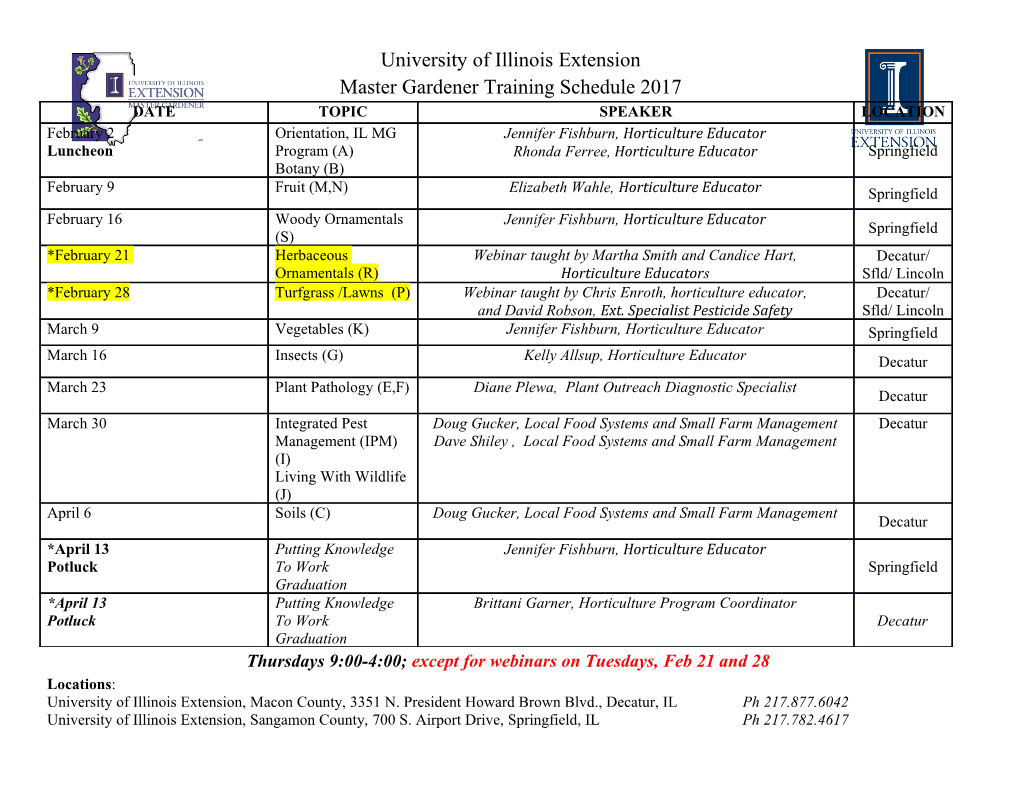
The Solidification and Welding Metallurgy of Galling-Resistant Stainless Steels The autogenous welding response of common galling-resistant stainless steels are evaluated and compared BY C. V. ROBINO, J. R. MICHAEL AND M. C. MAGUIRE ABSTRACT. The autogenous welding Introduction these alloys and case studies of welded behavior of two commercial galling-re- fabrication were discussed. Maguire, et sistant austenitic stainless steels, Ni- Conventional austenitic stainless al. (Ref. 2), examined the heat-affected tronic 60 and Gall-Tough, was steels typically display relatively poor zone (HAZ) cracking behavior of Ni- evaluated and compared. The solidifi- galling resistance in many applications, tronic 60 using gas tungsten arc weld- cation behavior and fusion zone hot- and, as a result, a variety of nonstan- ing (GTAW) and HED processing, as cracking tendency of the alloys was dard austenitic steels have been devel- well as weld thermal cycle simulations. evaluated by using differential thermal oped to overcome this difficulty. These Depending on the GTAW conditions, analysis, Varestraint testing and laser steels are normally high-silicon, high- both HAZ liquation and subsolidus spot-welding trials. Gleeble thermal manganese, nitrogen-strengthened al- cracking were observed. For HED over- cycle simulations were used to assess loys and include such grades as lapping spot welds, HAZ cracking was the hot ductility of the alloys during both Nitronic 60, Gall-Tough and Gall- observed under essentially all process- on-heating and on-cooling portions of Tough PLUS. Fusion welding of these ing conditions. weld thermal cycles. Solidification mi- alloys by conventional filler metal pro- There have been a number of investi- crostructures were characterized by cesses such as shielded metal arc (SMA) gations of the weld solidification behav- light optical and electron microscopy, and cold wire feed gas tungsten arc ior, solidification mode and weld and the solidification modes and phases (GTA) welding is normally not prob- cracking behavior of nitrogen-alloyed were identified. Gas tungsten arc (GTA) lematic (Ref. 1). For these processes, and high-manganese, nitrogen-strength- welds in both alloys solidified by the fer- standard filler metals (e.g., E/ER 240 ened stainless steels (Refs. 3-7). In addi- ritic-austenitic mode, and their behavior and E/ER 308) and specially developed tion, there have been several was best described using chromium and fillers (e.g., ER 218) generally provide comprehensive reviews detailing the nickel equivalents developed specifi- satisfactory welding response and many aspects pertaining to the welding cally for the Nitronic series of alloys. weldment performance; however, in sit- of austenitic stainless steels (Refs. 8, 9). Both alloys were found to be somewhat uations requiring autogenous and/or In general, the results of these works in- more susceptible to solidification hot high-energy density (HED) processing, dicate that the effects of manganese and cracking than conventional austenitic the solidification behavior and cracking nitrogen can be rationalized with current stainless steels, although the cracking tendency of the alloys is important. austenitic stainless steel theory, although resistance of Nitronic 60 was somewhat The autogenous weldability of this the roles of these elements are relatively