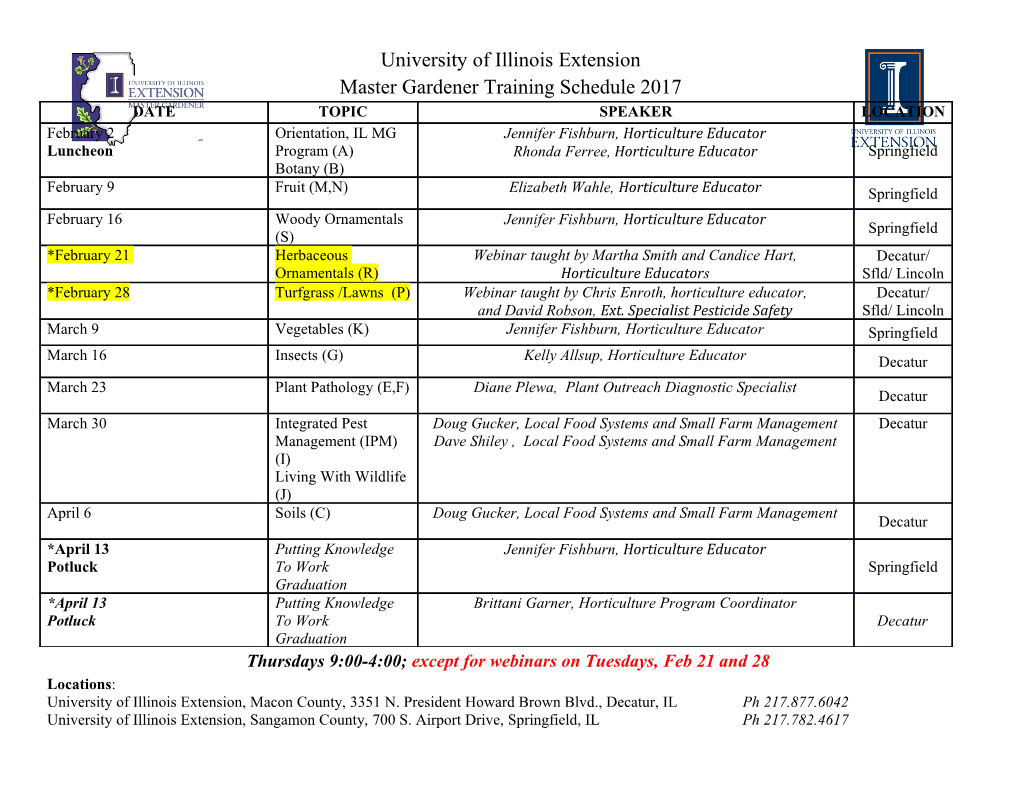
materials Article Effects of Sintering Conditions on Structures and Properties of Sintered Tungsten Heavy Alloy Lenka Kunˇcická 1,2,*, Radim Kocich 2 and Zuzana Kleˇcková 2 1 Institute of Physics of Materials, CAS, 61662 Brno, Czech Republic 2 Faculty of Materials Science and Technology, VŠB-Technical University of Ostrava, 70833 Ostrava 8, Czech Republic; [email protected] (R.K.); [email protected] (Z.K.) * Correspondence: [email protected]; Tel.: +420-532-290-471 Received: 27 April 2020; Accepted: 18 May 2020; Published: 19 May 2020 Abstract: Probably the most advantageous fabrication technology of tungsten heavy alloys enabling the achievement of required performance combines methods of powder metallurgy and processing by intensive plastic deformation. Since the selected processing conditions applied for each individual processing step affect the final structures and properties of the alloys, their optimization is of the utmost importance. This study deals with thorough investigations of the effects of sintering temperature, sintering time, and subsequent quenching in water on the structures and mechanical properties of a 93W6Ni1Co tungsten heavy alloy. The results showed that sintering at temperatures of or above 1525 ◦C leads to formation of structures featuring W agglomerates surrounded by the NiCo matrix. The sintering time has non-negligible effects on the microhardness of the sintered samples as it affects the diffusion and structure softening phenomena. Implementation of quenching to the processing technology results in excellent plasticity of the green sintered and quenched pieces of almost 20%, while maintaining the strength of more than 1000 MPa. Keywords: tungsten heavy alloy; powder metallurgy; sintering; quenching; microstructure 1. Introduction Given by the requirements on high density, high strength, and favorable toughness and ductility, tungsten heavy alloys (THAs) are advantageously used for demanding applications, such as for radiation shielding, space industry components, therapeutic devices in oncology, aircraft counterbalances, or kinetic penetrators [1–3]. THAs can be fabricated via modern technologies, such as spark plasma sintering (SPS), or selective laser melting (SLM) [4–8]. However, the processing parameters, which can be varied during such procedures, are limited. Probably the most advantageous THA fabrication technology enabling the achievement of required performance of the final product combines methods of powder metallurgy and processing by intensive plastic deformation, which can preferably be performed by severe plastic deformation (SPD) methods [9–14] imparting significant grain refinement, down to the ultra-fine scale (0.1–1.0 µm, e.g., equal channel angular pressing—ECAP [15]), or even to nano-scale ( 100 nm, e.g., high pressure torsion—HPT [16]), resulting in the enhancement ≤ of mechanical and utility properties via imposing high shear strain. THAs typically consist of 90 to 97 wt. % of tungsten plus a mixture of other relatively low melting elements, such as Fe, Ni, Co, and Cu, the combination and volume fractions of which significantly influence the strength and plastic properties of the final product [17–20]. The tungsten content can be increased up to 98 wt. % to improve the strength, however, the strength usually increases at the expense of ductility; the content of matrix-forming elements lower than 3 wt. % usually supports brittleness of the final product [21]. On the other hand, increasing the addition of alloying, i.e., matrix-forming, elements generally decrease strength, but increase ductility [22]; high contents of Materials 2020, 13, 2338; doi:10.3390/ma13102338 www.mdpi.com/journal/materials Materials 2020, 13, 2338 2 of 11 Materials 2020, 12, x FOR PEER REVIEW 2 of 12 matrix-formingforming elements elements contribut contributee to uneven to unevenshape of shape the cross-section of the cross-section of the sintered of the sintered piece due piece to gravity due to gravitysedimentation sedimentation during duringsinterin sintering,g, and consequentl and consequentlyy to non-uniformi to non-uniformityty of mechanical of mechanical properties. properties. THAs are mostly consolidated from initial powder mixtures through powder metallurgy techniques; preferably via liquid phase sintering (LPS) [[23]23],, the boundaries of thethe grainsgrains during which meltmelt andand ensure ensure binding binding of of the the tungsten tungsten particles particles and and elimination elimination ofporosity of porosity via diviaffusion diffusion [24]. LPS[24]. oLPSffers offers the advantages the advantages of a relativelyof a relatively low processinglow processing temperature, temperature, favorable favorable densification densification and structureand structure homogenization, homogenization, high high productivity, productivity, and and minimum minimum production production waste waste (< (<5%) 5%) [ 25[25].]