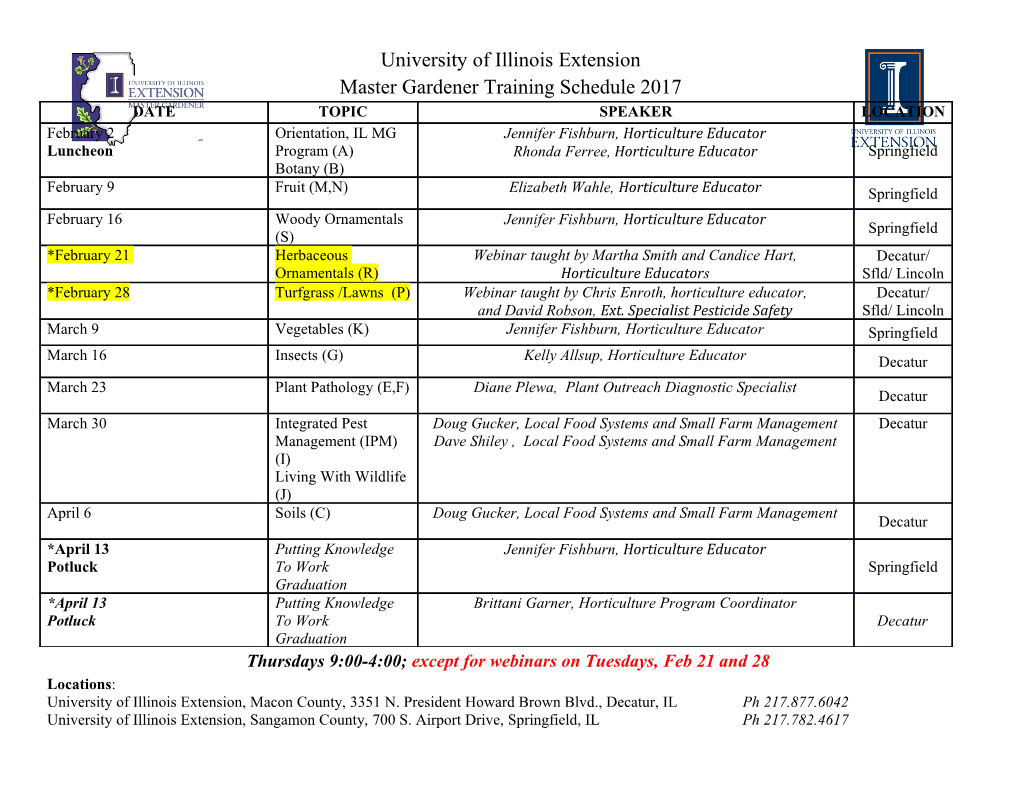
agronomy Article Harvest of Southern Highbush Blueberry with a Modified, Over-the-Row Mechanical Harvester: Use of Soft-Catch Surfaces to Minimize Impact Bruising Steven A. Sargent 1,* , Fumiomi Takeda 2, Jeffrey G. Williamson 1 and Adrian D. Berry 1 1 Horticultural Sciences Department, University of Florida/IFAS, Gainesville, FL 32611, USA; jgrw@ufl.edu (J.G.W.); adberry@ufl.edu (A.D.B.) 2 United States Department of Agriculture, Agricultural Research Service, Appalachian Fruit Research Station, 2217 Wiltshire Road, Kearneysville, WV 25430, USA; [email protected] * Correspondence: sasa@ufl.edu; Tel.: +1-352-273-4780 Abstract: Harvest of fresh market, southern highbush blueberries (SHB) is labor intensive and costly, leading to a demand for alternative harvest methods. Recent research has shown potential for mechanically harvesting blueberries with minimal bruising by using a modified over-the-row (OTR) harvester. For two harvests, SHB cultivars Optimus and Vireo were either hand-harvested (HH) or mechanically harvested (MH) by two commercial harvesters, one unmodified with standard hard-catch surfaces (HCS) or by the other modified with soft-catch surfaces (SCS). For Harvest 1, fruit from all harvest methods were hand-sorted into the following categories: blue fruit (marketable), ◦ red fruit, green fruit and culls. Samples from each cultivar and treatment were then held at 24 C overnight, and the following day firmness and impact bruise severity were determined. Harvest 2 Citation: Sargent, S.A.; Takeda, F.; had identical harvest treatments; however, the fruit were sorted on a commercial packing line prior Williamson, J.G.; Berry, A.D. Harvest to packing in clamshells (n = 16). A subsample was held overnight as in Harvest 1 for bruise severity of Southern Highbush Blueberry with rating, while the remaining fruit were stored at 1 ◦C for 14 days (d). Although percent marketable a Modified, Over-the-Row fruit was more affected by cultivar than harvest method, determination of bruise severity revealed Mechanical Harvester: Use of the benefit of harvest with SCS over HCS for both cultivars. The former had 16–26% severe bruising, Soft-Catch Surfaces to Minimize Impact Bruising. Agronomy 2021, 11, compared to 27–40% for the latter; HH had 1–4%. During storage, HH fruit remained firmer than 1412. https://doi.org/10.3390/ HCS and SCS, which were similar. After 14 d, firmness for “Optimus” was 239 N (HH), 157 N (HCS agronomy11071412 and SCS) and for “Vireo” it was 189 (HH), 155 N (HCS and SCS). Fruit weight loss increased during storage (1.1–4.4%), but there was no difference due to catch plate surface. SSC, TTA and Ratio were Academic Editor: Baohua Zhang not affected by catch surface type or storage period within cultivar. Using modifications such as “soft” catch surfaces on currently available OTR harvesters reduces impact bruise damage; however, Received: 18 June 2021 impacts incurred during commercial packing operations can negate this effect. MH for fresh market Accepted: 10 July 2021 blueberries may provide an economical alternative for blueberry growers; however, with current Published: 14 July 2021 technology, the fruit should be utilized within a week of harvest. Publisher’s Note: MDPI stays neutral Keywords: machine harvest; mechanical harvest; impact surface; soft catch surface; fruit quality; with regard to jurisdictional claims in bruising; packout published maps and institutional affil- iations. 1. Introduction The United States (U.S.) is the world’s largest producer of blueberries, with estimated Copyright: © 2021 by the authors. production in 2019 at 309 million kg, an increase of 21% from the previous year. Production Licensee MDPI, Basel, Switzerland. This article is an open access article for fresh and processing markets was 169 and 136 million kg, respectively, for a total value distributed under the terms and of $909 million. U.S. production begins in Florida in the late March market window when conditions of the Creative Commons prices are high. In 2019, Florida growers harvested 2064 ha and produced 24 million pounds Attribution (CC BY) license (https:// of primarily southern highbush blueberries (SHB) with a value over $62 million [1]. How- creativecommons.org/licenses/by/ ever, increased imports of blueberries during the early spring season has reduced prices 4.0/). Agronomy 2021, 11, 1412. https://doi.org/10.3390/agronomy11071412 https://www.mdpi.com/journal/agronomy Agronomy 2021, 11, 1412 2 of 13 for Florida growers and emphasized the importance of increased production efficiency to remain competitive internationally. Blueberries destined for fresh market require intensive labor during the harvest season, and this cost is a major factor leading to a demand for alternatives to reduce manual labor. For example, labor costs comprise approximately 