superior to Gall-Tough. Laser spot- class of alloys has not been reported in complex (Ref. 5). welding trials resulted in both fusion the literature, although the general In the case of the three alloys men- and heat-affected zone cracking in the welding behavior of Nitronic 60 was tioned above, the alloy design approach Nitronic 60, while Gall-Tough was re- evaluated by Espy (Ref. 1 ). In that work, appears to be similar, although there are sistant to cracking in these high-solidifi- Espy developed a modified Schaeffler some differences in the balance of alloy cation-rate welds. Comparison of the diagram to describe the ferrite content additions. These differences are most laser weld microstructures indicated of welds in the Nitronic series of alloys. distinct between Nitronic 60 and Gall- that Nitronic 60 shifts to fully austenitic In addition, mechanical properties for Tough, while the Gall-Tough PLUS alloy solidification, while Gall-Tough shifts to is generally similar in composition to an austenitic-ferritic solidification mode Nitronic 60. The Gall-Tough alloy is bal- in high-energy-density processing. The anced to a somewhat higher Creq/Nie~ ratio than Nitronic 60, which implie~ hot ductility measurements indicated KEY WORDS that Gall-Tough is generally superior to that higher as-solidified ferrite contents Nitronic 60 in both on-heating and Galling Resistant are likely and that the autogenous weld- on-cooling tests, apparently as a result GTAW ability of the two alloys may be differ- of differences in grain size and the Hot Ductility ent. Therefore, the purpose of the mechanism of ferrite formation at LBW present study was to evaluate and com- high temperatures. Solidification pare the solidification and autogenous Stainless Steels weldability of Nitronic 60 and Gall- Varestraint Testing Tough alloys. Fusion, HAZ behavior and C V. ROBINO, J. R. MICHAEL and M. C Weldability laser weldability were examined and MAGUIRE are with Sandia National Labora- evaluated. tories, Albuquerque, N.Mex. 446-S I NOVEMBER 1998 Experimental Procedure tility testing performed on a Gleeble also used on selected samples. In this 1500 thermomechanical simulator. This case, samples were polished (or polished The alloys used in this study were test subjects the alloy to a simulated and etched) sections and were generally from commercial heats of Nitronic 60 HAZ thermal cycle, which is interrupted examined in the backscattered electron and Gall-Tough, and the compositions of by rapid fracture during either the on- or secondary electron imaging modes, the heats are shown in Table 1. From heating or on-cooling portion of the ther- respectively, in a JEOL 6400 or Hitachi these heats, samples for differential ther- mal cycle. The thermal cycle used was $4500 SEM operating at 20 kV. Identifi- mal analysis, hot ductility testing, and determined from the Gleeble software cation of microstructural constituents Varestraint testing were machined. All and represents a cycle very close to the was conducted by combinations of AEM, heats were tested in the mill-annealed fusion boundary of a 3.94 kJ/mm weld in electron microprobe analysis (EPMA) condition. Table 1 also shows the com- a 12.7-mm-thick plate. The peak tem- and through the use of backscattered positions of the 304L and 316 stainless perature for these tests was approxi- electron Kikuchi patterns (BEKP) in the steels used for comparison