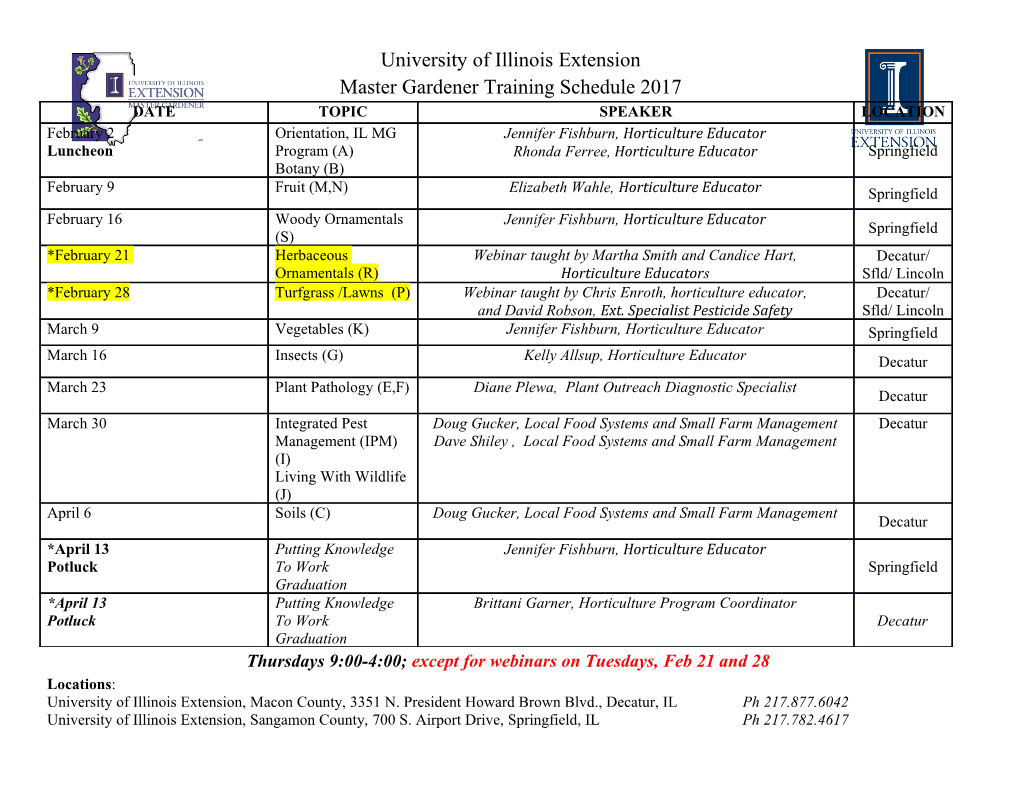
hot· Peening Before Plating? Plating tends to reduce fatigue stre·ngfth.But by shot peening before plating you can have the benefits of plating without the loss· of fatigue strength. Result: more durable parts. .. By T. J. MEISTER Metal Improvement Company, Inc. Paramus, New Jersey · f you momentarily excused your­ alone, however, since many engineers : self from your metallurgical en­ don't understand how it improves the I. gineering class, you might have durability of parts, plated and missed what little was said about a unplated. cold-working process called "con­ When faced with a fatigue failure, trolled shot peening." You aren't for example, engineers will usually I. PEENING compresses surface layer, compressively stf4!ssing it. o o o o 0 o o 0 0 0 '0 0 o o High-speed shot hits metal o 0 0 0 0 0 122 PRODUCTS FINISHING JUNE, 1987 ./1 A) redesign, re·alloy, change heat treat r--"""""'!~r:"':':'~~r------"" and so on. Overlooked is the usually more economical alternative of shot peening. Compressive Stress. Dr. Henry Fuchs and J .0. Almen observed the life-prolonging benefits of residual compressive stress left by a crude cold working operation. By controJIing Peened Surface --"-7 the variables, they found, residual' Tension o Compression f stress could be enhanced, thus dra­ \ matically improving the fatigue life 60 pet of UTS and strength of metals. Controlled shot peening is one way Residual Stress to compressively stress part surfaces. Shot peening involves bombardment 2. EFFECT of shot peening on tension . and compression. A) Typical stress . C) 50 pet Peened Surface- distribution in surface of metal beam, unloaded. It exhibits residual tensile stress from normal fabricating operations. B) Same beam after shot peening, still without external load• . Surface stress is now compressive. C) Beam, when subjected to design M= Bending Moment loading, still shows some residual on Section .compressive stress. JUNE, 1987 PRODUCTS FINISHING 123 Shot Peening Before P~ating~ ... By peening, we have increased the fa­ tigue strength. Since a part is usually designed so that it has to withstand 'Cy?'os,;?1j;:~s+}~~!\!~;~(~In~;fl no more than 50 pct of its ultimate , Bend . tensile strength, a shot-peened part's Polished (unplated) ,,-i;, /':/];'>:;;' ,;,;. 54,000 i surface remains in compression by a Shot' peened (unplated) . .:. 200,000 i factor of 10 pct (60 pct residual-50 Electroless nickel plated (unpeenedr:, 39,000' pct applied) when the designed-for Shot peened and EN plated . 141, OO~ ; load is applied. Even if the part is overloaded to 75 pct of its ultimate tensile stress, the net surface stress of metal parts with small, spherical, stilI will be only a mere 15 pct in ten­ steel, stainless steel, glass or ceramic sion (60 pct residual-75 pct applied). beads. The peening causes the surface Fig. 2 graphically shows the effect of of the part to yield (Fig. 1), residu­ shot peening on the surface of a part. ally compressing the sub-surface }i'atigue Cracking. Since nearly all layer. fatigue cracks initiate in highly Compressive stress generated by stressed af(~as at the surface, their shot peening is generally equal to 50 propagation