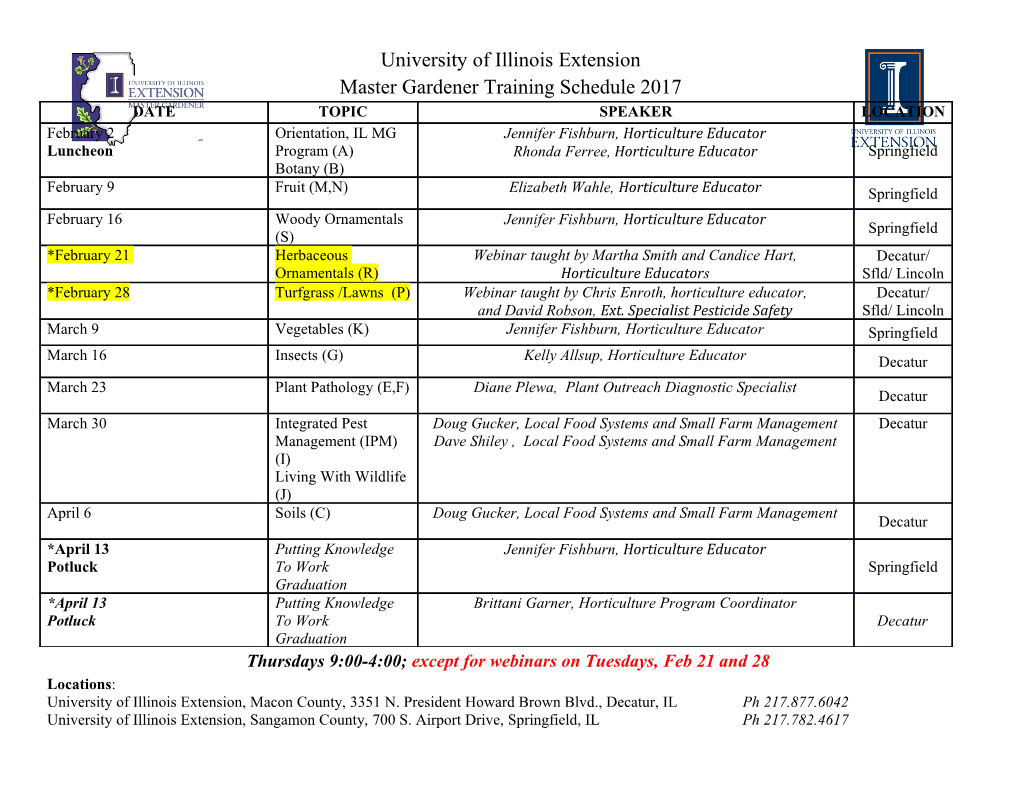
EXAMENSARBETE INOM TEKNIKOMRÅDET TEKNISK FYSIK OCH HUVUDOMRÅDET ELEKTROTEKNIK, AVANCERAD NIVÅ, 30 HP STOCKHOLM, SVERIGE 2018 Energy Management of Parallel Hydraulic Hybrid Wheel Loader with Focus on Fuel Consumption Minimization HOANG THAI DO KTH SKOLAN FÖR ELEKTROTEKNIK OCH DATAVETENSKAP Abstract Hybridization of driveline system is one possible solution to increase fuel efficiency. In this thesis a parallel hybrid hydraulic wheel loader concept was studied. A high pressure accumulator was added to the system and acted as a second source of en- ergy. By adding the high pressure accumulator, regenerative braking energy can be stored for later utilization. A backward facing simulation model was developed where the high pressure accumulator's State Of Charge (SOC) as state variable and hydraulic pump/motor's displacement as control input. Furthermore, differ- ent energy management strategies: Dynamic Programming (DP), rule-based and Equivalent Consumption Minimization Strategy (ECMS) were developed. These strategies were evaluated and compared to each other all with respect to the fuel consumption. The result from conventional machine acted as the benchmark for other strategies to compare with. From simulation results, rule-based strategies showed to be the most robust, resulted in lower fuel consumption in every tested driving cycle. For ECMS, the performance varied from cycle to cycle. A reduction in fuel consumption was observed for short-loading cycles. Especially in one cycle, ECMS result outclassed rule-based and was almost the same as DP. However, a small increment was observed for long-carry cycle. Here the introduction of lock-up feature in the torque converter yielded instead the most fuel saving. These valuable conclusions acted perfectly as a good starting point for future product development. 2 Sammanfattning Hybridisering av drivlinan ¨aren m¨ojligal¨osningf¨or¨okad br¨ansleeffektivitet. En par- allell hybrid hydraulik hjullastare koncept unders¨oktesi detta arbetet. Genom att s¨attaen extra h¨ogtrycksackumulator till systemet kunde regenerativ bromsningsen- ergi lagras f¨orsenare anv¨andning. En bak˚atsimuleringsmodell med ackumulators laddningstillst˚andsom tillst˚andsvariabel och hydraulisk pumps/motors f¨orflyttning som reglering signal utvecklades tillsammans med olika energy regleringstrategier s˚a som: dynamisk programmering (DP), regelbaserad (RB) och Ekvivalent Konsum- tion Minimering Strategi (engelska - ECMS). Strategierna evaluerades och j¨amf¨ordes med h¨ansyn till br¨anslef¨orbrukningend¨arresultaten fr˚ankonventionella maskinen anv¨andessom referens. Regelbaserad strategier visades vara mest robusta d¨ar br¨anslef¨orbrukningminskades f¨oralla testade k¨orcyklar.F¨orECMS varierades re- sultatet mellan olika k¨orcyklar.En minskning av br¨anslef¨orbrukningnoterades f¨or alla kortcyklar. F¨oren cykel utklassade ECMS RB och var n¨astanlika bra som DP. F¨orl˚angcyklarresulterade ECMS i en liten ¨okningav br¨anslef¨orbrukning.Att intro- ducera "l˚asa-in"funktion i momentomvandlare gavs den st¨ortabr¨ansleminskningen. Slutsatserna var mycket v¨ardefullatill framtidens utveckling. 