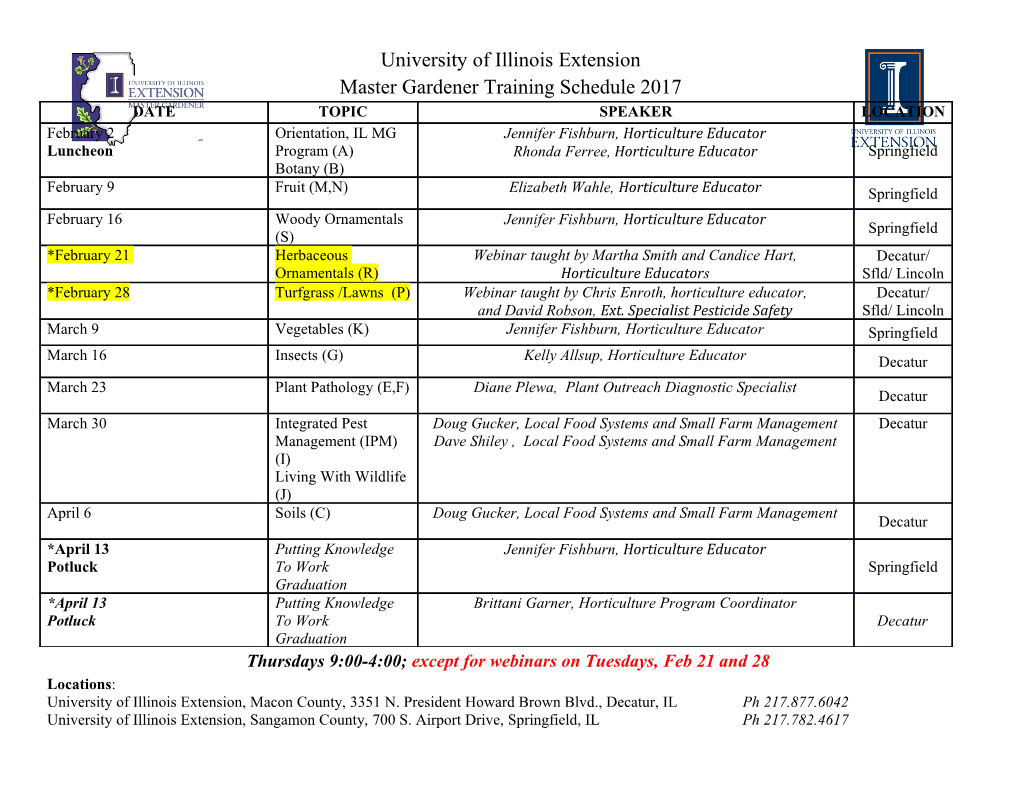
IIBA Lean Six Sigma Introduction – Janet Lau Janet Lau is a certified Lean Six Sigma Master Black Belt with thirteen years of business improvement experience. She is also a recent Executive MBA graduate at the University of Alberta. Currently, Janet is the Principal Consultant and Owner of Breakthrough Solutions Consulting. She is specialized in delivering transformational business results for organizational effectiveness, productivity, and profitability. Janet successfully delivered over hundred projects ranging in complexity from simple Lean projects to complex technical projects across the full spectrum of the business - operations, supply chain management, HR, Finance, Health & Safety, IT, and cross-department level initiatives. She is passionate about developing the next generation of Lean Six Sigma practitioners and offers a variety of Lean Six Sigma training courses. Her key strategy for success is being people-oriented, data-driven, and taking a stand for making a difference. Presentation Topics: • What is ‘Lean’...and what is ‘Six Sigma’? 1. Introduction to Lean • What are the similarities and differences? and Six Sigma • How does this help me in my work? • Taking a data-driven approach to define the 2. Data! Data! Data! problem, identify defects, and validate the effectiveness of solutions. 3. Hands-on learning and real-world problem • How does experiential project engagement and solving create learning increase project ownership? engagement. Part 1: What is Lean Six Sigma? In the 1980s Lean and Six Sigma were two separate methodologies. Lean – known from Toyota Six Sigma – known from Motorola Both were derived from the manufacturing industry with same goal: improve customer improvement on improving the speed improve employee reduction in cost satisfaction, product quality of production engagement. In 2001, by a book titled Leaning into Six Sigma: The Path to Integration of Lean Enterprise and Six Sigma by Barbara Wheat, Chuck Mills, Mike Carnell.[6] The book was developed as a guide for managers of manufacturing plants on how to combine lean manufacturing and Six Sigma in order to dramatically improve quality and cycle time in the plant. What is Lean? Goal o Remove of Waste o Maximize Process Flow o Eliminate non-value added process steps o Create standization o Create balance load process o Focus on Customer Requirements Speed What is Waste? (MUDA) Practice: Are you able to identify waste in your workplace?.. Or day to day life? What is Six Sigma? Which pilot do you choose? P1 P2 P3 x x x xx x x x x x x x x x xx x x What is Six Sigma? Problem with Spread Problem with Centering Target Actual Target Actual xx x xx x x x x x x x xx x x x x x x x x d x x x x x x xx x x x x x x x x x x x x x x x x x xx x x x xx x x x x x x x x x x x x x x x x x x x x x x x x x x x x x x x x x x x x x Off - Target Large Variation Unfocused Efforts Six Sigma used to reduce spread Six Sigma used to Six Sigma used to Center Process focus efforts xx x x xx xxxx x xxx x On Target Slide 8 Minimal Variation What is Six Sigma? Why do