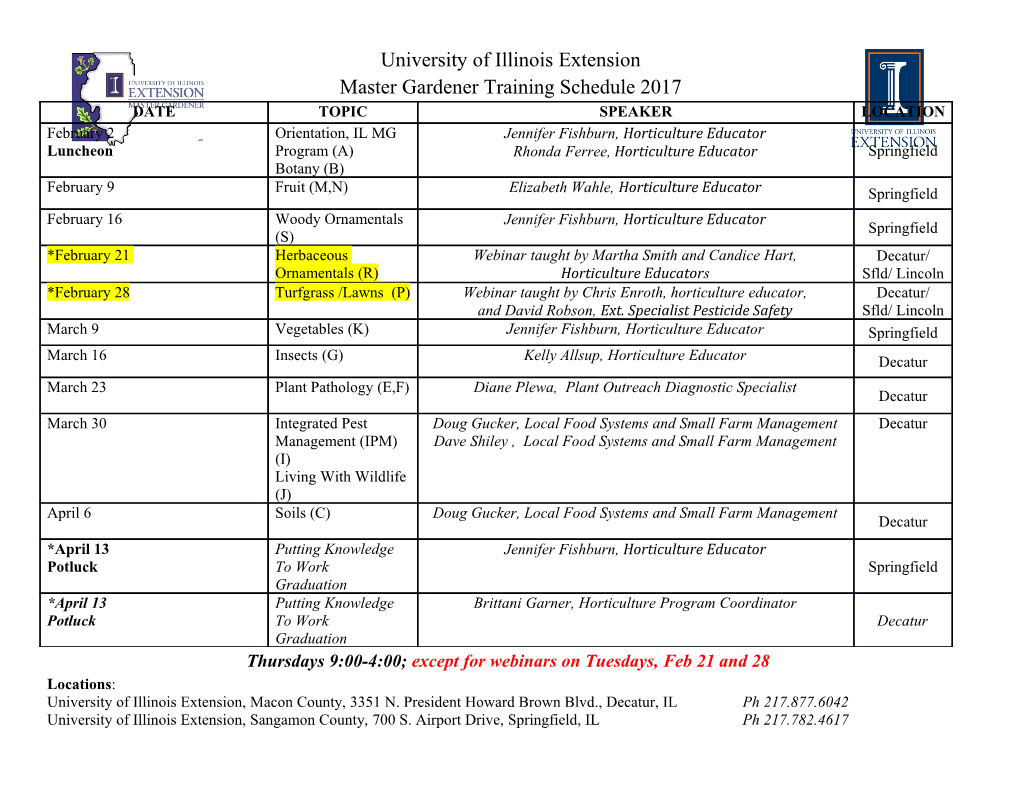
Towards Legged Amphibious Mobile Robotics Chris Prahacs*, Aaron Saunders**, Matthew K. Smith*, Dave McMordie**, Martin Buehler** * Mechanical Engineering **Boston Dynamics McGill University Cambridge, MA, USA Montreal, QC, Canada {aaron, mcmordie, buehler} {chris.prahacs, matthew.smith}@mail.mcgill.ca @BostonDynamics.com Abstract—New areas of research focus on bridging the gap between mobile robotics on land and at sea. This paper describes the evolution of RHex, a power-autonomous legged land-based robot, into one capable of both sea and land-based locomotion. In working towards an amphibious robot, three versions of RHex with increasing levels of aquatic capability were created. While all three platforms share the same underlying software, electronic and mechanical architectures, varying emphasis on aspects of similar design criteria resulted in the development of varied platforms with increasing ability of amphibious Figure 1. – Research-RHex platform navigation. The current Research-RHex is a compact and agile hexapod robot able to walk and run up to 2.7 m/s 1. Introduction and Background on flat terrain [3], traverse highly varied outdoor environments, climb slopes over 40 degrees, and Legged robots have long captured the traverse railroad tracks, brush and brambles. RHex’s imagination of researchers for the promise, motivated construction demonstrates that an exceptionally agile by observations of animal locomotion, for outstanding robot can result from the combination of simple rough terrain mobility and versatility. Yet, artificial compliant and recirculating legs, each with only one legged machines of the past were hard pressed to actuated degree of freedom, driven in a clocked, open- compete in terms of outdoor rough terrain mobility loop manner [1]. even with similarly sized tracked and wheeled The first RHex was constructed on an open vehicles. This is about to change, thanks to aluminum frame with bent Delrin legs coupled directly improvements in actuation, sensing, materials, to the motor/gear output shafts. Control was computation, and most importantly, our understanding accomplished with an eight-card PC/104 computer of locomotion. A product of these improvements and stack (standard industrial computer format) running understanding has been RHex, a six-legged robot, [1, Proportional-Derivative servo and gait-generation 2] which is currently the most agile and versatile software in a 1 kHz loop. This simple embedded untethered legged robot in existence (www.rhex.net). system controlled its actuators via a custom-designed It was developed from 1999 – 2004 in an inter- motor control and breakout boards and a custom university collaboration between McGill and several breakout board. Power was supplied from two 12 V US universities, with sponsorship from DARPA. sealed lead acid batteries. The first version of RHex RHex has continuously improved over the years, and weighed 7 kg [2] and was able to walk at about 0.5 we will refer to the many iterations that have not been m/s for over fifteen minutes on one battery charge. It waterproofed (but have been ruggedized considerably) was able to demonstrate exceptional mobility over as “Research-RHex”. This paper takes Research-RHex obstacles exceeding its body clearance. Yet failures as a point of departure and describes subsequently the were common, with fractures of the Delrin legs, motor RHex versions that were waterproofed and further shaft slippage and connector problems being the most ruggedized. frequent. Design refinement reduced the mass of RHex to about 6 kg, increased the run time to over 30 minutes and liberated much of the internal volume occupied by 2.1. Shell Design the PC/104 stack, motor drive and I/O card. Versions Composites were chosen as the shell material of this platform demonstrated stair climbing [4], because of their high strength-to-weight ratio as well pronking [5], bounding [6], flipping [7], pipe-traversal as their amenability in conforming to complex behaviours, and even a bipedal running mode [8]. A 3- curvatures. Specifically, carbon fiber was selected axis laser gyro and onboard vision system were later over Kevlar for its non-hydroscopic properties. added to provide sufficient feedback for self-servoing Indeed, the final shape chosen for the shell was abilities, including online autonomous gait parameter composed entirely of curved surfaces for several optimization [3]. reasons: As the mobility and performance of the research 1. They allow for the more even distribution of platform improved rapidly, it became apparent that the impact loads. original open aluminum frame, even with the addition 2. They reduce hydrodynamic drag while swimming. of a Lexan cover (see Figure 1), would not be 3. They decrease the likelihood of the platform sufficient for rigorous outdoor testing in uncontrolled getting ‘caught up’ on obstacles during land-based environments. The platform now routinely operation. encountered such hazards as rain, mud, sticks and 4. They provide a pleasing aesthetic more sand, and often fell from heights greater than 30 cm. reminiscent of biological