3 Contents 1 Introduction 1 1.1 Background . .1 1.2 Problem description . .1 1.3 Energy Management Strategy . .2 1.4 Purpose and project aim . .3 1.5 Method . .3 1.6 Thesis Outline . .4 2 Hydraulic Hybrid Vehicle 5 2.1 Parallel Hybrid Hydraulic Vehicle . .6 2.2 Series Hybrid Hydraulic Vehicle . .6 2.3 Power-split Hybrid Hydraulic Vehicle . .7 2.4 Studied Wheel Loader Hybrid Configuration . .8 3 Theory 9 3.1 Driving cycles . .9 3.1.1 Short Loading Cycle . .9 3.1.2 Load and Carry Cycle . 10 3.2 Torque Converter . 11 3.3 Energy storage . 13 3.4 Accumulators . 14 4 System Modeling 15 4.1 Backward simulation model . 15 4.1.1 Propeller shaft . 16 4.1.2 Transmission Gear ratios . 16 4.1.3 Add-on Hydraulic Hybrid Pump/motor . 17 4.1.4 Transmission . 17 4.1.5 Torque Converter . 18 4.1.6 Work Hydraulic Machine . 18 4.1.7 Internal Combustion Engine . 18 4.2 Lock-up Activation . 19 4 5 Control Strategies 20 5.1 Dynamic Programming . 20 5.1.1 Theory . 20 5.1.2 Mathematical Problem Formulation . 23 5.2 Rule-based Strategies . 24 5.2.1 Working moment based . 24 5.2.2 Power and Torque based . 24 5.3 Equivalent Consumption Minimization Strategy . 25 5.3.1 Mathematical Problem Formulation . 28 5.3.2 Optimal equivalent factor . 28 6 Result and Analysis 29 6.1 Fuel consumption . 29 6.2 Additional Lock-up Feature . 30 6.3 Simulation parameters - ECMS . 30 6.4 Strategies analysis . 31 7 Conclusions and Future Work 34 7.1 Conclusion . 34 7.2 Future Work . 34 List of Figures 1.1 Energy Management Strategies overview of classification . .2 2.1 A schematic illustration of a parallel HHV. .6 2.2 A Schematic illustration of serie HHV. .7 2.3 A Schematic illustration of power-split HHV. .7 2.4 Driveline components for hydraulic hybrid wheel loader concept . .8 3.1 Short loading cycle. [11] . .9 3.2 Load & carry cycle [11] . 10 3.3 Schematic presentation of a TC together with fluid flow direction [12] 11 3.4 Specific power and specific energy for different short-term energy stor- age systems [7] . 13 3.5 Common types of hydropneumatic accumulator [13] . 14 4.1 Simple version of backward simulation model with one control signal and one state variable. 15 5 5.1 The red arc is the optimal trajectory. Any problem initiated from a point on the optimal trajectory will have the remaining trajectory as the optimal trajectory. 21 5.2 The DP algorithm. The red arc is the optimal path with lowest cost- to-go . 22 5.3 The energy flow in ECMS for recharging and discharging phase . 25 5.4 Weight function WSOC for different exponent a with SOCmin = 0, SOCmax = 1 and SOCfinal = 0:5 .................... 27 5.5 The algorithm of the bisection method for optimal equivalent factor searching. 28 6.1 DP and ECMS SOC trajectory for the short loading cycle 1. 31 6.2 DP and ECMS SOC trajectory for load carry cycle without lock-up. 32 6.3 DP and ECMS SOC trajectory for load carry cycle with lock-up. 32 6.4 Rule-based 1 and 2 SOC trajectory for short loading cycle 1. 33 List of Tables 6.1 Fuel consumption comparison for different EMS and driving cycles with fuel consumption for conventional machine as baseline . 29 6.2 Fuel consumption comparison (in % ) for load and carry cycle be- tween no lock-up and lock-up with fuel consumption for conventional machine without lock-up as baseline. 30 6.3 Simulation parameter in ECMS for different driving cycle. 