of hot-crack- mately 15°C (27°F) below the SEM (Ref. 13). ing response. nil-strength temperature (NST), although Electron probe microanalysis was per- Differential thermal analysis (DTA) the effect of peak temperature was also formed on a JEOL 8600 electron micro- experiments were performed using a evaluated in several cases. The NST was probe X-ray analyzer operating at 15 kV, Netsch STA 429 thermal analyzer on determined by imposing a tensile load of a spot size of approximately 1 pm and samples of approximately 750 mg mass. approximately 175 N on a hot ductility beam current of 25 nA. Elemental com- Tungsten (>99.99% purity) was used as sample and ramping up the temperature position data was determined by estab- the reference material. Both the refer- at 100°C/s (180°F/s) until sample failure. lished ~(pz) algorithms with integrated Kct ence and the samples were held in high The hot ductility samples were 6.35- X-ray intensities (Ref. 14). BEKP analysis purity alumina crucibles during testing. mm-diameter rods. During hot ductility was conducted on a JEOL 6400 SEM All tests were run in a flowing-helium at- testing, the samples were loaded at a equipped with a custom-made charge mosphere at heating and cooling rates of crosshead velocity of 2 cm/s and ductil- coupled device (CCD) based detector for 0.33°C/s (0.59°F/s). The peak tempera- ity was measured as the reduction of BEKP (Ref. 13). Patterns were collected at ture during testing was approximately area at the fracture surface. an accelerating voltage of 20 kV and a 1500°C (2732°F). Previous experience As-received material, DTA samples beam current of 1 nA and were obtained (Ref. 1O) with this equipment and proce- and welds were examined by light opti- by stopping the beam on a feature of in- dures indicated that a reproducibility of cal metallography. Sample preparation terest and collecting a BEKP by exposing approximately 2°C (3.6°F) in measured for the microstructural examinations in- the CCD camera for 10-20 s. Phase iden- temperatures could be expected. Inter- cluded mounting and polishing through tification was accomplished by auto- pretation of the DTA curves was con- 0.05-pm colloidal silica using standard matic extraction of the important ducted using the convention established metallographic procedures. Samples crystallographic information from the by Maclssac, et al. (Ref. 11 ). were electrolytically etched using a 10% patterns. The crystallographic parameters Susceptibility to fusion-zone hot oxalic acid solution at room temperature are then used in conjunction with quali- cracking was quantified using the longi- and 6 V. Ferrite fraction measurements tative chemical information determined tudinal Varestraint test (Ref. 12). Vare- were conducted using a calibrated mag- by EDS analysis to search a crystallo- straint samples measuring 165 x 25 x negage. Analytical electron microscopy graphic database. Once a candidate 3 mm were fabricated with the long (AEM) was used for further characteriza- match is obtained, the patterns are simu- dimension parallel to the plate rolling tion of selected samples. For these anal- lated and the simulation is compared direction. Autogenous GTAW was used yses, thin foil specimens were prepared with the original pattern. in the tests.
Details
-
File Typepdf
-
Upload Time-
-
Content LanguagesEnglish
-
Upload UserAnonymous/Not logged-in
-
File Pages12 Page
-
File Size-