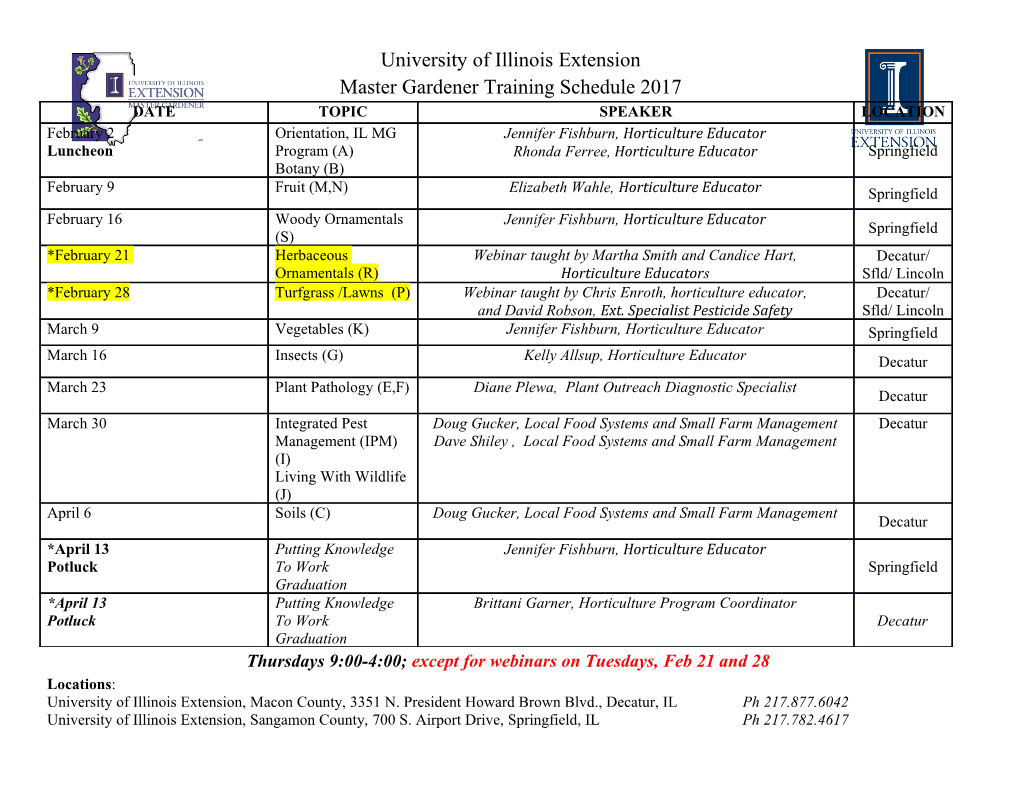
Maintenance Planning Optimisation for the Boeing 737 Next Generation Masters Thesis By ir. Anthony K. Muchiri Supervisors: Prof. ir Klaas Smit ing. Willem van Steenis Delft/ Schiphol East, 30 May 2002 Colophon Colophon Final Report Title: Maintenance Planning Optimisation for the Boeing 737 Next Generation Author: Anthony K. Muchiri Date: Thursday, 30 May 2002 Board Of Examiners: Prof. Ir. K. Smit - TU Delft (Coach) Ir. B. Agusdinata - TU Delft ing. W. van Steenis - Transavia Airlines (Supervisor) Ir. R. Hol - Transavia Airlines Delft University of Technology Transavia Airlines Faculty of Aerospace Engineering Technical Department Department of Industrial Engineering Maintenance Planning & Support and Technical Management P.O. Box 7777, 1118 ZM Schiphol Airport P.O. Box 5058, 2600 GB Delft The Netherlands The Netherlands i Preface Preface This thesis represents the results of my graduation assignment, a research project carried out to conclude the Master Phase of the Industrial Engineering Department, Faculty of Aerospace Engineering, of the Delft University of Technology. The assignment was assigned and carried out at the Maintenance Planning and Support (MP& S) department of Transavia Airline’s Technical Department, and it entails the optimisation of maintenance planning for the 737 Next Generation fleet of the airline. The report has been subdivided into five chapters, and it can be read as follows: - For readers interested in the development of a new maintenance planning strategy, Chapters 3 and 4.4 are recommended - For readers interested in the analysis of the current situation and the proposed situation, it is recommended that they read Chapter 4.4 - For readers interested in the conclusions and recommendations, they should look at Chapter 5 - For readers interested in the development of the whole research, all chapters and Appendix documents are recommended. A summary highlighting all major items from the report has also been included In all cases, some knowledge on aircraft maintenance is needed. I would also like to take this opportunity to thank my professor, Prof. Ir. K. Smit of the TU Delft, and my supervisor, Mr. W. van Steenis, Maintenance Manager Transavia Airlines, for their coaching and encouragement. My thanks also go to all staffers of the MP&S department for their assistance and for the good time they gave me at the department, the head of Engineering, Mr. R. Hol, all maintenance engineers - and especially the maintenance programme engineers, and all members of the technical department for their corporation. Anthony Muchiri Delft, May 2002 iii Executive Summary Executive Summary With the increasing need to reduce maintenance costs and increase aircraft availability, the need to simplify the way maintenance is planned and executed has become a major issue in the aircraft industry. Aircraft manufacturers continue to develop aircraft with a low maintenance demand, while airlines strive to keep their maintenance costs as low as possible. The Boeing 737 Next Generation (737 NG) is an example of such an aircraft, developed to demand less maintenance, as compared to previous versions of the Boeing 737 series. This 737 NG aircraft has a Maintenance Planning Data (MPD) document that is based on the Maintenance Steering Group (MSG)-3 philosophy. This is a task-based maintenance philosophy that looks at maintenance more at a task-level, as compared to previous philosophies, which were more focused on maintenance processes. Transavia airlines currently possesses 13 737 NG aircraft, but has a maintenance program that strongly borrows from other aircraft models in its fleet (namely the B 757-200 and the B 737-300). This assignment is aimed at developing a cost-effective maintenance planning and packaging method that will lead to the reduction in direct maintenance costs, yet maintaining the reliability of the 737 NG fleet. Maintenance Planning and Scheduling Background Maintenance at Transavia is broadly categorised into Line Maintenance (maintenance performed within Transavia), and Base Maintenance (Maintenance work contracted out). Line maintenance is performed at short intervals (given in weeks). Currently, line maintenance is performed at a frequency of 5 weeks. Every line maintenance visit is planned in a so-called hangar slot. A single hangar slot is 7.75 hours long and it can produce 55 maintenance man-hours, while 2 slots produce 100 man-hours. Three slots lead to 300 man-hours. Each aircraft receives 14 maintenance slots a year for routine line maintenance. These slots have a repeating distribution rhythm of 1-1- 2-1-1-3-1-1-2-, and are also planned in this rhythm. However, the realisation of the planning for these slots deviates from the pattern above. A reason for this may be attributed to the dependence of maintenance on the utilisation