60% of the annual Florida blueberry production budget and <10% is harvested mechanically for the processing market [2]. According to a survey of U.S. blueberry growers conducted by Gallardo et al. [3], growers used the following factors to determine harvest method: market price (77%), labor avail- ability (63%), labor cost (56%), fruit quality (39%), cultivar characteristics (18%), mechanical harvest cost (17%), infrastructure for fresh fruit (7%), and knowledge of machine harvesting (5%). Most fresh blueberry growers indicated that they would be receptive to adopting new machine harvesting technologies, especially if they were concerned about labor uncertainty or price [4]. Mechanical harvesting (MH) of northern highbush blueberries specifically for fresh market has been investigated since the mid-1990s, beginning with the introduction of the V45 blueberry harvester, which used slanted shaker drums and padded fruit catch- ing surfaces [5,6]. Later, Takeda et al. [7] determined that harvesting southern highbush and rabbiteye blueberries with the V45 harvester improved packout and reduced impact damage compared to commercial, over-the-row (OTR) harvesters available at that time. Harvesting blueberries with the V45 also reduced ground loss and increased shelf life. Bruising resulted from impacts with hard surfaces of the harvester such as beater rods, catch plates, and conveyer belts. To characterize the impacts created by mechanical harvesters, Yu et al. [8,9] developed a blueberry impact recording device (BIRD) and found that rotary-type harvesters gen- erated fewer and lower-magnitude impacts than either sway- or slapper-type harvesters. These studies revealed that detached blueberry fruit were more likely to strike the catch plates than the tunnel wall and that maximum impact occurred when the fruit hit the catch plates [8,9]. Takeda et al. [10] achieved a significant reduction in bruise incidence by incorporating soft-catch surfaces onto a semi-mechanical harvesting system. Additional research has shown potential for harvesting berries with minimal bruising by modifying a commercial OTR harvester. In 2017, studies were conducted in Florida [11] and Washing- ton [12] in which a small harvest crew rode on an OTR harvester with various soft-catch surfaces and used handheld shakers to remove fruit as a means to make harvest labor more efficient. These studies indicated that the semi-mechanical harvesting method and capturing detached berries on soft surfaces had potential for small-sized farms. In addition to mechanical harvester improvements, there has been continued effort to develop SHB varieties that are suitable for machine harvest for fresh market. The U.S. and Canada blueberry industry indicated that the most important breeding traits were fruit firmness, flavor, and shelf life [13]. However, to develop cultivars to withstand machine harvest, the following factors should be considered: bush architecture, harvest timing, loose fruit clusters, easy detachment of ripe fruit, minimal stem retention or scarring, firmness [14–17], and most importantly, fruit attributes that contribute to minimizing internal bruising from impact force. Several currently grown SHB cultivars, such as Farthing, Meadowlark, Indigocrisp, Keecrisp, and Optimus, have been released through the University of Florida breeding program and are considered suitable for fresh market machine harvest [17,18]. Other studies have focused on improving harvest efficiency. Casamali et al. [19] investigated grafting blueberry cultivars onto Vaccinium arboretum, a species with single-trunk growth habit, with the goal of improving mechanical harvest efficiency by reducing ground loss. Other studies examined fruit detachment force for several SHB cultivars, and green “Farthing” fruit were found to have higher detachment force than blue fruit, which should reduce the number of unripe fruit harvested, thereby increasing packout [20,21]. It was also determined that extending the harvest interval from each 3 d (with manual harvest) to 7 d nearly doubled the amount of soft fruit harvested. Extending the harvest interval also negatively affected fruit quality and shortened shelf life due to the advanced maturity of the fruit [19]. Although there are many challenges Agronomy 2021, 11, 1412 3 of 13 to overcome, current efforts are underway by a number of research groups including USDA, University of Florida, University of Georgia, Michigan State University, Oregon State University, and Washington State University. Several commercial manufacturers are developing innovative mechanical harvest systems for fresh-market blueberries. For example, commercial engineering approaches to reduce the interaction between blueberry fruit and
Details
-
File Typepdf
-
Upload Time-
-
Content LanguagesEnglish
-
Upload UserAnonymous/Not logged-in
-
File Pages13 Page
-
File Size-