is retarded by a com­ to 60 pct 0 f the ultimate tensile pressive layer. Fatigue cracks will not strength of the material being peened. initiate in or propagate through a 3. SHOT PEENING before chromium plating improves fatigue life, as shown by these rotating-beam tests, involving 4340 steel, 52-53 Rc. ~ 120,000 84 0 ~}~ Bt, not peened CIt 8 ( • I 100,000 \ • - 70 ..... Shot-peened, ch~omium '(i) E plated and baked E .9; ....... (/) \L I en (/) ~ ~ 80,000 l (l HARD Pl.ATING ~ ~ ( - 56 u) en VJ I l ' ::::;:E~:~~~~~~~i:J~:::n~W5:::: ~ en ~ Not Peened Basis Peened Metal 60,000 '\ I-- 42 A' x 1Chromium PlatJ and baked 40,000 28 10,000 100,000 1 Million 10 Million 100 Million Cycles to Failure 124 PRODUCTS FINISHING JUNE, 1987 compressively stressed zone. Stress­ in the plating. But those cracks will concentration sites such as machine not propagate into the basis metal. or tool marks, keyways, drilled holes, Therefore, a designer could expect to threads, splines, and induction­ see about the same fatigue life from hardening runouts all can markedly his peened and plated part that he benefit. would have anticipated had he not Shot Peen, Electroplate. One of plated it at all. By shot peening prior the more common applications of to electroplating, he makes a part shot peening is its use prior to the ap­ with excellent fatigue life as well as plication of a nickel or chromium the wear resistance, corrosion resis­ electrodeposit. Plating with such hard tance and other properties provided materials reduces fatigue strength of by electroplating. Another plus is that the basis metal by as much as 50 pet. the dimpled surface left by peening Cracking that initiates in the plating favors good plate adhesion. may subsequently propagate into the Bending type 4340 steel plated with basis material (Fig. 3). This can lead 0.001 inch of electroless nickel and to premature failure. tested at 90,000 psi exhibited the By introducing a compressive bar­ results shown in Table I. rier on the surface of the basis metal, Because of such results, the mili­ before the electroplate is applied, you tary amended Federal Specification will not prevent formation of cracks QQC-320. Any parts designed for un- 4. SHOT PEENING keeps fatigue strength from falling as carburization improves , tensile strength. 200 r-----.,.-----y-----r------r------r-----, Rockwell hardness- Rc34 Rc42 Rc50 .~ 1501-----1----4---Peened-notchedI -I1---""'2fI*'~=+-----t I Peened-smooth ~ g, 100 t------+-----+----::II"'f~C::.,,_r.:::...-+_---_t_---__t ~ (I) Q) :::s 01 ;f 501-----+-""""""'~..;"F:+---__J----_t_--=-....._---_t ".."" / Ou;..~ ,.. -'- .....L Not peened-notChed--JL..- -'-- --I- --' 100 200 300 Ultimate'tensile strength, 103 psi JUNE, 1987 PRODUCTS FINISHING 125 Shot Peening Before -Plating? .. Single-Tooth Fatigue Tests of Carburized Gears 4 G . I / Peened (.) ..... P' " - .. - Itch line --- / l_ • ~: - ) l t, ) ,.., ') .. ........ _.. -{'XForce I .. - .. ~ / No failure at I II III Not poened (0) - 5 x 106 cycles _ Loading method: 11'11 III ill gear held stationary 1 I IIII 10~ 10 7 Cycles to failure 5. CARBURIZED, peened planet gears from 4118 stock show increased load capacity. limited life, subject to dynamic loads, matically indicate the value of shot and having a hardness above Rc40 peening. In Fig. 5, the carburized and must be shot peened and baked at shot peened gears withstood 20 pct to 190.5C (375F) for not less than three 30 pct more load than the non-peened hours. The harder the part or area (as specimens. in the case of localized induction In similar tests, life-cycle improve­ r,: hardening) the greater the life­ ment was paramount on carburized ­ prolonging results of shot peening. 8620 stock. Fig. 6 shows a life­ How Much Compressive Stress? improvement factor of ten fold at a The amount of compressivestress is load level of 87,000 psi. a function of the ultimate tensile Any gear or spline is in reality strength of a material. In analysis of nothing more than a series of can­ many part failures, we have found tilever beams. Typically gears fail in that increasing part hardness, fol­ fatigue at the roots of the teeth or lowed by shot peening, will overcome near a spline runout. When a designer brittleness and notch sensitivity. Fig. must alter a part and its strength be­ 4 shows fatigue strength improve­ cause such things as turbo chargers ments of as much as 3X at Rc58. have been added, shot peening may Only when the tensile stress exerted avoid the tremendous cost of his al­ on the part exceeds the residual com­ ternatives: redesign or material pression from carburizing, for exam­ change. ple, will the part be prone over a Uesidual Tensile Stresses. Scratches, number of cycles to fatigue failure. tool marks and machining in general Tests performed on two sets of can leave behind residual tensile gears (4118 stock) clearly and dra- stresses and stress risers. Such condi- 126 PRobuCfS FINISHING JUNE, 1987 M 0..- vi en ~ en "0 ~ 70 ::l 0. E u0 60 50 5 10 Cycles to failure 10' 6. SHOT PEENING can improve fatigue life of carburized gears. tions are detrimental to parts, 150,OOO-f. "0 whether plated or unplated. They can (1) -o.c: (1) U be overcome by shot peening (Fig. 7). C:rt; (1)'­ (1) U Gear-flank frosting and high spots on a.. en the pitch line also can be negated by -0 (1) -0 .c: .peening, leaving behind the compres­ (1) U 100,000-- ~T§ sive stress and "pounding down" the (1) U 0. en '(ij ........ high spots. ' o 0 -0 0. Z Z (1)-0 c: (1) The negative effects of grinding (1).c: (1) U also can be eliminated, as shown in - ~~ (1) o U Fig. 8. Many manufacturers have :z (J) Uc: found it more economical to take a ~ 50,000 - "plunge" grind followed by shot -0c: ~ W peening rather than try to control a ~ gentle grind in a production situation. Almen Strips. Early on, both Dr. Fuchs and John Almen recognized ~..L--ILI:u:\\I\:u:\\\':u:I\IL-..J the need for. process controls to o'--..L-_..L--.L·__ achieve reliable, repeatable results in shot peening. A flat metal strip (1070 7. EFFECT of peening and scratches on endurance limit of 4340 steel at Rc51. steel) in three thicknesses (A,N,C) is used to measure the kinetic energy of ing time intervals, an intensity curve the shot stream on the target area is generated during process develop­ (Fig.
Details
-
File Typepdf
-
Upload Time-
-
Content LanguagesEnglish
-
Upload UserAnonymous/Not logged-in
-
File Pages9 Page
-
File Size-