of drive belts). temperature fluctuations (dust, oil, magnetic fields, ionizing radiation) – Only encoders with an integrated line driver – No additional tacho bearings or friction (RS422) should be used in positioning con- Encoders and maxon controllers – No couplings, high mechanical resonance trols. This prevents electromagnetic interfer- – As a standard the maxon controllers are pre- frequency ence signals from causing signal loss and set for encoders with 500 pulses per revolu- accumulated positioning errors. tion. – Positioning applications often require the – The input frequency of the controller electron- index channel of the encoder for precise refer- ics can limit the maximum possible counts per Resolver ence point detection. turn of the encoder. The resolver is mounted on the motor’s through – The higher the number of pulses and the shaft and adjusted according to the magnetic higher the accuracy the better a smooth, jerk- fi eld of the motor rotor. The resolver has a rotat- free operation can be achieved even at low ing primary coil (rotor) and two secondary coils speeds. (stator) offset by 90°. An alternating current – maxon controllers can be set for low or high connected to the primary coil is transferred to speed operation and for encoders with a low the two secondary coils. The amplitudes of the or high number of pulses. secondary voltages are sin ϕ and cos ϕ, where ϕ is the rotation angle. Characteristics – Robust, for industrial use Schematic design of Recommendations on encoder selection – Long service life the inductive MILE encoder () Conditionally applicable – No mechanical wear – Output signal can be transmitted over long distances without problems QUAD MEnc MR EASY MILE optical – No sensitive electronics 1 very high speed – Special signal evaluation required 2 very low speed ()() sin – Only one sensor for position and speed infor- arctan 3 precise position ( )( )( ) mation A/D 4 line driver possible – EC motors with resolver are supplied without Hall sensors LUT index channel possible cos 5 6 compact design () 7 dust, dirt, oil 8 External magnetic fi elds ()()() 9 ionising radiation November 2014 edition / subject to change Technology – short and to the point 39 1404_Technology.indd 39 20.11.14 11:13.
Details
-
File Typepdf
-
Upload Time-
-
Content LanguagesEnglish
-
Upload UserAnonymous/Not logged-in
-
File Pages2 Page
-
File Size-