I need 6 Sigma? Sigma Performance Levels What Does This Look Like In The Real World? -- One To Six Sigma Real-World Performance Levels Defects Per Sigma Level In 1 In 3 In 6 Million Situation/Example Sigma Sigma Sigma World World World 1 690,000 Pieces of your mail lost per year 1,106 107 <1 2 308,537 [1,600 per year] 3 66,807 Number of defective iphones 4 6,210 24M 2.4M 119 [35,000,000] (2019) 5 233 6 3.4 Number of telephone 4,839 467 0.02 disconnections [7,000 talk minutes] Number of airplane incidents in Toronto Airport with 39000 flights 26,910 2605 0.9 in 2019 What is Six Sigma? Reduce Goal Variation o Reduce process variation o Reduce defects o Improve quality Focus Shift the Six Sigma o Data driven appraoch Effort performance o Predictable process outcome & control o Focus on customer Drill down requirements to root cause Accuracy When to use Lean ? When to use Six Sigma Use Lean & Six Sigma to stabilize Use Lean to reduce the new process waste & maximize flow to reach to process capacity Process Use Six Sigma to get to capability next level Process stabilization & performance consistency How does it help me? Systematic Data Driven Team Based Experiential Problem Approach Approach Learning Solving Develop the Critical Thinking for Being in Continuous Improvement Improves Business Analysis Reduces Project Cycle Time Delivers Better Bottom Line Part 2. Data! Data! Data! Typical Mindset in Problem Solving Problem Occurs we assume what cause the problem Solutions generated We assert in knowing the root cause are another version of the same thing. It We assert in knowing the solutions makes no difference Our Past Our Past We insist the current way of doing thing is the Experience correct way Einstein Quote Lean Six Sigma Approach to Problem Solving Practical Data gives us Problem Traditional access to Approach discover what the facts to the problem Data/Statistical are… Problem Lean & Six Sigma Approach Data/Statistical Solution Lean Six Sigma = take a Business Problem… * translate it into a Statistical Problem… Practical * from which a Statistical Solution is derived … Solution * and translated back into a Business Solution The Problem Solving Equation (X ) (X ) (X ) Y = f (x) 10 7 4 (X ) Output of a process Factors of the process 1 (X8) (Business Metric) = that affect the output (X3) (X5) (X ) Y = f (x1+x2+x3….) 9 There are many factors within the process. Lean Six Sigma interested in factors that are most significant influences on the output (X ) 2 (X6) We use a variety of Lean Six Sigma (X ) tools to help find the vital few 11 variables that have the biggest impact. The Organizational Process Level Key Results Area Mission and Critical to Customer Vision Requirements 5-Year Business Plan Improvement Program Success Metrics (KPIs) Support processes: Maintenance, Supply, Finance, Human Resources, IT, Communications, Water, Energy, Safety, Environment Level 0 Long Term Marketing & Explore Drill and Load and Sorting and Core Business Strategic Processing Portfolio & Acquire Blast Haul Valuation Processes Planning Management Process Process Process Process