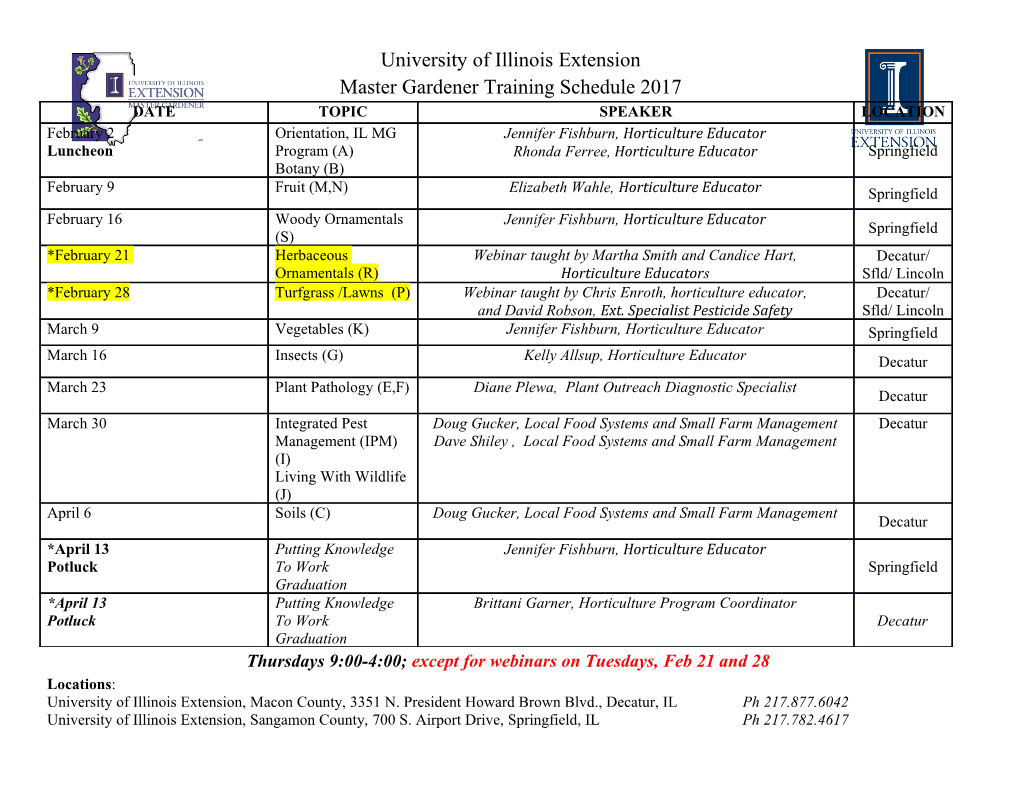
Learning From Success: A Discussion Paper September 2017 Contents Introduction ���������������������������������������������������������������������������������������������������������������������������������������������������� 1 The limitations of only looking at failure ��������������������������������������������������������������������������������������������������� 2 The limitations of our traditional approach to looking at what goes wrong for learning �������������������� 2 The benefits of a more positive approach �������������������������������������������������������������������������������������������������� 6 What can we learn from positive psychology? ���������������������������������������������������������������������������������������������� 6 The value of near miss investigation as an examination of success �������������������������������������������������������� 7 Why find out about what went right? �������������������������������������������������������������������������������������������������������������� 8 A positive methodology for learning from success �������������������������������������������������������������������������������� 10 Near miss/near hit investigations ������������������������������������������������������������������������������������������������������������������ 10 Scenario 1 Case Study: Near miss/near hit involving Qantas Flight 32 �������������������������������������������������� 12 Serious Incidents ������������������������������������������������������������������������������������������������������������������������������������������������ 16 Scenario 2 Case Study: Australian Transport Safety Bureau Report – Safe working irregularity following rail track maintenance �������������������������������������������������������������������������������������������������������������� 20 Learning from success during projects ��������������������������������������������������������������������������������������������������������� 24 Tips for exploring success �������������������������������������������������������������������������������������������������������������������������������� 25 Scenario 3 Case Study: The London Summer Olympics ����������������������������������������������������������������������� 28 If the lessons from incidents were as simple as our current approach to incident investigations suggests, why haven’t we learn the lessons already? Michael Tooma Partner Clyde & Co Introduction The key to improving at anything is learning� But what are we learning from? So much We need to find the of the time in safety, the conversation is about learning from what has gone wrong� passion for learning An incident has occurred� What went wrong, from all that we do: we ask? How do we prevent that incident from re-occurring? our successes as well But if that is all we do, are we not missing out on many potentially as our failures� fruitful lessons? What happens if we turn this paradigm on its head? Instead of focusing all our attention on failures in safety performance, what if we started to learn from success? What Michael Tooma would that look like? Partner T: +61 457 087 952 There is success in everything we do� Even in failure, there E: michael�tooma@clydeco�com may be successes from which we can learn� While we have a in/michael-tooma-0b222421 tendency to cherry-pick what went wrong in the lead-up to an @ MichaelTooma incident, the reality is not so simple� Undoubtedly, there will also be a number of things that proceeded according to plan Alena Titterton and worked successfully� There is benefit in learning from that� Partner T: +61 439 077 702 In this paper, we will explore: E: alena�titterton@clydeco�com • the limitation of only exploring past failure for ‘lessons learnt’ in/alena-titterton-91888a56 • the benefits of a more positive approach @AlenaTitterton • a methodology for learning from success, and • scenarios using the methodology� We hope that this paper provides some inspiration for moving beyond simply looking at failure to derive our lessons in order to achieve better safety outcomes� The limitations of only looking at failure The limitations of our traditional approach Further, we engage in cherry picking of events� Things take to looking at what goes wrong for learning on more significance with the benefit of hindsight than they The challenge for everyone involved in incident management did in real time� We focus on those things because they fit a and investigation is that we fall victim to the mindset of over- certain narrative, an explanation for the wrong path taken� simplifying causes of disasters� Disaster reports are starting But identifying them in this way has little preventative to sound the same� They all tell the tale of a company that value because they clearly did not seem obvious to