organisms. Moreover, in an early display of legged robot While the carbon fiber shell was being versatility in 2001, RHex’s body was sealed and designed, hip sealing tests were performed using the demonstrated for the first time amphibious abilities. It research platform. Since the robot’s ‘hip’ design at the walked from a sandy beach into a lake, swam using its time consisted simply of clamping a leg directly to the unmodified legs on the surface, and walked back out output shaft of the motor gearhead, small rubber o- on land over slippery rocks. rings had to be used to seal the rotating shafts, since This experiment, combined with the RHex standard rotary seals were not available in the project’s mandate to demonstrate increased necessary diameter. ruggedness and reliability in all outdoor environments, However, while the shell design was underway, initiated the development of three new successive the hip was also redesigned to improve durability robot designs: Shelley-RHex, Rugged-RHex, and through the addition of a bearing supported shaft AQUA. These three platforms, described in the sequel, collar. The bearing increased the hips’ robustness, each served to increase the platforms’ waterproofing eliminating shaft failures due to bending loads, while and/or ruggedness. increasing the diameter of the hip’s sealing surface enough to allow for the use of standard single-lip 2. Shelley-RHex rotary seals. Initially made from titanium to satisfy dynamic seal surface hardness specifications, later versions of the shaft collar were fabricated in stainless steel with no apparent reduction in performance. In order to slide over the motor assembly shaft, an internal ‘D’ shaped hole was cut using wire electrical discharge machining (EDM) through the full length of the shaft collar. The gap between the shaft collar and motor assembly shaft was designed at 0.005” in order to allow for ease of assembly and Figure 2. - Shelley-RHex platform because it was specified as the optimal gap (in terms of strength) for the removable 2-part acrylic glue In order to protect the electronics from impact, selected to bond them. Threads were then added to the dirt and moisture, a project was undertaken to replace external end of the shaft collar in order to allow for Research-RHex’s open frame with an enclosed shell. disassembly. Removal of the shaft required heating the Loose specifications for the shell prescribed that it assembly above 250F for several seconds and should withstand high impact loads while not ‘pushing’ the motor assembly shaft out of the shaft significantly increasing the weight or size of the robot, collar using a modified bolt inserted into its threaded and that it should be waterproof enough that the end. platform would be able to operate amphibiously. The shell’s ‘one-piece’ design necessitated the use of a removable body panel to replace batteries and provide access to the electronics. This panel was originally sealed using common weather stripping and These factors resulted in the under utilization of screws to apply sufficient clamping force. As the shell the developed platform. Due to the aforementioned was tested, however, this design was improved costs of modifications to the shell design, the above through the use of a hollow rubber extrusion for better issues were not addressed until the creation of the sealing and quarter-turn fasteners to improve ease and subsequent platform. speed of accessibility. The broad design goals for the next platform Other sealing issues arose through the need to were quite similar to those of Shelley-RHex, to use an external power switch, and from the antenna’s develop a highly mobile platform that could walk or interface with the shell. In the former case, an swim in most weather conditions. The material and appropriate waterproof switch could not be found with sealing problems experienced with Shelley-RHex, the sufficient amperage rating so a recessed standard desire to improve ease of platform maintainability and automotive switch was used and sealed using a design iteration, motivated differences in the emphasis clamped elastomeric film. The antenna was sealed by and the details of the chosen development goals and simply smearing its mounting flange with silicone constraints. What followed was a radically different caulking during assembly. platform, known as Rugged-RHex. While the shell provided the electronics with impact, debris and moisture protection from the 3. Rugged-RHex environment, increasingly rigorous testing of the platform still subjected them to damaging vibrations. Neoprene dampers were used as an interface between the electronics and the shell in order to mitigate these effects. While use of the shell increased platform length by 3 in. and width by 1 in., it actually became slightly thinner than the research version, thus increasing ground height and obstacle avoidance. This design tradeoff was achieved by splitting the PC/104 stack in two, and connecting the two halves using a ribbon cable.
Details
-
File Typepdf
-
Upload Time-
-
Content LanguagesEnglish
-
Upload UserAnonymous/Not logged-in
-
File Pages10 Page
-
File Size-