Process Process Process Metrics Metrics Metrics Metrics Metrics Metrics Metrics Level 1 Processes Raw Ore Primary Crush Cone Crusher Scrubber HPGR HMS Convey to Sort Level 2 Processes Detailed Process Map – Highest Project Level – often Projects are at an even lower level Drilling Down to Define the Problem Slicing the data into logical categories can be used to narrow the focus to the right size ThisCost byis Categoryhow you eat an elephant 100 200,000 80 t s n r 60 e a l l c r o 100,000 e D 40 P Pareto20 Chart for External COPQ by Type 100 0 5000 0 n tio al al on n rn rn ti ve – 80 c e Category xte nte te 4000Pr E I De “One bit at a time” t Amount ($) 106,000 76,000 53,000 t 0 Pareto60 n Chart for External Accuracy Defects n 3000 e u Percent 45.1 32.3 22.6 0.0 3500 c r 100 o Cum % 45.1 77.4 100.0 100.0 e C 2000 3000 40 P 80 2500 1000 20 t t 60 n n 2000 e u c 0 0 r o e C 1500 y s 40 P c s rs ra ine e cu ml th Defect Ac Ti O 1000 Count 4672 300 226 20 500 Percent 89.9 5.8 4.3 Cum % 89.9 95.7 100.0 0 0 fo r t s In be n tie r m rs ou al me u he m n to t N t Defect A Pe s cc O Cu A Count 877 855 845 823 22 Percent 25.6 25.0 24.7 24.1 0.6 Cum % 25.6 50.6 75.3 99.4 100.0 Use Data to Drill Down to Projects! KPA = Process Plant Production KPI = Recovery – Maximise to meet Customer demand - % Increase KPI Gap = Aspiration (Target) – Baseline Level 0 = Recovery (%) (BC) Increase Increase Head Process Metrics Level 1 = Flotation Business Case(s) Grades (g/t) Recovery (%) Potential Projects = Improvement Projects Improve Improve Install Rougher = Primary Metric Recovery Resource Bigger Cells Build Heavy Definition Medium Use Improve Improve Plant Statements Better Scavenger Grade Reagents Recovery Control Problem /Opportunity Problem Business Excellence One business case linked to a key business imperative can2009 spawn several narrowly Page 20 scoped projects Account Receivable: Drill Down to Projects! KPA = EBIT KPI = Revenue per month Account KPI Gap = Aspiration (Target) – Baseline Level 0 = Receivable per month (BC) # Invoice Bill to Process Metrics Level 1 = # Open Billing Business Case(s) customer Potential Projects = Improvement Projects Over the = Primary Metric Billing Accuracy of Counter Preventive Cycle time Billing Reactive Maintenance Maintenance Service Service Statements Part order Top vendor Part order Flat Rate Tech Missing Info ship billing Problem /Opportunity Problem with WO Billing behaviors for billing freight requirement One business case linked to a key business imperative can spawn several narrowly scoped projects Problem Solving Methods Six Define Measure Analyze Improve Control Sigma Lean Plan Do Check Act BA Describe Identify Evaluate Solution Control Identify & Identify Gather Analyze Improve IT define Solutions problem Data Data Solutions Plan Implem- entation Test Solutions Lean Six Sigma Tool Map At every step of the project, DATA is used to map the problem, process, root cause, and find solutions.
Details
-
File Typepdf
-
Upload Time-
-
Content LanguagesEnglish
-
Upload UserAnonymous/Not logged-in
-
File Pages28 Page
-
File Size-