30 6 Nomenclature Acronyms DP Dynamic Programming ECMS Equivalent Consumption Minimization Strategy EMS Energy Management System FD Final Drive FWD Forward HV Hybrid Vehicle HEV Hybrid Electric Vehicle HHV Hybrid Hydraulic Vehicle ICE Internal Combustion Engine KD Kick Down REV Reverse SOC State of Charge TC Torque Converter 7 Symbols ηaxle Axle efficiency [-] λ Equivalent factor [-] µ Torque converter slip [-] ν Torque multiplication factor [-] hyb Relative displacement setting hybrid hydraulic system [-] WH Relative displacement setting work hydraulic system [-] γ Polytropic index [-] Dhyb Maximum hybrid machine displacement [ml/rev] DWH Maximum work hydraulic displacement [ml/rev] fuelICE Engine consumed fuel [l] Fwheel Vehicle wheel traction force [Nm] 2 JICE Engine moment of inertia [kgm ] iaxle Gear ratio for drive [-] ihyb Gear ratio propulsion axle - hybrid machine axle [-] itra Gear ratio transmission [-] iWH Gear ratio work hydraulic - engine crankshaft [-] nhyb Rotational speed of hybrid machine [rpm] nICE Engine speed [rpm] nprop Rotational speed of propulsion axle [rpm] nturb Rotational speed of torque converter turbine [rpm] nimp Rotational speed of torque converter impeller [rpm] nWH Rotational speed of work hydraulic [rpm] p Accumulator pressure [bar] p0 Accumulator initial charge pressure [bar] pmax Accumulator maximum pressure [bar] pmin Accumulator minimum pressure [bar] pWH Work hydraulic pressure [bar] Paux Auxiliary power [W] Pprop;lim Propulsion axle power limit [W] peng Engine power [W] 3 QWH Work hydraulic pump flow [m =s] Qlvh Diesel lower heating value [MJ/kg] rtire Tire radius [m] T s Simulation time step [s] TICE Engine torque [Nm] TICE;load Engine load torque [Nm] Timp Torque converter impeller torque [Nm] Thyb Hybrid hydraulic machine torque [Nm] Tprop Propulsion axle torque [Nm] Tprop;lim Propulsion axle torque limit [Nm] Tturb Torque converter turbine torque [Nm] Ttra Transmission torque [Nm] TWH Work hydraulic machine torque [Nm] Paux Auxiliary power [W] 8 Chapter 1 Introduction 1.1 Background Higher fuel efficiency has been one of the biggest goal in automotive industry for decades. Reasons are many: more restrictive emission legislation, high fuel prices and the fact the fossil fuel is a limited resource are some of the examples. In the past few years, the trend towards hybridization of driveline is easier to observe than ever. In the field of off-road machinery, the same trend can be observed. Volvo CE, as one of the biggest player in the construction equipment industry has always strive for higher fuel efficiency by investigating of new driveline configurations. Again, hybridization is one of the possible solution. Wheel loaders are heavy machines where a typical operating cycle contains many starts and stops. Large amount of energy is wasted as heat when the tradition friction brakes are used [1]. If these energy can somehow be recuperated and stored for later utilization, significant improvement in term fuel efficiency can be achieved. It raises the questions of how to recuperate and store these energy and when is the best occasion to use the stored one. 1.2 Problem description In the concept studied in this thesis, the first problem for recuperating the energy is solved by introducing hydropneumatic accumulators and a hydraulic pump/motor mounted on a transmission shaft to enable regenerative braking. In order to deal with the second question, it is important to have adequate simulation models and suitable energy management strategies.
Details
-
File Typepdf
-
Upload Time-
-
Content LanguagesEnglish
-
Upload UserAnonymous/Not logged-in
-
File Pages61 Page
-
File Size-