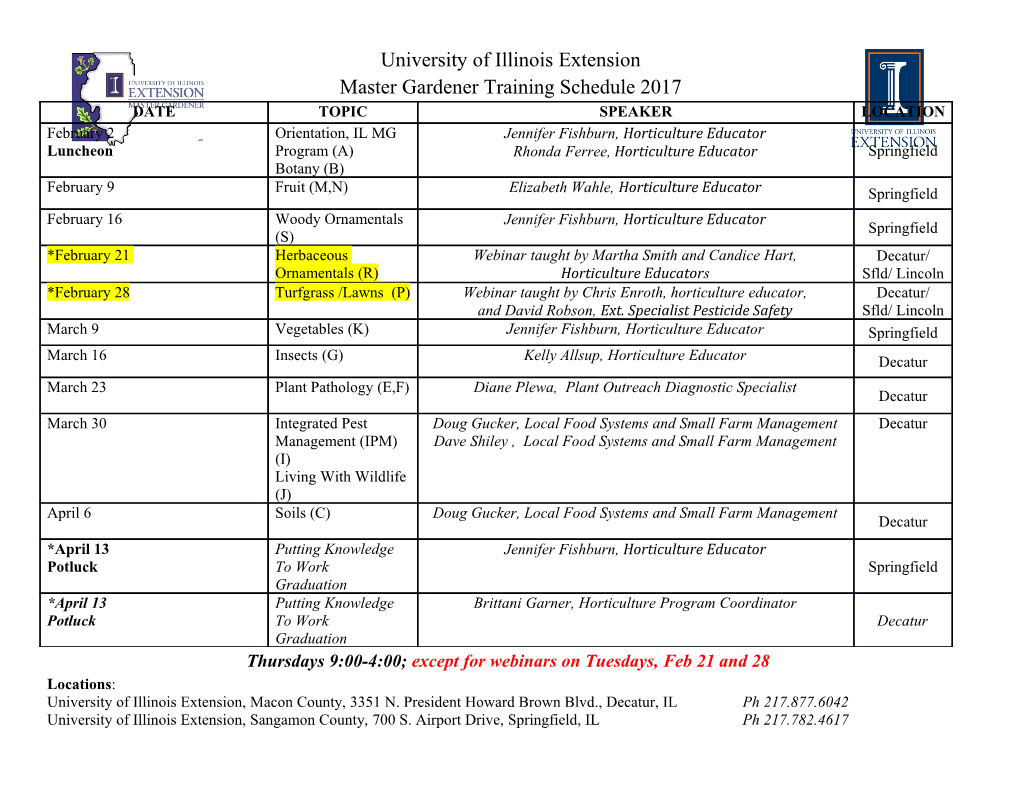
The Space Congress® Proceedings 1966 (3rd) The Challenge of Space Mar 7th, 8:00 AM Testing the Man-Rated Launch Vehicle Francis X. Carey Martin Company Follow this and additional works at: https://commons.erau.edu/space-congress-proceedings Scholarly Commons Citation Carey, Francis X., "Testing the Man-Rated Launch Vehicle" (1966). The Space Congress® Proceedings. 2. https://commons.erau.edu/space-congress-proceedings/proceedings-1966-3rd/session-6/2 This Event is brought to you for free and open access by the Conferences at Scholarly Commons. It has been accepted for inclusion in The Space Congress® Proceedings by an authorized administrator of Scholarly Commons. For more information, please contact [email protected]. TESTING THE MAN-RATED LAUNCH VEHICLE Francis X. Carey Martin Company Cocoa Beach, Florida Although manned space flight is still in From this mathematical relationship, it its infancy, testing of launch vehicles can be seen that achieving a satisfactory has progressed to a high degree of so­ level of probability of crew survival phistication. required that careful consideration be given to such launch vehicle items as: As of December 1965, the Martin-built Gemini launch vehicle has launched 1. Component and/or system, redundancy seven Gemini spacecraft successfully which can improve the reliability out of seven attempts. This remarkable of the launch vehicle record was made possible by two facts: 2. Analysis of launch vehicle failure 1. The basic reliability of the modes followed by design of a re­ hardware liable malfunction detection system or MDS 2. The test program. 3. Functional utilization of the crew This paper briefly describes the Gemini as part of the malfunction detection launch vehicle noting the major differ­ system ences between it and the Titan II and discusses the test program. It is not 4. Emphasis in launch vehicle checkout proposed that this is the only method on minimizing the possibility of of testing a man-rated launch vehicle; launching a bad vehicle however, it is a successful one. 5. Test, countdown, and launch proced­ The Gemini launch vehicle is a basic ures that will lead to maximum Air Force Titan II which has been modi­ probability of launching a good fied in certain areas to achieve man- vehicle rating (see Figure 1). 6. System simplification where possible Launch Vehicle Man-Rating to achieve reliability. Man-rating is the philosophy and plan Man-rating a Titan II is a many-sided for marshaling the disciplines necess­ process conceived by Martin and the Air ary to achieve a satisfactory proba­ Force to improve the reliability of the bility of mission success and crew basic vehicle by modifying existing sys­ survival. This probability may be tems, by using redundant components, by expressed in terms of reliability of adding special systems for crew safety the malfunction detection and escape purposes, by special handling of critical systems. Mathematically, these terms components, by meticulous selection of are linked in the equation: qualified people, and by developing pro­ cedures in the entire design-production- = RLV *MDS manufacturing-test-launch cycle that es­ tablishes as a goal flawless performance where: from the launch vehicle. PCS = probability of crew survival Titan II Modifications for Gemini RT XT = reliability of the launch The high reliability of the ultimate man- vehicle rated Gemini-Titan launch vehicle was the made early in the = reliability of the malfunction result of two decisions engineers-- detection and escape systems. program by Martin and Air Force 332 first, to make as few changes as possible with one important exception: ASIS was in the basic Titan II and secondly, to completely automatic (after a serious make every necessary change count toward malfunction was discovered, ASIS auto­ overall reliability. Each of the modifi­ matically initiated mission abort), cations added to reliability and safety while MDS only provides vehicle condi­ and contributed to man-rating. tion information to the astronauts. In other words, MDS signals to the astronaut The major modifications, accepted only the proper or improper functioning of the after careful review by a top level Air launch vehicle and allows him to make the Force-Martin engineering board, were: decision as to whether to continue the mission in the event of a malfunction or 1. The addition of a malfunction de­ when to abort the mission if this should tection system designed to sense become necessary. Only in the event of problems in any of the vital an engine hardover condition does the MDS booster systems and transmit this automatically act and in this case, only information to the astronaut crew to switch over to redundant hydraulic, flight control, and electrical systems, 2. A redundant flight control system not to abort the mission. As a result, which could take over should the the MDS is a relatively simple system primary system fail in flight with a high degree of reliability. It takes advantage of one of the lessons of 3. Redundancy in the electrical sys­ Project Mercury - that man can