. Under optimized sinteringsintering conditions, conditions, the the W andW and NiCo NiCo phases phases are homogenously are homogenously distributed distributed and the and sintered the piecesintered contains piece nocontains visible no pores visible [7]. pores Sintering [7]. Sintering is typically is typically performed performed at temperatures at temperatures between 1000between and 15001000 ◦andC to 1500 ensure °C melting to ensure of themelting matrix-forming of the matrix-forming binding elements binding [22 ,26elements,27]. The [22,26,27]. green sintered The green THA worksintered pieces THA typically work pieces feature typically high density feature (16–18 high density g cm 3), (16 and–18 relatively g·cm−3), and high relatively strength andhigh plasticity. strength · − Nevertheless,and plasticity. besidesNevertheless, the chemical besides composition,the chemical composition, the absolute the values absolute of the values mechanical of the mechanical properties afterproperties sintering after depend sintering on depend the character on the of character the sintered of the structure, sintered and, structure, last but and, not last least, but also not on least, the subsequentalso on the subsequent processing stepsprocessing (the mechanical steps (the properties mechanical of properties THAs can alsoof THAs be enhanced can also by be post-sintering enhanced by deformationpost-sintering processing). deformation processing). The presentedpresented workwork deals deals with with the the eff effectsects of sinteringof sintering conditions, conditions, sintering sintering temperature, temperature, and timeand intime particular, in particular, and possible and possible quenching quenching on the on structure the structure and basic and mechanical basic mechanical properties properties of the studied of the WNiCostudied tungstenWNiCo tungsten heavy alloy. heavy The alloy. primary The primary goal is to goal optimize is to optimize the sintering the sintering procedure procedure in order toin provideorder to theprovide best possiblethe best startingpossible conditionsstarting conditions for subsequent for subsequent deformation deformation processing. processing. 2. Material Materialss and Methods The investigated 93W6Ni1Co tungsten heavy heavy alloy alloy samples samples were were prepared prepared at at Ú JPJP PrahaPraha a.s.a.s. company (Praha, Czech Republic) from a homogeneous mixture of individual powders prepared by mechanical alloying (impurities(impurities~ ~ < 13 ppm of Fe, Cr, Mo, Al, and Ca). The granulometric distribution of the powder particles within the mixture was between 2 and 4 µm, and the mean particle size was 2.78 µμmm.. TheThe scanningscanningelectron electron image image of of the the powder powder is is depicted depicted in Figurein Figure1. After 1. After powders powders mixing, mixing, the mixturethe mixture was was cold cold isostatically isostatically pressed pressed at 400 at MPa, 400 MPa, and subsequentlyand subsequently prepared prepared in the in following the following steps: steps:(1) sintering under a protective atmosphere (hydrogen) at temperatures varying between 1450 and 15501) sintering◦C, with under the step a protective of 25 ◦C, for atmosphere 30 min each (hydrogen) (the temperature at temperatures range was varying suggested between by the 1450ÚJP Prahaand 1550 a.s. ° companyC, with the based step of on 25 their °C, previousfor 30 minutes experience); each (the temperature range was suggested by the Ú JP (2)Praha optional a.s. company quenching based in water-aon their setprevious of samples experience); was quenched after the mentioned sintering procedures2) optional in order quenchin to observeg in water- possiblea set changes of sampl in structureses was quenched and properties; after the mentioned sintering procedure(3) baseds in order on the to observ acquirede possibl data,e additionalchanges in experimentsstructures and with properties; variable sintering time were performed-sintering3) based on the for acquired 60 to 180 data, min, additional with the experiments step of 30 min, with at variable the sintering sintering temperature time were of 1500 ◦C, and sintering for 180 min at the sintering temperature of 1525 ◦C. Figure 1. SEM image of original powder mixture. The following structure analyses performed on cross-sectional cuts of the sintered (and possibly quenched) pieces primarily focused on structure character and possible changes in distribution of the individual elements within the structure. The transversally cut cross-sectional samples were ground Materials 2020, 13, 2338 3 of 11 The following structure analyses performed
Details
-
File Typepdf
-
Upload Time-
-
Content LanguagesEnglish
-
Upload UserAnonymous/Not logged-in
-
File Pages11 Page
-
File Size-