of the aircraft, unpredictable events, large work packages that are not executable within the stipulated time, and aircraft operations. Base maintenance is performed every 1½-years (18 months). Transavia has an operational pattern that is strongly seasonal (high between April –October, and low between November - March). Base maintenance is preferably planned in the low season, because it requires aircraft to be withdrawn from operations for multiple days. However, a frequency of 18 months will always lead to maintenance due dates that fall in the high season. This problem is solved by performing the maintenance in advance (at 16 or 17 months), an undesired situation. Maintenance Clusters Definition and Development Clustering is the process of grouping maintenance tasks together into packages that can be planned in for execution. Clustering can be done by following two v Maintenance Planning Optimisation: B737 NG approaches, namely the Top-Down approach (answering the questions When maintenance and What maintenance), and the Bottom-Up approach (answering the questions What maintenance and When maintenance). The Bottom-Up approach begins by evaluation what maintenance has to be done. By considering that the MPD document is a task-based maintenance document, a look is taken into the properties of each maintenance task. Thereafter, all tasks requiring the same fixed conditions/procedure/cost, and the same maintenance interval limit, are grouped together to form Maintenance Task Packages. This applies to all maintenance tasks intended for line maintenance (at Transavia). All other tasks are grouped together based on their maintenance interval, and become Base Maintenance Checks. This process is illustrated in Figure 0. 1 below. OMP Maintenance Tasks Line? Base? Line Maintenance Base Maintenance Tasks Tasks Transavia L/B Classification Criteria Set-up properties Maintenance Intervals (CT/FH/FC) Maintenance Maintenance Task Packages Checks Figure 0. 1 Creation of Line Maintenance Task Packages and Base Maintenance Checks The Transavia Line/Base classification criteria classifies all tasks, for which Transavia is equipped to perform, has the certified personnel and materials needed, as line maintenance tasks. All other tasks are base maintenance tasks. The next step in the Bottom-Up approach is to determine when the Maintenance Items (Maintenance Task Packages or Maintenance Checks) are due for performance. This follows from combining the aircraft utilisation (flight hours and flight cycles) and calendar with the maintenance interval limits of the various Maintenance Items. The Top-Down approach begins by analysing the aircraft utilisation requirement at an annual, weekly and daily level. The annual level reveals a seasonal pattern while the weekly and the daily levels do not reveal specific patterns. Slot allocation follows these patterns; fixed slots are allocated at an annual level (for line and base maintenance). Ad-hoc slots can be located at a weekly and daily level (for base maintenance). Cluster Formation and Evaluation Through the implementation of the Bottom-Up and the Top-Down approach, Maintenance Task Packages and Maintenance Checks can be grouped together into maintenance clusters. Such clusters can either be static (base maintenance clusters) or dynamic (line maintenance clusters) vi Executive Summary The clustering process is done using a computer model, developed in Visual Basic and MS Excel. The model combines maintenance item intervals with simulated aircraft utilisation scenarios (high, average and low utilisation) and maintenance scenarios (such as low maintenance frequencies). From these, the Maintenance Demand (in number of visits and maintenance man-hours) is calculated. Further, the model also calculates losses following from maintenance performed before the interval limits are reached. Line Maintenance clusters are evaluated for frequencies ranging between 4-6 weeks, for a period of 6 years (starting from 2001, where an assumption of aircraft introduction is made). Frequencies above 6-weeks would lead to the escalation of maintenance interval limits. It is observed that line maintenance is strongly utilisation dependent (in terms of flight hours and flight cycles). The results of the evaluation are tabulated in Table 0. 1 below. It follows that the maintenance demand decreases with a decreasing maintenance frequency, as does the de-escalation. Table 0. 1 Maintenance man-hour demand per aircraft by a varying maintenance frequency Line Maintenance Man-hour demand De-escalation (in man-hours) 4-weeks 5-weeks 6-weeks 4-weeks 5-weeks 6-weeks 2001 440 409 362 27 11 17 2002 734 684 626 51 37 48 2003 821 705 606 60 31 33 2004 762 664 584 55 29 28 2005 634
Details
-
File Typepdf
-
Upload Time-
-
Content LanguagesEnglish
-
Upload UserAnonymous/Not logged-in
-
File Pages183 Page
-
File Size-