function tem with necessary changes to in space as a working pilot, not just as provide power for such added a passenger in his spacecraft. The MDS, launch vehicle equipment as the which is completely redundant, monitors MDS during flight: propellant tank pressures, staging of the launch vehicle, thrust 4. Substitution of radio guidance chamber pressures, electrical system volt­ for inertial guidance used in the age, and turning rates which would indi­ Titan II ICBM version to provide cate a need for action if the launch a weight reduction and also to vehicle structural limits are approached. provide a more responsive system during critical orbital injection Hydraulic System 5. Redundancy in the hydraulic sys­ The launch vehicle's hydraulic systems tems where desirable for pilot control the position of the Stage I and sa±£ry, sucn as hydraulic actua­ Stage II rocket engine thrust chambers tors for engine gimbaling in response to electrical signals from the flight control system. Changing the 6. Instrumentation to provide addi­ thrust direction in this manner, the tional data during pre-flight launch vehicle is steered along the de­ checkout and flight not considered sired line-of-flight by making corrections necessary in the ICBM version. in pitch or yaw axes. The thrust chambers are gimbal-mounted to allow two degrees of Malfunction Detection System freedom. Stage I roll control is provided also by varying direction of the two The malfunction detection system (MDS) thrust chambers. A separate roll control (Figure 2) is perhaps the most signifi­ nozzle with one degree of freedom is pro­ cant modification made to Titan II to vided in Stage II which has one thrust prepare it for the manned Gemini mis­ chamber. sion. The MDS monitors operation of vital launch vehicle subsystems and The Gemini-Titan launch vehicle has three signals the spacecraft crew if a mal­ separate hydraulic systems - the Stage I function takes place. The Gemini-Titan primary system, the Stage I secondary sys­ MDS is comparable in function to the tem, and the Stage II system. A schematic launch vehicle ASIS (Abort Sensing and of the redundant Stage I hydraulic system Implementation System) of Project Mercury is shown in Figure 3. 333 Stage I Primary, Basic components chamber for pitch and yaw control, and of the Stage I primary hydraulic system one on :he off-center turbine exhaust are an engine-driven pump, an accumula­ nozzle for roll control. tor/reservoir, four servo actuators, and an electric motor-driven pump. An axial piston, pressure-compensated, variable volume engine-driven pump The Gemini-Titan flight control system pressurizes the system at 3000 psi constitutes a basic change from the during Stage I flight. The pump is Titan ICBM system. Specifically, the driven by the accessory drive pad on system is designed to withstand any the turbodrive assembly of the Stage I single malfunction (failure) and com­ engine. The servo actuators control plete the launch phase successfully. the movement of the Stage I thrust The design achieves this increased re­ chambers. The actuators are built as liability by complete flight control tandem units consisting of two complete system redundancy (Figure 4) . electro-hydraulic servo system sections. One servo section of each actuator is A complete secondary or redundant flight connected to the primary hydraulic sys­ control system is provided in the Gemini- tem; the other servo actuator section Titan launch vehicle to protect the in each actuator comprising a portion astronaut crew from this one event. of a secondary or redundant hydraulic Switchover from the primary to second­ system* The actuator sections are in­ ary system in the event of an engine dependent but interconnected by a hardover condition is automatic and special "switchover"valve that permits requires only 15 milliseconds. The only one of the servo sections to be switchover is final and no provision operable at any given time. is made for switching back during Stage I flight. After staging, the pilot may Stage I Secondary. The secondary switch back to the primary mode. or redundant Stage I hydraulic system Switchover to the secondary system is identical to the primary system. It also can be effected by three other operates in line with the secondary or methods: redundant flight control system. The same electric motor-driven pump is used 1. Astronaut command for both secondary and primary systems during checkout through use of a system 2. Vehicle overrate detected by the test selector valve. The secondary sys­ MDS rate sensors tem is pressurized throughout flight, although not in use unless switchover 3. Loss of Stage I primary hydraulic occurs. The actuator switchover valves system pressure. are designed to sense primary system pressure and initiate switchover to the The primary flight control system con­ secondary hydraulic system in case of sists of the following: any failure within the primary system that would result in a loss or degrada­ 1.
Details
-
File Typepdf
-
Upload Time-
-
Content LanguagesEnglish
-
Upload UserAnonymous/Not logged-in
-
File Pages21 Page
-
File Size-