workers, preferred profit over safety� They make recommendations for managers and/or leaders in real time� greater safety leadership, the need for a safety culture and for The problem with focusing on what went wrong a more effective regulator� We analyse things in the same way, is that we never get the full story make the same recommendations and somehow expect the result next time around to be different� In addition, people get defensive when you ask them about what went wrong� They either deliberately or subconsciously We do this at a smaller scale also� The imperative in the distort the truth to sound more favourable or to make their aftermath of an incident is to minimise the impact of the mate sound more favourable� While you can improve that incident� That means reducing shutdown time associated with somewhat by creating just culture in the workplace, you can’t damaged equipment, regulatory notices or industrial action� eliminate it altogether� What you get, ultimately, is the version This often leads to reactive and narrow-focused decision of the truth that people are willing to share with you so you making on corrective actions - a new safe working procedure never fully capture the learning from any incident� and training course, for example, is the most popular corrective action� The assumption is that if we identify the cause of the These things are further exacerbated by the fact that most incident, we can simply develop a procedure for addressing it, of our investigation techniques are best designed for story train workers in the procedure and require them to follow it� telling rather than analysis� They are based on uncovering That thinking satisfies the regulators, they being more eager the linear timeline of events: “This happened and then that than most to move on to the next incident being investigated� It happened�” But often the order in which things happen limits liability in that it is usually accompanied by a third feature distorts the understanding of why they happened in that -the implicit or explicit blame of the workers involved, either for conditions may have existed within the system for many needing a procedure or for failing to follow it� It also satisfies the years that are important to the incident� This limits our conscience of managers who feel they have addressed the issue analysis of incidents� as soon as it came onto their radar� Crucially, it is cost effective� So how do we factor that into incident investigations? A procedure is relatively cheap compared to an engineering By accepting that, faced with the same facts, people will not solution� Of course, if that procedure works and will be followed, necessarily behave in the same way� The world we live in is far then the problem is truly solved and all objectives have been more complex than that� Dekker (2011) observes: met� In a perfect world, that would be the case since, for “Rational decision-making requires a massive amount of example, it is in the best interest of the company to ensure that cognitive resources and plenty of time� It also requires a the procedure is comprehensive and effective� It is in the best world that is, in principle, completely describable� Complexity interest of the workers to understand the procedure and follow denies the possibility of all of these� In complex systems it; after all, it is there for their health and safety� Unfortunately, (which our world increasingly consists of) humans could not the world is not that simple� or should not even behave like perfectly rational decision- There are a number of biases that prevent us from makers� In a simple world, decision-makers can have perfect understanding what goes wrong� For example, investigations and exhaustive access to information for their decisions, as suffer from hindsight bias – we know exactly what happened well as clearly defined preferences and goals about what they and how it happened so it seems obvious to us where the want to achieve� But in complex worlds, perfect rationality operator went wrong� But if it seems so obvious to us, why (that is, full knowledge of all relevant information, possible would they have done what they have done? Surely no one outcomes, and relevant goals) is out of reach ... goes to work with the intention of hurting themselves or In complex systems, decision-making calls for judgments others around them� If they did something wrong, it must under uncertainty, ambiguity and time pressure� In those have seemed like a good idea at the time, right? settings, options that appear to work are better than perfect 2 Subconsciously Strategically distorted truth distorted truth Judging people for what Protectionism should have been done Cherry-picking Hindsight bias
Details
-
File Typepdf
-
Upload Time-
-
Content LanguagesEnglish
-
Upload UserAnonymous/Not logged-in
-
File Pages36 Page
-
File Size-